A sheet metal press brake is an indispensable tool in metal fabrication, used to bend sheet metal into desired shapes. It works by clamping the workpiece between a matching punch and die, forming precise bends.
Originating in the 19th century as a manually operated process, sheet metal press brakes are one of the oldest methods of mechanically deforming metal. The introduction of hydraulic-driven press brakes in the 1930s significantly boosted production efficiency.
Press brakes come in various types, each suited to specific applications, making them essential equipment in any manufacturing facility.
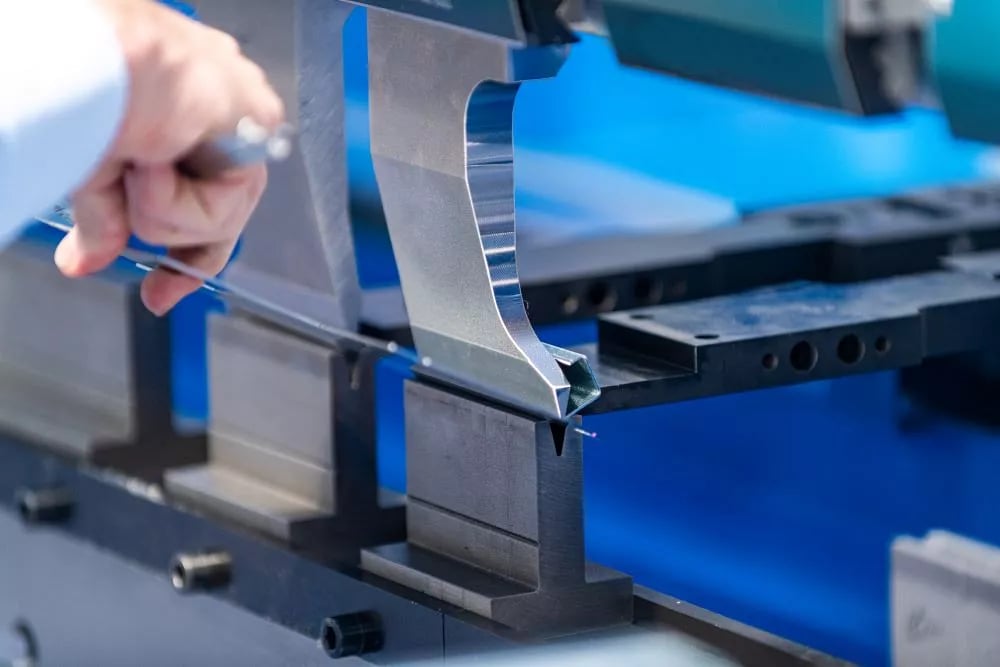
Types of Sheet Metal Press Brakes
Mechanical Press Brakes: Suitable for lightweight sheet materials.
- Advantages: High speed operation and simple design, beneficial for high-speed applications.
- Disadvantages: Applied force is difficult to adjust, limiting versatility. Regular maintenance is required due to component wear.
Hydraulic Sheet Metal Press Brakes: Suitable for medium to heavy-gauge sheet materials.
- Advantages: Hydraulic systems offer controllable and consistent bending force, capable of handling complex tasks. Steadier operation, quieter, and longer lifespan.
- Disadvantages: Slightly slower operation compared to mechanical brakes. Hydraulic oil leakage requires regular maintenance and monitoring.
Electric Press Brakes: Suitable for small-scale sheet materials.
- Advantages: Faster response time, energy-efficient, consistent bending force. Compact moving components reduce maintenance demands.
- Disadvantages: Higher initial investment cost compared to hydraulic systems. May lack strength for extremely high tonnage applications.
CNC (Computer Numerical Control) Press Brakes: Ideal for large-scale and complex-shaped sheet metal fabrication.
- Advantages: High precision and accuracy, easy operation with automated controls, increased production efficiency, strong adaptability to handle intricate bend patterns, labor-saving capabilities, and convenient maintenance with diagnostic systems.
- Disadvantages: Substantial initial investment cost, requires trained operators proficient in programming and operating CNC systems, potential risks associated with system malfunctions or programming errors, and over-reliance on technology may reduce manual skills and expertise.
Components and Functions of Press Brake Machines
A press brake is a complex machine composed of several key components that work in unison to bend and form metal sheets. The main elements include a sturdy frame, bed, ram, die, back gauge, and controller.
The frame serves as the robust backbone, welded together from left and right vertical plates (or side panels), a flat worktable (or bed), and a vertical moving ram, providing structural support for the other parts.
The bed offers a smooth surface on which the metal sheet is placed for bending operations.
The ram is the moving component, consisting of a thick steel plate connected to hydraulic piston rods on the left and right oil cylinders (typically labeled Y1 and Y2). It applies downward force, exerting pressure on the metal sheet to create the desired bend.
The die is a stationary part on the press brake that provides the bending surface over which the metal sheet is formed.
The back gauge is an essential device that accurately positions the metal sheet for precise bending. In CNC (Computer Numerical Control) press brakes, the back gauge utilizes a motor-driven system or chain-driven gauging mechanism to synchronously move two ball or lead screws, allowing the measuring rod to extend or retract to the required exact position.
The back gauge's positioning is crucial as it determines the length of each flange (the portion of the metal sheet bent upward), and its movement is controlled by the CNC controller.
The controller acts as the central command unit, responsible for operating and regulating various aspects of the press brake's performance.
During operation, the metal sheet is placed on the bed of the press brake. The back gauge positions the sheet accurately for bending. Then, the ram descends, applying force to the metal sheet, causing it to conform to the shape of the die.
The controller manages the force exerted by the ram and oversees other parameters throughout the bending process. Some systems incorporate mechanical synchronization mechanisms like torque arms, swing arms, or spherical bearings to enhance precision and performance.
How Press Brakes Work
Operating Principle
The press brake typically features two C-shaped frames (also known as side frames) that connect the bottom workbench and the top moving beam.
The bottom tooling or dies are mounted on the workbench, while the top tooling or punch is installed on the upper beam.
The depth of the punch's movement can be precisely controlled, allowing for accurate bending angles.
Press brakes can be operated manually or equipped with a CNC (Computer Numerical Control) system to execute complex bending operations.
Metal Forming Tips for Sheet Metal Press Brakes
The difficulty of press brake forming is influenced by the grade of material being formed. Harder materials tend to exhibit greater springback, where the metal attempts to return to its original shape after bending.
Softer materials generally experience less springback, as they more readily conform to the angle pressed into the die.
Sharp bending operations can lead to cracking or spreading of the material, which is an important consideration.
Bottoming out, or bottom bending, where the material is bent to the full depth of the die, can increase the risk of cracking.
The coining process, which involves multiple bending steps, can provide precise bending results.
Press brake forming techniques aim to compensate for springback not by relying on bottom bending but through the proper selection and use of tooling.
Operating a Sheet Metal Press Brake
Pre-Operation Checks: Before starting the machine, perform a thorough inspection of the press brake to ensure it is in good working condition. Verify that all components are functioning properly and that there are no signs of damage or abnormal conditions. Ensure that all operators are wearing appropriate personal protective equipment, such as safety goggles, gloves, and steel-toed shoes.
Tooling Selection: Choose the appropriate top punch and bottom die tools based on the specific bending requirements and install them according to the manufacturer's instructions.
Parameter Setup: Set the machine parameters, such as pressure and speed, according to the metal sheet's material properties, thickness, and the desired bending angle.
Workpiece Positioning: Place the metal sheet on the work table and use the back gauge or other positioning tools to ensure accurate and even bending. Proper positioning of the workpiece is crucial for achieving the desired bend quality.
Machine Operation: Initiate the bending cycle by pressing the start button, which will cause the upper punch to descend and apply force to the metal sheet, creating the bend.
Monitoring: Continuously monitor the bending process to ensure that the metal sheet is being bent evenly and correctly. Keep hands and other body parts clear of the working area during operation.
Completion and Inspection: Once the bending process is complete, stop the machine and remove the bent metal sheet. Inspect the bending angle and overall precision to ensure it meets the required specifications.
Machine Shutdown and Cleanup: After finishing the operation, shut down the sheet metal press brake and disconnect power sources. Clean the work area and ensure that all tools and materials are properly stored or returned to their designated locations.
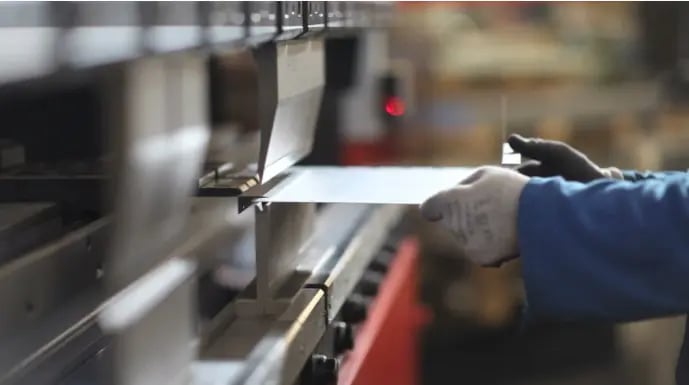
Safety Tips
- Before operating the sheet metal press brake, ensure that the workers have been trained, and familiar with the operation procedures.
- When operating the machine, please wear personal protective equipment, like gloves and goggles.
- When operating the machine, please do not put your hands or other body parts between the upper die and bottom die, and in the workbench.
- Ensure the working area is clean, tidy, and has no obstacles.
- Avoid wearing loose clothes and accessories, to avoid being clamped by the machine.
- Check and maintain the equipment regularly, and ensure the machine is always in good condition.
- Do not adjust and maintain when the machine is working.
Press Brake Bending Techniques
Air Bending
The workpiece only contacts the tip of the punch and the edge of the die. The punch will slightly exceed the top of the chosen die.
As for the V-shaped die, it passes through the top of the V-shaped die, but will not up to the bottom.
The opening shape of the v-shaped die determines the bending radium.
Advantages: owing to the metal sheet being incompletely in contact with the die, the required die force could be little. Besides, using the same die can achieve multiple bending angles, which feature high flexibility.
Disadvantages: owing to the bending results being related to the material’s elasticity, specializing adjustment may be required to achieve the needed accurate bending angle.
Bottom Bending
The die angle should be matched with the anticipated workpiece angle. Unlike the air bending, the workpiece rests against the upper bottom of the die through the punch.
Advantages: owing to the bending angle exactly matching with the die, the accurate bending angle can be achieved.
Disadvantages: bottom bending needs larger die pressure. Because sheet material is in complete contact with the die, probably resulting in sheet material surface damage.
Coining
Coining involves stamping the metal sheet between the die and punch. Through proper pressure, the tip of the punch will penetrate the workpiece.
Advantages: coning can obtain a very precise bending angle. The metal sheet can keep its shape after it is bent.
Disadvantages: due to the large die force required, this method may lead to the overwear of the sheet and die.
FAQs
What is the primary function of a press brake?
The primary function of a sheet metal press brake is to bend and form metal sheets into various shapes by applying controlled pressure. During operation, the punch (upper tool) is forced downward by the ram, causing the metal sheet to deform and take the shape of the die (lower tool). This process allows press brakes to achieve precise bending angles, radii, and shapes in metal fabrication applications.
How do CNC press brakes differ from traditional press brakes
The key difference between a CNC (Computer Numerical Control) press brake and a traditional press brake lies in the level of automation and control. CNC press brakes are computer-controlled machine tools that operate based on pre-programmed instructions, while traditional press brakes require manual operation by an operator.
CNC sheet metal press brakes offer several advantages, including higher precision and accuracy, increased production efficiency, the ability to handle complex bending tasks automatically, and the capability to store and reuse programs for repeatable operations. Additionally, CNC sheet metal press brakes can be remotely monitored and controlled over an internet connection, enhancing flexibility and productivity.
How do you maintain a press brake for optimal performance?
Proper maintenance is crucial for ensuring optimal performance and longevity of a sheet metal press brake. Here are some key steps:
Visual Inspection: Conduct a thorough visual inspection of all areas to identify any potential issues or signs of wear.
Hydraulic System Check: Examine the hydraulic circuit, including the oil level, temperature, cleanliness, and viscosity.
Mechanical System Check: Inspect mechanical components for any loose bolts, worn bearings, bushings, pins, keyways, gears, splines, shafts, couplings, belts, pulleys, chains, or sprockets.
Electrical System Check: Check the electrical system for loose connections, damaged wires or cables, switches, relays, fuses, circuit breakers, transformers, or contactors.
Tooling Check: Examine the punch and die tools for signs of wear or damage, and replace them if necessary.
Proper maintenance is crucial for ensuring optimal performance and longevity of a press brake. Here are some key steps:
Visual Inspection: Conduct a thorough visual inspection of all areas to identify any potential issues or signs of wear.
Hydraulic System Check: Examine the hydraulic circuit, including the oil level, temperature, cleanliness, and viscosity.
Mechanical System Check: Inspect mechanical components for any loose bolts, worn bearings, bushings, pins, keyways, gears, splines, shafts, couplings, belts, pulleys, chains, or sprockets.
Electrical System Check: Check the electrical system for loose connections, damaged wires or cables, switches, relays, fuses, circuit breakers, transformers, or contactors.
Tooling Check: Examine the punch and die tools for signs of wear or damage, and replace them if necessary.