When choosing press brake tooling, there are many factors to consider. Understanding these factors is crucial to get the correct results from your manufacturing processes of sheet metal bending. Press brakes are an integral part of almost all modern metal fabrication shops. Due to this, there has been an explosion of options for press brake tooling to accommodate a wide variety of applications.
This article explores the details of press brake tooling materials, styles, types, and important factors when considering press brake tooling.
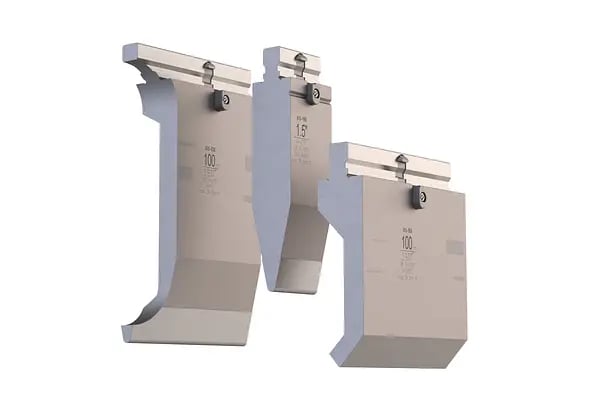
Table of Contents
What is Press Brake Tooling?
Press brake tooling is composed of dies and punches used in the operation of bending sheet metal. The tooling is not built into the machine, but rather swappable parts that are used for specific bends. The tooling is what comes into contact with the workpiece. As said before, the wide variety of applications calls for a wide variety of tooling.
What is the Main Purpose of Press Brake Tooling
The purpose of press brake tooling is to make the machine capable of bending various metals into different angles. Without this tooling, your press brake will be very limited in the type, shape, and size of bend it can perform. However, by incorporating different tooling into your shop, you can expand the application of a press brake. Different bend angles and radii can be formed by swapping the tooling. This allows press brakes to adapt to changing jobs.
Key Elements of Press Brake Tooling
Punches for Press Brake
- V-Die Punches: V-die punches, also known as bottoming or V-bottom punches, are the most commonly used punches in press brake operations. They feature a V-shaped groove that corresponds with the desired bend angle. V-die punches are versatile and suitable for a wide range of bending applications, from simple straight bends to complex profiles.
- Gooseneck Punches: Gooseneck punches, also called offset or horn punches, have a unique curved design that allows for bending close to the side walls of a workpiece or reaching over existing flanges. They are particularly useful for forming U-shaped or box-shaped bends with limited clearance.
- Radius Punches: Radius punches, as the name suggests, feature a rounded tip instead of a sharp point. They are used to create bends with a smooth, rounded inside radius, ideal for applications where a crisp edge is not required, such as architectural components or decorative elements.
- Acute Angle Punches: Acute angle punches are designed to create sharp, precise bends with acute angles less than 90 degrees. They are commonly used in applications requiring tight tolerances and precise geometries, such as aerospace or electronics manufacturing.
- Hemming Punches: Hemming punches are specialized punches used to create hemmed edges or folds in sheet metal. They feature a flattened or rounded tip that tucks the edge of the material back onto itself, providing a clean and finished appearance while increasing the strength of the bend.
- Offset Punches: Offset punches, also known as jog or step punches, have an offset design that allows for bending at a specific distance from the edge of the material. They are useful for creating bends with precise offsets or flanges, such as in enclosure or chassis fabrication.
- Custom Punches: In addition to standard punch designs, custom punches can be manufactured to meet specific bending requirements. Custom punches are tailored to unique applications, allowing for the creation of complex shapes, angles, and forms beyond the capabilities of standard tooling.
Dies for Press Brake
What Material is Press Brake Tooling
Chromium-molybdenum alloy steel (or chrome moly)is widely regarded as the best material for press brake tooling. Chrome moly steel has exceptional strength and is resistant to corrosion. Due to this strength and corrosion resistance, chrome-moly provides a long service life for tooling.
What is the Typical Hardness of Press Brake Tooling
The typical hardness of press brake tooling falls right around 45 HRC on the Rockwell scale. There are press brake tooling options that offer higher hardness based on bending application needs. In comparison, the hardness of stainless steel is approximately 28 HRC which is why tooling can bend parts made from these materials without incurring damage.
However, it is important to remember that when calculating bending needs, the hardness of tooling is not indicative of tonnage. The hardness instead indicates the ability to resist scratches and indentations when bending material. Indents lead to internal defects and compromise the press brake tooling. This is why the consideration of material used in press brake tooling is crucial.
Styles of Press Brake Tooling
The three most common types of press brake tooling are American, European, and New Standard.
American Tooling
American tooling is a style of press brake tooling that has a reduced surface area of the clamping mechanism. American tooling directs pressure through a straight line down the tool. This requires tool manufacturers to accurately grind the surfaces to the left and right of the holder in relation to the tip position. American-style tooling is generally cheaper than other options and is characterized by an ½ inch-broad tang.
European Tooling
European tooling has the defining characterization of having an offset holder. Being one of the most common styles, European tooling offers more options comparatively. Press brake operators and owners will typically have double the options of European-style tools compared to American styles. Due to their offset design, European tools tend to be more slim and therefore offer greater geometry options when bending. Additionally, because of the locking mechanism and design, clamping pressure is typically higher on European tooling. This achieves greater precision when conducting bends with your press brake.
New Standard Tooling System
The new standard tooling system introduced by Wila has been adapted by various tooling manufacturers. This system provides an auto-clamping mechanism that seats itself. This ensures the tooling is in the proper location for bending applications and helps to minimize user error in changing tooling. This provides high precision in the operation of the press brake. The design of these tools supports high-speed changeover. Typically tooling under 27.6 pounds utilizes a spring-loaded fast change button and tooling over 27.6 pounds utilizes a pin-locking system.
How to Choose the Right Press Brake Tooling
- Understand Your Bending Requirements: Begin by assessing the types of bends you'll be performing, such as straight bends, box bends, or intricate profiles. Consider the material type, thickness, and desired bend angles.
- Determine Tooling Types: Press brake tooling comes in various types, including V-dies, hemming dies, radius punches, and specialty tooling for specific applications. Identify the types of tooling that best suit your bending needs.
- Consider Material Compatibility: Different tooling materials are suitable for bending various types of metals, such as mild steel, stainless steel, aluminum, and exotic alloys. Ensure the tooling material is compatible with the materials you'll be working with.
- Evaluate Tooling Styles: Choose between American-style and European-style tooling systems based on your preferences and machine compatibility. American-style tooling typically features a tang and key design, while European-style tooling uses a clamping system.
- Assess Tooling Geometry: The geometry of the tooling, including the angle and radius, determines the bend characteristics. Select tooling with the appropriate geometry to achieve the desired bend radius and angle.
- Consider Tooling Length: The length of the tooling affects the bending capacity and flexibility. Longer tooling allows for bending larger workpieces and performing multiple bends in one setup.
- Factor in Tooling Maintenance: Consider the ease of maintenance and regrinding for prolonging the lifespan of your tooling. Choose tooling that is durable and easy to maintain to minimize downtime and costs.
- Evaluate Tooling Accessories: Some tooling systems offer accessories such as inserts, adapters, and safety features to enhance versatility and safety. Assess the availability and compatibility of accessories for your specific needs.
- Consult with Suppliers: Seek advice from press brake tooling suppliers or manufacturers to discuss your bending requirements and explore suitable tooling options. They can provide insights and recommendations based on their expertise.
- Test Tooling Compatibility: Before purchasing, test the compatibility of the selected tooling with your press brake machine. Ensure proper fit and alignment to avoid issues during operation.
Conclusion
Choosing the right press brake tooling is a decision that directly impacts the quality, efficiency, and longevity of operations. By understanding the various factors such as material type, thickness, and bending requirements, manufacturers can make informed decisions that optimize performance and minimize downtime. Additionally, investing in high-quality tooling, coupled with regular maintenance and proper storage practices, ensures consistent precision and extends the service life of the equipment. To start on your press brake tooling quote, contact the press brake experts at Krrass Machine Tools today!