What is Press Brake Follow-up Device?
UN Presse plieuse Follow-up Device is primarily used in metal fabrication processes, particularly in sheet metal bending operations performed on press brake machines. Its main purpose is to automate and control the positioning of the workpiece during bending, ensuring precision, consistency, and efficiency in the manufacturing process.
What is the Follow-up Device Used For
Here are some specific applications and uses of a Presse plieuse Follow-up Device:
Pliage de tôles: The follow-up device is used to accurately position the back gauge or back stop relative to the bending tooling and the workpiece. This ensures that the bends are made at the correct locations and angles, resulting in accurately formed sheet metal components.
Complex Bending Operations: In applications where multiple bends are required on a single workpiece or where complex shapes need to be formed, the follow-up device helps maintain precise positioning throughout the bending sequence.
High-Volume Production: For manufacturing environments with high production volumes, the follow-up device enables efficient and repeatable bending processes, reducing setup times and increasing throughput.
Custom Fabrication: In custom fabrication projects where tight tolerances and intricate geometries are required, the follow-up device ensures that each bend is made according to the specified dimensions and design requirements.
Prototype Development: Even in prototype or small-batch production scenarios, the follow-up device helps achieve consistent results, allowing manufacturers to quickly iterate and refine their designs.
Automotive, Aerospace, and Industrial Components: Press Brake Follow-up Devices are commonly used in industries such as automotive, aerospace, and general manufacturing for producing a wide range of components and parts, including brackets, panels, enclosures, chassis, and structural elements.
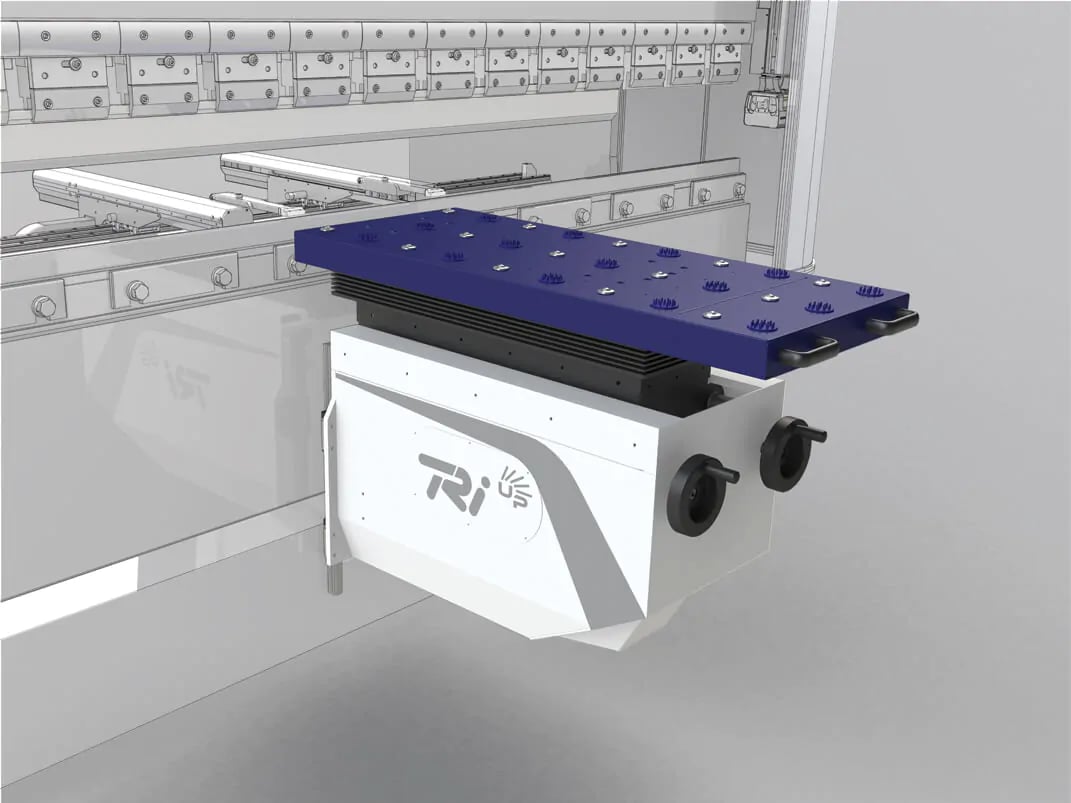
How Press Brake Follower Works
A Press Brake Follow-up Device, also known as a back gauge system or CNC back gauge, is a crucial component in modern press brake machines. It enhances precision and efficiency in bending operations by automating the positioning of the workpiece during bending. Here's how it works:
Installation: The follow-up device is mounted on the press brake machine behind the bending tooling. It consists of a linear guide or rail system along which a back gauge finger or stop can move horizontally.
Programmation: The operator inputs the desired bending dimensions, angles, and sequences into the press brake's CNC control system. This information includes the thickness of the material, the desired bend angle, and the location of bends along the workpiece.
Positionnement: As the operator loads the workpiece onto the press brake, the follow-up device automatically positions the back gauge finger according to the programmed dimensions. The back gauge finger moves along the linear guide to the specified location, ensuring accurate positioning of the workpiece relative to the bending tooling.
Processus de pliage: Once the workpiece is correctly positioned, the press brake's ram descends to apply the bending force to the material. The bending tooling presses the workpiece against the back gauge finger, ensuring precise alignment and consistent bending angles across multiple bends.
Feedback Control: During the bending process, the follow-up device continuously monitors the position of the back gauge finger relative to the workpiece. It provides feedback to the CNC control system, which adjusts the back gauge position as needed to maintain accuracy, especially when bending complex shapes or multiple bends on the same workpiece.
Caractéristiques de sécurité: Many modern press brake follow-up devices incorporate safety features such as light curtains or sensors to prevent collisions between the back gauge finger and the operator or other objects in the workspace. These safety mechanisms help ensure safe operation and protect both the equipment and personnel.
Overall, a Press Brake Follow-up Device streamlines the bending process, reduces setup time, minimizes material waste, and improves bending accuracy and repeatability. It is an indispensable tool for modern sheet metal fabrication operations seeking efficiency and precision in bending operations.