hWhen it comes to press brake die capacity, it is essential to have a clear understanding of the maximum thickness and length of material that can be bent. This information is crucial for determining the suitability of a particular press brake for your specific fabrication needs. By knowing the die capacity, you can ensure that you have the right equipment to handle the materials you work with, avoiding costly mistakes and delays in production.
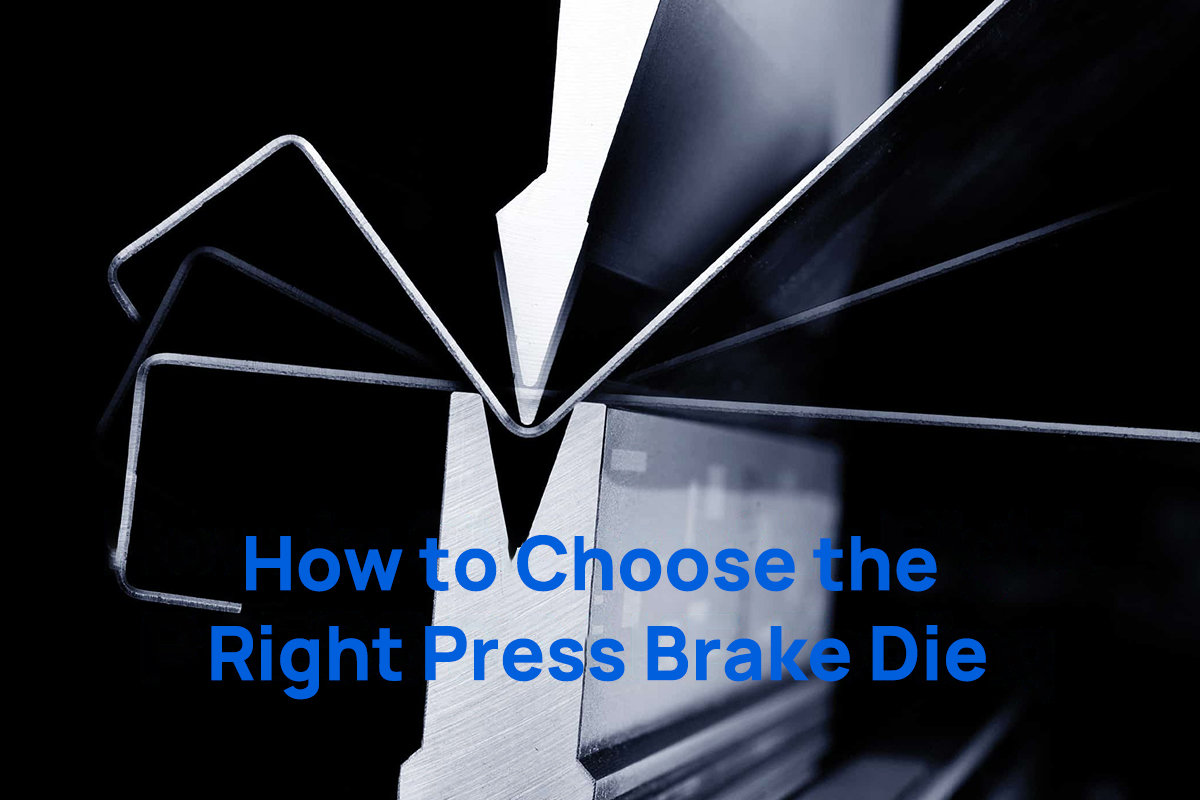
What Is Press Brake Die Capacity
Press brake die capacity refers to the maximum thickness and length of material that a press brake can effectively bend. It is a crucial factor in metal fabrication, as it determines the suitability of the press brake for specific bending needs. Understanding the die capacity of a press brake is essential for achieving accurate and consistent bends.
The thickness capacity of a press brake die refers to the maximum thickness of material that the machine can bend. This capacity is determined by the tonnage of the press brake, which represents the force required to bend the material. The tonnage required increases with the thickness of the material being bent. It’s important to select a press brake with sufficient tonnage capacity to handle the desired material thickness.
In addition to thickness capacity, the length capacity of a press brake die is also important to consider. This refers to the maximum length of material that can be bent by the press brake. The length capacity is determined by the distance between the press brake’s side frames, which limits the size of the material that can be accommodated. It’s crucial to choose a press brake with a length capacity that matches the size of the materials being worked with.
By understanding and selecting the appropriate press brake die capacity, metal fabricators can optimize their production processes. They can ensure that their press brake is capable of bending the desired material thickness and length, resulting in accurate and consistent bends. This not only improves the quality of the fabricated products but also enhances efficiency and reduces waste.
Importance Of Press Brake Die Capacity
When it comes to metal fabrication, understanding the importance of press brake die capacity is crucial. The capacity of a press brake die refers to its ability to handle certain thicknesses and lengths of material. This information is vital in determining whether a press brake is suitable for specific fabrication needs, ensuring accurate and consistent bends.
1. Determining Maximum Material Thickness
One of the key factors in press brake die capacity is the maximum thickness of material that the machine can bend. This is determined by the tonnage of the press brake. By knowing the maximum thickness capacity, metal fabricators can select the appropriate press brake for their needs. Using a press brake with insufficient tonnage for a particular thickness can result in inaccurate bends and potential damage to the machine.
2. Ensuring Optimal Production Processes
Another aspect to consider is the maximum length of material that can be bent. The length capacity of a press brake die is essential in determining the size and scale of projects that can be undertaken. By selecting a press brake with the appropriate length capacity, fabricators can optimize their production processes and improve efficiency. This ensures that projects can be completed within the desired timeframe, reducing downtime and increasing productivity.
3. Improving Product Quality
Selecting the right press brake die capacity is not only important for the efficiency of production processes but also for the quality of the end product. Using a press brake with the correct tonnage and length capacity ensures that bends are accurate and consistent. This leads to high-quality finished products that meet the required specifications. Consistency in bend angles and dimensions is crucial for creating parts that fit together seamlessly and function correctly.
Understanding the importance of press brake die capacity is vital for metal fabricators. By considering the maximum thickness and length capacity of a press brake die, fabricators can select the right equipment to optimize production processes and improve the quality of their products.
Factors Affecting Press Brake Die Capacity
When it comes to press brake die capacity, there are several factors that can impact the bending capabilities of the machine. These factors need to be taken into consideration when selecting the right equipment for a specific fabrication job. Let’s explore some of the key factors that affect press brake die capacity:
- Tonnage: The tonnage of a press brake is a crucial factor in determining its bending capacity. Tonnage refers to the amount of force that the press brake can exert on the material. Higher tonnage machines can handle thicker and longer materials, while lower tonnage machines are suitable for thinner and shorter materials.
- Material Type: Different materials have different bending characteristics, and this can affect the die capacity of a press brake. Harder materials like stainless steel or aluminum may require higher tonnage machines to achieve the desired bends, while softer materials like mild steel may require less tonnage.
- Material Thickness: The thickness of the material being bent is another important factor to consider. Thicker materials require higher tonnage machines to achieve the desired bends, while thinner materials can be handled by lower tonnage machines.
- Die Opening: The size of the die opening also plays a role in press brake die capacity. A larger die opening allows for bending larger and thicker materials, while a smaller die opening is suitable for smaller and thinner materials.
- Length of Bend: The length of the bend required also affects the die capacity of a press brake. Longer bends require higher tonnage machines to achieve the desired results, while shorter bends can be achieved with lower tonnage machines.
By considering these factors, fabricators can select the right press brake with the appropriate die capacity for their specific needs. This ensures accurate and consistent bends, optimizing production processes and improving overall efficiency and product quality.
Understanding Tonnage And Length Requirements
When it comes to press brake die capacity, one of the key factors to consider is tonnage. Tonnage refers to the force or pressure that the press brake can exert on the material being bent. It determines the bending capacity of the machine and is typically measured in tons. The higher the tonnage, the thicker and longer the material that can be bent.
Another important consideration is the length of the bend. This refers to the total length of the material that needs to be bent. Press brakes come in various lengths, and it’s essential to select a machine that can accommodate the required length of the bend.
To determine the appropriate tonnage and length requirements for a press brake, fabricators need to consider the type and thickness of the material they will be working with. Different materials have different properties and require varying amounts of force to be bent effectively. Thicker materials generally require higher tonnage, while softer materials may require less.
It’s worth noting that the die opening size also affects the press brake’s capacity. The die opening is the distance between the two tooling surfaces that form the bend in the material. It needs to be large enough to accommodate the material thickness and allow for proper bending.
By understanding the tonnage and length requirements, fabricators can choose a press brake with the right capacity for their specific needs. This ensures that they can accurately and consistently bend materials of the desired thickness and length, optimizing their production processes and achieving high-quality results. So, when considering press brake die capacity, it’s crucial to take into account tonnage, length of bend, material type, material thickness, and die opening size.
Considerations For Different Material Types
When it comes to press brake die capacity, it’s essential to take into account the different material types that will be used in fabrication. Each material has unique properties that can impact the bending process, and understanding these considerations is crucial for achieving accurate and consistent results. Here are a few factors to consider when working with different material types:
- Material Strength: Different materials have varying levels of strength, which can affect the tonnage required for bending. For instance, stainless steel is generally harder to bend compared to aluminum. It’s important to choose a press brake with sufficient tonnage to handle the strength of the material being used.
- Material Thickness: The thickness of the material being bent is another critical factor to consider. Thicker materials require more tonnage and a larger die opening size. By selecting a press brake with the appropriate capacity, fabricators can ensure that the machine can handle the thickness of the material without compromising the quality of the bend.
- Material Ductility: The ductility of a material refers to its ability to undergo plastic deformation without fracture. Some materials, such as copper or brass, are more ductile and easier to bend compared to others. Fabricators should consider the ductility of the material when determining the tonnage and die opening size required.
- Material Surface Finish: Certain materials, like stainless steel or polished aluminum, have delicate surface finishes that need to be protected during the bending process. Choosing a press brake with the right capacity and utilizing appropriate tooling can help prevent scratches or marks on the material’s surface.
By considering these factors, fabricators can select the appropriate press brake die capacity for the specific material types they will be working with. This ensures that the bending process is optimized for each material, resulting in accurate and consistent bends, improved product quality, and increased efficiency in the fabrication process.
Conclusion
Press brake die capacity is a critical factor in metal fabrication. It determines the maximum thickness and length of material that can be bent, as well as the tonnage required. By considering factors such as tonnage, material type, material thickness, die opening size, and length of bend, fabricators can select the right press brake with the appropriate die capacity for their specific needs. This ensures accurate and consistent bends, optimizing production processes and improving overall efficiency and product quality.
Tonnage is a key consideration, as it determines the bending capacity of the press brake. The length of the bend also plays a significant role, as it determines the total length of the material that needs to be bent. Fabricators must consider the type and thickness of the material they are working with to determine the appropriate tonnage and length requirements. The die opening size is another important factor, as it needs to be large enough to accommodate the material thickness and allow for proper bending.
By understanding the tonnage, length requirements, and material characteristics, fabricators can choose a press brake with the right capacity for each material type. This ensures accurate and consistent bends, resulting in optimized bending processes and improved product quality.