L’importance des positions focales dans découpe laser Les opérations de découpe laser ne peuvent pas être surestimées, car elles ont un impact direct sur la qualité, l'efficacité et la précision du processus de découpe. La position focale fait référence au point exact auquel le faisceau laser converge vers son plus petit diamètre, appelé point focal. C'est à cet endroit que le faisceau laser fournit une densité énergétique maximale, permettant des performances de découpe optimales. Voici plusieurs raisons clés soulignant l'importance des positions focales dans les opérations de découpe laser :
Mise au point de la découpe laser
Focaliser les faisceaux laser
Chaque fabricant peut avoir son opinion sur ce qui est l'élément le plus important dans découpe laser. Pensez-vous que cela est dû au maintien de la plus petite taille de spot et d'une orientation de la lentille perpendiculaire à l'axe du faisceau laser ? Si vous avez répondu oui, vous avez partiellement raison, mais de nombreux autres facteurs doivent être pris en compte en ce qui concerne les propriétés du faisceau laser et les applications de découpe. Le maintien des positions de mise au point dans le matériau est essentiel à la répétabilité des paramètres de découpe laser et à la production d'une qualité de bord constante.
Par exemple, lorsqu'il s'agit de matériaux épais, il est en fait nécessaire de créer un motif de brûlure plus large pour créer un canal plus large, qui est nécessaire pour supporter un plus grand volume de matériau fondu qui doit être expulsé pendant le processus de découpe. Pour créer ce motif de brûlure élargi, vous focalisez le faisceau soit au-dessus, soit au-dessous de la surface du matériau en fonction du gaz d'assistance. Par conséquent, focaliser un petit point sur la surface est généralement une approche moins efficace pour les matériaux plus épais.
Cependant, pour les matériaux plus fins, un petit point focalisé sur la surface du matériau est beaucoup plus efficace qu'un point plus grand, car moins de matériau est impliqué et, par conséquent, un canal plus large n'est pas nécessaire.
Un facteur très important à prendre en compte lors de la découpe au laser est l'utilisation d'un gaz d'assistance, tel que l'oxygène, l'azote ou l'air comprimé. Chaque gaz possède des propriétés spécifiques liées à l'accélération du processus de combustion, à l'évacuation du matériau en fusion, ou aux deux.
Dans la découpe laser, les gaz auxiliaires favorisent deux réactions spécifiques : exothermique ou endothermique. Les règles de focalisation varient selon le type de réaction et de gaz utilisé.

Mise au point pour les réactions exothermiques
Les réactions exothermiques sont créées par l'utilisation d'un gaz aux propriétés accélératrices, comme l'oxygène. Lors de ce type de réaction, l'énergie intense du faisceau laser vaporise – ou fait littéralement bouillir – le matériau découpé, tandis que l'oxygène réagit vigoureusement avec le matériau fondu à l'état liquide. Lors de la découpe haute pression assistée par oxygène, le matériau de base est porté à une température si élevée que sa conversion en vapeur thermique est presque complète.
Les règles de focalisation pour soutenir les réactions exothermiques nécessitent que les positions de focalisation soient au-dessus de la surface pour les matériaux épais ou juste dans la surface supérieure pour les matériaux plus minces.
Lorsque le foyer est placé au-dessus du matériau, vous utilisez généralement une faible pression et un faible volume pour aider à liquéfier puis à expulser le matériau fondu (environ 6 à 8 livres par pouce carré à 40 pieds cubes par heure). En fait, très peu de matériau est vaporisé car le petit volume d'oxygène est incapable de supporter une vaporisation complète. Lorsque le foyer est placé juste à la surface du matériau, vous utilisez généralement une pression élevée et un volume élevé (environ 60 PSI à 80 CFH). Cela suffit à supporter une vaporisation vigoureuse du matériau.
C'est pourquoi, lors de l'inspection de la plupart des tables de découpe où sont principalement découpés des matériaux fins, on constate très peu d'accumulation de matière sur les supports. En revanche, les tables de découpe utilisées pour le traitement de matériaux plus épais présentent un volume de matière accumulé beaucoup plus important sur leurs supports.
Mise au point pour les réactions endothermiques
Les réactions endothermiques, en revanche, se produisent lorsque l'on utilise un gaz aux propriétés inertes ou non réactives. L'azote et l'argon entrent dans cette catégorie.
Lors de ce type de réaction, le gaz ne fait que favoriser l'évacuation du matériau fondu à travers le canal de coupe. Le processus endothermique dépend fortement de l'énergie brute du faisceau laser focalisé pour amener rapidement le métal de base à l'état fondu et créer le canal de coupe approprié. Cela permet au gaz inerte d'expulser le matériau liquéfié à travers le canal de coupe, laissant une surface de coupe nette sans adhérence de scories.
Les règles de focalisation favorisant les réactions endothermiques exigent que les positions focales soient situées au niveau du fond du matériau, ou juste en dessous. Maintenir la focalisation sous le matériau crée une légère forme de V dans le canal de coupe, permettant au gaz à haute pression de comprimer le matériau en fusion à grande vitesse à travers le canal de coupe et de l'expulser par le fond du canal.
Les réactions endothermiques nécessitent un volume et une pression élevés pour permettre une évacuation rapide du matériau fondu. Les volumes typiques peuvent commencer à 350 CFH pour les matériaux minces et atteindre plus de 3 000 CFH pour les matériaux plus épais. Les pressions peuvent commencer à 140 PSI pour les matériaux minces et monter jusqu'à plus de 300 PSI pour les matériaux plus épais.
L'utilisation d'air comprimé comme gaz d'assistance produit simultanément des réactions endothermiques et exothermiques. Cependant, le volume d'air étant principalement composé d'azote (environ 78 %), il s'agit principalement d'une réaction endothermique, le faible volume d'oxygène (environ 20 %) créant une réaction exothermique simultanée, mais plus faible. Il en résulte une fusion plus rapide du matériau de base grâce aux propriétés réactives de l'oxygène. Le reste de l'air est essentiellement inerte et ne contribue qu'à la réaction endothermique produite par l'azote.
La découpe à l'air comprimé donne les meilleurs résultats lorsque la position de mise au point est maintenue au centre de l'épaisseur du matériau.
Effets de faisceau brut
Tout comme l'intensité du soleil affecte la capacité de la loupe à focaliser et à créer un point focal efficace, le faisceau laser brut influence la capacité de focalisation de son énergie et la taille du point focal obtenu. En règle générale, plus le diamètre du faisceau brut est grand, plus le diamètre de la ceinture focale résultante est important et plus le point focal est éloigné de la lentille.
Une autre façon de modifier efficacement la taille du spot consiste à utiliser un objectif avec une distance focale effective (EFL) différente. Cela crée non seulement une taille de spot différente, mais également une profondeur de champ (DOF) différente, comme illustré dans la Figure 3. Gardez à l'esprit que la DOF ne se limite pas à l'endroit où le faisceau est le plus petit (taille focale), mais comprend également une plage juste avant et après la plus petite taille de spot.
À titre d'exemple de modification de la taille du spot et de la profondeur de champ, prenons un faisceau laser CO2 d'une longueur d'onde de 10 600 nm, d'un diamètre de faisceau brut de 20 mm et d'un M2 de 2. Si nous faisons passer ce faisceau à travers une lentille de 3,75 pouces (95,25 mm), le diamètre au niveau de la taille focale serait d'environ 128 microns (0,128 mm). Maintenant, si nous remplaçons une lentille de 5 pouces (127 mm), en utilisant le même faisceau brut de 20 mm, le diamètre au niveau de la taille focale serait de 170 microns (0,170 mm). Simultanément, un changement de profondeur de champ entre les deux lentilles se produirait. La lentille de 3,75 pouces aurait une profondeur de champ d'environ 1,2 mm, contre une profondeur de champ de 2,16 mm pour la lentille de 5 pouces.
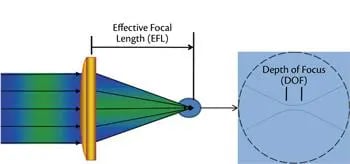
Un autre facteur pouvant modifier la projection du point focal du faisceau est la modification du front d'onde avant son impact sur la lentille. Le front d'onde du faisceau brut peut être décrit comme convergent, parallèle ou divergent. Dans le cas d'un front d'onde convergent, le faisceau rétrécit au fur et à mesure de sa propagation. Lorsque ce front d'onde convergent frappe la lentille, la projection focale résultante est plus courte que celle d'un front d'onde parallèle, en raison du diamètre plus petit du faisceau projeté au sommet de la lentille. Inversement, la focalisation d'un front d'onde divergent entraîne une projection focale plus longue que celle d'un front d'onde parallèle, en raison du diamètre plus grand du faisceau projeté au sommet de la lentille.
Applications concrètes
Il est important de contrôler tous les aspects liés au maintien des projections de points de focalisation appropriées. Vous devez vous assurer que le faisceau brut au niveau du résonateur optique est en bon état et qu'il est correctement délivré à la lentille. L'utilisation d'une lentille à distance focale appropriée peut modifier la vitesse à laquelle le matériau est fondu et l'épaisseur qui peut être traitée. Une lentille à courte distance focale, telle qu'une lentille EFL de 3,75 pouces, est plus efficace jusqu'à une épaisseur maximale de calibre 12 ou 0,104 pouce. Une lentille de 5 pouces est plus efficace jusqu'à une épaisseur maximale de 0,250 pouce. Pour les matériaux plus épais, utilisez une lentille de 7,5 pouces jusqu'à un maximum de 1,25 pouce et une lentille de 10 pouces jusqu'à un maximum de 1,312 pouce pour obtenir la coupe la plus efficace.
Un véritable gain de temps consiste à utiliser un EFL qui vous permet de couvrir la majeure partie de votre production quotidienne sans avoir à changer d'objectif. L'utilisation d'un objectif de 7,5 pouces vous permettra, dans la plupart des cas, d'atteindre tous les objectifs liés au maintien d'une mise au point optimale, de calibre 16 à 1 pouce d'épaisseur, tout au long de la journée de production.
Comme mentionné précédemment, le choix du gaz d'assistance a beaucoup à voir avec la façon dont votre position focale sera déterminée dans le matériau. La découpe laser assistée par oxygène (exothermique) nécessitera que les positions focales soient juste à la surface ou au-dessus de la surface du matériau. Très peu de changements de focale sont nécessaires, sauf si vous passez d'une découpe haute pression à une découpe basse pression, car la focale est toujours sur ou près de la surface du matériau et n'est donc pas affectée par les changements d'épaisseur du matériau. D'autre part, la découpe laser assistée par azote (endothermique) dépend fortement de la focale en fonction de l'épaisseur du matériau à traiter, car la focale est au niveau ou près du fond du matériau.
Dans les deux cas, tous les points focaux de base peuvent être satisfaits en utilisant un dispositif de mise au point automatique CNC, tel qu'un miroir adaptatif.
Un miroir adaptatif fonctionne en modifiant la forme de sa surface par l'application d'une pression sur son dos. À l'état normal, sans pression, la surface du miroir adaptatif est concave. Sous l'effet de la pression, la surface passe de concave à plane, puis à convexe. La modification de la forme du miroir modifie le front d'onde du faisceau et, par conséquent, la taille du faisceau sur la lentille et la position focale projetée dans le matériau.
Un autre avantage majeur de l’autofocus est la possibilité de modifier la position focale de manière dynamique pendant le processus de perçage, ce qui permet un apport d’énergie maximal dans l’épaisseur du matériau et réduit les temps de perçage globaux.
Les progrès réalisés dans les technologies de découpe laser, qui permettent d'améliorer le rendement et la productivité, se poursuivent encore aujourd'hui. Cependant, ce qui reste très important, c'est la transmission du faisceau brut à la lentille et le maintien des positions focales appropriées, en fonction de l'application.
Si la position focale et les formes de projection appropriées sont maintenues dans le matériau à traiter, les exigences restantes nécessaires pour produire une découpe homogène et de haute qualité sont minimisées. Cela permet de gagner du temps de configuration tout en maintenant une productivité et un débit constants.