Manipulation de formes complexes sur un presse plieuse La réalisation de pliages peut être un véritable défi. Assurer le bon ordre de pliage et un espace suffisant pour chaque pliage peut sembler simple, mais un faux pas peut entraîner la mise au rebut de pièces et des retards de livraison. Heureusement, la technologie de freinage moderne peut apporter une aide. Qu'un atelier investisse dans une nouvelle machine ou détermine quelle technologie peut être ajoutée à une configuration existante pour améliorer le rendement, les considérations suivantes peuvent s'avérer utiles.
Table des matières
CAO/FAO
Logiciel Dans tout atelier de fabrication performant, une bonne conception des pièces est la clé d'une production efficace, car elle crée un processus plus rationalisé pour toutes les personnes impliquées dans le projet. Les logiciels jouent un rôle crucial pour aider les ateliers à atteindre cet objectif.
Certains logiciels offrent désormais la possibilité d'appliquer des outils au sein du logiciel. Les processus en amont peuvent être fortement impactés lorsque l'ingénierie ne prend pas en compte le rayon obtenu par l'outillage dans l'atelier. La possibilité de modifier la matrice en V dans le programme peut donner lieu à un modèle 3D plus précis avant le traitement d'une seule pièce. Lorsque la matrice en V souhaitée est appliquée au niveau de la modélisation, le rayon correct peut être obtenu, et c'est là que tout commence avec le formage.
Un autre outil que de nombreux logiciels proposent désormais est un moyen de calculer la déduction de pliage requise lors du développement du modèle plat de la pièce. Les ateliers ayant une expérience du formage comprennent l'importance d'utiliser la déduction de pliage correcte lors de la découpe de pièces brutes pour la production. Les plates-formes logicielles qui permettent des facteurs K personnalisés fournissent des tolérances de pliage plus précises, tenant compte de la longueur de l'arc de l'axe décalé après le formage. Ensuite, le retrait extérieur (OSSB) et la déduction de pliage sont calculés.
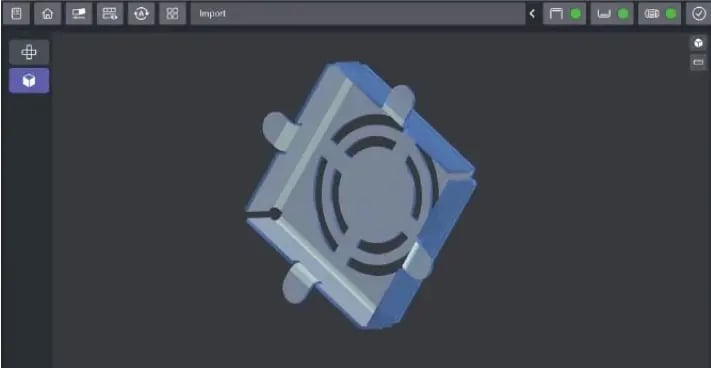
Ces calculs sont essentiels pour développer la taille de pièce appropriée avant qu'elle ne soit envoyée au processus de découpe. Le logiciel gère les calculs mathématiques longs et rationalise le processus. Certaines plates-formes logicielles permettent aux utilisateurs de télécharger des fichiers STEP directement sur l'interface homme-machine (IHM) de la machine. Le logiciel de la machine peut ensuite aplatir le modèle et simuler directement le pliage tout en garantissant la précision des dimensions de la pièce. Cette simulation offre également un avantage en termes de sécurité. Les opérateurs qui regardent la simulation peuvent comprendre à l'avance où positionner en toute sécurité leur pince de pièce, pour éviter tout point de pincement contre le côté du vérin ou le côté de l'outillage.
Couronnement
Le bombage d'une presse plieuse est un défi sur toute pièce nécessitant un pliage de plus de 1,2 m. Le fait de ne pas tenir compte de la déflexion du vérin peut entraîner des écarts d'angularité sur toute la longueur du pliage. Chaque constructeur de machines tente de relever ce défi d'une manière différente. Le bombage de type coin, qui est réalisé avant ou après le formage, peut prendre du temps et être moins précis.
Le bombage dynamique est obtenu au moment du pliage et à l'endroit où se trouve le pliage sur la table. Plusieurs vérins hydrauliques dans le lit inférieur réagissent avec des capteurs surveillant la pression du matériau pour produire le bombage. Bystronic relève ainsi ces défis. Le bombage dynamique permet également d'utiliser le pliage multiposte sur toute la longueur de pliage, car le bombage se produit de manière dynamique en fonction de l'emplacement du pliage. La fabrication de pièces complexes et de grande taille nécessite que l'opérateur comprenne comment la machine est réglée pour réagir à ces situations.
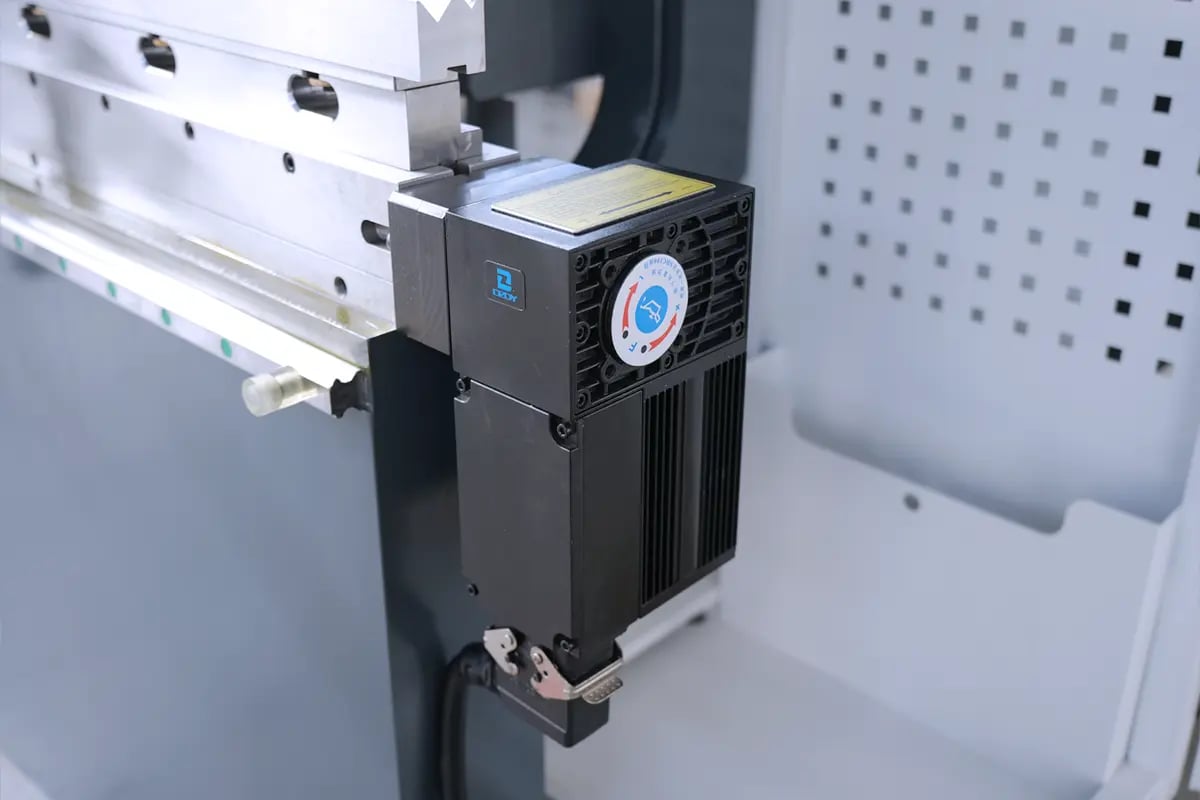
Butée arrière de presse plieuse
La butée arrière est un allié pour l'opérateur de la presse plieuse lors du pliage de formes complexes car elle empêche la pièce de « marcher » en raison d'un nombre trop faible de points de contact sécurisés. Avec des cônes et des brides uniques, disposer d'une butée arrière réglable pour mieux fixer une pièce est inestimable. Chaque constructeur de machines-outils adopte une approche légèrement différente à ce sujet.
Par exemple, Krrass propose un système de butée arrière à 6 axes pour plus de flexibilité. Les butées arrière gauche et droite ont une portée indépendante l'une de l'autre, ce qui est utile lorsque les pièces ne sont pas parallèles au système de butée arrière. La conception multifonctionnelle des doigts offre une ouverture au centre du cadre de la jauge, ce qui permet au logiciel de déterminer le bord de contact. Il place ensuite la pièce dans cette ouverture tout en maintenant deux points de contact pour éviter que la pièce ne se déplace.
Serrage et outillage spécialisé
Outils spéciaux Les outils de serrage sont indispensables pour les pièces complexes qui présentent un risque de contact entre une bride et l'outillage. Le défi avec un tel outillage est de le retirer entre les travaux. Des options de serrage sont disponibles qui permettent à l'opérateur de changer rapidement d'outil individuel, sans avoir à nettoyer l'ensemble du vérin. Investir dans le bon outillage spécialisé peut également avoir un impact important sur le traitement de pièces complexes.
Certains outils spécialisés peuvent transformer quatre coudes en un seul, comme un profilé en U. Le bon outillage peut créer des persiennes, des formes de charnières, presque tout ce qui peut être conçu dans un logiciel de CAO/FAO. S'il s'agit d'une pièce à grand volume, le retour sur investissement est souvent facilement justifié. Les ateliers doivent revoir régulièrement leurs pièces pour voir si une refonte et un réoutillage pourraient rendre leur processus plus efficace.
Mesure sur machine
La mesure sur machine permet de mesurer activement le retour élastique de vos pièces, ce qui permet de capturer toutes les variations d'angle et d'ajuster automatiquement le pliage. Il existe un logiciel de pliage capable d'intégrer des matériaux uniques dans une base de données. En utilisant la base de données avec les propriétés des matériaux, les opérateurs peuvent être sûrs que l'angle souhaité sera atteint. Le système de mesure sur machine peut tenir compte des variations des propriétés des matériaux, augmentant ainsi la productivité globale.
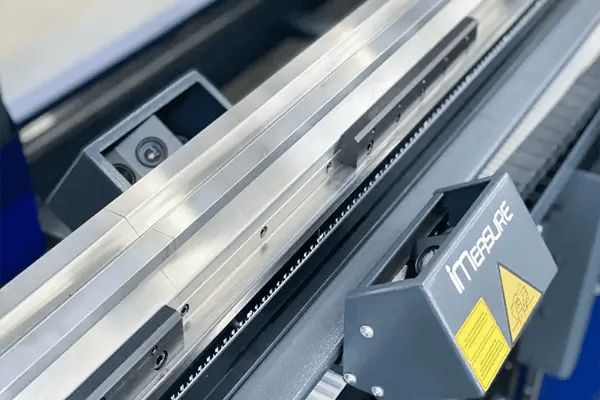
Certaines entreprises utilisent un système de mesure laser, tandis que d'autres utilisent une caméra de sécurité à profil latéral ou un bras mécanique qui va toucher le matériau pour réaliser sa mesure. L'objectif est d'ajuster l'action du vérin pour obtenir rapidement des pièces précises et répétables. L'efficacité est la clé du succès continu dans la fabrication. Il est essentiel de s'assurer que votre presse plieuse est équipée des options et des outils appropriés pour obtenir une flexibilité de production maximale des géométries complexes qui passent par votre atelier.