When it comes to cutting and welding capabilities, fiber lasers often outperform CO2 lasers in terms of precision and processing speed. This is owing to fiber lasers' superior beam quality and energy efficiency. Furthermore, fiber lasers are frequently less expensive in terms of energy consumption and maintenance, making them an excellent alternative for industrial applications. Fiber lasers are very simple to integrate into automated manufacturing systems, making them ideal for high-volume production environments. Overall, fiber lasers are a preferred choice for many industrial and commercial laser applications due to their better performance, efficiency, and versatility.
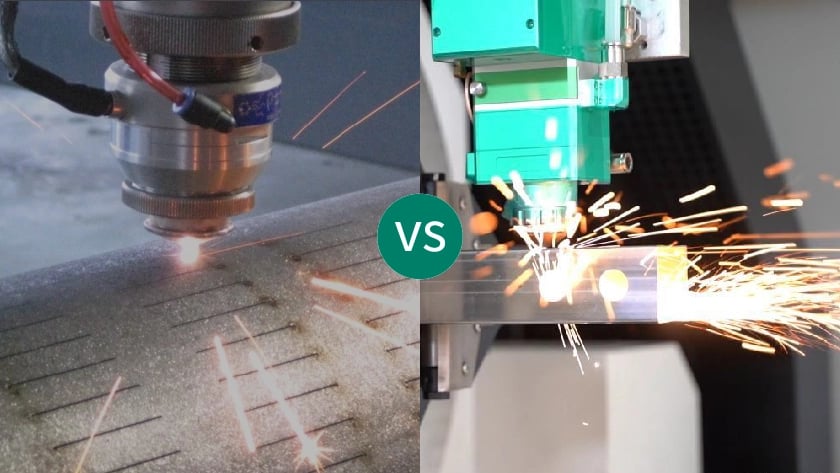
I. Introduction
- Explanation of the increasing popularity of fiber lasers in industrial and manufacturing applications
Several factors contribute to the growing use of fiber lasers in industrial and manufacturing applications. Firstly, fiber lasers outperform other types of lasers in terms of performance and efficiency. They are well-suited for a wide range of industrial applications, including cutting, welding, marking, and engraving, because to their high beam quality, energy efficiency, and quick processing rates.
Fiber lasers are more cost-effective in terms of energy consumption and maintenance, in addition to their performance. Because of their solid-state construction and usage of fiber optic cables, they have lower operating costs and downtime, making them a more cost-effective solution for industrial users.
Fiber lasers are also very versatile and easily integrated into automated industrial processes. This makes them excellent for high-volume production environments requiring precision, speed, and dependability. The flexibility of fiber lasers to be readily integrated into current production lines and robotic systems has contributed to their increasing acceptance in industrial settings.
Furthermore, advances in fiber laser technology have resulted in the development of more powerful and adaptable systems, hence expanding their potential and uses. As a result, manufacturers are increasingly turning to fiber lasers to fulfill their changing production needs, fueling the growth of these lasers in the industrial and manufacturing sectors.
Overall, fiber lasers' better performance, cost-effectiveness, adaptability, and technological developments have made them a preferred choice for industrial and manufacturing applications, resulting in their growing appeal in these industries.
- Comparison of fiber lasers to CO2 lasers, which have been traditionally used in these industries
Fiber lasers and CO2 lasers have traditionally been utilized in industrial and manufacturing applications, but there are numerous key differences between the two technologies that have resulted in fiber lasers' rising acceptance.
1. Efficiency: Fiber lasers are more efficient than CO2 lasers in general. They convert a greater proportion of the input energy into the laser beam, resulting in decreased power consumption and operating expenses.
2. Beam Quality: Fiber lasers provide enhanced beam quality, resulting in improved focus and precision. This makes them ideal for high-precision applications such as cutting thin materials and complicated drawings.
3. Maintenance: Because fiber lasers are solid-state and employ fiber optic cables, they require less maintenance than CO2 lasers, which rely on gas mixes and mirrors. As a result, downtime is decreased and overall maintenance expenses are lowered.
4. Versatility: Fiber lasers are extremely adaptable and may be used for a variety of tasks such as cutting, welding, and cleaning. They can process a wide range of materials, including carbon steel, stainless steel. And aluminum, etc. Making them an excellent solution for a wide range of production requirements.
5. Integration: Because fiber lasers are simple to incorporate into automated manufacturing systems, they are suited for high-volume production environments. Because of their compatibility with robotic systems and CNC machinery, they may be seamlessly integrated into current production lines.
Overall, the efficiency, beam quality, fewer maintenance requirements, diversity, and ease of integration of fiber lasers have led to their growing appeal in industrial and manufacturing applications, resulting in a transition away from the conventional use of CO2 lasers in these industries.
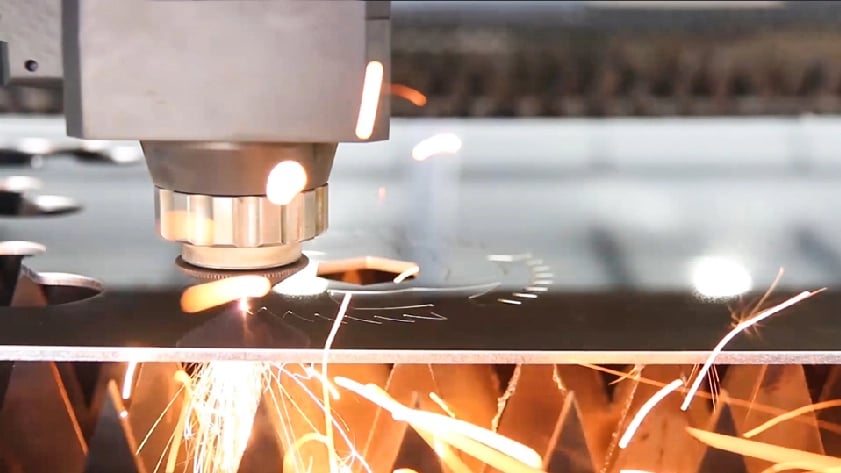
II. Advantages of Fiber Lasers
- Discussion of the unique properties of fiber lasers that make them highly desirable for certain applications
Fiber lasers have various unique features that make them particularly appealing for specific applications. These characteristics contribute to their expanding use in a variety of industrial and manufacturing operations. Some of the key properties that make fiber lasers useful for particular applications are as follows:
1. High Beam Quality: Fiber lasers provide a high-quality laser beam with exceptional focus and stability. This makes them ideal for precision cutting, welding, and marking operations that require a clean and accurate beam profile.
2. Efficiency: Fiber lasers are noted for their great efficiency in turning input energy into laser beam. This leads in decreased power consumption, cheaper running costs, and a smaller environmental footprint, making them a cost-effective solution for high-volume production environments.
3. Versatility: Fiber lasers are versatile and may be utilized with a variety of materials such as . Their capacity to process a wide range of materials qualifies them for metal cutting.
4. Maintenance Requirements: Fiber lasers require less maintenance than other types of lasers, such as CO2 lasers. Fiber optic cables, with their solid-state construction, contribute to less downtime and lower overall maintenance costs, making them an appealing option for continuous industrial operations.
5.Fiber Delivery: By using optical fibers for beam delivery, fiber lasers can send laser beams across vast distances with minimal power loss. This characteristic is useful in applications requiring remote or flexible beam delivery, such as robotic welding or laser cutting systems.
6. Reliability: Fiber lasers are well-known for their dependability and lengthy operational lives. Their tough design and tolerance to environmental conditions make them ideal for challenging industrial situations where consistent performance is essential.
Fiber lasers are very sought for specialized applications due to their unique qualities, notably in industries such as automotive, aerospace, electronics, and medical device manufacture, where precision, efficiency, and dependability are critical. As a result, fiber lasers have seen significant adoption in these industries, resulting in a shift away from classic laser technologies such as CO2 lasers.
Highlighting factors such as high beam quality, efficiency, and reliability
Fiber lasers are well-known for their high beam quality, which is essential for precision cutting, welding, and marking applications. The high beam quality ensures a clean and accurate beam profile, which leads to greater performance and consistency in a variety of industrial operations.This reduces not just power consumption but also operating expenses, making fiber lasers an economical solution for high-volume industrial situations. Their efficiency also leads to a lower environmental imprint, which aligns with sustainability objectives.
Furthermore, the dependability of fiber lasers is a major feature that distinguishes them. Their solid-state design and sturdy construction contribute to their long operational lifespan and low maintenance needs. This dependability is especially important in tough industrial contexts where consistent performance is critical for ongoing manufacturing processes.
Fiber lasers' high beam quality, efficiency, and dependability make them an excellent choice for a wide range of industrial applications, providing superior performance, cost-effectiveness, and constant operation. Thank you for recognizing and valuing these critical components of our fiber laser technology.
III. Cost Considerations
- Analysis of the factors that contribute to the higher cost of fiber lasers compared to CO2 lasers
Several factors contribute to the higher cost of fiber lasers compared to CO2 lasers:
1. Technology and Materials: Fiber lasers need advanced technology and high-quality materials such as semiconductor diodes, which are more expensive to develop and maintain than CO2 laser components.
2. Efficiency and Performance: Fiber lasers are known for their greater efficiency and performance, which results in better beam quality, faster processing speeds, and lower energy consumption. Fiber lasers' sophisticated features and capabilities contribute to their greater cost.
3. R&D: The creation and refining of fiber laser technology necessitate significant expenditure in R&D, which is reflected in the overall cost of these systems.
4. Customization and Integration: Fiber lasers are frequently integrated into complex manufacturing systems and customized for specific purposes, necessitating additional engineering and integration efforts that contribute to their higher overall cost.
Finally, the advanced technology, improved performance, and specific materials utilized in fiber lasers, as well as the expenditure in research, development, all contribute to the higher cost of fiber lasers when compared to CO2 lasers. However, the benefits of greater efficiency, performance, and productivity frequently justify the expenditure in many industrial applications.
Explanation of the complex and precise manufacturing processes required for fiber lasers:
Fiber laser manufacturing techniques entail sophisticated and precise procedures to develop advanced components and assemble them into a functional laser system. Here's an outline of the intricate production procedures necessary for fiber lasers:
1. Optical Fiber Production: The manufacturing process begins with the creation of high-quality optical fibers, which are commonly formed of silica glass. This entails drawing and stretching the fibers to precise dimensions with excellent uniformity and consistency. To obtain the appropriate optical and mechanical qualities, the fiber drawing process necessitates precise control over temperature, tension, and drawing speed.
2. Fabrication of Semiconductor Diodes: Fiber lasers rely on high-power semiconductor diodes to pump the active fiber core and start the lasing process. To develop precise and reliable light-emitting components, these diodes are manufactured using complicated semiconductor manufacturing techniques such as epitaxial growth, lithography, etching, and metallization.
3. Laser Cavity Assembly: Integrating the active fiber, pump diodes, and optical components such as mirrors, isolators, and couplers in the fiber laser cavity. To provide optimal light amplification and lasing efficiency, this technique necessitates accurate alignment and bonding. To accomplish the needed alignment and stability within the laser cavity, certain equipment and techniques are used.
4. Thermal Management: Because fiber lasers generate heat while operating, proper thermal management is required to preserve performance and dependability. This entails integrating cooling systems, heat sinks, and thermal insulation to disperse heat and keep the laser system working at stable temperatures.
5. Control and Electronics Integration: The integration of control systems, electronics, and software for power modulation, wavelength control, and beam shaping is crucial for the functioning and performance of fiber lasers. This entails the assembly and integration of complicated electronic components, control algorithms, and user interfaces to enable precise and reliable operation.
6. Quality Assurance and Testing: Throughout the production process, stringent quality assurance and testing methods are used to ensure the performance, reliability, and safety of the fiber laser systems. This comprises optical characterization, power measurements, thermal testing, and environmental stress testing to verify compliance with demanding performance criteria.
In summary, the manufacturing processes for fiber lasers involve a combination of precision engineering, material science, semiconductor fabrication, thermal management, and quality control to produce advanced laser systems with high efficiency, exceptional beam quality, and reliable performance for a wide range of industrial applications.
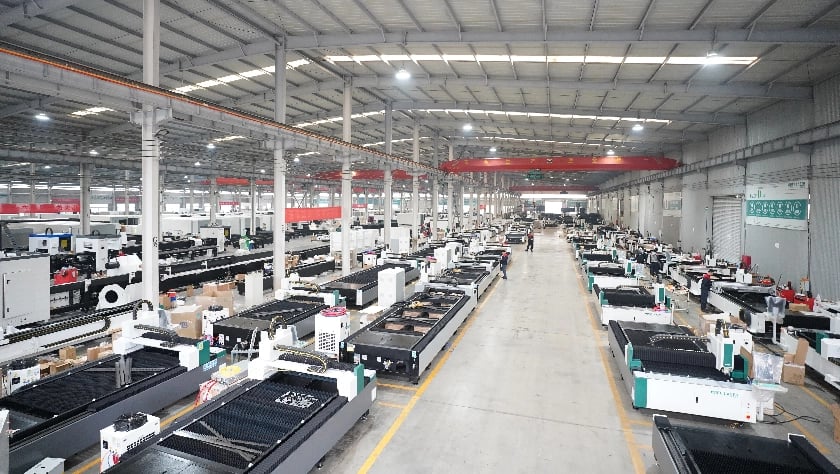
IV. Applications
- Overview of the specific industries and applications where fiber lasers are particularly advantageous
Fiber lasers have gained popularity in a variety of industries due to its multiple benefits, which include high efficiency, great beam quality, small design, and adaptability. Here's a rundown of the industries and applications where fiber lasers are very useful:
1. Industrial Manufacturing: Fiber lasers are widely employed in procedures such as cutting, welding, marking, and engraving in the industrial manufacturing industry. They are perfect for cutting and welding metal components in the automotive, aerospace, and general industrial industries due to their great power and precision. Fiber lasers are also used for high-speed, high-precision marking and engraving on a variety of materials, including metals, polymers, and ceramics.
2. Automotive Industry: Fiber lasers are widely used for welding, cutting, and marking applications in the automotive industry. Because of their capacity to produce high-quality welds and exact cuts on various metals and alloys, they are used in the production of automobile components such as body panels, and exhaust systems.
3. Aerospace and Defense: In the aerospace and defense sectors, fiber lasers are used for cutting, drilling, and surface treatment of materials such as titanium, aluminum, and composites. Their high power and beam quality enable efficient and precise processing of components, including aircraft structures, engine parts, and defense equipment.
4. Medical Device Manufacturing: Fiber lasers are employed in the production of medical devices, including surgical instruments, implants, and medical equipment. Their ability to process a wide range of materials with high precision makes them well-suited for cutting, welding, and marking applications in the medical industry.
5. Electronics and Semiconductor Manufacturing: Fiber lasers are utilized for micromachining, cutting, and drilling of electronic components, circuit boards, and semiconductor materials. Their high precision and fine beam quality enable the fabrication of intricate features and microstructures in electronic devices and semiconductor components.
6. Watchmaking: Fiber lasers are favored in the watchmaking industries for high-precision cutting of precious metals, and other materials.
7. Oil and Gas Industry: Fiber lasers find applications in the oil and gas sector for processes such as pipeline welding, surface treatment, and material processing. Their ability to operate in harsh environments and their high power make them suitable for various oil and gas-related fabrication and maintenance tasks.
In summary, fiber lasers are particularly advantageous in industries such as industrial manufacturing, automotive, aerospace, medical devices, electronics, additive manufacturing, and oil and gas, where their high performance, precision, and versatility meet the demands of diverse applications and production processes.
V. Conclusion
- Summary of the unique properties and advantages of fiber lasers
Fiber lasers have several unique properties and advantages that make them a popular choice across various industries. Here is a summary of the key benefits of fiber lasers:
1. High Efficiency: Fiber lasers have high electrical-to-optical conversion efficiency, resulting in lower power consumption and reduced operating costs.
2. Excellent Beam Quality: Fiber lasers produce a high-quality beam with a small spot size and low divergence, making them ideal for precision cutting, marking, and welding applications.
3. Versatility: Fiber lasers can process a wide range of materials, including carbon steel, aluminum, stainless steel, making them suitable for various applications.
4. Low Maintenance: Fiber lasers have a long lifespan and require minimal maintenance, resulting in reduced downtime and increased productivity.
5. High Power: Fiber lasers can deliver high power levels, enabling fast and efficient processing of materials.
6. Environmentally Friendly: Fiber lasers do not require any hazardous chemicals, making them an environmentally friendly option for industrial applications.
Overall, the unique properties and advantages of fiber lasers make them a versatile and efficient tool for various industrial applications, including cutting, welding, marking, and engraving.
For further insights into the topic, we would like to recommend checking out the article on CO2 Laser VS Fiber Lasers - Which One Should You Buy?
If you have any questions, we encourage you to get in touch with us. We value the opportunity to hear from you and are here to assist with any queries you may have.