Le plieuse à cintre en U La technique de pliage en U est une méthode clé utilisée dans le travail des métaux, en particulier dans la fabrication de tôles, où une presse plieuse est utilisée pour créer un pli en forme de « U » dans une pièce de métal. Ce processus de pliage est essentiel pour produire des pièces avec des angles et des configurations spécifiques, souvent utilisées dans des industries telles que l'automobile, l'aérospatiale et la construction. La technique de pliage en U de la presse plieuse offre précision et répétabilité, ce qui en fait un choix incontournable pour les fabricants qui cherchent à créer efficacement des plis de haute qualité. Dans ce guide, nous explorerons le processus étape par étape, les outils et les meilleures pratiques pour obtenir des résultats optimaux en utilisant une presse plieuse pour les applications de pliage en U.
Comment comprendre le pliage en U d'une presse plieuse ?
Notions de base sur les cintres en U des presses plieuses
Le pliage en U de la presse plieuse fait référence à un processus dans lequel la tôle sera pliée en permanence sur la presse plieuse deux fois ou plus pour être formée en forme de « U ».
Ce procédé est réalisé en contrôlant avec précision les degrés de fermeture des matrices supérieures et inférieures et les courses pour répondre aux exigences de taille et d'angle précises de la conception. Le pliage en U est l'une des techniques de formage les plus courantes dans les industries de fabrication de métaux.
Le coude en U est essentiel dans diverses industries telles que la fabrication de métaux et la construction mécanique. Il est largement utilisé dans la production de pièces architecturales et structurelles, de pièces automobiles, de boîtiers d'appareils électroménagers et dans la fabrication de conceptions nécessitant un espace intérieur comme les systèmes de tuyauterie et les armoires électriques.
Le coude en U peut non seulement réduire les coûts de matériaux et améliorer l'efficacité de la production, mais également garantir les bonnes propriétés mécaniques et la qualité d'apparence des produits.
Histoire et évolution de la technologie des presses plieuses
La presse plieuse est considérée comme un équipement de formage de tôle de précision essentiel, et son histoire remonte au début de l'industrialisation. La presse plieuse manuelle initiale dépend de la main-d'œuvre, qui se caractérise par un fonctionnement complexe et une faible efficacité.
Avec l'avancement de la technologie, la technologie hydraulique et CNC améliore considérablement le développement de la presse plieuse, permettant à la machine de procéder à un pliage précis et complexe, y compris le pliage en U.
La technologie de pliage en U est constamment mise à niveau avec l'évolution de la technologie de la presse plieuse, qui va du simple pliage en ligne droite au pliage tridimensionnel. Non seulement elle permet d'obtenir un angle de pliage et une précision apparents améliorés, mais elle permet également de réaliser un pliage constant automatique en plusieurs étapes.
Moderne Presses plieuses CNC Il est même possible de l'intégrer à un logiciel de CAO/FAO, en imitant et en contrôlant précisément le coude en U dans son ensemble, ce qui permet d'obtenir des projets de haute précision et de production en série. De plus, la technique de l'outil et les outils d'assistance, comme la butée arrière et le dispositif de support avant, enrichissent et améliorent encore davantage les possibilités et l'adaptabilité du coude en U.
Aspects techniques
Types de presses plieuses pour le pliage en U
Presse plieuse mécanique
Avantages: structure simple, performances à coût élevé, entretien pratique, fonctionnement intuitif, adapté aux petites échelles ou aux occasions nécessitant moins de précision.
Inconvénients : Il est peu probable qu'il puisse réaliser un contrôle précis sous un tonnage élevé en raison des restrictions de ses voies de déplacement. De plus, son efficacité de travail est inférieure à celle des types hydrauliques et il n'est pas adapté à la production en série et constante.
Presse plieuse hydraulique
Avantages : Le système hydraulique offre une pression stable et intense, qui peut être adaptée au pliage précis de tôles avec plusieurs épaisseurs de matériaux. Il peut également être réglé sans paliers dans une plage plus étendue, adaptée à la production de masse et aux industries nécessitant une haute précision.
Inconvénients : l'équipement est complexe et nécessite un entretien régulier pour fonctionner normalement. Ses coûts d'entretien initiaux et ultérieurs sont relativement élevés.
Presses plieuses CNC
- Avantages :
- Le contrôle programmable garantit une grande précision et une répétabilité.
- Minimise le gaspillage de matériaux, ce qui les rend rentables pour la production à grande échelle.
- Idéal pour la production de composants détaillés, tels que des pièces de châssis automobiles.
- Inconvénients :
- Coûts d’achat et d’exploitation élevés en raison de la technologie avancée.
- Nécessite des opérateurs qualifiés pour la programmation et la maintenance.
- Pas toujours rentable pour la production à faible volume.
Presses plieuses électriques
- Avantages :
- Efficacité énergétique, ce qui se traduit par des coûts d’exploitation réduits au fil du temps.
- Offre une excellente précision et des courbures uniformes.
- Besoins de maintenance réduits par rapport aux systèmes hydrauliques.
- Inconvénients :
- Capacité limitée pour le pliage de charges élevées, ce qui les rend inadaptés aux applications lourdes.
- Coût initial plus élevé par rapport aux presses plieuses mécaniques.
Presses plieuses hybrides
Les presses plieuses hybrides allient la précision des systèmes électriques à la puissance des mécanismes hydrauliques. Ces machines sont souvent utilisées dans des applications nécessitant un tonnage modéré, comme la production de composants aéronautiques et automobiles. Elles allient efficacité énergétique et performances, ce qui en fait une option polyvalente.
- Avantages :
- Consommation d’énergie inférieure par rapport aux systèmes hydrauliques traditionnels.
- Capable de gérer une gamme d’épaisseurs de matériaux.
- Besoins de maintenance réduits grâce à la technologie hybride.
- Inconvénients :
- Une complexité accrue augmente les coûts d’investissement et de formation initiaux.
- Nécessite des connaissances spécialisées pour l'exploitation et la maintenance.
Choisir la bonne plieuse
Pour choisir la presse plieuse la plus adaptée, il faut prendre en compte les exigences spécifiques du projet, telles que le type de matériau, l'épaisseur de la tôle, le volume de production et le budget. Par exemple :
- Les presses plieuses hydrauliques sont idéales pour les applications lourdes comme la construction navale.
- Les presses plieuses CNC excellent dans les industries de haute précision comme la fabrication automobile.
- Les presses plieuses électriques sont privilégiées dans les opérations respectueuses de l'environnement. Comprendre les avantages, les limites et les applications spécifiques de chaque type garantit une décision éclairée adaptée aux besoins de production.
Matériaux adaptés aux coudes en U
La connaissance des propriétés physiques et mécaniques des différents types de matériaux métalliques est essentielle à la conception et à la mise en œuvre précises du processus de pliage en U, ce qui est bénéfique pour éviter les problèmes de qualité du produit en raison d'une mauvaise utilisation des matériaux.
Acier à faible teneur en carbone:il présente une intensité modérée, une bonne plasticité, est facile à plier et est l'un des matériaux les plus courants pour la production de coudes en U.
Acier inoxydable: il est bon, résistant à la corrosion et décoratif. Il nécessite un calcul et un contrôle précis des paramètres de déformation lors du pliage en raison de sa haute intensité et de ses propriétés de retour élastique.
Aluminium: Il présente une faible densité et une bonne conductivité électrique et thermique, ce qui le rend adapté aux pièces légères. Lors du pliage, vous devez tenir compte des propriétés de forte ductilité et de faible module d'élasticité afin d'éviter un rebond excessif et une influence sur la qualité du produit.
Alliage de cuivre : Il présente une bonne conductivité électrique et une bonne résistance à la corrosion. En raison de sa grande solidité, il doit être traité avec des matrices et des conditions de traitement appropriées.
Considérations de conception pour les coudes en U
Rayon de courbure : elle est généralement supérieure à un certain multiple de l'épaisseur du matériau pour éviter de générer des fissures ou des contraintes internes trop importantes lors du pliage, garantissant ainsi l'intégrité de la structure de la pièce.
Angle de courbure : elle détermine la forme finale de la pièce. Elle est calculée en fonction des exigences de conception du produit et de l'effet de retour élastique, compensant ainsi et obtenant la taille géométrique prévue.
Force de flexion : La valeur de pression est déterminée par de nombreux facteurs tels que l'épaisseur du matériau, le rayon de courbure et la longueur. Une pression trop élevée ou trop faible peut entraîner des problèmes de qualité. Des outils de calcul professionnels et des formules empiriques sont donc nécessaires pour garantir la valeur de pression appropriée.
Facteurs influençant la précision du pliage en U
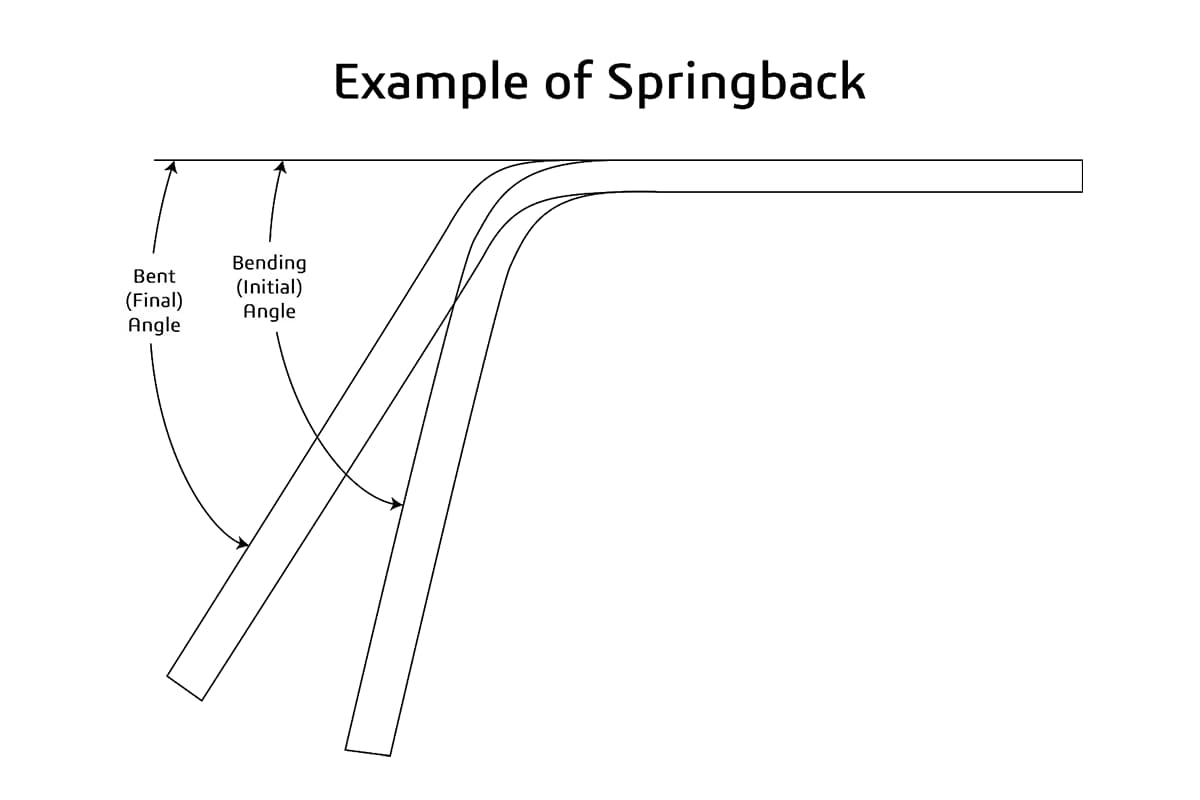
Le retour élastique se produit lorsque le métal revient partiellement à sa forme initiale après pliage. Pour résoudre ce problème, des techniques telles que le pliage en surépaisseur, le pliage en creux et le matriçage sont utilisées :
- Surplier applique une force supplémentaire pour contrer le retour élastique.
- Bas pliage consiste à presser le matériau dans la matrice pour obtenir un pli précis.
- Frappe crée une déformation permanente grâce à une flexion à haute pression, éliminant ainsi le retour élastique du matériau.
Propriétés matérielles
La ductilité, la dureté et l'épaisseur du matériau ont une incidence directe sur les performances de pliage. Les matériaux plus durs peuvent nécessiter une force plus importante et une manipulation plus prudente pour éviter les fissures, tandis que les matériaux ductiles permettent des pliages plus lisses.
Rayon de courbure
Le maintien d'un rayon de courbure constant est essentiel pour obtenir des formes en U uniformes. Le rayon dépend du nez du poinçon et de la géométrie de la matrice, les rayons plus serrés nécessitant un outillage spécialisé.
Paramètres clés de la machine pour un pliage en U précis
Force de flexion
La force de pliage fait référence à la quantité de pression appliquée par la presse plieuse, qui dépend de l'épaisseur et de la résistance du matériau. Elle est influencée par des facteurs tels que l'épaisseur du matériau, le rayon de courbure et la longueur de la pièce.
Une force insuffisante peut entraîner des pliages incomplets, tandis qu'une force excessive peut endommager l'outillage ou le matériau. Pour garantir des pliages précis, il faut utiliser le bon jeu d'outils (poinçons et matrices) pour correspondre à la force requise.
Longueur de pliage
La longueur de pliage définit la longueur maximale du matériau que la presse plieuse peut traiter en une seule opération. Cela est particulièrement important pour les applications à grande échelle, où le maintien de l'uniformité sur l'ensemble du pliage est essentiel. Des longueurs de pliage plus longues réduisent le besoin d'opérations multiples, améliorant à la fois l'efficacité et la cohérence.
Course du cylindre
La course du vérin désigne la plage de mouvement vertical du vérin pendant le processus de pliage. Une course de vérin plus longue offre plus de flexibilité pour plier des matériaux plus épais ou plus hauts, s'adaptant aux angles de pliage requis et contribuant à compenser le retour élastique.
Ouverture à la lumière du jour
L'ouverture de la presse plieuse correspond à l'espace entre les poutres supérieure et inférieure lorsque la presse plieuse est entièrement ouverte. Cet espace détermine la taille maximale du matériau et de l'outillage qui peuvent être positionnés dans la machine à travailler les métaux. Des ouvertures de la presse plieuse plus grandes permettent de plier des pièces plus hautes et d'utiliser des outils spécialisés.
Vitesse et contrôle
La vitesse de la poutre supérieure affecte directement l'efficacité de la production. Les machines modernes permettent aux opérateurs de presses plieuses d'ajuster la vitesse à différentes étapes du cycle de pliage, de l'approche rapide au pliage précis, garantissant à la fois vitesse et précision. Les systèmes CNC offrent un contrôle amélioré, permettant une programmation précise des paramètres de force, de vitesse et d'angle, améliorant ainsi la cohérence et réduisant les erreurs.
Avantages du cintrage en U
Le cintrage en U offre plusieurs avantages notables :
- Versatilité: Adapté à une large gamme de matériaux et d'épaisseurs, ce qui le rend applicable à tous les secteurs industriels.
- Précision: Les presses plieuses avancées avec commandes CNC garantissent des résultats cohérents et précis.
- Rentabilité : Le procédé minimise le gaspillage de matériaux et s'adapte à la production à petite et grande échelle. Par exemple, dans l'industrie automobile, il a été démontré que le cintrage en U permet de réduire les coûts de fabrication des composants du châssis en optimisant l'utilisation des matériaux.
Guide pratique
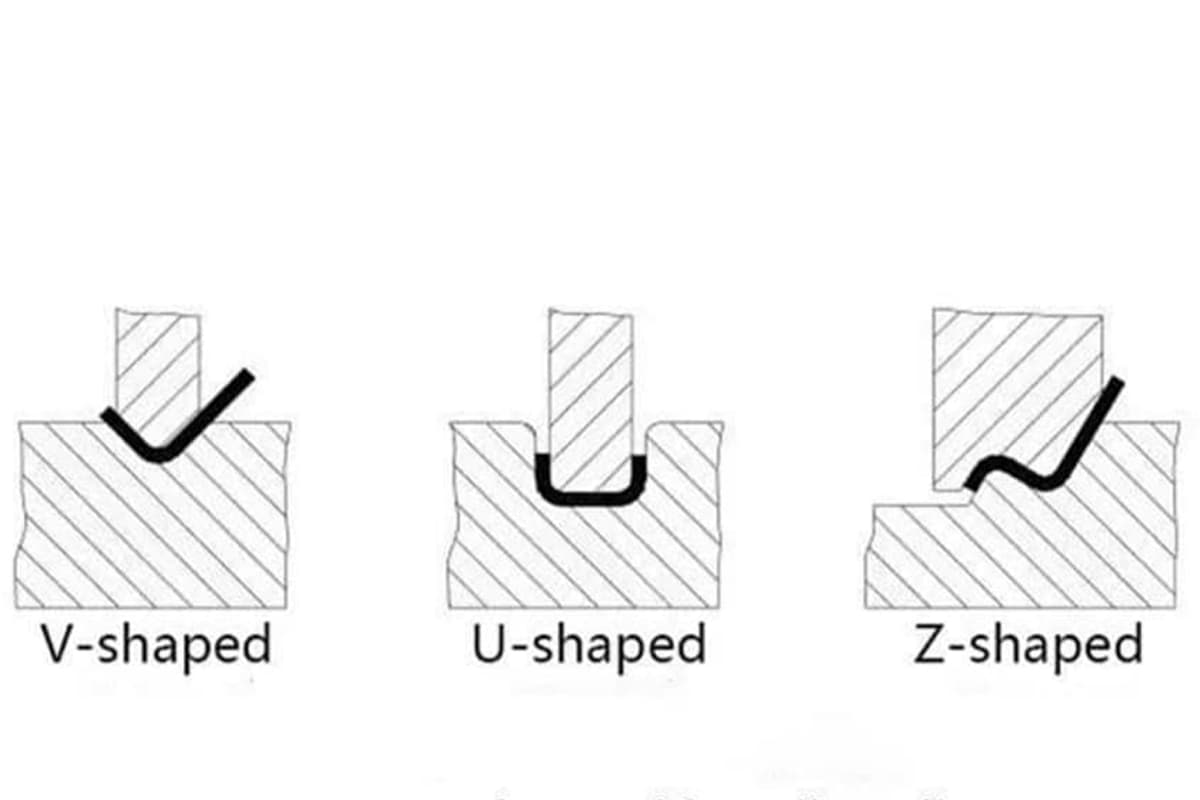
Guide étape par étape pour réaliser un coude en U
Choisissez la presse plieuse et les matrices appropriées: Choisissez une presse plieuse mécanique ou hydraulique en fonction du type et de l'épaisseur du matériau. Choisissez la matrice supérieure et inférieure appropriée en fonction de la taille et de la forme du coude en U requises.
Préparation du matériel : mesurer et couper la tôle à la taille requise.
Régler les paramètres de la machine : définissez les paramètres de force de flexion, de vitesse et d'angle raisonnables en fonction de l'épaisseur du matériau et du rayon de flexion.
Faire fonctionner le pliage : placez la tôle sur la presse plieuse, assurez-vous qu'elle est au milieu de la matrice et pliez-la selon les paramètres décidés.
Vérifier et ajuster: Surveiller la déformation du matériau, vérifier la précision de la taille et de l'angle, et ajuster en temps opportun la pression et l'angle pour compenser l'effet de retour élastique. Après le pliage initial d'un ou deux côtés, réaliser l'autre partie du pliage selon les mêmes procédures.
Technique:utilisez des outils de mesure précis pour vérifier plusieurs fois la position de la matrice et le réglage de l'angle.
Pour les pièces complexes en forme de U, la méthode de formage étape par étape peut être acceptée. Pliez une petite section à la fois et maintenez la section constante et uniforme.
Élaborez des procédures opérationnelles standardisées, procédez de manière stricte et améliorez vos compétences opérationnelles grâce à la pratique répétée.
Comment calculer le rayon de courbure d'une presse plieuse en U ?
- Comprendre les bases du rayon de courbure
- Le rayon de courbure d'une presse plieuse en U est le rayon de la courbe intérieure de la forme en U. Il s'agit d'un paramètre crucial car il affecte l'intégrité structurelle, l'apparence et la fonctionnalité de la pièce pliée. Un rayon de courbure plus petit peut donner lieu à un pli en U plus compact, tandis qu'un rayon plus grand peut être nécessaire pour les pièces qui nécessitent plus de flexibilité ou pour éviter la fissuration du matériau.
- Facteur d'épaisseur du matériau
- L'épaisseur du matériau (Rmin) est un facteur clé dans le calcul du rayon de courbure minimal. En règle générale, le rayon de courbure minimal () est lié à l'épaisseur du matériau. Pour la plupart des métaux, il existe un rayon de courbure minimal recommandé pour éviter les fissures. Par exemple, dans l'acier doux, le rayon de courbure minimal est souvent d'environ 1 à 2 fois l'épaisseur du matériau. Cela signifie que Rmin = (1-2)t.
- Le rapport exact dépend de la ductilité du matériau. Les matériaux ductiles comme l'aluminium peuvent généralement avoir un rayon de courbure plus petit par rapport à leur épaisseur par rapport à des matériaux moins ductiles comme certains aciers à haute résistance.
- Considérations relatives à l'outillage
- L'outillage utilisé dans la presse plieuse affecte également le rayon de pliage. Le rayon du poinçon et de la matrice joue un rôle important. Le rayon du poinçon (r,) doit être légèrement inférieur au rayon de pliage final souhaité (R). La relation entre le rayon du poinçon et le rayon de pliage peut être approximée comme , où est un petit facteur d'ajustement qui tient compte du retour élastique. Le retour élastique est la tendance du matériau à revenir partiellement à sa forme d'origine après pliage.
- Le rayon de la matrice () est généralement plus grand que le rayon du poinçon et est conçu pour s'adapter au matériau plié et fournir un support pendant le processus de pliage. Une règle empirique courante est que le rayon de la matrice est d'environ 1,5 à 2 fois le rayon du poinçon ().
- Formule de calcul basée sur la géométrie et les propriétés des matériaux
- Pour un calcul plus précis, vous pouvez utiliser la formule suivante basée sur le concept d'axe neutre. L'axe neutre est la couche à l'intérieur du matériau qui ne se comprime ni ne s'étire pendant la flexion. La formule pour le rayon de courbure () prenant en compte l'épaisseur du matériau (), l'angle de courbure () et le facteur d'allongement () est :
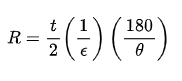
- où est l'allongement de la fibre extérieure du matériau pendant la flexion et peut être obtenu à partir des tableaux de propriétés des matériaux ou par des essais. L'angle de flexion est mesuré en degrés.
- En pratique, il est également important de tenir compte des marges de retour élastique. Le retour élastique peut être estimé par essais et erreurs ou en utilisant des données empiriques fournies par le fournisseur de matériaux ou le fabricant de presses plieuses. En règle générale, vous devrez peut-être ajuster le rayon de courbure calculé d'un certain pourcentage (généralement autour de 5 - 10%) pour tenir compte du retour élastique, en fonction du matériau et du processus de pliage.
Erreurs courantes et comment les éviter
Un mauvais choix des matrices et un réglage inexact de l'écartement des matrices peuvent entraîner un mauvais effet de pliage ou endommager la pièce. Si la force de pliage est trop importante ou trop faible, cela entraînera la rupture du matériau. Le retour élastique est trop important, ce qui affectera la précision du produit. Un mauvais positionnement du matériau et une mauvaise fixation entraîneront un décalage pendant le processus de pliage.
Il existe plusieurs approches de précaution basées sur les questions ci-dessus :
Respectez strictement le manuel d'utilisation, choisissez la matrice intégrée à l'expérience pratique, vérifiez régulièrement et ajustez l'écartement de la matrice.
Calculez la force de flexion en fonction des propriétés et de l'épaisseur du matériau, et tenez également compte du ressort en augmentant de manière appropriée le volume de compensation.
Améliorez la formation des opérateurs et améliorez la précision de serrage et de positionnement des matériaux.
Entretien et maintenance des presses plieuses
Entretien quotidien
Nettoyez régulièrement les débris intérieurs et extérieurs de la presse plieuse, assurez-vous que le système de lubrification est lisse et complétez ou remplacez l'huile de lubrification à temps.
Vérifiez les propriétés d'étanchéité du système hydraulique pour éviter les fuites d'huile et assurez-vous que les composants hydrauliques fonctionnent correctement. Entretenez et vérifiez le système de contrôle électrique pour vous assurer que les composants fonctionnent de manière stable et sûre. Vérifiez l'état d'abrasivité de la matrice, rectifiez, réparez ou remplacez les nouvelles matrices si nécessaire.
Stratégies de maintenance à long terme
Élaborez un plan détaillé de maintenance de l’équipement, vérifiez et réparez-le régulièrement, afin d’éviter que d’éventuels dysfonctionnements ne se produisent.
Établir un registre d'utilisation et suivre l'état de fonctionnement de l'équipement afin de fournir des preuves pour une maintenance ultérieure.
Sensibiliser les employés à l'importance de l'entretien des équipements et développer de bonnes habitudes de fonctionnement, afin de prolonger la durée de vie de la presse plieuse et l'efficacité du travail.
Applications industrielles
Coudes en U dans diverses industries
Industrie automobile
Dans la fabrication automobile, le coude en U est largement utilisé dans la production de conduits d'échappement, de composants de suspension et de pièces structurelles de carrosserie. Le choix du matériau, la précision du processus de pliage et la durabilité des produits sont des critères stricts, car ces composants doivent généralement supporter des températures élevées, des pressions élevées et des vibrations.
Industrie aérospatiale
L'industrie aérospatiale a des exigences extrêmement élevées en matière de légèreté et de résistance. Le procédé de pliage en U est généralement utilisé dans les systèmes d'alimentation en carburant des avions, les structures de cadre de fuselage et d'autres configurations de canalisations internes, garantissant que chaque pièce peut répondre à des normes strictes et atteindre les objectifs de perte de poids.
Secteur de l'architecture
Dans l'industrie de la construction, l'acier ou les tubes en forme de U sont largement utilisés dans le support de structure, les systèmes d'échappement, la tuyauterie CVC, etc. En particulier dans l'architecture de structure en acier, les poutres en forme de U pré-cintrées peuvent améliorer l'efficacité de travail et la stabilité de la structure, ce qui est pratique pour l'assemblage sur place.
Tendances futures dans le pliage en U avec presse plieuse
Technologies et méthodes émergentes
Technologie CNC et les degrés d'automatisation sont constamment améliorés, ce qui permet à la presse plieuse d'accomplir des tâches de pliage en U plus complexes et de réduire les erreurs provoquées par l'intervention manuelle.
La technologie des machines et le système de production intelligent sont utilisés pour rendre le coude en U plus efficace, plus flexible et adapté aux petites échelles, aux types de variétés et aux besoins de production personnalisés.
Le développement de la science des matériaux, comme l'émergence de nouveaux matériaux composites, remettra en question le processus de pliage par presse plieuse et offrira également à la technologie du pliage en U la possibilité d'applications innovantes.
Anticipation de l'industrie de fabrication de métaux
La technologie future des presses plieuses évoluera vers une haute précision, une vitesse plus rapide et une grande flexibilité pour gérer la conception de pièces plus complexes.
Le concept de protection de l'environnement est profondément ancré dans le cœur des gens. Les équipements et technologies à faible consommation et à forte production seront les principaux, y compris l'application du système hydraulique à économie d'énergie, le recyclage de la chaleur résiduelle et d'autres mesures sur la presse plieuse.
Les technologies numériques et de réseau seront davantage intégrées dans le processus de formage des métaux. Le processus de production sera amélioré grâce à l'Internet des objets et à l'analyse des mégadonnées, ce qui améliorera l'efficacité et la qualité globales de la production.