A press brake consists of several key parts, including two C-shaped frames on the left and right sides that form the main structure. The bottom workbench and top crossbeam are attached to these frames. The plunger section includes a crossbeam with a top punch and a workbench with a bottom die, which are essential for the bending process. The back gauge provides precise positioning, ensuring accuracy during operations. While the basic components of a press brake remain consistent across models, the driving mechanisms, such as manual, hydraulic, or CNC systems, may differ. CNC press brakes, in particular, utilize electrical hydraulic servo systems and linear scales for enhanced control and precision in bending operations. Each of these press brake parts plays a crucial role in achieving the desired accuracy and efficiency.
What Is the Press Brake?
In the realm of metal fabrication, a crucial tool that plays a significant role is the press brake. But what exactly is it? The press brake, often also referred to as a brake press machine, is a machine tool used primarily for bending sheet and plate material. It forms predetermined bends by clamping the workpiece between a matching punch and die.
Essentially, the press brake is a piece of manufacturing equipment where a tool, die, and sheet metal are placed. The die, which is shaped as per the required bend, rests on the table (or bed). The sheet metal is located on top of the die, while the tool, or punch, presses down onto the sheet metal and forces it into the die to form the preferred bend.
From the automotive industry to aircraft manufacturing, and from kitchen appliances to construction, press brakes are employed widely. They are integral for shaping metal parts for various industrial applications and are noted for their precision and efficiency. A range of press brake models is available, from manual to CNC (Computer Numeric Control) machines, each offering specific advantages based on the requirements.
It's essential to note that the function and efficiency of a press brake hinge significantly on its components. To understand the process of bending and shaping metal with utmost precision, one needs to delve deeper into its structure and the different press brake parts.
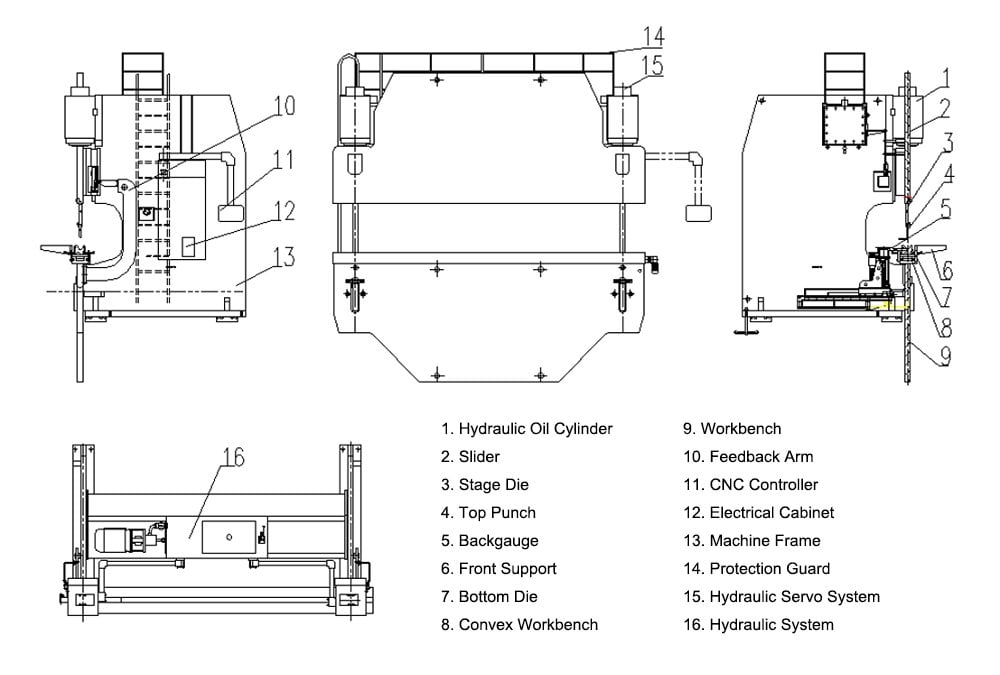
Importance and Applications of Press Brakes
In the manufacturing world, press brakes have an undeniable significance. They have transformed the way we shape and design metallic parts, adding to the precision, uniformity, and efficiency of the process. Thanks to press brakes, we have a consistent method to create intricate designs and complex bends in metal sheets and plates.
One of the principal reasons for their critical role is the wide range of applications. Press brakes are versatile tools that cater to numerous industries. These industries demand strict standards for the manufacturing of their products, where the tolerance for error is minimal. Therefore, the usage of press brakes becomes inevitable.
Automotive Industry
In the automotive industry, where precision and accuracy are paramount, brake press machines are extensively used. They shape and bend metal parts such as body panels, frames, brackets, and other essential parts of vehicles.
Aerospace Industry
The aerospace industry also reaps the benefits of press brakes. They help in shaping parts of airplanes, spacecraft, and related machinery, where the necessity for precise bends and folds is of utmost importance.
Construction and Infrastructure
In construction and infrastructure, press brakes are utilized for manufacturing structural steel, HVAC parts, roofing, and other equipment. The shaping of these materials is crucial for ensuring the durability and stability of our buildings and infrastructure.
Press Brake Parts Explained
Frame
The main structure that supports the entire machine.
It is usually a high strength fully welded C-shaped structure, and composed of vertical plates on both left and right, bed (workbench) and connecting structures.
The depth of frame is equivalent to throat depth, which offers much bending space.
There are also monitoring tools on the frame, which can detect springback and keep it to a minimum.
Ram
The ram, during the process of opening die (the process of separating the upper and lower dies), is a die component which can slide vertically or form a certain angle responding to the opening die direction.
It drives top punch to do reciprocating linear movement relative to the bottom die to achieve bending sheet metal, thus a specific bending angle or arc will be formed.
The movement of ram contains four parts as following: machine homing, rapid drive, working stroke, and slide return.
It can be divided into top parts and bottom parts. And also it is a driving mechanism component, which can applies pressure to the machine.
Besides, the ram is made of steel plate, and can be connected with oil cylinder through piston rod, driven by synchronized hydraulic cylinders on both sides.
The linear scale on the both sides of ram can provide precise positioning for synchronous movement.
With the help of oil cylinder and mechanical stopper, the ram can avoid crowning.
It works with oil cylinder, mechanical stopper and fine adjustment structure to compose ram parts. Via hydraulic pressure, it drives the piston (rod) to move up and down.
The mechanical stopper is controlled and adjusted by the numerical control system.
Workbench
The workbench is the foundation of the press brake. The tool holder for the bottom dies is installed on the workbench.
Workbench is one of the three components in press brake (left and right oil cylinder, workbench, ram), and made of base and pressure plate.
It is operated by a button box (a device for controlling the operation of press brake), and drives motor to move back and forth along with back gauge.
It is controlled by CNC system to determine the moving distance.
There are two ways of movement: one is the downward movement of the top punch, and the other is the upward movement of the bottom die.
The beam drives the ram to exert a force downward, which is evenly distributed.
The crowning mechanism of the press brake workbench can adjust the force distribution accordingly.
When you select one, it is crucial to consider choosing a relatively shorter size while still satisfying the requirements of the machining tasks.
Back Gauge
The back gauge is a crucial part of a press brake, responsible for controlling and adjusting the position and length of the workpiece during the bending process. Located at the rear of the machine, it ensures precise positioning of the workpiece before bending. Driven by various motors, the back gauge moves across different axes, with the ball screw and timing belt ensuring synchronized movement. Controlled by the CNC system, the back gauge can operate on six axes: the R-axis for upward and downward movement, the X-axis for forward and backward movement, and the Z-axis for left and right movement. During operation, the workpiece is placed on the die, pushed to fit with the stop finger, and then bent in the correct position. The back gauge limits the movement of the workpiece to ensure accuracy and can be adjusted via motor, servo motor, or cylinder. Operators set the position and length of the back gauge through the press brake's control system to meet the specific requirements of different workpieces.
(1) The stop finger is a key component that displays the size of the processed workpiece as the front and back gauge adjust their displacement. It moves smoothly along the linear guide rail and can be adjusted up and down for easy and efficient control. Typically, a press brake features multiple stop fingers, configured based on specific operational needs. These point-contact fingers help prevent issues like insufficient straightness in the sheet metal, allowing for accurate bending of various lengths of metal parts.
(2) The back gauge bar is a rod-shaped assembly that works in tandem with the stop finger, enabling movement and positional adjustments through electric or hydraulic drives. Its position is precisely controlled by the press brake’s control system.
(3) The back gauge sensor tests the position and length of the workpiece, providing feedback signals to the control system. This allows for more accurate positioning during the bending process.
(4) The back gauge controller is an electrical device responsible for controlling the back gauge. It receives signals from the back gauge sensor and adjusts the position of the back gauge bar accordingly to achieve the correct workpiece positioning.
(5) The back gauge guide rails are installed on the press brake bed, supporting and guiding the movement of the back gauge bar. These rails ensure the bar moves steadily and precisely along the bed for optimal performance.
Tool Clamps
Press brake clamps are used to fix the tooling, and are divided into upper clamps and clamps on the workbench.
During the clamping process, the upper clamps can automatically align the center.
Clamps are also divided into ordinary clamps and fast tool clamps.
Fast clamp is a fast clamping and fixing device for top punch on the press brake.
It locates on the ram of press brake and can be used to quick clamping and removal of top punch.
It contains a fixture base and a front pressure plate device, which can adjust the die to ensure even force, prevent ram damage, and ensure the machining accuracy of the workpiece stably.
Punches and Dies
The tooling of the press brake is divided into the punch (top die) and the die.
Punch and die is applied for stamping formation and separation of sheet metal, which makes the piecework into specific shapes and sizes.
The die used for bending depends on bending method, bending angle, raw material, and material thickness.
During bending, the ram drives the top punch to press into the bottom die, which is a bending stroke.
Punches feature right angle dies, acute angle dies, gooseneck dies, etc., and the bottom die has U-shaped dies, V-shaped dies, etc.
Hydraulic System
Hydraulic system is used to control the hydraulic cylinder’s pressure and flow rate.
It mainly consists of motor, oil pump, oil filling valve, and oil cylinder, which are mounted on the press brake's frame, and there is an oil cylinder on each of the left and right vertical plates.
The hydraulic pump converts mechanical energy into hydraulic pressure energy to drive the hydraulic system.
The hydraulic cylinder converts the liquid pressure into kinetic energy to drive the ram.
Control System
The controller, which serves as the brain of the press brake, receives input commands in the form of text, numbers, symbols, and graphics that make up the machining instructions.
It controls the press brake to execute the machining program. It is able to store diverse programs, and is equipped with interface circuits and servo drive devices.
Controller is applied for setting and controlling the parameters and operations of press brake.
The controller of CNC press brake can control the bending process through programming.
A variety of parameters can be saved in the system. Currently, the most popular controller brands in the market include Delem, ESA, Cyblec, etc.
There are two versions of the controller: button and touch screen. And it provides 2D and 3D graphics programming to simulate the bending process.
Safety Devices
Such as protective covers, emergency stop buttons, etc., which are used to ensure the safety of operators.
And there are safety doors on the both sides of press brake. When the safety doors are closed, the dangerous area on both sides is inaccessible.
When they are opened during operation, all axes will stop moving.
More advanced protection devices include light curtain safety devices and laser protection devices.
Oil Cylinder
Basically, the oil cylinder is composed of cylinder barrel, cylinder head, piston, piston rod, sealing device, cushioning device, and exhaust device. It is fixed on the both sides of press brake, and drives the ram to perform up-and-down reciprocating movement.
Front Support
Front support is used to support metal sheet being bent and can be adjusted up and down.
It is equipped with guide rails and can move automatically. It is more safer and stable compared with manual support, thus achieving better bending results.
Crane Arm
The crane arm is used to hang or support the small control box, which can be turned around in all directions.
It boosts a good load-bearing capacity and a strong and solid structure. It is mostly made of high-quality aluminum alloy with open molding.
Electrical Cabinet
The electrical cabinet is a small low voltage power distribution box, used to enclose electrical wires, measuring instruments, switches, and related equipment in a metal cabinet.
It is compact, and usually installed on the side of the press brake.
Crowning
To ensure the accuracy of piecework and compensation of deformation of ram, the press brake crowning features numerous functions, such as angle crowning, length crowning, gap error crowning, etc.
And it has two crowning ways: hydraulic crowning and mechanical crowning. Mechanical crowning boosts more compensation points, which can make the bending effect to achieve the expected effect, and is durable and stable during use.
Foot Pedal
The foot pedal is one of the four main components (operator, equipment, system, foot pedal) in the operation of the press brake. It integrates emergency stop, cycle, and single-step remote control functions.
The foot pedal allows for the free control of the back gauge left and right movement, as well as the machine's start and stop functions, and integrates control of the machine tool.
What’s more, it can be added with a WIFI module for networking, enabling seamless monitoring and management across the entire area, and offering simplified management capabilities.
Main Motor
The motor is located next to the filter element and is usually used to provide the driving force and power transmission, such as driving a hydraulic pump or actuator.
Servo Motor
The servo motor applies for the control system of press brake and aims to achieve precise position, speed and torque control.
It is usually connected to the transmission mechanism of the top punch or bottom die for precise bending operation.
Filter Element
The filter element is usually used to filter the liquid in the hydraulic system to keep the hydraulic system working properly.
Linear Scale
Linear scale serves for measuring and controlling the location and angle during bending process. It can be installed on the top punch or bottom die of the press brake.
It is used to measure the location of top punch or bottom die accurately, and control the motion of press brake timely.
Linear scale boosts for its high precision and high definition, which can meet your expected requirements, improving the precision and stability in bending process.
Mechanics of Bending with a Press Brake
The intricate design and precise operation of a press brake are most visible when it bends metal sheets. This bending process is a play of various forces and material properties and employs different techniques. Let's explore this in detail:
Bending Forces and Material Properties
Bending involves applying force to a metal sheet to deform it into the desired shape. The amount of force needed depends on the thickness and type of material, the bend angle, and the length of the bend. The material's properties, such as its yield strength and elasticity, significantly impact how it responds to the bending force.
For instance, a material with a high yield strength will require a more substantial force to bend, while a more elastic material will spring back more after bending, requiring over-bending to achieve the desired angle. Knowing these properties is crucial to effectively control the bending process and achieve high-quality results.
Role of the Press Brake in Different Bending Methods
Different bending methods can be applied using a press brake. These include air bending, bottoming, and coining. The type of press brake and the selection of the appropriate punch and die are essential for these methods.
In air bending, the material is only in contact with the punch and die at three points. The press brake exerts force to push the material into the die, but not all the way. This method allows for a wide range of bend angles using the same die.
In bottoming and coining, the material is pushed all the way into the die. Coining requires more force but results in more accurate and consistent bends.
By understanding the bending mechanics, operators can optimize the bending process, improving the efficiency and quality of the produced parts. All these elements, when combined with the robustness of a press brake and its various components, offer a truly flexible and efficient metal bending solution.
With the detailed insights provided in this article, it's clear that the press brake, a cornerstone in the field of metal fabrication, is a marvel of modern engineering. Its complex design, coupled with precise operation, facilitates the creation of countless metal products essential for various industries.
Conclusion
In conclusion, press brakes, especially hydraulic models, play a vital role in industries requiring precise metal bending. A clear understanding of their structure and components allows users to maximize performance while enhancing maintenance and durability. As a trusted manufacturer, Krrass provides a wide selection of premium press brakes and sheet metal machinery, helping industries achieve their fabrication goals with exceptional precision and efficiency.