Table des matières
Développement de la découpe laser
Le développement de la technologie de découpe laser a constitué une avancée significative dans les processus de fabrication et de fabrication. Voici un bref aperçu des étapes clés du développement de découpe laser:
Invention du laser (années 1960) : Le concept du laser (amplification de la lumière par émission stimulée de rayonnement) a été proposé pour la première fois par des scientifiques dans les années 1950, et le premier laser fonctionnel a été développé en 1960. Cette invention révolutionnaire a ouvert la voie à de nombreuses applications, notamment la découpe laser.
Premières expériences (années 1960-1970) : Au cours des premières années de la technologie laser, les chercheurs ont mené des expériences pour explorer ses applications potentielles. Les premières expériences de découpe laser impliquaient l'utilisation de lasers CO2 pour couper des matériaux tels que les métaux, les plastiques et les tissus.
Adoption industrielle (années 1980) : Dans les années 1980, les progrès de la technologie laser ont conduit à la commercialisation de systèmes de découpe laser pour les applications industrielles. Les lasers CO2 sont devenus le choix privilégié pour la découpe laser industrielle en raison de leur capacité à couper une large gamme de matériaux avec une grande précision et une grande efficacité.
Progrès dans la technologie laser (années 1990-2000) : Au cours des années 1990 et 2000, des progrès considérables ont été réalisés dans la technologie laser, ce qui a permis d'améliorer la vitesse de découpe, la précision et la polyvalence. Les lasers à fibre, qui utilisent des fibres optiques pour générer des faisceaux laser, sont apparus comme une alternative aux lasers CO2, offrant des avantages tels que des vitesses de découpe plus élevées et des coûts d'exploitation plus faibles.
Intégration de la technologie CNC : L'intégration de la technologie de commande numérique par ordinateur (CNC) aux systèmes de découpe laser a révolutionné l'industrie. Les contrôleurs CNC ont permis un contrôle précis du processus de découpe, permettant de découper facilement des formes et des motifs complexes.
Diversification des applications : À mesure que la technologie de découpe laser a évolué, ses applications se sont diversifiées dans divers secteurs, notamment l'automobile, l'aérospatiale, l'électronique, les appareils médicaux et la conception architecturale. La découpe laser est devenue la méthode privilégiée pour découper des motifs, des contours et des prototypes complexes dans ces secteurs.
Progrès en matière d’automatisation et de robotique : Ces dernières années, la tendance s'est orientée vers l'automatisation et l'intégration de la robotique dans les systèmes de découpe laser. La manutention automatisée des matériaux, le tri des pièces et le chargement et déchargement robotisés ont encore amélioré la productivité et l'efficacité des opérations de découpe laser.
Tendances émergentes : Les efforts de recherche et développement en cours continuent de stimuler l'innovation dans la technologie de découpe laser. Les tendances émergentes comprennent le développement de systèmes de découpe laser hybrides, la fabrication additive par dépôt laser et les avancées dans les sources laser et l'optique pour des performances de découpe améliorées.
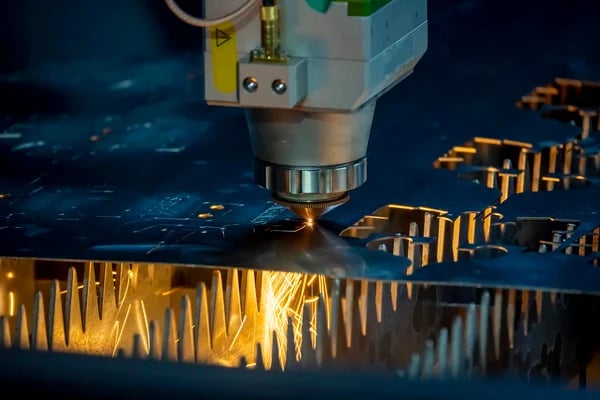
Qu'est-ce que la découpe laser et comment fonctionne-t-elle ?
Découpe laser Le procédé utilise un laser haute puissance qui est dirigé par l'intermédiaire d'un système optique et d'une commande numérique par ordinateur (CNC) pour orienter le faisceau ou le matériau. En règle générale, le processus utilise un système de contrôle de mouvement pour suivre un code CNC ou G du motif à découper sur le matériau. Le faisceau laser focalisé brûle, fond, se vaporise ou est emporté par un jet de gaz pour laisser un bord fini de surface de haute qualité.
Le faisceau laser est créé par la stimulation de matériaux laser par des décharges électriques ou des lampes à l'intérieur d'un récipient fermé. Le matériau laser est amplifié en étant réfléchi à l'intérieur par un miroir partiel jusqu'à ce que son énergie soit suffisante pour qu'il s'échappe sous forme d'un flux de lumière monochromatique cohérente. Cette lumière est focalisée sur la zone de travail par des miroirs ou des fibres optiques qui dirigent le faisceau à travers une lentille qui l'intensifie.
À son point le plus étroit, un faisceau laser mesure généralement moins de 0,0125 pouce (0,32 mm) de diamètre, mais des largeurs de trait aussi petites que 0,004 pouce (0,10 mm) sont possibles en fonction de l'épaisseur du matériau.
Lorsque le processus de découpe au laser doit commencer ailleurs que sur le bord du matériau, un processus de perçage est utilisé, par lequel un laser pulsé de haute puissance fait un trou dans le matériau, prenant par exemple 5 à 15 secondes pour brûler une feuille d'acier inoxydable de 0,5 pouce d'épaisseur (13 mm).
La découpe au laser utilise un laser haute puissance qui est dirigé par l'intermédiaire d'un système optique et d'une commande numérique par ordinateur (CNC) pour orienter le faisceau ou le matériau. En règle générale, le processus utilise un système de contrôle de mouvement pour suivre un code CNC ou G du motif à découper sur le matériau. Le faisceau laser focalisé brûle, fond, se vaporise ou est emporté par un jet de gaz pour laisser un bord fini de surface de haute qualité.
Le faisceau laser est créé par la stimulation de matériaux laser par des décharges électriques ou des lampes à l'intérieur d'un récipient fermé. Le matériau laser est amplifié en étant réfléchi à l'intérieur par un miroir partiel jusqu'à ce que son énergie soit suffisante pour qu'il s'échappe sous forme d'un flux de lumière monochromatique cohérente. Cette lumière est focalisée sur la zone de travail par des miroirs ou des fibres optiques qui dirigent le faisceau à travers une lentille qui l'intensifie.
À son point le plus étroit, un faisceau laser mesure généralement moins de 0,0125 pouce (0,32 mm) de diamètre, mais des largeurs de trait aussi petites que 0,004 pouce (0,10 mm) sont possibles en fonction de l'épaisseur du matériau.
Lorsque le processus de découpe au laser doit commencer ailleurs que sur le bord du matériau, un processus de perçage est utilisé, par lequel un laser pulsé de haute puissance fait un trou dans le matériau, prenant par exemple 5 à 15 secondes pour brûler une feuille d'acier inoxydable de 0,5 pouce d'épaisseur (13 mm).
Type de découpe laser
Ce procédé peut être décomposé en trois techniques principales : le laser CO2 (pour la découpe, l'alésage et la gravure) et le laser néodyme (Nd) et néodyme yttrium-aluminium-grenat (Nd:YAG), qui sont de style identique, le Nd étant utilisé pour l'alésage à haute énergie et à faible répétition et le Nd:YAG utilisé pour l'alésage et la gravure à très haute puissance.
Tous les types de lasers peuvent être utilisés pour le soudage.
Les lasers CO2 utilisent le passage d'un courant à travers un mélange gazeux (excitation CC) ou, plus couramment de nos jours, la nouvelle technique d'énergie radiofréquence (excitation RF). La méthode RF utilise des électrodes externes et évite ainsi les problèmes liés à l'érosion des électrodes et au placage du matériau de l'électrode sur la verrerie et l'optique qui peuvent se produire avec le CC, qui utilise une électrode à l'intérieur de la cavité.
Un autre facteur pouvant affecter les performances du laser est le type de flux de gaz. Les variantes courantes du laser CO2 comprennent le flux axial rapide, le flux axial lent, le flux transversal et la plaque. Le flux axial rapide utilise un mélange de dioxyde de carbone, d'hélium et d'azote circulant à grande vitesse par une turbine ou un ventilateur. Les lasers à flux transversal utilisent un simple ventilateur pour faire circuler le mélange de gaz à une vitesse inférieure, tandis que les résonateurs à plaque ou à diffusion utilisent un champ de gaz statique qui ne nécessite aucune pressurisation ni verrerie.
Différentes techniques sont également utilisées pour refroidir le générateur laser et les optiques externes, en fonction de la taille et de la configuration du système. La chaleur perdue peut être transférée directement dans l'air, mais un liquide de refroidissement est généralement utilisé. L'eau est un liquide de refroidissement fréquemment utilisé, souvent mis en circulation via un système de transfert de chaleur ou de refroidissement.
Un exemple de traitement laser refroidi par eau est un système à microjet laser, qui associe un faisceau laser pulsé à un jet d'eau à basse pression pour guider le faisceau de la même manière qu'une fibre optique. L'eau offre également l'avantage d'éliminer les débris et de refroidir le matériau, tandis que d'autres avantages par rapport à la découpe laser « à sec » incluent des vitesses de découpe élevées, une saignée parallèle et une découpe omnidirectionnelle.
Les lasers à fibre gagnent également en popularité dans le secteur de la découpe des métaux. Cette technologie utilise un milieu de gain solide plutôt qu'un liquide ou un gaz. Le laser est amplifié dans une fibre de verre pour produire une taille de spot bien plus petite que celle obtenue avec les techniques au CO2, ce qui le rend idéal pour la découpe de métaux réfléchissants.
Les avantages de la découpe laser incluent :
Précision : la découpe laser offre des niveaux élevés de précision et de répétabilité, ce qui la rend idéale pour produire des formes complexes et complexes avec des tolérances serrées.
Polyvalence : la découpe laser peut être utilisée sur une grande variété de matériaux, notamment les métaux, les plastiques, le bois, etc.
Rapidité : La découpe laser est un procédé rapide et efficace, permettant une production rapide de pièces et de composants.
Déchets de matériaux minimaux : la découpe laser produit des entailles étroites, ce qui entraîne un gaspillage de matériaux minimal et une meilleure utilisation des matériaux.
Bords nets : la découpe laser produit des bords nets et lisses sans nécessiter de processus de finition secondaires.
Découpe sans contact : Étant donné que le faisceau laser ne touche pas physiquement le matériau, le risque d’endommagement ou de déformation de la pièce est minime.
Automatisation : les systèmes de découpe laser peuvent être facilement intégrés à l’automatisation et à la robotique pour une productivité et une efficacité accrues.