Le plieuse de panneaux est une machine avec des fonctions similaires à la presse plieuse mais qui est plus automatique et possède plus de fonctionnalités.
Dans le passé, des cintreuses manuelles étaient utilisées pour le pliage du métal.
Avec le progrès continu de la technologie, le formage de tôles est entré dans l’ère de l’automatisation.
Le pliage de tôles peut être divisé en centres de pliage manuel, semi-automatique et entièrement automatique.
Les systèmes de changement d'outils automatiques, les systèmes de mesure, etc., améliorent l'efficacité du pliage des métaux.
Puis est arrivée la plieuse de panneaux, dont les fonctions sont similaires à celles de la presse plieuse traditionnelle.
La lame de la cintreuse de panneaux peut former une bride dans le sens horizontal, et le support de flan dans l'autre sens peut maintenir le matériau stable.
Les lames de pliage standard permettent de réaliser de nombreux types de rayons. Le pliage de la plieuse à panneaux ne laisse pas de traces.
Par rapport à la pièce pliée de la presse plieuse, elle sera plus esthétique et plus propre.
Par rapport à la presse plieuse précédente, la cintreuse de panneaux présente les avantages d'être économique en main-d'œuvre et à grande vitesse.
La plieuse de panneaux peut effectuer des processus de pliage entièrement automatiques, y compris le chargement et le déchargement automatiques des outils, l'alimentation, la mesure, le pliage et la sortie.
Il a une course de pliage courte et une vitesse d'alimentation rapide et produit des pièces de haute précision.
Des outils spéciaux peuvent être utilisés pour des pliages complexes, tels que le sertissage et le pliage décalé.
Cependant, toutes les pièces ne conviennent pas à la plieuse de panneaux.
En général, il est préférable de produire des pièces de type boîte, car il peut plier le côté de la boîte entière en une seule fois.
De nos jours, une plieuse de panneaux ou une presse plieuse connectée à un robot peut atteindre une automatisation complète, mais leurs fonctions ne sont pas aussi complètes que celles d'un centre de pliage robotisé.
Comprendre les différences entre la plieuse de panneaux et la presse plieuse traditionnelle peut vous aider à choisir la bonne machine.
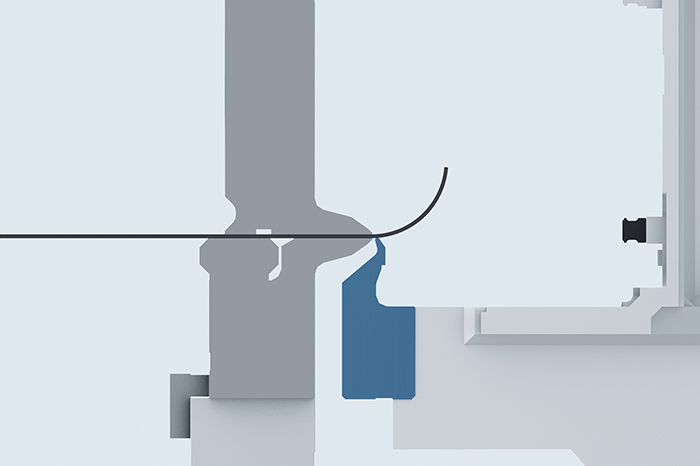
Comment fonctionne une plieuse de panneaux ?
Le principe de fonctionnement du plieuse de panneaux est différent de celui de la presse plieuse.
Lors de l'utilisation de la cintreuse de panneaux, l'opérateur n'a plus qu'à charger la tôle.
Le positionnement, le pliage et l'inversion de la pièce sont contrôlés par la machine et le logiciel.
La plieuse de panneaux n'enfonce pas la plaque métallique dans la matrice inférieure au moyen de poinçons.
La plieuse de panneaux doit fixer la plaque à l'aide d'une paire de lames et la plier de haut en bas pour former le profil final.
Lors du pliage d'un angle complexe, la lame oscille autour d'un seul point de pliage jusqu'à ce que l'angle souhaité soit atteint.
Il ne se déplace pas de haut en bas le long d'une ligne droite, ce qui est différent de la presse plieuse.
Après avoir positionné la plaque, la cintreuse de panneaux peut s'ajuster rapidement à la longueur d'outil correcte.
Lors du pliage, une fois la pièce positionnée, l'outil de serrage serre la pièce en place.
L'outil inférieur se déplace vers le haut pour plier dans une direction positive ; l'outil supérieur se déplace vers le bas pour plier dans la direction négative.
L'outil de pressage supérieur et l'outil de pressage inférieur serrent la tôle en place.
Mais ils ne plieront pas directement le métal, mais les lames supérieures et inférieures appliquent une pression pour le former.
La plaque métallique de la cintreuse de panneaux est placée sous la griffe de serrage, puis la griffe de serrage descend et serre la pièce.
Plus la plaque dépasse de l'autre côté, plus la bride produite par la gorge de la machine est haute.
La cintreuse de panneaux est très rapide et précise. Une fois la pièce positionnée, les outils de pliage se déplacent de haut en bas pour former une bride.
Lors du processus de pliage latéral, la griffe de serrage fait tourner la pièce et les outils se déplacent de haut en bas pour plier la plaque.
Le mouvement des outils détermine l'angle de pliage et le rayon de la pièce, ce qui permet de former un cintrage uniforme.
La lame de pliage forme plus de 90 degrés de matériau et l'outil tombe pour former le bouclage final.
Les pièces de type boîte, plates et de grande taille conviennent également à la cintreuse de panneaux.
Quelles sont les caractéristiques de la plieuse de panneaux ?
Avantages
La cintreuse de panneaux dispose d'un changeur d'outils automatique, ce qui réduit le temps d'installation.
Le pliage de toutes les pièces peut être réalisé grâce à un jeu complet d'outils.
La zone d'interaction des outils de la plieuse de panneaux sur la surface de la plaque métallique est très petite.
Il y a peu de rayures sur la surface de la pièce ainsi réalisée.
L'usure de l'outil de la cintreuse de panneaux est également très faible car le frottement entre l'outil et la surface métallique est faible.
L'ensemble du processus de la cintreuse de panneaux peut être réalisé automatiquement, ce qui permet d'économiser des ressources humaines.
Le changement d'angle de pliage de la cintreuse de panneaux est formé par le mouvement des lames supérieures et inférieures.
Ses outils ne sont donc pas aussi compliqués que ceux des presses plieuses.
La cintreuse de panneaux dispose d'un changeur d'outils automatique, qui peut changer rapidement d'outils pour ajuster l'angle de pliage.
Certaines grandes pièces à brides positives et négatives conviennent à la fabrication avec une cintreuse de panneaux.
Si la cintreuse de panneaux peut régler automatiquement le serre-flan, un seul opérateur peut la manipuler.
La plieuse de panneaux applique uniquement une pression sur la plaque métallique à travers les lames supérieures et inférieures.
Cette méthode de pliage rend le changement et le retour élastique de la plaque métallique au cours du processus de pliage moins évidents.
Il peut donc plier tout le côté de la boîte en une seule fois.
La méthode de pliage de la plieuse de panneaux est très adaptée à la production de boîtes, de couvercles et d'articles similaires.
L'utilisation d'une presse plieuse pour fabriquer de petites pièces pose certains problèmes de sécurité.
Alors que la cintreuse de panneaux peut produire des profils plus petits en serrant des griffes ou en manipulant manuellement.
Inconvénients
La cintreuse de panneaux présente également certains inconvénients.
La cintreuse de panneaux est plus chère, elle est donc moins populaire que la presse plieuse.
La cintreuse de panneaux ne peut pas gérer des plaques plus épaisses comme la presse plieuse.
En raison de la profondeur de gorge et de la hauteur d'ouverture limitées de la cintreuse de panneaux, elle est plus adaptée à la production de brides plus petites.
La position de l'outil de serrage et de la lame de pliage de la cintreuse de panneaux rend difficile la réalisation de pliages internes sur la machine.
Application
Plieuse de panneaux est très adapté à la production de pièces carrées, grandes et rectangulaires.
Ces pièces ont des exigences élevées en matière d'apparence et de forme.
La surface de la pièce fabriquée par la plieuse de panneaux présente peu de rayures.
Tels que les réfrigérateurs, les climatiseurs et autres appareils électriques, ainsi que les portes, les ascenseurs, les meubles en métal, etc.
Lors de la sélection d'une plieuse de panneaux, il est très important de savoir à quelles pièces sa méthode de pliage est adaptée.
Conclusion
Par rapport à la presse plieuse, la cintreuse de panneaux possède des fonctions plus complètes, une automatisation plus élevée et un fonctionnement plus sûr.
Le coût de la presse plieuse est bien inférieur à celui de la cintreuse de panneaux, mais le fonctionnement de la machine à panneaux est simple.
L'utilisation d'une cintreuse de panneaux peut également réduire le coût de la main-d'œuvre et des ressources matérielles grâce à une production par lots efficace.
ADH produit diverses presses plieuses CNC ainsi que diverses cintreuses de panneaux pour répondre aux différents besoins des clients.
Nos experts produits peuvent vous fournir des suggestions pour choisir la machine la plus appropriée et la plus rentable.