Qu'est-ce qu'une presse plieuse à commande numérique
UN Presse plieuse à commande numérique Il s'agit d'une machine-outil utilisée dans les procédés de travail des métaux et de fabrication de tôles. Elle est spécialement conçue pour plier et façonner les tôles selon les formes et les angles souhaités. Contrairement aux presses plieuses manuelles classiques, les presses plieuses à commande numérique sont équipées de systèmes de commande numérique qui permettent un fonctionnement automatisé et un contrôle précis des paramètres de pliage.
composants clés d'une presse plieuse à commande numérique
Cadre : Le cadre assure le support structurel et la rigidité nécessaires aux opérations de pliage. Il abrite les mécanismes hydrauliques ou mécaniques chargés d'appliquer la force sur la pièce.
Outillage de pliage : Les machines utilisent divers outils, notamment des matrices supérieures et inférieures, pour réaliser les opérations de pliage. Ces ensembles d'outils sont sélectionnés en fonction des exigences de pliage spécifiques de la pièce.
Système de butée arrière : un système de butée arrière est constitué d'une série de butées réglables, ou doigts, positionnées derrière la zone de pliage. Il permet de positionner la pièce avec précision pour des pliages réguliers et reproductibles.
Système hydraulique : La plupart des machines sont alimentées par des systèmes hydrauliques qui génèrent la force nécessaire au pliage du métal. Le système hydraulique comprend des pompes, des vérins, des vannes et des actionneurs qui contrôlent le mouvement du vérin et de l'outillage de pliage.
Système de commande numérique (CN) : Le système CN d'une presse plieuse se compose de commandes électroniques, de moteurs et d'une interface utilisateur permettant aux opérateurs de programmer et de contrôler les opérations de pliage. Il comprend généralement un écran tactile ou un panneau de commande permettant de saisir les paramètres de pliage tels que l'angle, la longueur et l'épaisseur du matériau.
Caractéristiques de sécurité : les presses plieuses NC sont équipées de dispositifs de sécurité tels que des verrouillages, des rideaux lumineux et des boutons d'arrêt d'urgence pour garantir la sécurité de l'opérateur pendant le fonctionnement.
Les presses plieuses à commande numérique offrent plusieurs avantages par rapport aux presses plieuses manuelles, notamment des temps de réglage plus rapides, une productivité accrue, une plus grande précision et la possibilité de produire des plis et des formes complexes. Elles sont couramment utilisées dans divers secteurs tels que l'automobile, l'aérospatiale, l'électronique et la construction pour la fabrication d'une large gamme de composants et de produits métalliques.
Cet article explore chaque partie plus en détail.
Corps de presse plieuse
Le Presses plieuses à commande numérique Le châssis est constitué du soudage des montants gauche et droit, de la table de travail, des corps de support et des réservoirs de carburant. La table de travail est placée sous les montants gauche et droit, tandis que le réservoir de carburant est soudé à ces derniers.
Cette conception améliore la rigidité et la résistance du châssis, tout en élargissant la zone de dissipation de la chaleur de l'huile hydraulique.
Caractéristiques de la structure de la presse plieuse :
La structure de la presse plieuse est le cadre qui supporte le vérin et qui est soudé à la table inférieure, elle se compose généralement de deux parties avec une forme en « C » à l'arrière.
La structure entièrement soudée offre une résistance et une rigidité suffisantes.
L'huile hydraulique est transmise vers le haut, avec les cylindres situés aux deux extrémités de la presse plieuse installés sur le curseur, qui entraîne directement le travail coulissant.
Le bélier utilise la torsion pour assurer la synchronisation.
Une butée mécanique est utilisée, assurant stabilité et fiabilité.
La course du vérin est réglée par le contrôleur et peut être réglée manuellement avec précision, avec un affichage du compteur.
La conception du couronnement en forme de coin garantit une précision de pliage plus élevée.
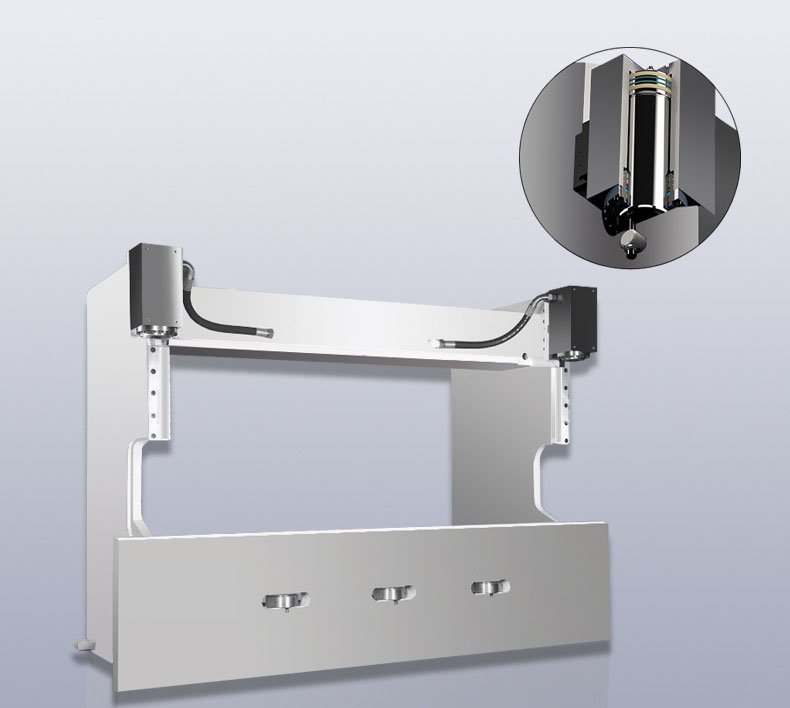
Contrôleur de presse plieuse
La commande numérique des presses plieuses est une caractéristique courante des machines-outils.
Les machines-outils à commande numérique ou machines-outils CN sont des machines-outils dont le fonctionnement est contrôlé par un ordinateur intégré à la machine.
Cet ordinateur gère les mouvements et les fonctions de la machine conformément à un programme de travail spécifique.
Grâce à un encodeur dans la commande numérique, elle mesure les positions de ses pièces mobiles et actionne des actionneurs, (moteurs, pistons hydrauliques ou autres), qui contrôlent les mouvements de la machine et positionnent l'outil à un point spécifique choisi arbitrairement.
Un mouvement donné de la machine mesuré par un codeur et contrôlé par un ordinateur au moyen d'un moteur capable de positionner la machine avec précision à un point arbitraire le long de la course disponible est appelé axe contrôlé ou simplement axe de la machine.
En plus de sélectionner les dimensions ou les caractéristiques d'une presse plieuse, un acheteur peut choisir parmi un certain nombre de types de commandes numériques différents, qui sont montés à une extrémité de la machine et constituent le principal point de contrôle à partir duquel la programmation de l'ensemble du système a lieu.
Les types de commandes numériques disponibles sur le marché diffèrent par le nombre d'axes qu'ils peuvent contrôler et par leur capacité à produire une simulation vidéo de la séquence de pliage.
Vérin de presse plieuse
Le vérin de la presse plieuse est constitué d'une plaque d'acier solide et est relié à la tige de piston située au centre des vérins hydrauliques gauche et droit. Le vérin est fixé à la plaque de connexion des plaques murales gauche et droite, et la tige de piston est entraînée par la force hydraulique pour déplacer le coulisseau vers le haut et vers le bas.
Pour garantir un positionnement précis du vérin au point mort haut, des règles à grille sont placées de chaque côté du vérin afin de transmettre les informations de position au contrôleur CN, qui ajuste ensuite la position. Cela garantit également le fonctionnement synchronisé du vérin.
Le vérin utilise une transmission hydraulique et son système se compose du vérin, d'un vérin hydraulique et d'une butée mécanique pour un réglage précis. Les vérins gauche et droit sont fixés au châssis, et le piston est actionné par la pression hydraulique pour déplacer le vérin de haut en bas. La butée mécanique est contrôlée par un système de commande numérique.
Accident vasculaire cérébral
Le trait indique le mouvement maximal disponible le long de l'axe Y. Ceci
la dimension est extrêmement importante pour vérifier la possibilité d'utiliser de grandes
poinçons. Dans de tels cas, l'opérateur doit vérifier que : [Lumière du jour – hauteur de la matrice
(de la base au fond en V) – hauteur du poinçon (de la poutre supérieure à la pointe du poinçon) –
épaisseur de la tôle < course de la machine.
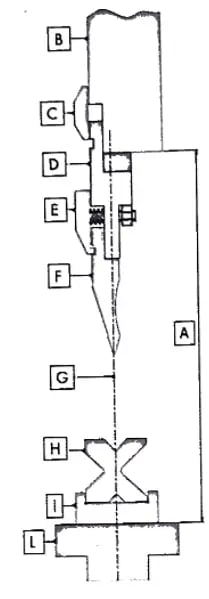
Le schéma ci-dessus montre une coupe transversale d'une presse plieuse avec un outil standard Promecam-Amada.
A → lumière du jour : distance entre le faisceau supérieur et la table
B → poutre supérieure : partie supérieure d'une presse plieuse
C → pince de poutre supérieure : pince montée sur la poutre supérieure pour maintenir les intermédiaires
D → intermédiaire : pièce de montage des poinçons sur la poutre supérieure
E→ pince intermédiaire : pince montée sur l'intermédiaire pour maintenir les poinçons
F→ poinçon : outil supérieur
G → axe machine : axe de pliage passant par la pointe du poinçon et le centre en V de la matrice
H → matrice : outil inférieur
I→ porte-matrice : pièce pour le serrage des matrices
L→table de presse plieuse : table de support des matrices.
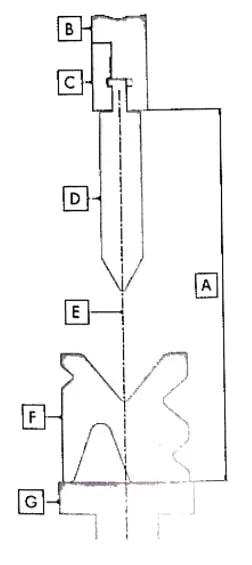
L'image ci-dessus, en revanche, montre une presse plieuse avec un outil axial (Trumpf, Beyeler, etc…). Dans ce cas, le poinçon est serré directement dans la poutre supérieure et l'axe de la presse plieuse traverse à la fois le poinçon et la pointe.
A → lumière du jour : distance entre le faisceau supérieur et la table
B → poutre supérieure : partie supérieure d'une presse plieuse
C → pince de poutre supérieure : pince montée sur la poutre supérieure pour maintenir les poinçons
D → poinçon : outil supérieur
E→ axe machine : axe de pliage passant par la pointe du poinçon et le centre en V de la matrice
F → matrice : outil inférieur
G → table de presse plieuse : table de support des matrices.