When choosing a press brakes, consider the following factors:
- Material: Determine the type of material you’ll be bending, such as metal sheets, plastic, etc. Different materials require different types of press brakes.
- Bending length and thickness: Specify the typical lengths and thickness ranges of the materials you’ll be working with to select a press brake with the appropriate capacity.
- Technological requirements: Some press brakes offer digital control features that can enhance production efficiency and bending accuracy, whereas traditional mechanical press brakes are simpler in operation.
- Space and budget: Consider your workshop space and budget to ensure that the press brake you choose fits your production needs.
- Brand and after-sales service: Opt for a reputable brand and ensure reliable after-sales service and technical support.
By considering these factors, you can choose a press brake model and specification that suits your requirements.
Type of Press Brakes?
Press brakes come in different types, each with its specific advantages and applications. The main types of press brakes include:
- Mechanical Press Brakes: These press brakes use a flywheel to generate the bending force. They are known for their simplicity and cost-effectiveness but may have slower cycle times compared to other types.
- Hydraulic Press Brakes: These presses use hydraulic cylinders to apply the bending force. They offer high bending accuracy and speed, making them suitable for a wide range of applications.
- CNC Press Brake: These are hydraulic press brakes equipped with computer numerical control (CNC) systems. They are highly automated and allow for precise control over the bending process, making them ideal for complex bending tasks and high-volume production.
- Servo-Electric Press Brake: These press brakes use an electric servo motor to drive the ram, offering high precision, energy efficiency, and low maintenance compared to hydraulic counterparts.
Each type of press brake has its unique features, and the choice depends on factors such as the material being processed, bending requirements, production volume, and budget.
What is Mechanical Press Brakes?
A mechanical press brake is a type of press brake that utilizes a mechanical mechanism, often a flywheel, to generate the bending force required to shape metal or other materials. When the machine’s pedal or lever is activated, the flywheel’s rotational energy is transferred to a mechanical linkage system that drives the ram downward to perform the bending action.
Mechanical press brakes are known for their straightforward design, reliability, and cost-effectiveness. They are suitable for a variety of bending applications, especially when dealing with lower to medium production volumes and simpler bending tasks. However, they may have slower cycle times compared to hydraulic or CNC press brakes, and their bending force may not be as easily controllable or adjustable as with hydraulic or servo-electric press brakes.
Overall, mechanical press brakes are a practical choice for many workshops and manufacturing operations, particularly those with basic bending requirements and a focus on affordability and simplicity.
What is hydraulic press brakes?
A hydraulic press brake is a type of press brake that uses hydraulic cylinders to apply the downward force needed for bending metal or other materials. This type of press brake offers several advantages, including precision, speed, and versatility.
Here are some key features of hydraulic press brakes:
- Hydraulic System: Hydraulic press brakes utilize a hydraulic power system to control the motion of the ram, providing smooth and precise bending capabilities.
- Force Control: Hydraulic press brakes allow for precise control over the bending force, enabling operators to achieve accurate bends across a wide range of materials and thicknesses.
- Speed and Efficiency: Hydraulic systems offer fast and efficient bending cycles, making them suitable for high-volume production and complex bending tasks.
- Versatility: Hydraulic press brakes can handle a variety of bending applications, from simple bends to intricate shapes, and they are suitable for working with various materials, including metal sheets and plates.
Overall, hydraulic press brakes are widely used in metal fabrication, manufacturing, and other industries where accurate and efficient bending operations are crucial.
What is cnc press brakes?
A CNC press brake is a type of press brake equipped with a computer numerical control (CNC) system, which provides automated control over the bending process. This advanced technology enhances precision, flexibility, and efficiency in metal bending operations.
Key features of CNC press brakes include:
- Computer Control: The CNC system allows operators to input bending parameters and program a sequence of bends, angles, and tool changes, enabling precise control over the bending process.
- Automated Adjustments: CNC press brakes can automatically adjust the back gauge, ram positioning, and bending force, reducing the need for manual setup and enhancing repeatability.
- Versatility: CNC press brakes are capable of handling complex bend profiles and varying material thicknesses with ease, making them suitable for a wide range of bending applications.
- Productivity: By automating the bending sequence, CNC press brakes can significantly increase productivity and reduce setup times, especially for complex or repetitive bending tasks.
Overall, CNC press brakes are ideal for modern manufacturing environments requiring high precision, rapid turnaround times, and the ability to handle diverse bending requirements.
What is servo-Electric press brakes?
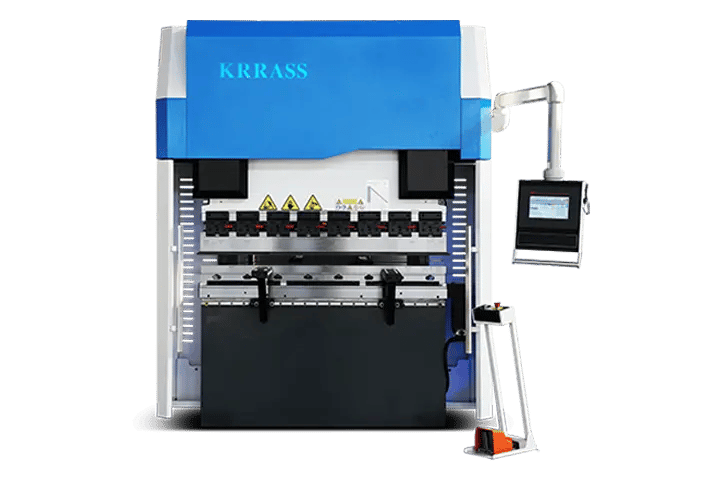
A servo-electric press brake is a type of press brake that employs a servo-electric motor to drive the ram, providing precise control over the bending process. Unlike traditional hydraulic press brakes, which use hydraulic fluid to generate force, servo-electric press brakes use an electric motor coupled with a system of ball screws or belts to move the ram.
Key features of servo-electric press brakes include:
- Precision and Control: Servo-electric press brakes offer exceptionally high levels of precision and control over the bending process, allowing for accurate positioning and consistent bending results.
- Energy Efficiency: Compared to hydraulic press brakes, servo-electric press brakes can be more energy-efficient, as they only consume power during the actual bending operation, without the continuous need for hydraulic fluid.
- Quiet Operation: The electric motor-driven operation of servo-electric press brakes results in quieter performance compared to hydraulic counterparts, making them suitable for noise-sensitive environments.
- Low Maintenance: Servo-electric press brakes generally have lower maintenance requirements due to the absence of hydraulic components, resulting in reduced downtime and operating costs.
Overall, servo-electric press brakes are well-suited for applications that demand high precision, energy efficiency, minimal maintenance, and quieter operation. They are particularly advantageous for industries focused on advanced manufacturing technologies and sustainable production practices.