Calculating press brake tonnage is essential in metalworking and sheet metal fabrication, right press brake tonnage helps in selecting the appropriate press brake machine for the job. Different bending tasks demand varying levels of force, and using the right tonnage capacity ensures the machine can handle the specific material and thickness.
But tonnage can be very confusing at a glance and trying to calculate limits can be a challenge. Not having accurate tonnage calculations can cause serious problems. To help you get a better idea of how to get started, we’ve put together some important things to know about calculating press brake tonnage.
Calculating Press Brake Tonnage Limits
Basic calculations for press brake tonnage limits are fairly straightforward. The calculation is based on the point where yield is broken and the bending starts. As a baseline, the formula is calculated on AISI 1035 cold-rolled steel that has a 60,000-PSI tensile strength.
Tonnage for air bending AISI 1035 =
{[575 × (material thickness2)] /
Die-opening width /12} x the length of the bend
Die-opening width, metal thickness and bend length are calculated in inches, with a constant 575 value. The material thickness value is squared, multiplied by 575, divided by the die-opening width inch value and then divided again by 12 inches. The tonnage per inch is now calculated. You can then multiply the value by the bend length.
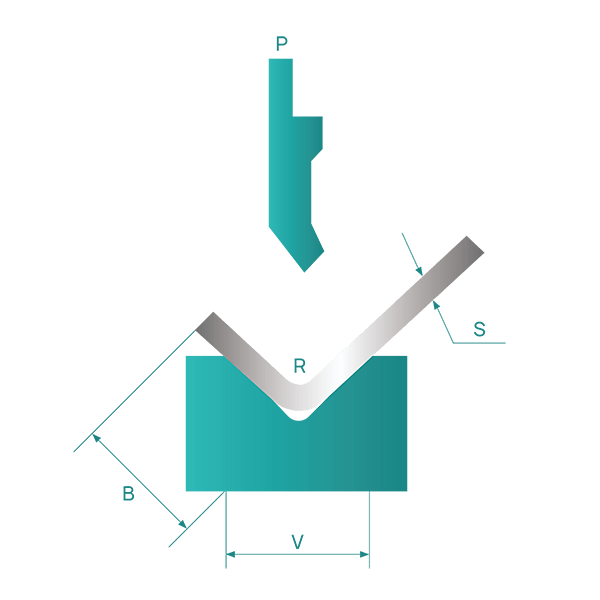
Forming method
These calculations are formulated for air bending, which allows tonnages to be decreased or increased when the die-opening width is narrowed or widened. In air bending, the die-opening width will be affected by the inside bend radius. Bend reduction will need to be calculated according to the inside radius made in the die width.
Tonnage will be different when using a different forming method. In this case, a method factor will need to be added to the formula. In the case of bottom bending, which forms to a depth of about 20% of the material thickness, there may be far more tonnage than air bending. Coining may require even more tonnage, as it happens when the forming is done below the thickness of the material.
Tooling factor
You will also need to consider variables such as the multiple-bend tooling factor. If you are using tools made to form more than one bend at once, this will need to be added to your formula. You may be using hemming operations, offset tools and hat tools, for example. Offset tools will increase the tonnage required - especially in thicker materials.
Final formula
The full formula that you will need to use in your calculation will include forming tonnage and method, material, bend length, and multiple bend tooling. Measurements are done in inches.
- Forming tonnage = {[575 x (material thickness squared)] /die-opening width/12} × length of bend × material factor × method factor × multiple-bend tooling factor
- Material factor = Material tensile strength in PSI/60,000
- Method factor = 5.0+ for bottom bending, 10.0+ for coining and 1.0 for air bending
- Multiple-bend tooling factor = 5.0 for offset bending, 10 for offset bending in thick material, 5.0 for bending with a hat tool, 4.0 for bending with a hemming tool, and 1.0 for conventional tooling
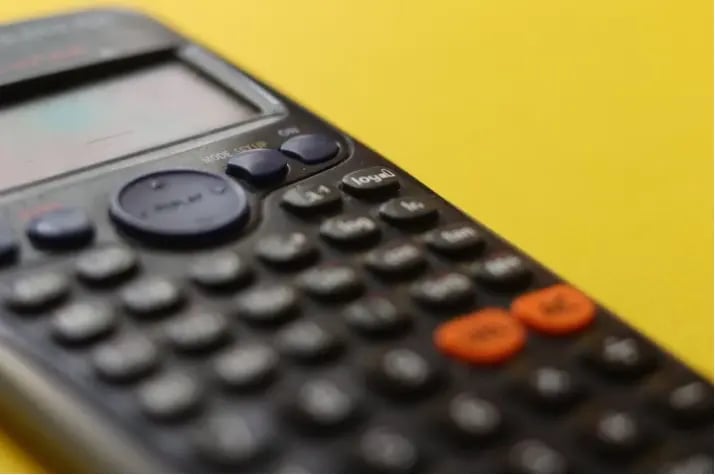
Air bending 60,000-PSI AISI 1035 when you use traditional tooling would result in a 1.0 value, incorporating all factors, from material to method and tooling. These factors will not affect the tonnage requirements. Bending a different material with another tensile value, bending method and tooling will give you a very different value.
We hope that these tips make it easier to work out the proper press brake tonnage, to get the best results from your bending and cutting.