The frequency of inspecting a press brake depends on several factors, including the machine's usage, operating conditions, and manufacturer's recommendations. However, as a general guideline, press brakes should undergo regular inspections to ensure they are operating safely and efficiently. Here are some considerations for determining how often to inspect a press brake:
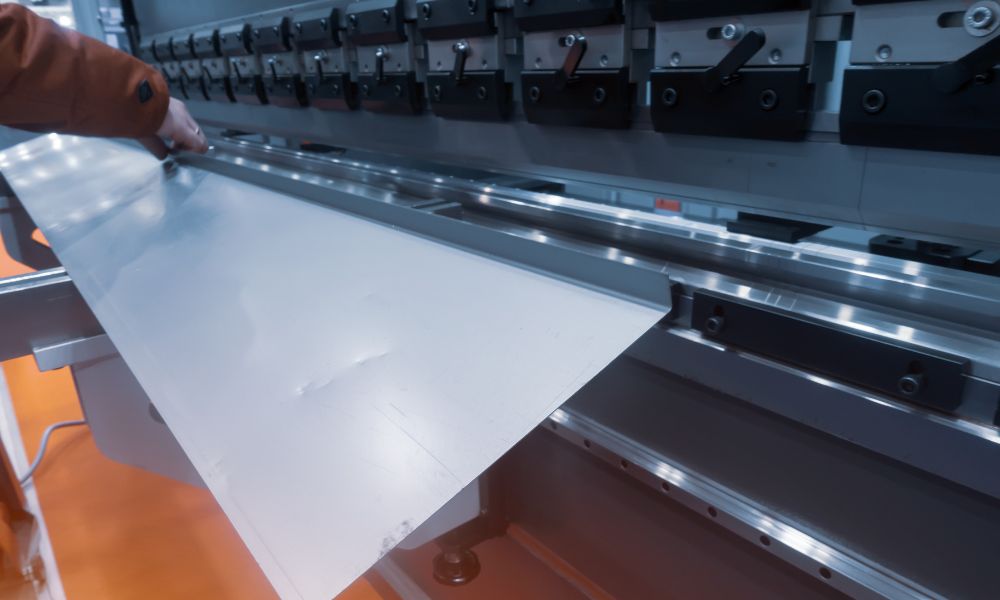
Manufacturer Recommendations: Follow the manufacturer's guidelines outlined in the press brake's operation manual. Manufacturers typically provide recommendations for routine maintenance tasks and inspection intervals based on the machine's design and expected usage.
Usage Frequency: Press brakes that are used heavily or operate in demanding production environments may require more frequent inspections. High-volume production facilities may inspect their press brakes on a weekly or monthly basis to ensure optimal performance and safety.
Operating Conditions: Press brakes operating in harsh environments, such as those exposed to excessive dust, heat, or humidity, may require more frequent inspections to prevent premature wear and damage to components.
Critical Components: Pay special attention to critical components that are subject to wear and stress during operation, such as hydraulic systems, mechanical linkages, tooling, safety guards, and electrical components. Inspect these components more frequently to identify signs of wear, damage, or malfunction.
Safety Considerations: Regularly inspect safety features and components to ensure compliance with safety standards and regulations. This includes checking emergency stop controls, light curtains, interlocks, and other safety devices to ensure they are functioning properly.
Visual Inspections: Conduct visual inspections of the press brake before each use to check for any obvious signs of damage, misalignment, or abnormalities. Look for leaks, loose fasteners, worn components, and any other issues that could affect performance or safety.
Preventive Maintenance Schedule: Develop a preventive maintenance schedule that includes regular inspections, lubrication, adjustments, and component replacements as needed. This schedule should be based on the machine's usage, operating conditions, and manufacturer recommendations.
By conducting regular inspections and maintenance, press brake operators can identify potential issues early, prevent unexpected downtime, extend the machine's lifespan, and ensure safe and efficient operation. It's essential to document inspections and maintenance activities to track the machine's condition and compliance with regulatory requirements.
Daily Checklist
Every day before starting operations, quickly inspect your press brake. Check the hydraulic fluid levels, and ensure there are no leaks. Inspect the bending tools for any signs of wear or damage, and make sure they’re secure. Also, confirm all safety devices are functional. These daily checks take time but can help you identify and prevent issues from worsening.
Weekly Maintenance
On a weekly basis, take the time to conduct a more detailed assessment. This involves cleaning the machine to remove accumulated dust or debris, which can affect its performance. Lubricate all moving parts as recommended by the manufacturer to reduce friction and prevent wear. Also, check the alignment of the back gauge and ram, and make adjustments if necessary.
Thorough Monthly Checks
Monthly inspections should be more comprehensive. At this stage, you need to examine the hydraulic system—look for signs of wear on the seals and cylinders. Also, check the electrical components for loose connections or signs of overheating. If your press brake is a CNC (computer numerical control) model, we suggest backing up the programs regularly.
Extended Maintenance at 2,000 Hours or Manufacturer’s Recommendation
Manufacturers may recommend different maintenance intervals, but a general rule is to perform a thorough maintenance check every 2,000 hours of operation. This includes replacing hydraulic oil, checking the ram and back gauge for signs of wear, and recalibrating the machine if necessary. It’s ideal to call in a professional technician for a comprehensive inspection and servicing at this time.
How Often Should You Inspect Your Press Brake?
The frequency of inspecting a press brake depends on several factors, including the machine's usage, operating conditions, and manufacturer's recommendations. However, as a general guideline, press brakes should undergo regular inspections to ensure they are operating safely and efficiently. Here are some considerations for determining how often to inspect a press brake:
Manufacturer Recommendations: Follow the manufacturer's guidelines outlined in the press brake's operation manual. Manufacturers typically provide recommendations for routine maintenance tasks and inspection intervals based on the machine's design and expected usage.
Usage Frequency: Press brakes that are used heavily or operate in demanding production environments may require more frequent inspections. High-volume production facilities may inspect their press brakes on a weekly or monthly basis to ensure optimal performance and safety.
Operating Conditions: Press brakes operating in harsh environments, such as those exposed to excessive dust, heat, or humidity, may require more frequent inspections to prevent premature wear and damage to components.
Critical Components: Pay special attention to critical components that are subject to wear and stress during operation, such as hydraulic systems, mechanical linkages, tooling, safety guards, and electrical components. Inspect these components more frequently to identify signs of wear, damage, or malfunction.
Safety Considerations: Regularly inspect safety features and components to ensure compliance with safety standards and regulations. This includes checking emergency stop controls, light curtains, interlocks, and other safety devices to ensure they are functioning properly.
Visual Inspections: Conduct visual inspections of the press brake before each use to check for any obvious signs of damage, misalignment, or abnormalities. Look for leaks, loose fasteners, worn components, and any other issues that could affect performance or safety.
Preventive Maintenance Schedule: Develop a preventive maintenance schedule that includes regular inspections, lubrication, adjustments, and component replacements as needed. This schedule should be based on the machine's usage, operating conditions, and manufacturer recommendations.
By conducting regular inspections and maintenance, press brake operators can identify potential issues early, prevent unexpected downtime, extend the machine's lifespan, and ensure safe and efficient operation. It's essential to document inspections and maintenance activities to track the machine's condition and compliance with regulatory requirements.
Daily Checklist
Every day before starting operations, quickly inspect your press brake. Check the hydraulic fluid levels, and ensure there are no leaks. Inspect the bending tools for any signs of wear or damage, and make sure they’re secure. Also, confirm all safety devices are functional. These daily checks take time but can help you identify and prevent issues from worsening.
Weekly Maintenance
On a weekly basis, take the time to conduct a more detailed assessment. This involves cleaning the machine to remove accumulated dust or debris, which can affect its performance. Lubricate all moving parts as recommended by the manufacturer to reduce friction and prevent wear. Also, check the alignment of the back gauge and ram, and make adjustments if necessary.
Thorough Monthly Checks
Monthly inspections should be more comprehensive. At this stage, you need to examine the hydraulic system—look for signs of wear on the seals and cylinders. Also, check the electrical components for loose connections or signs of overheating. If your press brake is a CNC (computer numerical control) model, we suggest backing up the programs regularly.
Extended Maintenance at 2,000 Hours or Manufacturer’s Recommendation
Manufacturers may recommend different maintenance intervals, but a general rule is to perform a thorough maintenance check every 2,000 hours of operation. This includes replacing hydraulic oil, checking the ram and back gauge for signs of wear, and recalibrating the machine if necessary. It’s ideal to call in a professional technician for a comprehensive inspection and servicing at this time.