What is Press Brake Crowning
Press brake crowning refers to a technique used in sheet metal bending to compensate for the deflection of the press brake's upper beam (also known as the ram) during the bending process. As the upper beam applies downward force to the metal sheet being bent, it can cause the beam to deflect slightly, resulting in uneven bending along the length of the workpiece.
To counteract this deflection and ensure uniform bending across the entire length of the workpiece, press brake crowning involves adjusting the shape of the lower die (also known as the bed) to form a slight curve that opposes the deflection of the upper beam. This curvature, often in the form of a parabolic profile, is strategically designed to apply an upward force to the workpiece, compensating for the downward deflection of the upper beam.
By implementing press brake crowning, manufacturers can achieve more precise and consistent bending results, especially when working with longer or thicker materials. This technique helps minimize variations in bend angle and ensures uniformity in the final product, improving overall quality and reducing scrap rates.
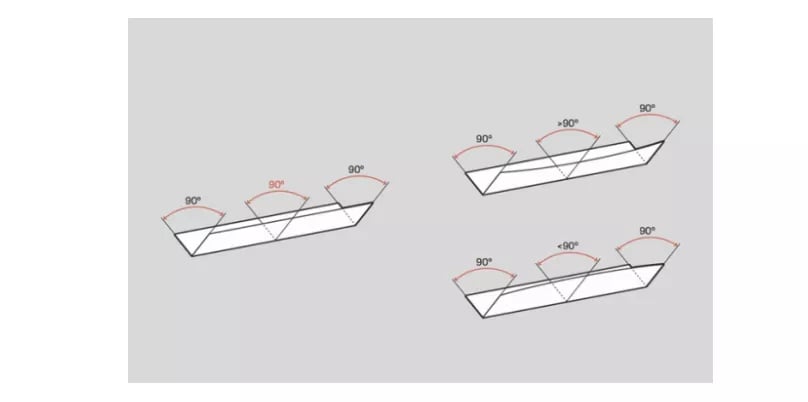
Why Need A Crowning for Press Brake
The press brake is pressurized by two working cylinders at both ends of the sliding block. The deformation force of the bending work piece is in the middle, so the sliding block and the worktable are deformed together with the upper and lower die, which causes the sheet material to be uneven along the length of the die edge, which directly affects the accuracy and straightness of the bending work piece.
Therefore, it is necessary to take corresponding measures to reduce or eliminate the deflection caused by the deformation.
The so-called deflection compensation device has preset a deformation in the direction of the opposite force-deformation in the sliding block and the upper die or the worktable and the lower die working table, and the deformation has the same amount of deformation generated in the actual work. Therefore,to realize the compensation of the relative deformation of the slider to the worktable, the pressure distribution between the dies is more uniform and the bending quality of the sheet material is improved.
Types of Crowning System
At present, the press brake crowning mainly has three kinds-geometric crowning, hydraulic crowning,and mechanical crowning.
Geometric crowning
Generally, not adopt this type of crowning method.
Working table fixed convex,that is at the time of manufacture, the worktable was machined into arc shape with a slightly convex in the middle to compensate for the deflection caused by bending.
To make the appropriate correction for the upper mold, so that the middle part of the mold slightly curved,so that when the slider occurs upward deflection deformation, the upper die edge basically tends to be straight, so that it keeps each bending point along the bend line generate the same bending force for the plate.
The advantages of the geometrical compensation method are low cost and easy to manufacture, but there are some disadvantages which can only realize the compensation of fixed deformation and small compensation flexibility.
In addition, the compensation block arc correction quantity needs to pass through the precise calculation. The calculation method which based on the mechanics` theory and the finite element calculation all has the certain error, therefore,even this kind of crowning method can achieve the deflection compensation effect, but it is very difficult to realize.
Hydraulic crowning
Mainly used on the electro hydraulic synchronous CNC press brake, because the amount of compensation needs to be controlled from the CNC system, such as DA56 DA66 etc.
On the press brake frame, in addition, to installing two hydraulic cylinders at two sides, install another two-auxiliary hydraulic cylinder in the middle of the machine. When stroke down, the auxiliary cylinder filled with liquid oil and go downward. During bending process, hydraulic oil inlet into the auxiliary cylinder, so that the slider generate downward deflection for compensation.
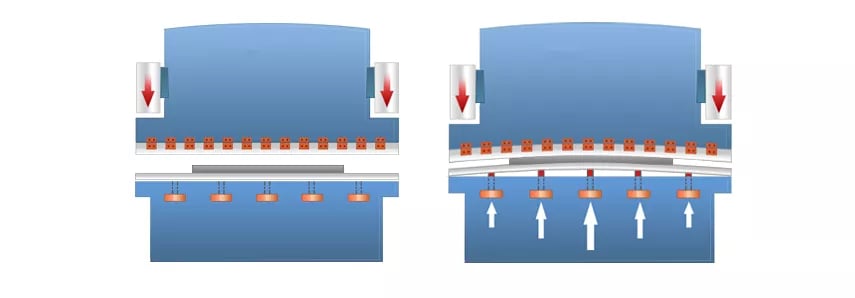
Install the auxiliary hydraulic cylinder in the lower part of the worktable. During bending process, it generates an upward force on the worktable, which forms the automatic crowning system.
The pressure compensation device is composed of several small oil cylinders, comprising an oil cylinder, a motherboard, an auxiliary plate and a pin shaft, and a compensating cylinder is placed on the worktable, and a pressure compensation system is formed with a proportional relief valve.
When working, the auxiliary plate supports the oil cylinder, the oil cylinder holds up the motherboard up, just overcomes the deformation of the slider and the worktable. The convex device is controlled by a numerical control system, so that the preload can be determined according to the thickness of the plate, the opening of the die and the tensile strength of the material when bending different sheet materials.
The advantage of hydraulic crowning is that it can realize the deflection compensation for continuous variable deformation with large compensation flexibility,but there are some disadvantages of complex structure and relatively high cost.
Mechanical crowning
Most widely used crowning method for the ordinary press brake, with good compensation effect and low cost. In real operation, it is very convenient and easy for operators.
Mechanical crowning is a kind of new deflection compensation method, which is generally used triangular oblique wedge structure.
The principle is that the two-triangle wedge block with a angles, the upper wedge moving is fixed at x-direction,can only move in y-direction. When the wedge moves the distance along the x-direction, the upper wedge moves up the h distance under the lower wedge force,which is the principle of the mechanical crowning.
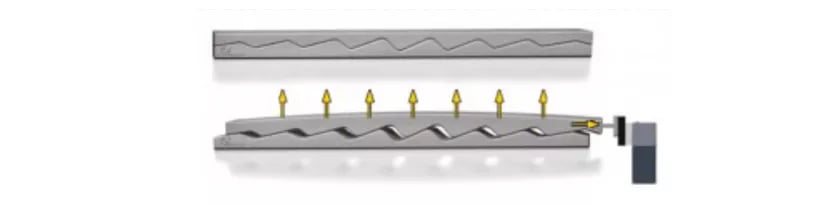
Regarding existing mechanical compensation structure,two bolster plates are placed in full length on the worktable, the upper and lower plates are connected through the disc spring and bolts. The upper and lower plates are consist of a number of oblique wedges with different slopes, through the motor drive to make them relatively moving, forming and ideal curve for a set of convex position.
Conclusion
A press brake crowning is essential for achieving precise, consistent, and efficient bending operations in sheet metal fabrication. It ensures that manufacturers can produce high-quality parts with accuracy and reliability, ultimately enhancing productivity and profitability.