What Is Hydraulic Press Brake
A hydraulic press brake machine is a tool used in metal fabrication to bend sheet metal and plate materials. It utilizes hydraulic force to apply pressure to a punch, which in turn bends the workpiece against a die to achieve the desired shape. Hydraulic press brakes are widely used in various industries for bending applications ranging from simple bends to complex shapes.
What Is the Function
The function of a hydraulic press brake machine is to bend sheet metal and plate materials to a specific angle or shape. It achieves this by applying controlled hydraulic force to a punch, which in turn bends the workpiece against a stationary die. Here are the primary functions of a hydraulic press brake:
Bending: The main function of a hydraulic press brake is to bend sheet metal or plate materials to the desired angle. It can perform a variety of bending operations, including V-bending, U-bending, and air bending, among others.
Forming: Hydraulic press brake machines are capable of forming complex shapes and contours in sheet metal and plate materials. By using different tooling configurations, they can create bends, curves, and flanges to meet specific design requirements.
Precision: One of the key functions of a machine is to provide precise control over the bending process. With hydraulic cylinders and sophisticated control systems, operators can accurately position the ram and control the bending force to achieve consistent results.
Versatility: Hydraulic press brakes are versatile machines that can handle a wide range of materials, thicknesses, and bending applications. They can bend various metals, including steel, aluminum, stainless steel, and copper, as well as non-metallic materials like plastic and composites.
Automation: Many hydraulic press brake machines are equipped with automation features to streamline the bending process and improve productivity. This includes CNC (Computer Numerical Control) systems for programming bending sequences, automatic tool changes, and integrated backgauges for precise positioning of the workpiece.
Safety: Hydraulic press brakes incorporate safety features to protect operators and prevent accidents during operation. This may include safety guards, light curtains, two-hand controls, and emergency stop buttons to ensure safe operation in the work environment.
How Many Types of Hydraulic Press Brake Machine
There are several different types of hydraulic bending machine available, each designed to meet specific bending requirements and production needs in metal fabrication. Here are some common types:
Conventional Hydraulic Press Brake:
This is the most basic type of hydraulic press brake, featuring a simple ram and bed design. It operates using hydraulic cylinders to apply force to the upper ram, which then bends the metal sheet against the lower bed. Conventional hydraulic press brakes are versatile and suitable for a wide range of bending applications.
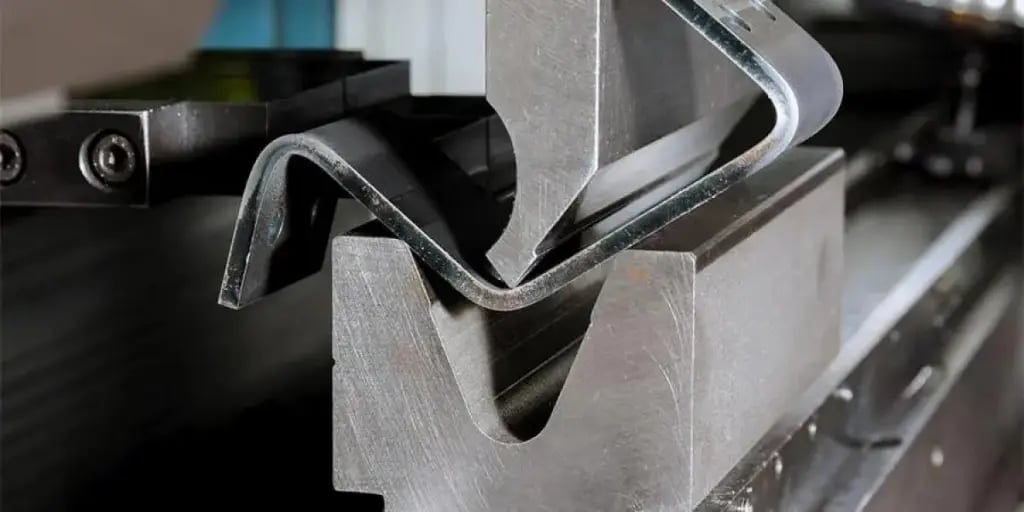
Synchronized Hydraulic Press Brake:
In synchronized hydraulic press brake machine, both sides of the ram are synchronized to ensure parallelism during bending. This ensures uniform bending across the entire length of the metal sheet, especially important for precision bending of longer workpieces. Synchronized press brakes are commonly used for applications requiring high accuracy and repeatability.
CNC Hydraulic Press Brake:
CNC (Computer Numerical Control) hydraulic press brakes feature advanced control systems that allow for precise and automated bending operations. These machines are equipped with servo-driven hydraulic systems and programmable backgauges, enabling operators to program and control various bending parameters such as bend angle, depth, and speed. CNC hydraulic press brakes offer high productivity, accuracy, and flexibility for complex bending tasks.
Tandem Hydraulic Press Brake:
Tandem press brakes consist of two or more press brake machines working in tandem to bend longer or heavier workpieces. These machines are synchronized to operate simultaneously, allowing for the bending of large and heavy parts that exceed the capacity of a single press brake. Tandem press brakes are commonly used in industries such as shipbuilding, construction, and automotive manufacturing.
Hybrid Hydraulic Press Brake:
Hybrid press brakes combine hydraulic and electric servo drive systems to optimize energy efficiency, speed, and precision. These machines use hydraulic power for high-force bending operations and electric servo drives for precise control of ram positioning and speed. Hybrid press brakes offer the benefits of both hydraulic and servo technologies, including reduced energy consumption, faster cycle times, and enhanced accuracy.
Variable Rake Hydraulic Press Brake:
Variable rake press brakes feature an adjustable angle for the upper ram, allowing for precise control over the bending process. By adjusting the rake angle, operators can optimize bending performance for different materials, thicknesses, and bending geometries. Variable rake press brakes are suitable for applications requiring versatile bending capabilities and optimal bend quality.
Conclusion
These are some of the most common types of hydraulic press brakes available in the market, each offering unique features and advantages to meet the diverse needs of metal fabrication operations. When selecting a hydraulic press brake, it's important to consider factors such as bending capacity, accuracy, automation capabilities, and overall cost-effectiveness to choose the best option for your specific applications.