Presses plieuses CNC sont largement utilisés dans les industries de la tôle et de la fabrication, mais ils représentent également une menace importante pour la sécurité des opérateurs.
Chaque année, de nombreux accidents liés à l’utilisation des presses plieuses se produisent.
Malheureusement, de nombreux employeurs ou utilisateurs négligent souvent la formation à la sécurité des opérateurs de presses plieuses, et de nombreux fabricants de presses plieuses ne fournissent pas de dispositifs de protection de sécurité adéquats.
Le principal danger lié à l’utilisation des presses plieuses est que les opérateurs peuvent contourner les protections de sécurité et pénétrer dans la zone de pliage de la machine.
De plus, les pinces et le mouvement rapide de la butée arrière présentent également un risque pour les opérateurs.
Chaque fois qu’une nouvelle presse plieuse est installée, mise à niveau ou rénovée, les facteurs de risque associés à la presse plieuse doivent être réévalués.
Le temps de séjour des presses plieuses mécaniques et à volant d'inertie est relativement long, ce qui ne peut être réduit sans l'utilisation d'une technologie moderne de protection par rideau lumineux.
D’autre part, le temps d’arrêt des presses plieuses hydrauliques est plus court, ce qui permet la mise en œuvre de mesures de protection plus nombreuses.
Risques potentiels liés à l'utilisation d'une presse plieuse CNC
Les blessures courantes qui surviennent pendant Presse plieuse CNC l'utilisation comprend des blessures par écrasement et un contact avec les points de fonctionnement de la machine.
Ces dangers peuvent survenir lors de diverses activités telles que le réglage et l'ajustement de la machine, le pliage avec la presse plieuse, le nettoyage des blocages de la machine, la lubrification de la machine et l'exécution de la maintenance.
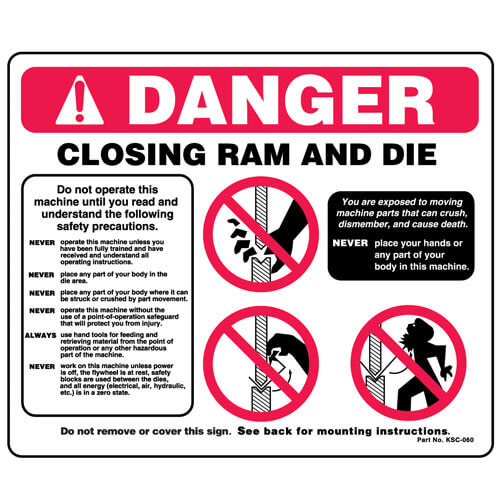
D'autres dangers courants incluent le fait de toucher la pédale de commande pendant le fonctionnement, d'être écrasé pendant la flexion et de se blesser en fermant mal les pièces concernées.
De plus, les personnes peuvent être pincées par la butée arrière ou blessées lors du changement du poinçon et de la matrice.
Précautions de sécurité de base
Avant d’utiliser la cintreuse, les employés doivent suivre une formation adéquate pour assurer leur sécurité.
La formation doit couvrir les procédures d’exploitation sûres, la connaissance de l’équipement et de ses dispositifs de protection, l’identification des dangers et les mesures de contrôle d’urgence.
Les opérateurs doivent être strictement surveillés pour garantir qu’ils respectent les règles établies.
Il est important de porter un équipement de protection individuelle approprié, tel que des gants et des lunettes, avant de commencer l'opération de pliage.
La zone autour de la machine doit être maintenue propre et exempte de toute obstruction susceptible de gêner le fonctionnement de la cintreuse.
Il est également important de mettre en service correctement la machine pour éviter les dysfonctionnements et la contamination.
Pendant le pliage, les opérateurs doivent rester vigilants et ne jamais laisser la cintreuse sans surveillance.
Protection par rideau lumineux infrarouge pour presses plieuses
La protection par rideau lumineux infrarouge est un dispositif de sécurité couramment utilisé dans les presses plieuses.
Le rideau lumineux, initialement conçu comme un équipement de test de produits, a depuis été adapté à la protection des machines.
Le rideau lumineux est un dispositif d’induction photoélectrique qui empêche le contact humain avec les zones dangereuses.
Il peut être installé à proximité des outillages d'une presse plieuse hydraulique et se compose d'un émetteur et d'un récepteur.
Le système de rideau lumineux doit être connecté au relais de surveillance de sécurité et au démarreur magnéto car il fait partie du circuit de commande de la machine.
En créant une zone de protection scellée grâce à un faisceau infrarouge, le rideau lumineux protège à la fois l'opérateur et les personnes à proximité.
Si un objet, comme la main d'un opérateur, traverse la zone de travail, la presse plieuse arrête de plier ou ne continue pas à fonctionner jusqu'à ce que l'objet soit retiré.
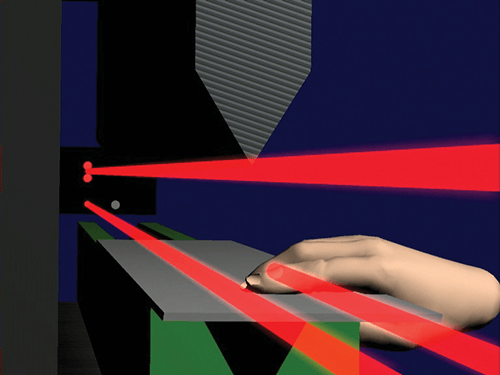
L'émetteur et le récepteur LED du rideau lumineux détectent l'objet et envoient un signal de sortie en cas d'interruption du plan lumineux.
Cependant, la distance de sécurité entre le rideau lumineux et la presse plieuse est incertaine et peut varier en fonction de l'installation, du type et de la fonction de freinage d'urgence du rideau lumineux.
Il existe également un risque de recevoir des signaux erronés pendant le processus de pliage.
Le rideau lumineux est un dispositif de protection courant utilisé avec les presses plieuses et est un type d'équipement d'induction photoélectrique conçu pour empêcher le contact humain avec les zones dangereuses.
Il fonctionne en créant une zone de protection scellée à proximité des outillages grâce à un faisceau infrarouge.
Si la main d'un opérateur pénètre dans la zone de travail, la presse plieuse arrête de plier ou ne continue pas à fonctionner jusqu'à ce que la main soit retirée.
Le rideau lumineux offre une protection non seulement aux personnes présentes dans la zone de travail, mais également à celles qui se trouvent à proximité.
Le système de rideau lumineux est connecté au relais de surveillance de sécurité et au démarreur magnéto, et il fait partie du circuit de commande de la machine.
Il déclenche le signal de sortie lorsqu'il détecte un objet, tel qu'un travailleur ou un autre objet, interrompant le plan lumineux.
De plus, le rideau lumineux a pour fonction de fermer automatiquement le système avant que le poinçon ne plie la pièce.
Il dispose également d'une fonction de flan flottant qui permet à la course de pliage de continuer sans s'arrêter.
De part et d'autre de la presse plieuse, les faisceaux infrarouges émis par le rideau lumineux sont synchrones et parallèles.
Le rideau lumineux peut être programmé ou non programmable.
Les rideaux lumineux programmables peuvent introduire la bride de la pièce dans le programme, ce qui annule le faisceau lumineux bloqué par la pièce et permet au vérin d'atteindre le point mort haut sans s'arrêter.
Les rideaux lumineux non programmables ne peuvent pas annuler le faisceau lumineux d'interférence et peuvent obliger l'opérateur à fermer le rideau lumineux, créant ainsi un danger.
Enfin, lors du pliage de très petites pièces, l'opérateur peut avoir besoin de les régler manuellement, ce qui signifie que le rideau lumineux ne fonctionnera pas lorsque l'opérateur se trouve devant la zone de travail.
Dispositif de commande à deux mains
Un dispositif de commande à deux mains est un outil efficace pour protéger les mains contre les blessures.
Il se compose d'un dispositif de commande vertical avec deux boutons de commande manuels.
Pour que la machine démarre, l'opérateur doit appuyer simultanément sur les deux boutons de commande.
Si les boutons ne sont pas enfoncés, la machine cessera de fonctionner.
Une fois les deux boutons enfoncés manuellement, la machine s'arrête lorsque le moule atteint une certaine position.
À ce stade, l'opérateur peut alors alimenter la pièce et utiliser la pédale de commande au lieu des boutons de commande manuelle pour lancer le pliage de la pièce.
Le dispositif de commande à deux mains permet à l'opérateur d'alimenter la pièce à une distance de sécurité du point de fonctionnement entre le poinçon et la matrice, protégeant ainsi les mains de l'opérateur contre les blessures causées par le poinçon et la matrice.
Le but de ce dispositif est d'empêcher les mains de l'opérateur d'entrer en contact avec le point de fonctionnement pendant que la machine est en fonctionnement.
Barrières de sécurité
Les protections latérales de la presse plieuse sont des barrières mobiles situées de chaque côté de la machine.
Ces protections empêchent l'opérateur d'entrer dans la zone de travail ou d'atteindre la jauge arrière de chaque côté, protégeant ainsi ses mains des blessures.
La protection arrière bloque l'accès à la machine par l'arrière, empêchant l'opérateur d'entrer en contact avec la jauge arrière.
Le boîtier de la presse plieuse et la barrière de verrouillage de la presse peuvent également être positionnés à une distance de sécurité pour éviter d'endommager la machine et de blesser l'opérateur par le personnel ou les objets.
Outils d'installation
Il existe des dangers potentiels pour l'opérateur lors de l'installation des outils, tels que la chute inattendue des outils et leur impact sur la main de l'opérateur ou le mouvement brusque du vérin de la machine.
Avant d'installer l'outillage ou tout autre outil, il est nécessaire de verrouiller le vérin en position haute fermée et de le relever jusqu'à la position la plus haute.
Avant d'éteindre l'interrupteur concerné, il est également nécessaire d'ajuster la position lors de l'installation d'autres outils.
Conclusion
Un entretien régulier est nécessaire pour la presse plieuse et un équipement de protection doit être porté pendant son utilisation.
La presse plieuse doit être équipée de dispositifs de sécurité appropriés et de panneaux d'avertissement clairs.
Le fabricant de la presse plieuse doit fournir du matériel de formation opérationnelle à ses clients.
Les employeurs doivent fournir une formation professionnelle préalable à l’opération à leurs opérateurs et établir des règles strictes pour l’utilisation de la presse plieuse.
L'utilisation d'une presse plieuse est une tâche complexe et une attention particulière doit être accordée aux considérations de sécurité.