As the manufacturing landscape undergoes continual evolution, hydraulic press brake machines emerge as indispensable tools within the realm of metal fabrication. Renowned for their ability to bend metal sheets with precision, press brakes play a pivotal role in crafting components and parts across diverse industries. Yet, maximizing their performance hinges upon meticulous setup and installation procedures.
Building upon the foundational information available on our website, this article delves into an in-depth guide for setting up and installing press brakes. By exploring key considerations and providing detailed instructions, we aim to equip readers with comprehensive insights into this critical process, empowering them to harness the full potential of their hydraulic press brake machine.
Table of Contents
Proper Setup and Installation Steps for Hydraulic Press Brake Machines
Equipment Location Selection:
Selecting the appropriate installation site for a press brake requires careful consideration of several factors. Firstly, ensure placement on a sturdy and level surface to mitigate potential vibrations stemming from an unstable foundation. Additionally, assess factors such as operator workspace, safety zones around the machine, and potential environmental impacts.
Foundation Construction:
The stability of a press brake hinges upon the quality of its foundation. A meticulously designed and constructed foundation is essential to ensure the machine's stability during operation. Considerations should encompass foundation dimensions, choice of materials, and reinforcement methods to withstand both the machine's weight and the forces generated during operation.
Electrical and Hydraulic Connections:
Press brakes typically incorporate intricate electrical and hydraulic systems. Correctly establishing connections for these systems is paramount. Adhere to prescribed procedures to ensure precise cable and pipeline connections. Upon completion of connections, conduct thorough system functionality tests and pressure tests to verify smooth operation of all components.
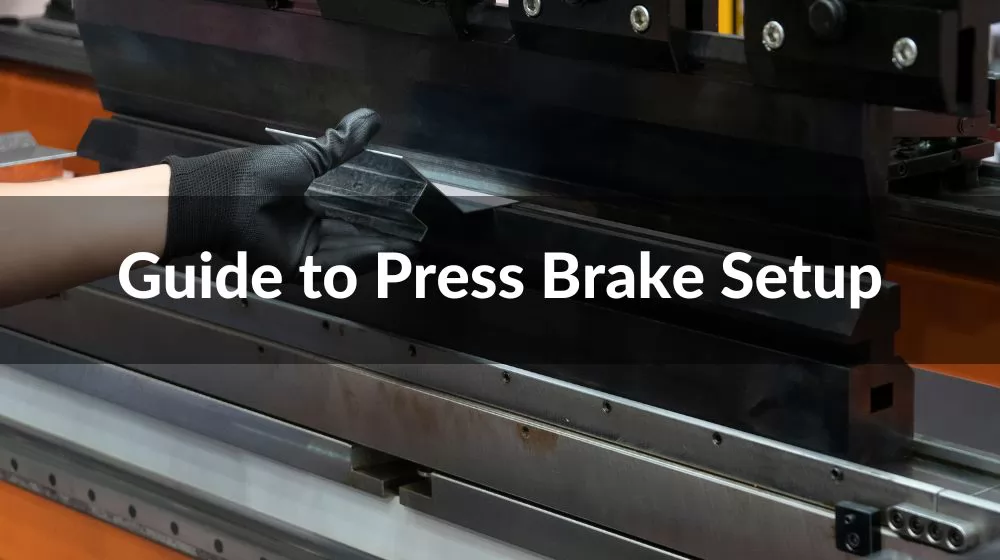
Installation Considerations
Safety Training for Operators:
Comprehensive safety training is imperative for equipment operators. This training encompasses familiarization with standard operating procedures, emergency shutdown protocols, the use of personal protective equipment, and more. By equipping operators with this knowledge, they can maintain heightened awareness during operations, minimizing the risk of accidents.
Equipment Inspection and Debugging:
Following installation, conducting a meticulous inspection and debugging process is essential to ensure optimal performance. Thoroughly examine all mechanical components, sensors, hydraulic valves, and other parts to verify their security and integrity. Conduct sample processing to validate the precision and stability of the press brake.
Development of Maintenance Plans
Establishing detailed maintenance plans is critical for sustaining the long-term operation of the press brake. These plans should encompass tasks such as lubrication, cleaning, and fastener inspections. By adhering to a structured maintenance regimen, equipment lifespan can be prolonged, and maintenance costs minimized.
Accelerating Setup for Enhanced Production Efficiency
Efficient setup is paramount in maximizing production efficiency within press brake operations. Employing consistent setups when producing large component volumes can significantly reduce the cost per component. Operators can achieve this by mastering rapid setup techniques, enabling them to produce more components at a reduced cost. This involves acquiring proficiency in various setup methods and adeptly applying them during practical operations to optimize overall production efficiency.
Blueprint Analysis and Fixture Selection
Before initiating the bending process, operators must thoroughly comprehend the characteristics of the required components. This encompasses material type, flange dimensions, angle specifications, radii, and other pertinent details. Accurate blueprints furnish operators with precise processing requirements, mitigating the risk of inaccuracies resulting from inadequate information. Utilizing these blueprints as a guide, operators can select appropriate fixtures such as air bending, bottom bending, coining, etc., to accommodate diverse processing needs effectively.
Conclusion
The proper setup and installation of hydraulic press brake machines form the cornerstone of ensuring machining quality and operational efficiency. By adhering to the correct installation steps, paying attention to crucial safety considerations, and formulating maintenance plans, we can ensure that hydraulic press brake machines consistently perform at their best throughout the production process. Furthermore, staying attuned to the continuous development of new technologies will contribute to further enhancing the performance and application scope of press brakes.If you are looking for a reliable press brake supplier, please feel free to contact Krrass Inc, We are a leader with many years of experience.