Why Press Brake Safety Is Important
Press brake safety is of utmost importance due to several key reasons:
Operator Protection: Press brakes involve moving parts, high pressure systems, and sharp tools, all of which pose significant risks to operators. Proper safety measures such as guards, light curtains, and interlocks are essential to prevent accidents and protect operators from injuries.
Compliance with Regulations: Regulatory bodies such as OSHA (Occupational Safety and Health Administration) have established strict safety standards for the operation of press brakes to ensure workplace safety. Compliance with these regulations is essential to avoid fines, penalties, and legal liabilities.
Prevention of Accidents: Press brake accidents can result in severe injuries such as amputations, crush injuries, and lacerations. Implementing safety measures helps reduce the likelihood of accidents, minimizing the risk of harm to operators and bystanders.
In the metalworking industry, specialized equipment known as press brakes is utilized for precision bending and shaping of metals. Despite their efficiency, one challenge with these machines is the requirement for highly skilled operators who must maintain unwavering focus throughout operation. Unfortunately, even with experienced and attentive operators, the risk of injury while handling press brakes persists.
Hence, implementing press brake safeguarding measures to mitigate such risks is imperative. Organizations like the Occupational Safety and Health Administration (OSHA) have established stringent standards to ensure the safety of individuals working with this equipment. This post underscores the importance of adhering to industrial safety standards and provides essential guidelines for press brake safety.
Common Harzards Related To Press Brake
These hazards include:
Caught-in or Caught-between Hazards: Operators' body parts or clothing can get caught in the moving parts of the press brake, leading to severe injuries or amputations.
Crushing Hazards: The powerful force exerted by the press brake during operation poses a risk of crushing injuries to operators who come into contact with the machine's moving components.
Striking Hazards: Materials being worked on by the press brake may be ejected forcefully, posing a risk of striking operators and causing injuries.
Noise and Vibration Hazards: Press brakes can generate high levels of noise and vibrations during operation, which can lead to hearing damage, fatigue, and other health issues if proper precautions are not taken.
Exposure to Hazardous Substances: Some materials processed by press brakes may release hazardous substances, such as fumes or particulates, which can pose health risks if inhaled or ingested.
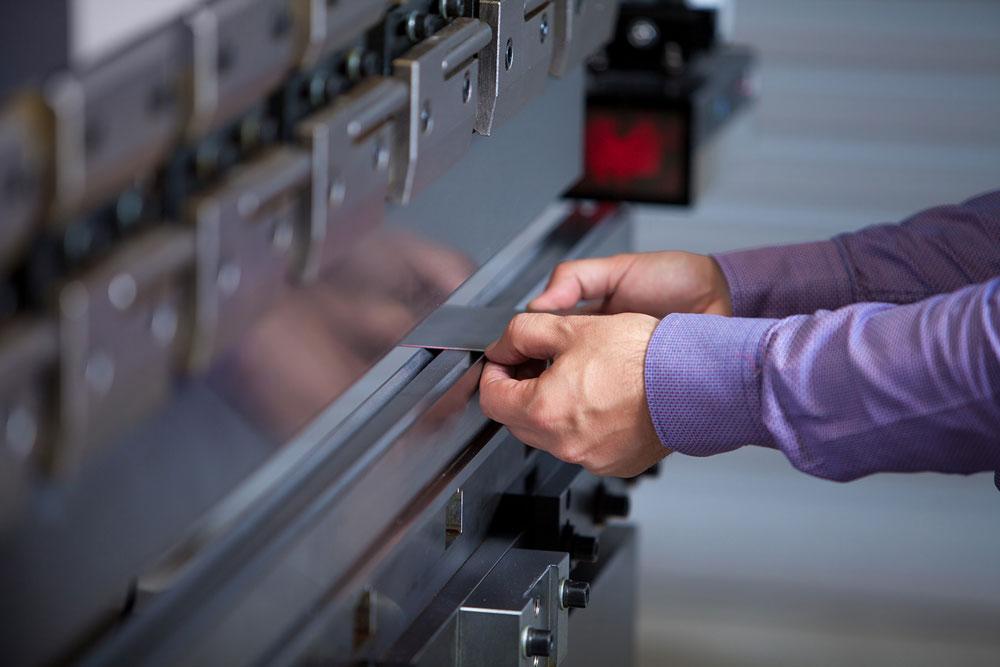
Industrial Press Brake Safety Standards
In order to avoid accidents with press brake, metalworking service providers need to comply with the following standards.
OSHA- General Duty Clause 1910.212:
This standard is set by the Occupational Safety and Health Administration (OSHA) for industrial safety. It requires business owners to provide industrial protection to employees.
ANSI B11.3:
The American National Standard Institute (ANSI) has set the safety standard for operating heavy-duty, hazardous industrial equipment. The use of press brakes is cited under this standard, therefore many industries in the United States follow ANSI B11.3- 2012. This ANSI standard advises the use of Active Opto-electronic Protective Devices (AOPD) to avoid common press brake hazards. It also sets a speed limit of restrictive10 mm/sec for press brake operation.
Now as the safety standards are discussed, the question arises, how to safeguard press brakes?
Let us discuss some ways to safeguard press brakes to avoid accidents at the workplace.
How To Ensure Press Brake Safety
Different ways to secure the press brake system and operators from accidental hazards are detailed as follows.
Awareness Barrier:
Awareness barrier is one of the effective ways of safeguarding press brakes. It involves securing the back end of the press brake machine from any interruption. Depending on local OSHA standards, it is important to protect backend by adding an awareness cable, chain, or barrier with a pictorial warning sign. This isn’t considered a preventive measure but a caution indication.
Barrier Guards:
According to OSHA standards, the press brakes are to be protected with barrier guards, on both the ends. The interlocked barrier guards can be used to prevent hands from going inside the machine area while the operator tries to reach the punch and die. The latest barrier guards feature electrically interlocked fasteners that prevent any manual flawed activity during the operation.
Light Curtains:
Light curtains are sensitive surfaces between the operator and press brake. These safeguarding tools feature vertically positioned transmitters and receivers where laser beams transmit in between. These laser beams create a vertical sensing surface between the operator and the machine. If anytime the operator’s hand comes in contact with the laser curtain, the machine will stop working. It is only possible in press brakes due to the quick responsive nature of the machine. These machines are hydraulic, therefore act immediately on the termination or activation commands. This is a truly effective safeguarding tool used
Two-Hand Controls:
This is another effective method of protecting hand injuries caused by press brakes. These devices inspire operators to use both their hands to trigger the stroke. There are two buttons on each side of the device, which must be pressed at the same time to start the press brake. If a button is not pressed properly then the machine will stop working.
Laser AOPD:
Laser AOPDs is the latest press brake safeguarding technology. This technology offers to safeguard to absolute zero distance. It features speed limit monitoring as well as operator safety. If these AOPD tools are installed and operated correctly, it can give absolutely safety from press brake accidents.