A stamping press serves as a vital metalworking machine tool utilized to shape or cut metal through deformation with the aid of a die. This precision instrument employs meticulously crafted male and female dies to craft the desired final product. In essence, it serves as a contemporary alternative to traditional methods like the hammer and anvil, offering efficiency and precision in metal fabrication processes.
Understanding Components of Stamping Press
A stamping press typically consists of a bolster plate and a ram. Presses are available in different frame configurations, such as C-Frame, which features open front and left and right sides, and straight-side or H-Frame designs, preferred for stronger, higher tonnage applications.
Proper sizing of the press and tonnage is crucial, particularly based on the intended applications, whether it's blanking, forming, progressive, or transfer operations. Additionally, it's essential to carefully consider load distribution to avoid off-center conditions that can lead to premature wear on the press components
Bolster Plate:
Situated atop the press bed, the bolster plate serves as a substantial metal block where the lower portion of a die is securely clamped. In stationary position, it forms a foundational element of the press. For large-scale applications, such as those in the automotive industry, bolster plates may integrate die cushions to apply blank holder or counter draw forces, particularly essential in deep drawing operations conducted with single-acting presses. Ensuring long die life between maintenance intervals, the ram or slide guidance plays a critical role.
Various slide guide types are available, ranging from 4-point V-Gibs or 6-point square gibs on smaller presses to 8-point full-length slide guides on larger straight-side frame presses. Dies and material are introduced into the press between the bolster and slide. Effective press designs meticulously account for plastic deformation, or deflection, when evaluating frame design and load considerations.
Ram/Slide:
Functioning akin to a hammer striking an anvil, the vertical motion of the slide is central to press operations. Mechanical presses, the most prevalent type, commonly employ an eccentric drive mechanism to propel the ram slide. The stroke length or slide travel is contingent upon the crankshaft or eccentric. Hydraulic presses, in contrast, utilize hydraulic cylinders for motion.
The drive system's nature dictates the force progression throughout the ram's stroke. Mechanical presses exhibit tonnage rating points above Bottom Dead Center (BDC), typically at .187", .25", and .5". Thus, adherence to press capacity limits is imperative, given the tonnage curve inherent to mechanical presses. Alternatively, Link Motion mechanical presses offer a slide slowdown near BDC, beneficial for soft-touch tooling and enhancing die life, especially in blanking operations.
Hydraulic presses, devoid of a tonnage curve, can exert full tonnage at any point during the stroke. However, speed is a trade-off, with mechanical presses boasting greater velocity. Hydraulic presses are favored for deep forming or drawing processes, or when extended dwell time at the bottom is desirable.
Presses may also be categorized as single-acting or double-acting. Single-acting presses feature a solitary ram, while double-acting presses incorporate a subdivided ram, facilitating diverse operations such as blank holding and forming.
Additional Components and Controls:
Presses are typically integrated with an automatic feeder, electronically linked via a programmable logic controller. This feeder supplies metal raw material through the die, having been unrolled from a coil and passed through a straightener. Tonnage monitors may also be incorporated to monitor force exertion per stroke.
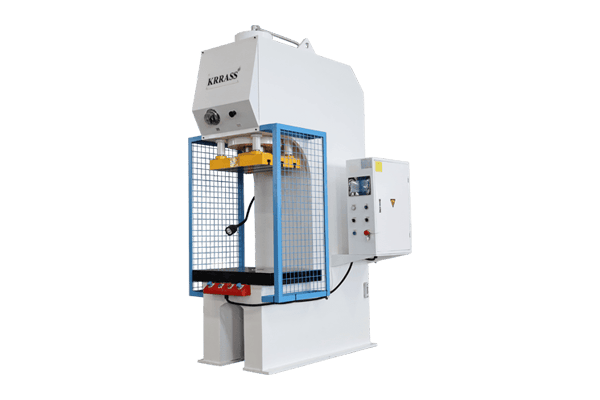
Choice of Right Stamping Press Machine For Your Shop
Explore the transformative capabilities of KRRASS's Stamping Press technology, poised to optimize your production processes. Our array of innovative sheet metal machines, tailored solutions, and user-friendly option suites are meticulously designed to cater to the real needs of our customers.
At KRRASS, our commitment to excellence extends beyond conventional product offerings. We are steadfastly dedicated to empowering our esteemed clientele with cutting-edge solutions aimed at enhancing productivity, efficiency, and meeting their distinct requirements. Embark on a journey to discover how our Stamping Press technology can revolutionize your manufacturing operations, streamline your workflow dynamics, and propel your success to unparalleled heights.