When it comes to investing in a laser cutter, understanding the fiber laser cutting machine cost landscape is key. Fiber laser technology has revolutionized the cutting industry, offering unparalleled precision and efficiency. However, navigating the costs involved requires careful consideration. Here's a comprehensive pricing guide to help you make informed decisions:
Table of Contents
Introduction
As technology advances in manufacturing, laser cutting machines have emerged as a sophisticated solution for precision board cutting.
Operating by focusing laser beams onto the workpiece's surface through specialized lenses, a laser cutter melts the material. It employs assist gases aligned with the laser beam to disperse the molten material. Simultaneously, the laser beam traverses along predefined paths relative to the materials, creating precise cuts in desired shapes.
The evolution of technology and associated costs has broadened the scope of applications for laser cutting machines. Renowned for their versatility and durability, these machines offer accurate and efficient processing, making them a preferred choice across various industries.
The overall costs of laser cutting machines encompass not only their initial purchase but also installation, training, maintenance, and operational expenses. Therefore, for enterprises contemplating investments in laser cutters, a comprehensive understanding of these costs and the ensuing return on investment is crucial. Such insight empowers companies and individuals to optimize profits through prudent budgeting and effective cost management.
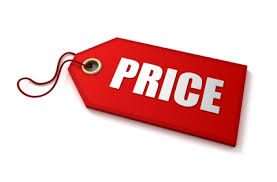
Fctors Affecting Fiber Laser Cutting Machine Cost
Machine Cost: The primary expense is the upfront cost of the fiber laser cutting machine itself. Prices can vary widely depending on factors such as power output, cutting area size, brand reputation, and additional features. Entry-level models may start around $50,000, while high-end industrial-grade machines can exceed $500,000.
Installation and Setup: Factor in the costs associated with installing and setting up the machine in your facility. This may include hiring technicians for assembly, calibration, and integration with existing workflows. Installation costs typically range from a few thousand to tens of thousands of dollars, depending on the complexity of the machine and your specific requirements.
Training and Certification: Proper training is essential to ensure safe and efficient operation of the fiber laser cutting machine. Budget for training programs provided by the manufacturer or third-party training providers. Training costs can vary based on the duration and depth of the program, ranging from a few hundred to several thousand dollars per operator.
Maintenance and Service Contracts: Ongoing maintenance is critical to keep your fiber laser cutting machine running smoothly and prevent costly downtime. Consider investing in service contracts offered by the manufacturer or authorized service providers. These contracts typically cover routine maintenance, repairs, and technical support. Costs vary depending on the level of coverage and duration of the contract, but average around 5-10% of the machine's purchase price annually.
Consumables and Spare Parts: Budget for consumables such as laser cutting nozzles, lenses, and protective covers, which need regular replacement to maintain cutting quality. Additionally, keep spare parts on hand for quick repairs and replacements to minimize downtime. The costs of consumables and spare parts depend on usage rates and machine specifications.
Operating Expenses: Factor in ongoing operational costs such as electricity, cooling water, and assist gases (e.g., nitrogen, oxygen). These costs can vary depending on the machine's power consumption and cutting requirements.
ROI and Cost Analysis: Conduct a thorough cost analysis to assess the return on investment (ROI) of purchasing a fiber laser cutting machine. Consider factors such as increased productivity, reduced material waste, labor savings, and potential revenue from expanded cutting capabilities. While the initial investment may seem substantial, the long-term benefits can outweigh the costs.
Other Factors Influencing Fiber Laser Cutting Machine Cost
Type of laser
Laser-cutting machines can be classified from multiple angles, including the type of laser, structural type, type of material being cut, power level, etc. The following is a classification of laser-cutting machines based on different criteria:
Classified by laser type:
(1) CO2 laser cutting machines:
They are suitable for cutting non-metal and some metal. Although their costs are reasonable, the price varies depending on the power, brand, and accessories.
(2) Fiber laser cutting machine:
They are mainly applied to cut metals and possess higher power, efficiency and speed. Therefore, their budgets are higher than those of CO2 laser cutters.
(3) YAG laser cutting machine:
Using solid-state lasers (such as Nd:YAG) is suitable for cutting both metals and non-metals. However, due to their lower efficiency, they have gradually been phased out by the market.
Classified by structure:
(1) Gantry laser cutting machine: the laser is fixed, and the workpiece moves, suitable for large materials or heavy industry.
(2) Cantilever laser cutting machine: the laser head is fixed at one end, suitable for small or medium-sized workpieces.
(3) Robotic arm laser cutting machine: a robotic arm is used for laser cutting, and it is suitable for complex or three-dimensional cutting.
Classified by the type of cutting materials:
(1) Metal laser cutting machine: they are suitable for cutting multiple metals, such as stainless steel and carbon steel.
(2) Non-metal laser cutting machines: they cut wood, plastic, paper, and other non-metals.
Classified by the power:
(1) Low-power laser cutting machine: suitable for thin materials or applications with low cutting requirements.
(2) Medium-power laser cutting machine: suitable for medium-thickness materials, balancing cutting speed and equipment cost.
(3) High-power laser cutting machine: used for thick materials or applications requiring high-speed mass production.
Classified by cutting bed width:
(1) Standard Format Laser Cutter: suitable for cutting standard format materials.
(2) Large Format Laser Cutter: suitable for cutting large format materials, such as large billboards, large metal sheets, etc.
These classifications help users choose the appropriate laser cutter based on their specific cutting needs and application scenarios.
Laser power
Laser power directly affects cutting speed and the maximum thickness of material. The higher the power, the stronger the cutting capability and, accordingly, the higher costs.
For example, when cutting the same material, fiber laser cutters of 3000w perform better than those of 500w in terms of speed and maximum thickness.
Work area size
Work area size decides the maximum size of materials to be processed. Larger work area size allows for improved flexibility and processing capability, which entails higher costs.
For example, the price of a laser cutting machine with a 2x3 meter work area will be higher than that of a standard-sized workbench.
Features and accessories
Advanced functions, like a CNC control system, automatic focusing, and rotate attachment, can significantly improve quality and operation convenience. However, additional functions and accessories also add to the budget.
Brand reputation and quality
Laser-cutting machines of high-end brands are famous for their excellent performance, reliability, and after-sale services. So, they also cost more.
Economic machines may have an edge in initial costs in the short term. However, they entail increased costs caused by long-term maintenance and performance stabilizing.
The selection of laser cutters should balance personal demands and budgets and consider the equipment's performance, efficiency, and long-term operating costs.
Therefore, understanding how various factors affect the price of a laser cutter can help customers generate wiser selections.
Tips for Getting the Best Value When Purchasing a Fiber Laser Cutting Machine
- Thoroughly Assess Your Needs and Budget: Evaluate your cutting requirements, including material type, thickness, size, and accuracy specifications. Choose laser powers, cutting heads, and workbench areas accordingly. Estimate automation levels and productivity demands based on your production scale.
- Research and Compare Multiple Options: Explore various laser cutter brands and prioritize reputable ones with comprehensive after-sales services. Obtain quotes and compare equipment parameters and additional expenses. Conduct field investigations or request on-site cutting trials to assess machine performance.
- Consider Long-Term Costs: Factor in both initial investments and long-term operational expenses. Account for labor costs, consumables, energy consumption, and maintenance. Evaluate the total cost of ownership over the machine's lifecycle to ensure cost-effectiveness.
- Look for Promotions and Package Deals: Stay informed about manufacturers' promotional activities and take advantage of discounts. Bargain moderately to secure better deals without compromising quality. Consider package deals that bundle equipment, accessories, consumables, and services for added value.
- Invest in Quality and Reliability: Prioritize quality and stability, especially for critical applications requiring high precision. Avoid compromising on quality for temporary cost savings, as premium products offer better long-term economic benefits due to their accuracy, stability, and low breakdown rates.
- Factor in Maintenance, Consumables, and Growth Potential: Choose brands with convenient maintenance and responsive support services. Emphasize the cost of consumables and select them at reasonable prices. Opt for laser cutters with flexibility and room for improvement to adapt to changing demands and support future growth.
By considering these factors, you can make informed decisions and select the most cost-effective laser cutting machine that meets your specific requirements while maximizing long-term benefits. Remember, prioritize quality and reliability over low expenses for optimal results.
Conclusion
In the article, factors influencing the fiber laser cutting machine cost are listed and discussed in detail so as to serve as a reference for readers who are wondering about the laser cutting machines.
Customers in need of procurement should estimate the cutting application demands thoroughly and carefully.
Don't pursue high-end machines blindly or just aim for low costs. It’s critical for enterprises and individuals to select suitable laser cutters to win in market competition and promote productivity.
KRRASS Machine Tool boasts a three-decade history of laser cutting machine R&D and is one of the largest exporters in China.
Our laser cutting machines enjoy high quality, accuracy, efficiency, and brand reputation. Don’t hesitate to browse our product page. We will never disappoint you.