Industries worldwide have been advancing rapidly thanks to technological innovations, with various machines and tools becoming essential assets. The manufacturing sector, in particular, relies heavily on specialized equipment like the CNC press brake machine, which is crucial for fabricators and overall industrial progress. Understanding how to operate a CNC press brake is essential for anyone in the field. This article will delve into the intricacies of CNC press brake machines, exploring their functionality and key features. So, if you're ready to enhance your knowledge, let's dive in!
Table of Contents
What is a CNC Press Brake Machine?
Before delving into its operational mechanisms, let's first understand what a CNC press brake machine is.
A CNC press brake machine is a type of press brake that integrates a Computer Numerical Control (CNC) system. This advanced system allows the machine to efficiently bend and manipulate metal sheets, whether they are a few millimeters or several meters long.
There are two primary types of CNC press brake machines:
Type 1 (Down Forming): This type features a fixed bed (bottom) with a V-shaped tool attached to it. The top beam, also V-shaped, applies force to press the metal against the V-shaped tool.
Type 2 (Up Forming): This type has the same components as Type 1. However, in this configuration, the top portion is fixed, while the bottom portion moves.
Regardless of the type, both configurations achieve the same results, allowing for a wide range of shapes and designs in the final product. Now that we've covered the basics of what a CNC press brake machine is, let's move on to understanding how to operate a CNC press brake.
How Does a CNC Press Brake Machine Work?
A CNC press brake machine is a mechanical tool powered by either a hydraulic or electrical system, integrated with a CNC system for precise and accurate bending of raw materials.
The operation of a CNC press brake machine is straightforward. First, you input the product specifications into the machine, detailing the exact angles and bends required. Once the CNC system analyzes and understands these instructions, it begins the bending process.
The machine uses hydraulic or electric force to create the bends, depending on whether it's a hydraulic or electric press brake. Based on the type of machine (down forming or up forming), the force is applied to the corresponding moving part. This moving part then presses the metal sheet against the fixed part, forming the desired bend.
For CNC machines, the CNC system precisely controls the movement of the metal sheet according to the programmed instructions, ensuring accurate and consistent results.
The V-shaped tool, typically referred to as the die (attached to the fixed part) and the punch (attached to the moving part), can be changed based on the desired shape. There are various tool sets available to create different bends and shapes, allowing for versatile and precise metalworking.
Features of CNC Press Brakes
CNC Control System
The CNC control system is the core feature that enables precise control over the bending process. It allows for the programming of complex bending sequences and ensures high accuracy and repeatability. Operators can input detailed instructions, including angles and bend sequences, which the machine executes with consistency. Modern CNC systems often come with user-friendly interfaces, such as touchscreens and intuitive software, making it easier for operators to program and control the machine.
Hydraulic or Electric Power System
CNC press brakes can be powered by either hydraulic or electric systems. Hydraulic systems offer high force and are ideal for heavy-duty applications, enabling the machine to handle thick and tough materials with ease. Electric press brakes, on the other hand, are known for their energy efficiency and quieter operation, making them suitable for environments where noise reduction and energy savings are important considerations.
Back Gauge System
The back gauge system is crucial for positioning the metal sheet accurately, ensuring precise bends. This system can be automatically adjusted according to the CNC program, accommodating different bending operations and material sizes. By automating the positioning of the sheet, the back gauge system significantly reduces manual setup time and increases overall productivity.
Tooling Flexibility
CNC press brakes support various tooling options, including different types of dies and punches. This flexibility allows for a wide range of bending operations, from simple bends to complex shapes. Many CNC press brakes are designed for quick and easy tool changes, which minimizes downtime and enhances operational efficiency.
Safety Features
Modern CNC press brakes are equipped with advanced safety features such as laser guards, light curtains, and emergency stop buttons. These features are designed to protect the operator from potential hazards during the bending process and ensure that the machine complies with international safety standards, providing a secure working environment.
Operation Mechanism of a CNC Press Brake
The CNC press brake is a sophisticated machine designed for precision metal bending. Its operation involves several key components and processes that ensure accurate and efficient bending. Here’s a comprehensive overview of its operation mechanism:
1. Machine Components
- Frame: The robust frame forms the backbone of the press brake, providing essential stability during operation. Its solid construction ensures minimal vibrations and maintains accuracy throughout the bending process.
- Bed: The stationary lower section where the metal sheet is placed. The bed supports the lower die and ensures the metal is correctly positioned and aligned for accurate bending.
- Upper Beam: This moving component houses the upper die and applies the necessary force to the metal sheet. It is driven by hydraulic or electric systems and is crucial for achieving the desired bend.
- Lower Die (V-die): Fixed to the bed, the lower die shapes the metal sheet. The V-die’s profile determines the bend’s angle and radius, affecting the final product’s geometry.
- Upper Die (Punch): Mounted on the upper beam, the punch applies force to the metal sheet, pressing it against the lower die to form the bend. Its shape and size are tailored to the specific bending requirements.
- Back Gauge: A critical positioning tool that helps accurately place the metal sheet on the bed. It ensures that each bend is made at the correct location, maintaining consistency across multiple parts.
- Hydraulic or Electric System: This system powers the press brake. Hydraulic systems use fluid pressure to move the upper beam, while electric systems rely on motors and drives for precise control. Both systems provide the force required to perform bending operations.
2. Programming and Setup
- Input Parameters: Operators enter essential parameters into the CNC control system, including material type, thickness, bend angles, and tool specifications. The precision of these inputs is crucial for achieving accurate bends.
- Tooling: Appropriate upper and lower dies are selected based on the bending requirements and installed on the press brake. Proper installation and alignment of these dies are critical to ensure accurate and uniform bends.
- Machine Calibration: The CNC system calibrates the machine based on the entered parameters. This involves adjusting hydraulic pressure or electric drive settings to match the specific requirements of the material and the desired bend.
3. Bending Process
- Material Placement: The metal sheet is positioned on the bed using the back gauge and other alignment tools. Proper placement is vital for ensuring that the bends are consistent and meet the specified dimensions.
- Program Execution: The CNC control system executes the programmed sequence, controlling the upper beam’s movement. It calculates the exact position of the upper die, the bending sequence, and any required adjustments to achieve precise bends.
- Bending Action: As the upper beam descends, it applies force through the upper die to press the metal sheet against the lower die. The CNC system manages the descent speed, pressure, and angle to achieve the desired bend with high precision.
- Springback Compensation: The CNC system accounts for material springback—the tendency of the metal to return slightly to its original shape after bending. Adjustments are made to the bending angles to ensure the final product matches the desired specifications.
4. Monitoring and Adjustment
- Real-Time Monitoring: Operators use the CNC control’s graphical interface to monitor the bending process in real time. The system provides visual feedback on the progress, allowing for immediate adjustments if necessary.
- Adjustments: Operators can make on-the-fly adjustments to the program or machine settings to correct any issues or accommodate changes in material behavior. This ensures that each part meets the required specifications.
5. Completion and Shutdown
- Product Inspection: After the bending process is complete, the finished metal sheet is inspected to verify that it meets the required dimensions and quality standards. Any discrepancies are addressed before proceeding.
- Machine Shutdown: Once the task is finished, the press brake is turned off, and the power supply is disconnected. The work area is cleaned, and all tools and materials are returned to their proper places. Regular maintenance and proper storage help ensure the machine’s longevity and readiness for future use.
By understanding these detailed operational mechanisms, users can effectively manage and utilize a CNC press brake to achieve high precision in metal fabrication, enhancing both efficiency and product quality in manufacturing processes.
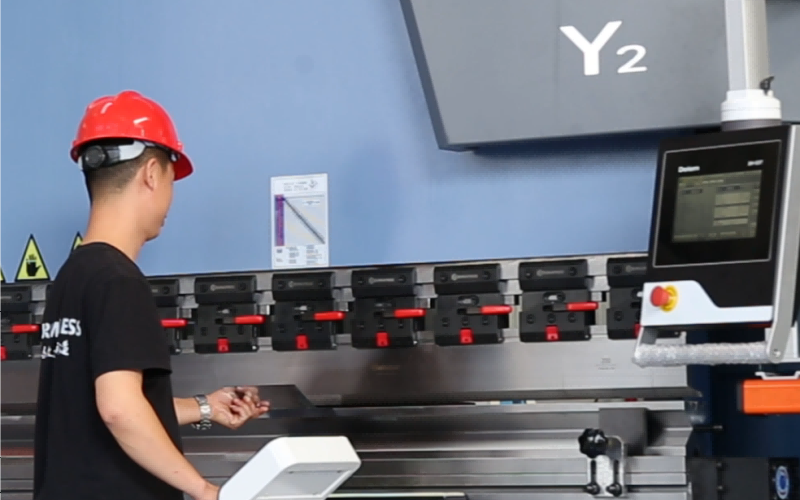
Is CNC Press Brake Hard to Operate?
Press brake operators are integral to the metal fabrication and manufacturing industry, where precision and efficiency are key. Their responsibilities include setting up and programming press brake machines, interpreting technical drawings, selecting appropriate tooling, and executing accurate metal bends. To excel in this role, operators must possess a combination of technical and interpersonal skills.
Soft Skills for Press Brake Operators
Attention to Detail:
Precision is critical in press brake operations, where even minor deviations can lead to significant errors. Operators must meticulously follow specifications to ensure that bends are executed accurately. This skill helps prevent costly mistakes and maintains the integrity of the final product. Maintaining a clean and organized workspace further supports accuracy and reduces the likelihood of errors.
Good Communication:
Effective communication is essential for interpreting and conveying technical details, such as reading and explaining blueprints and specifications. Clear communication with colleagues, supervisors, and quality control teams ensures that everyone is aligned on production goals and standards. This skill also aids in addressing and resolving any issues that may arise during the manufacturing process.
Time Management:
Press brake operators often work under tight deadlines. Strong time management skills are crucial for balancing productivity with quality. Efficiently managing time helps meet production targets while ensuring that each piece meets the required standards. Operators must also be adept at prioritizing tasks and managing workflow to optimize overall efficiency.
Problem-Solving Skills:
The ability to troubleshoot and resolve machine issues quickly is vital. Operators need to be skilled in identifying and addressing problems that may occur during operation, such as mechanical failures or deviations from specifications. Effective problem-solving ensures that production remains on track and minimizes downtime.
Adaptability:
Manufacturing environments are dynamic and often subject to rapid changes. Operators must be adaptable to handle unforeseen challenges and shifting production demands. Being flexible and open to learning new techniques or adjusting to new technologies is essential for maintaining productivity and staying current with industry advancements.
Hard Skills for Press Brake Operators
Tool Operation:
Proficiency in operating manual, semi-automatic, or automatic press brake machines is essential. Operators must be trained to handle these machines effectively, ensuring safety and preventing damage. Understanding the functions of different controls and features is also crucial for optimizing machine performance.
Choosing the Right Tooling:
Selecting the appropriate punches and dies for specific bending tasks is key to achieving desired outcomes. Operators must be knowledgeable about different tooling options and their applications. This includes understanding how various tools affect the bending process and choosing the right combination for different metals and angles.
Measurement Accuracy:
Accurate measurement is fundamental to producing high-quality bends. Operators must be skilled in using measurement tools such as calipers, micrometers, and rulers. They should also be familiar with different measurement units and conversion techniques to ensure that products meet exact specifications.
Blueprint Reading:
The ability to interpret technical drawings, blueprints, and engineering specifications is crucial for setting up the machine correctly. Operators need to understand detailed schematics to ensure that each metal component is manufactured according to the precise requirements outlined in the drawings.
How to Improve Your Press Brake Operator Skills
On-the-Job Training:
Gaining hands-on experience by working alongside seasoned professionals provides valuable insights and practical knowledge. On-the-job training helps operators develop proficiency in machine operation and problem-solving while adapting to specific workplace practices.
Continuous Learning:
Engaging in ongoing education through workshops, seminars, and industry events helps operators stay informed about the latest technologies and techniques. Subscribing to trade magazines and participating in online forums can also provide updates on industry trends and best practices.
Feedback and Reflection:
Actively seeking feedback from colleagues and supervisors allows operators to identify areas for improvement. Reflecting on performance and incorporating constructive criticism helps refine skills and enhance overall effectiveness.
Mentorship:
Building relationships with experienced mentors within the organization can provide valuable guidance and support. Mentorship offers practical advice and career development opportunities, helping operators navigate challenges and advance their skills.
By cultivating both hard and soft skills, press brake operators can improve their performance, contribute to successful manufacturing outcomes, and foster career growth in the metalworking industry.
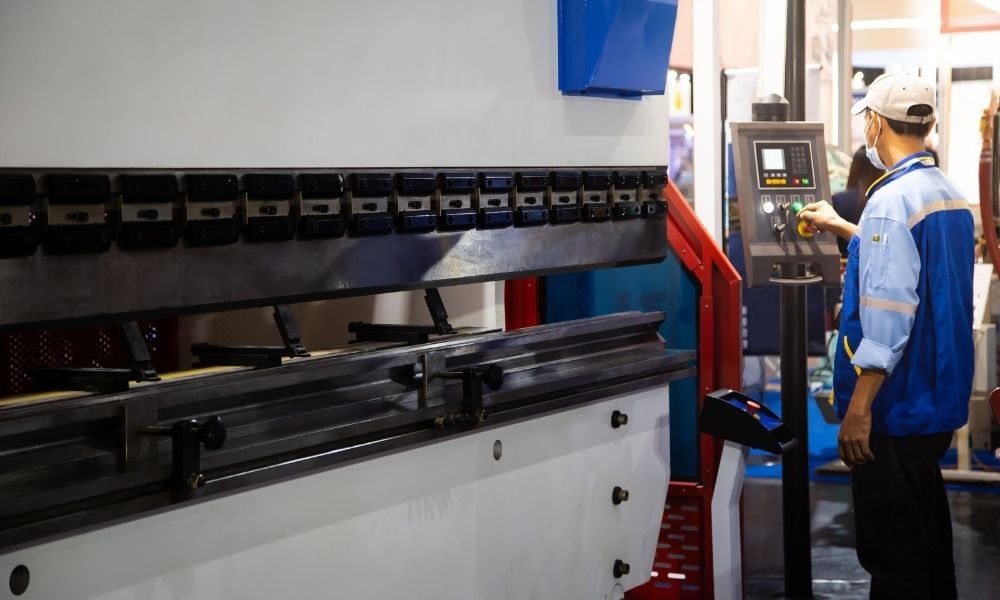
How to Programme CNC Press Brake Rapidly
Do you know how easy it is to program a modern CNC press brake? If you can use a smartphone, you can handle the latest generation CNC controls, allowing you to move from a paper design to a ready-to-run program in less than a minute!
The newest controls feature large, user-friendly touchscreens and offer intuitive programming, making it straightforward to create programs, even for complex parts.
How to Use a CNC Press Brake Control
Firstly, select your material parameters, such as thickness, width, and material type. Then, choose the top and bottom tools you want to use or continue with the current tools. Next, simply draw out the part by tapping on the screen and adjust the dimensions and angles as required. You’re now ready to create the program.
Calculate the Program
The CNC will calculate and optimize the program automatically. If there are any clashes, it will confirm that no solution is available. However, you have the option to override the control and manually sequence the part if an acceptable clash occurs, such as when the material can flex sufficiently to accommodate it.
Optimizing the bend sequence involves determining the best order for flips and rotations, and automatically programming the bend angles, back gauge position, retract function, and return heights. The CNC also calculates material stretching to ensure accurate developed length.
Run the Program
A graphical display of the current program allows the operator to follow the on-screen sequence and orientation of bends. The CNC calculates the Y1 and Y2 cylinder axis positions to achieve the required degrees in the program, accounting for springback in the material. If the springback is more or less than expected, a simple adjustment can be made.
Advanced Features
While these controls are user-friendly, they also include advanced features for users who need more from the machine. Many adjustments can be made to bending programs, including approach/return speed, mute point, pinch point, and dwell time. For specialized bending jobs such as coining or forming, Y-axis learning can be used to 'teach' the machine the required parameters.
How to Operate a CNC Press Brake: A Comprehensive Guide
Inspecting the Equipment
Before operating the press brake, conduct a thorough inspection to ensure the machine is in optimal working condition. Check all components for any signs of damage or malfunction. Verify that the hydraulic or electrical systems are functioning correctly. Ensure that safety features are operational and that there are no abnormal conditions. It's also crucial for all operators to wear appropriate safety gear, including protective goggles, gloves, and steel-toed shoes, to minimize the risk of injury.
Selecting and Installing Dies
Choose the correct top and bottom dies based on the specific bending requirements of your project. The selection of dies will depend on factors such as the material type, thickness, and the desired bending angle. Properly install the dies in the machine, ensuring they are securely fastened and aligned to avoid any operational issues during the bending process.
Setting Up Machine Parameters
Configure the press brake’s parameters to match the specifications of the metal sheet being used. Adjust settings such as pressure, speed, and stroke length according to the material’s properties and the required bend angles. Accurate parameter settings are essential for achieving precise bends and maintaining the quality of the finished product.
Positioning the Metal Sheet
Place the metal sheet on the work table of the press brake. Utilize back gauges, side stops, or other positioning tools to ensure the metal sheet is correctly aligned and secured. Proper positioning is vital for achieving even and accurate bends. Verify that the sheet is level and properly supported to prevent any movement during the bending process.
Operating the Machine
Activate the machine by pressing the start button. This action will cause the upper punch to descend and begin the bending operation. Monitor the machine as it performs the bend, ensuring that the metal sheet is being bent as per the set parameters. Stay alert and keep your hands and other body parts clear of the moving parts to avoid accidents.
Continuous Monitoring
Throughout the bending process, continuously observe the operation to ensure the metal sheet is being bent evenly and accurately. Regularly check the alignment and adjust the settings if necessary. Immediate intervention may be required if any issues arise, such as misalignment or excessive wear on the dies.
Completing the Task
Once the bending process is complete, stop the machine and carefully remove the bent metal sheet. Inspect the finished product to ensure that the bending angle and precision meet the required specifications. Make any necessary adjustments to the parameters for future bends if discrepancies are found.
Shutting Down the Machine
After completing the operation, turn off the press brake and disconnect the power supply. Clean the work area, removing any debris or metal scraps. Properly store all tools and materials, ensuring that everything is in its designated place. Regular maintenance and organization of the workspace contribute to a safe and efficient working environment.
By following these steps, you can effectively operate a press brake machine, ensuring safety and achieving high-quality results in your metal fabrication tasks.
Safety Tips for Operating a Press Brake
Ensure Proper Training
Before operating the press brake, confirm that all workers have received comprehensive training and are thoroughly familiar with the operating procedures. This ensures that everyone is aware of how to safely and effectively use the machine.
Wear Personal Protective Equipment (PPE)
Always wear appropriate personal protective equipment, including gloves and safety goggles, when working with the press brake. PPE is essential for protecting against potential hazards such as sharp edges and flying debris.
Keep Body Parts Clear
Never place your hands, fingers, or other body parts between the upper die and the bottom die, or in any part of the workbench while the machine is in operation. This precaution helps prevent serious injuries from the powerful forces involved.
Maintain a Clean and Organized Workspace
Ensure that the working area around the press brake is clean, tidy, and free of any obstacles. A clutter-free workspace reduces the risk of accidents and allows for better maneuverability and access to the machine.
Avoid Loose Clothing and Accessories
Do not wear loose clothing, jewelry, or accessories that could become entangled in the machine. Secure long hair and avoid wearing anything that might get caught in the moving parts of the press brake.
Regular Equipment Maintenance
Conduct regular checks and maintenance on the press brake to ensure it remains in optimal working condition. Routine inspections and servicing help identify potential issues before they lead to malfunctions or safety hazards.
Do Not Adjust or Maintain While Operating
Never attempt to adjust, repair, or perform maintenance on the press brake while the machine is running. Always stop the machine and disconnect the power before making any adjustments or repairs to avoid accidents and injuries.
By adhering to these safety tips, you help ensure a safer working environment and reduce the risk of accidents while operating the press brake. Prioritizing safety not only protects individuals but also contributes to the overall efficiency and reliability of the manufacturing process.
Maintenance and Care for a CNC Press Brake
Maintaining and caring for a CNC press brake is crucial to ensure its optimal performance and longevity. Here are a few key points to keep in mind:
Regular Cleaning: It’s important to keep the CNC press brake clean and free from debris. Regularly remove any accumulated dust, chips, or other materials that may affect its operation. Use appropriate cleaning tools and techniques to avoid damaging the machine.
Lubrication: Proper lubrication is essential for the smooth functioning of the press brake. Follow the manufacturer’s guidelines and lubricate the necessary parts regularly. This helps prevent friction and ensures smooth movement, reducing wear and tear.
Inspection and Maintenance Schedule: Create a routine inspection and maintenance schedule for the CNC press brake. Regularly check for any signs of wear, damage, or misalignment. Address any issues promptly to avoid further damage and potential breakdowns.
Software Updates: Keep the CNC press brake’s software up to date. Manufacturers often release software updates to enhance performance, add new features, and address any potential security vulnerabilities. Regularly check for updates and install them as recommended.
Tooling Maintenance: The tooling used in a CNC press brake plays a vital role in the quality of the bends and overall performance. Regularly inspect the tooling for any signs of wear or damage. Replace worn-out or damaged tooling to ensure accurate and consistent results.
Remember, proper maintenance and care not only extend the lifespan of the CNC press brake but also contribute to a safer work environment. Regularly following these maintenance practices will help minimize downtime, improve efficiency, and ensure the machine operates at its best.
Keep reading for more tips on operating a CNC press brake safely.
How to Troubleshoot Common Issues with a CNC Press Brake
When operating a CNC press brake, it’s important to be prepared for any potential issues that may arise. Here are some common problems that you may encounter and how to troubleshoot them:
Misalignment of the Ram and Bed: If you notice that the ram and bed of the press brake are not aligned properly, it can affect the accuracy of the bends. To fix this issue, you can use the machine’s manual adjustment feature to realign the ram and bed. Make sure to follow the manufacturer’s guidelines and instructions for proper adjustment.
Inconsistent Bending Angles: If you are experiencing inconsistent bending angles, it could be due to improper tooling setup or worn-out tooling. Check the tooling and ensure that it is properly aligned and in good condition. If necessary, replace the worn-out tooling with new ones.
Material Slippage: Sometimes, the material being bent may slip or move during the bending process, resulting in inaccurate bends. To prevent this, make sure that the material is properly secured before starting the bending operation. You can use clamps or other securing devices to hold the material in place.
Electrical or Software Issues: Occasionally, you may encounter electrical or software issues with the CNC press brake. If the machine is not responding or functioning properly, check the power supply and connections to ensure they are secure. Additionally, make sure that the software is up to date and functioning correctly. If the problem persists, consult the manufacturer or a qualified technician for further assistance.
Final Thought
Operating a CNC press brake involves a series of precise steps that ensure accurate and efficient metal bending. By understanding and following the outlined procedures, from setting up the machine and inputting parameters to executing the bending process and performing post-operation tasks, you can optimize the performance of your press brake and achieve high-quality results.
The key to successful operation lies in meticulous preparation, including proper calibration, accurate programming, and careful material handling. Regular monitoring and timely adjustments during the bending process are essential for maintaining precision and achieving the desired outcomes. Additionally, adhering to safety protocols and conducting routine maintenance will ensure that your CNC press brake remains in optimal condition, safeguarding both the equipment and the operator.
By mastering these operational steps, you not only enhance your productivity but also contribute to the overall quality and efficiency of your manufacturing processes. Whether you're a seasoned operator or new to CNC press brakes, continuous learning and practice will help you leverage the full capabilities of this advanced machinery.
For more information or personalized guidance on operating CNC press brakes, feel free to reach out to Krrass experts in the field or visit our website for additional resources and support.
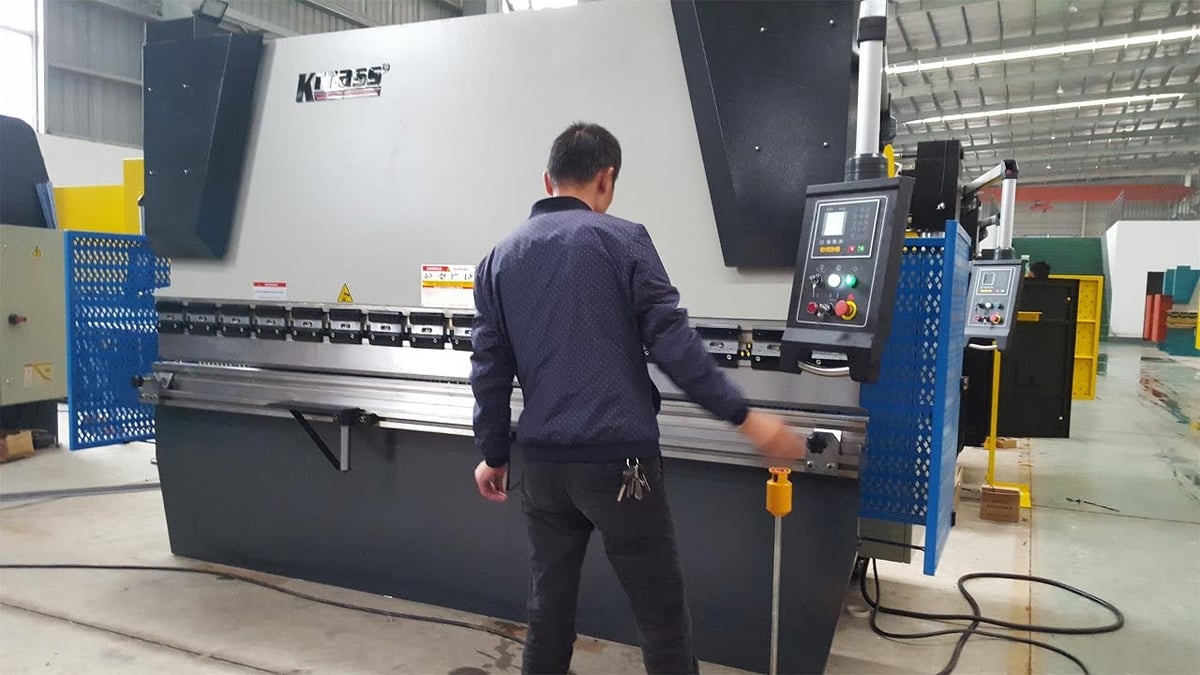