UN presse plieuse hydraulique Il s'agit d'un type de presse plieuse qui utilise la force hydraulique pour plier et façonner la tôle. Il s'agit d'un outil polyvalent et largement utilisé dans les industries de la métallurgie et de la fabrication pour former divers composants avec précision et efficacité. Les presses plieuses hydrauliques offrent des avantages en termes de contrôle, de flexibilité et de facilité d'utilisation par rapport à leurs homologues mécaniques.
Voici les principales caractéristiques et composants d’une presse plieuse hydraulique :
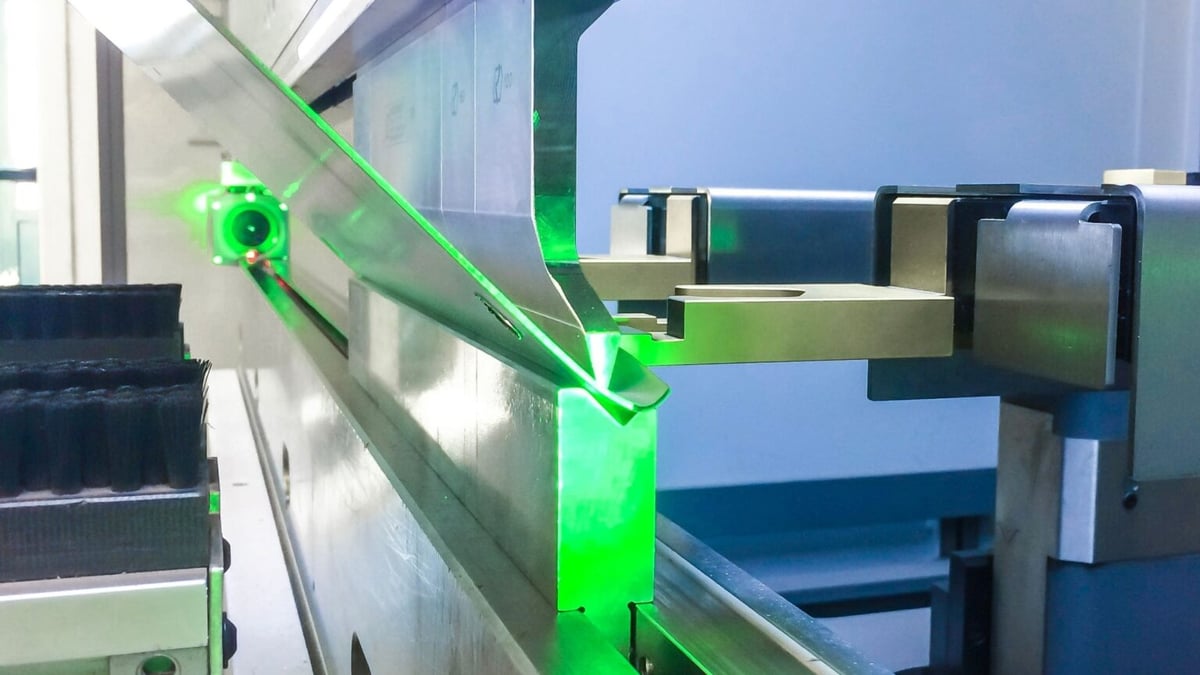
1.Système hydraulique :
Le cœur d'une presse plieuse hydraulique est son système hydraulique, qui se compose de vérins hydrauliques, d'une pompe hydraulique et d'un réservoir de fluide. Le fluide hydraulique est pressurisé par la pompe et utilisé pour actionner les vérins, générant la force nécessaire au pliage.
2. Cylindre et vérin :
Les presses plieuses hydrauliques sont équipées d'un ou plusieurs vérins hydrauliques qui entraînent un vérin (également appelé coulisseau) vers le bas. Le vérin porte l'outil supérieur, souvent appelé poinçon, qui entre en contact avec la tôle, appliquant la force de pliage.
2. Lit et matrice :
Le banc de la presse plieuse constitue le support inférieur de la tôle pendant le processus de pliage. La matrice, montée sur le banc, sert d'outil inférieur et permet de déterminer la forme finale du pli.
2. Butée arrière :
De nombreuses presses plieuses hydrauliques sont équipées d'un système de butée arrière, qui est un ensemble de doigts ou de butées réglables positionnés derrière la matrice. La butée arrière permet de positionner avec précision la tôle, garantissant des angles de pliage cohérents sur plusieurs pièces.
3. Système de contrôle :
Presses plieuses hydrauliques Les presses plieuses CNC peuvent être équipées de systèmes manuels, semi-automatiques ou entièrement CNC (commande numérique par ordinateur) pour contrôler le processus de pliage. Les presses plieuses CNC offrent des capacités de précision et d'automatisation, permettant des séquences de pliage complexes et une configuration rapide des outils.
4. Caractéristiques de sécurité :
Les presses plieuses hydrauliques sont équipées de dispositifs de sécurité tels que des protections, des boutons d'arrêt d'urgence et des verrouillages de sécurité pour assurer la sécurité de l'opérateur pendant le fonctionnement de la machine.
5. Avantages des presses plieuses hydrauliques :
Polyvalence : les presses plieuses hydrauliques peuvent gérer une large gamme de matériaux et d'épaisseurs, ce qui les rend polyvalentes pour diverses applications.
Précision : les systèmes hydrauliques assurent un contrôle précis de la force de pliage, ce qui permet des opérations de pliage précises et répétables.
Facilité d'utilisation : les presses plieuses hydrauliques sont généralement plus faciles à installer et à utiliser que les presses plieuses mécaniques.
Fonctionnement silencieux : les systèmes hydrauliques fonctionnent plus silencieusement que les systèmes mécaniques, contribuant ainsi à un environnement de travail plus silencieux.
7Applications :
Les presses plieuses hydrauliques sont utilisées dans des secteurs tels que l'automobile, l'aérospatiale, la construction, l'électronique et la fabrication de métaux. Elles conviennent à la production d'une variété de composants, notamment des supports, des boîtiers, des châssis et d'autres pièces avec des courbures précises.
En résumé, une presse plieuse hydraulique est une machine puissante et flexible utilisée pour plier des tôles. Son système hydraulique fournit une force contrôlée, permettant des processus de formage des métaux précis et efficaces dans diverses applications de fabrication.
En quoi une presse plieuse hydraulique diffère-t-elle des autres presses plieuses ?
Une presse plieuse hydraulique diffère des autres types de presses plieuses, principalement des presses plieuses mécaniques, en termes de source d'alimentation et de système de contrôle. Voici les principales différences entre une presse plieuse hydraulique et les autres presses plieuses :
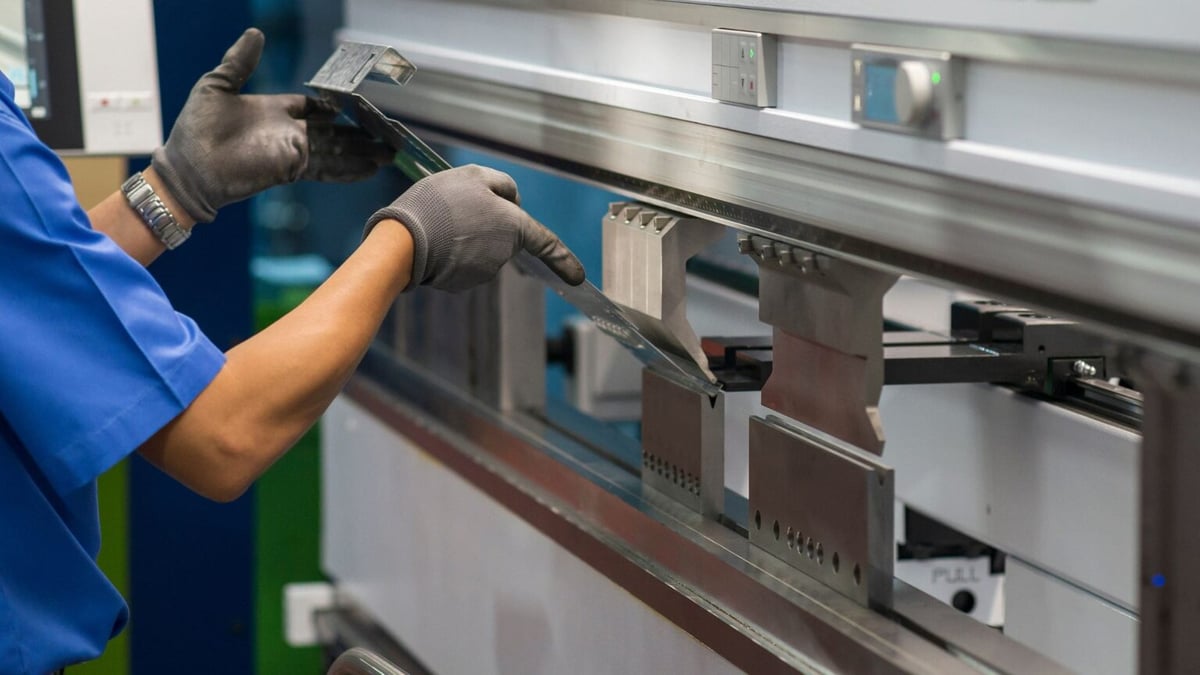
1. Source d'alimentation :
1.1 Presse plieuse hydraulique :
Les presses plieuses hydrauliques utilisent un système hydraulique pour générer la force nécessaire au pliage. Des vérins hydrauliques, alimentés par un fluide hydraulique pressurisé par une pompe, entraînent le vérin vers le bas pour appliquer une force sur la tôle.
1.2 Presse plieuse mécanique :
Les presses plieuses mécaniques, au contraire, utilisent un système mécanique avec un volant d'inertie et un embrayage pour générer la force. Le volant d'inertie stocke l'énergie et, lorsqu'il est engagé par l'embrayage, il entraîne le vérin vers le bas pour effectuer l'opération de pliage.
2. Génération de force :
2.1 Presse plieuse hydraulique :
Les presses plieuses hydrauliques assurent une application fluide et constante de la force tout au long du processus de pliage. Le système hydraulique permet un contrôle et un réglage précis de la force, contribuant ainsi à des pliages précis et répétables.
2.2 Presse plieuse mécanique :
Les presses plieuses mécaniques génèrent de la force grâce à l'énergie cinétique stockée dans le volant rotatif. Bien qu'elles puissent fournir une force élevée, l'application de la force peut ne pas être contrôlée avec autant de précision que dans les systèmes hydrauliques.
3. Système de contrôle :
3.1 Presse plieuse hydraulique :
Les presses plieuses hydrauliques peuvent être équipées de systèmes manuels, semi-automatiques ou entièrement CNC (commande numérique par ordinateur). Les presses plieuses hydrauliques CNC offrent des fonctions de contrôle avancées, permettant aux opérateurs de programmer et d'automatiser des séquences de pliage complexes.
3.2 Presse plieuse mécanique :
Les presses plieuses mécaniques sont généralement équipées de systèmes de commande manuels ou semi-automatiques. Les capacités CNC sont moins courantes sur les presses plieuses mécaniques et peuvent nécessiter davantage de réglages manuels pendant le fonctionnement.
4. Flexibilité et polyvalence :
4.1 Presse plieuse hydraulique :
Les presses plieuses hydrauliques sont connues pour leur polyvalence et leur capacité à traiter une large gamme de matériaux et d'épaisseurs. Elles conviennent à diverses applications de pliage et sont couramment utilisées dans la fabrication métallique moderne.
4.2 Presse plieuse mécanique :
Les presses plieuses mécaniques peuvent avoir des limites en termes de polyvalence des matériaux et sont souvent préférées pour des tâches de pliage plus simples ou spécifiques.
Facilité d'utilisation :
4.3 Presse plieuse hydraulique :
Les presses plieuses hydrauliques sont généralement considérées comme plus faciles à installer et à utiliser, en particulier avec la disponibilité des systèmes CNC. Elles offrent une plus grande flexibilité et une plus grande facilité d'utilisation pour les opérateurs.
Presse plieuse mécanique :
Les presses plieuses mécaniques peuvent nécessiter davantage de réglages manuels et une réflexion approfondie lors de la configuration, ce qui les rend potentiellement moins conviviales que les presses plieuses hydrauliques.
Niveau de bruit :
4.4 Presse plieuse hydraulique :
Les systèmes hydrauliques fonctionnent plus silencieusement que les composants mécaniques des presses plieuses mécaniques, contribuant ainsi à un environnement de travail plus silencieux.
4.5 Presse plieuse mécanique :
Les presses plieuses mécaniques peuvent être plus bruyantes en raison du fonctionnement du volant d'inertie et d'autres composants mécaniques.
En résumé, la principale différence entre une presse plieuse hydraulique et d'autres presses plieuses, telles que les presses plieuses mécaniques, réside dans la source d'alimentation (hydraulique ou mécanique) et le système de contrôle. Les presses plieuses hydrauliques sont souvent préférées pour leur précision, leur polyvalence et leur facilité d'utilisation dans diverses applications de formage des métaux.
Quels sont les principaux composants d’une presse plieuse hydraulique ?
Une presse plieuse hydraulique est composée de plusieurs composants clés qui fonctionnent ensemble pour plier et façonner la tôle avec précision. La compréhension de ces composants est essentielle pour faire fonctionner et entretenir efficacement la machine. Voici les composants clés d'une presse plieuse hydraulique :
1.Système hydraulique :
Le système hydraulique est le cœur de la presse plieuse, chargé de générer et de contrôler la force de pliage. Il comprend des composants tels que :
Pompe hydraulique : Pressurise le fluide hydraulique.
Vérins hydrauliques : Actionnent le vérin (coulissant) pour appliquer une force sur la tôle.
Réservoir de liquide hydraulique : stocke le liquide hydraulique et aide à dissiper la chaleur.
2.Ram (glissière) :
Le coulisseau est l'élément mobile qui porte l'outil supérieur, souvent appelé poinçon. Il descend sous l'effet de la force hydraulique pour plier la tôle contre l'outil inférieur (matrice). Le mouvement du coulisseau est contrôlé par le système hydraulique.
3. Lit et cadre :
Le banc fournit le support fixe de la tôle pendant le pliage. Il est monté sur le châssis, ce qui confère à la presse plieuse son intégrité structurelle. Le châssis abrite également les vérins hydrauliques et d'autres composants critiques.
4. Matrice et poinçon :
La matrice et le poinçon sont les outils supérieurs et inférieurs utilisés pour façonner la tôle. La matrice est montée sur le banc, tandis que le poinçon est fixé au vérin. L'espace entre la matrice et le poinçon détermine l'angle et le rayon de pliage.
5. Butée arrière :
La butée arrière est un système de doigts ou de butées réglables positionnés derrière la matrice. Elle permet de positionner la tôle avec précision, garantissant des angles de pliage cohérents sur plusieurs pièces. Les presses plieuses CNC sont souvent équipées de butées arrière programmables pour une automatisation accrue.
6. Système de contrôle :
Le système de contrôle régule et coordonne le fonctionnement de la presse plieuse hydraulique. Il peut être manuel, semi-automatique ou entièrement CNC (commande numérique par ordinateur). Les systèmes CNC offrent des fonctionnalités avancées telles que des séquences de pliage programmables, un contrôle d'angle et l'automatisation.
7. Caractéristiques de sécurité :
Les presses plieuses hydrauliques sont équipées de dispositifs de sécurité pour protéger les opérateurs et garantir un fonctionnement sûr. Ces caractéristiques peuvent inclure :
Bouton d'arrêt d'urgence : arrête le fonctionnement de la machine en cas d'urgence.
Protections de sécurité : Fournir des barrières physiques pour protéger les opérateurs des pièces mobiles.
Dispositifs de sécurité : Empêchent le fonctionnement de la machine si les dispositifs de sécurité ne sont pas activés.
8. Socle ou panneau de commande :
Le socle ou panneau de commande abrite les commandes permettant de faire fonctionner la presse plieuse. Il comprend des boutons, des interrupteurs et une interface utilisateur permettant de définir les paramètres, d'ajuster les réglages et de lancer les opérations de pliage.
9.Tuyaux et raccords hydrauliques :
Les flexibles hydrauliques transportent le fluide hydraulique entre les composants, tels que la pompe, les vérins et les vannes. Les raccords assurent des connexions sûres et évitent les fuites.
Refroidisseur d'huile :
Dans certaines presses plieuses hydrauliques, un refroidisseur d'huile est utilisé pour dissiper la chaleur générée pendant le fonctionnement du système hydraulique, maintenant ainsi une température optimale du fluide et l'efficacité du système.
10. Bloc collecteur et vannes :
Le bloc collecteur distribue le fluide hydraulique aux différents composants. Les vannes contrôlent le débit et la direction du fluide hydraulique, permettant ainsi un contrôle précis du mouvement des vérins hydrauliques.
Comment fonctionne une presse plieuse hydraulique ?
Une presse plieuse hydraulique fonctionne en utilisant la force hydraulique pour plier la tôle le long d'un axe prédéterminé. La machine se compose de plusieurs composants clés fonctionnant ensemble pour appliquer une pression contrôlée sur la tôle. Voici un aperçu du fonctionnement d'une presse plieuse hydraulique :
1. Placement de la tôle :
Le processus commence par le placement de la pièce en tôle entre l'outil supérieur (poinçon) et l'outil inférieur (matrice) sur le banc de la presse plieuse. La matrice est montée sur le banc, tandis que le poinçon est fixé au vérin (glissière).
2. Serrage :
La tôle est solidement serrée entre le poinçon et la matrice pour éviter tout mouvement pendant le processus de pliage. Un serrage approprié est essentiel pour obtenir des pliages précis et cohérents.
3. Sélection des outils et configuration :
Les outils de poinçonnage et de matrice appropriés sont sélectionnés en fonction de l'angle de pliage, du type de matériau et de l'épaisseur souhaités. La configuration comprend la configuration de la butée arrière, qui permet de positionner la tôle avec précision pour chaque pliage.
4. Entrée du panneau de commande (pour presses plieuses CNC) :
Dans le cas des presses plieuses hydrauliques CNC (commande numérique par ordinateur), l'opérateur saisit les paramètres de pliage, notamment l'angle de pliage, la longueur de pliage et toutes les exigences de séquençage spécifiques, via le panneau de commande ou l'interface logicielle.
5. Activation du système hydraulique :
L'opérateur actionne le système hydraulique, qui comprend une pompe qui met le fluide hydraulique sous pression. Ce fluide hydraulique sous pression est ensuite dirigé vers des vérins hydrauliques qui actionnent le vérin.
6. Descente du bélier :
Lorsque le fluide hydraulique s'écoule dans les vérins hydrauliques, le vérin (glissière) commence à descendre sous l'effet de la pression hydraulique. Le vérin descendant entraîne le poinçon fixé vers le bas, en direction de la tôle.
7. Processus de pliage :
Le poinçon entre en contact avec la tôle, applique une force et la plie contre la matrice fixe. La force exercée par le système hydraulique détermine l'angle et le rayon de pliage.
Compensation du retour élastique :
Une fois l'angle de pliage souhaité atteint, le système hydraulique permet un bref arrêt pour compenser le retour élastique. Le retour élastique est la tendance de la tôle à revenir partiellement à sa forme initiale après pliage.
8. Montée du bélier :
Une fois l'opération de pliage terminée, le système hydraulique rétracte le vérin, soulevant ainsi le poinçon loin de la tôle.
9. Retrait de la tôle :
Les pinces sont relâchées et l'opérateur retire la tôle pliée de la machine. Le processus peut être répété pour des pliages supplémentaires ou avec des configurations d'outillage différentes selon les besoins.
Fonctionnement contrôlé et programmable (pour presses plieuses CNC) :
Les presses plieuses hydrauliques CNC offrent l'avantage d'un fonctionnement programmable. Le système de contrôle permet un contrôle précis de plusieurs paramètres de pliage, facilitant l'automatisation de séquences de pliage complexes et améliorant l'efficacité.