For many hydraulic press brake machine operators, encountering issues with hydraulic press brake machines is common. Troubleshooting these problems can be time-consuming, especially for novices. Today, we'll provide some detailed solutions to common hydraulic press brake issues, hoping to assist you in resolving them efficiently.
Hydraulic press brake machines are integral to various manufacturing processes. However, like any machinery, they can encounter issues. This guide provides troubleshooting steps to address common problems encountered during operation.
Troubleshootings for Hydraulic Press Brake Machine
Issue 1: Lack of pressure in the hydraulic system or unresponsive pressure button
- Check if the solenoid coil of the proportional relief valve is energized and if the voltage meets requirements. If electrical issues are suspected, investigate related electrical components.
- Inspect if the cartridge valve or main spool is stuck and if the damping hole is blocked. If so, disassemble the overflow valve, clean it thoroughly, and reinstall it.
- Verify if phase adjustment in the three-phase power supply has caused motor reversal.
- Examine if the oil pump is rotating incorrectly or if it's damaged.
- Assess the condition of the pressure gauge; replace if damaged.
- Check if the pressure control valve is receiving electrical signals or if it's blocked.
- Investigate if the pressure cartridge valve is blocked or stuck, preventing oil sealing.
- Determine if the filling valve is stuck, causing slow ram movement.
- Adjust the compensation amplifier if it's set too small.
- Test the valve and oil pump by directly supplying 24V electricity to assess pressure limitations.
By addressing these potential causes systematically, you can diagnose and resolve hydraulic press brake issues effectively, minimizing downtime and ensuring smooth operations.
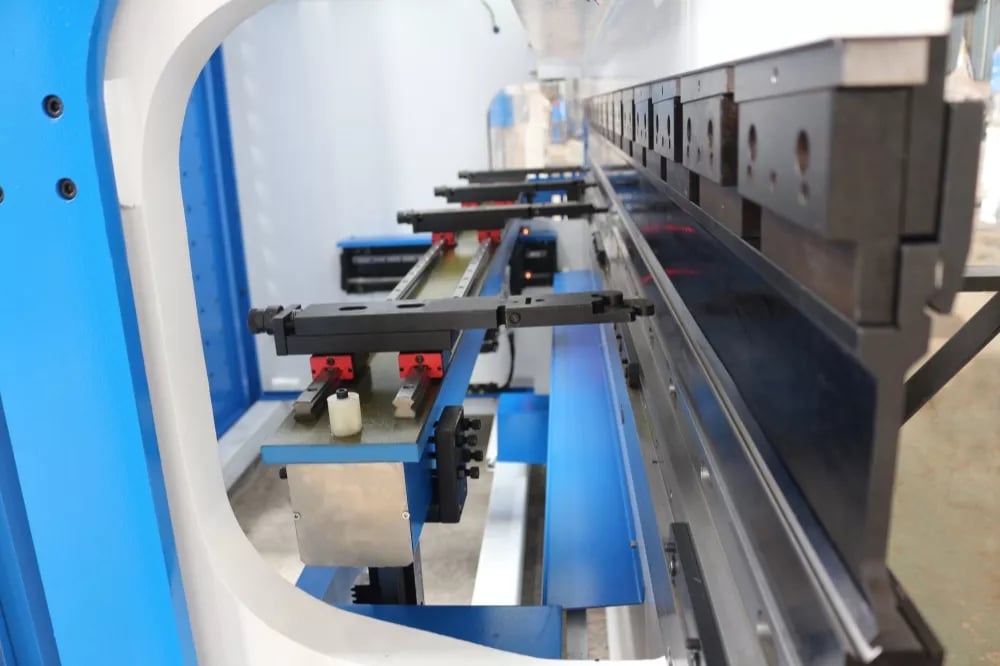
Issue 2: Extended delay at ram speed change point
- Air ingress into the upper cavity of the oil cylinder, resulting in prolonged pressure buildup (due to leaks in the self-priming pipeline).
- Insufficient flow rate through the filling valve or self-priming pipeline, or excessive sliding speed causing suction.
- Incomplete closure of the filling valve, causing a slowdown in upper cavity pressure.
- Failure to draw oil into the upper cavity after energizing the slow down valve due to the closure of the filling valve.
- Improper positioning of the proportional valve leading to varied openings and desynchronization.
- Reduction of fast down speed and assessment for any halts in testing.
- Adjustment of fast down pressure to influence the closure of the filling valve and elimination of fast down pressure.
- Modification of pressure parameters in the pre-work advance delay stage.
- Insufficiently sized damping hole in the filling valve control line causing pressure differences.
- Examination of CNC system parameters (delay before slowdown).
- Evaluation of CNC system parameters (decreasing gain parameter at slower speed).
- Verification of fuel tank oil level; ensure the filling port is adequately submerged. If not, add oil to maintain a level at least 5mm above the filling port to ensure complete submersion.
- Confirmation of full opening of the filling valve. If oil contamination causes the valve core to be inflexible and jammed, leading to insufficient filling, clean and reinstall the filling valve to restore flexibility.
- Assessment of fast forward speed; if too fast, it may result in insufficient filling. Adjust system parameters to reduce fast forward speed accordingly.
Issue 3: In manual mode, the hydraulic press brake ram fails to descend and lacks sufficient bending force.
- Verify the functionality of the "three-position four-way" reversing valve in the control filling control oil circuit. If operational, check if the filling valve is closed properly. If not, the upper cavity remains connected to the filling port of the fuel tank, preventing pressure buildup. Possible reasons for valve malfunction include lack of power or being stuck.
- Inspect the filling valve for any obstructions or sticking. Clean and reinstall the valve to ensure flexibility of the valve core.
Issue 4: Slow return speed of the hydraulic bending machine ram with high return pressure.
This issue typically arises when the filling valve fails to open, opposite to the scenario described in Issue 3. Refer to the solution for Issue 3 to address this problem.
Issue 5: Ram not perpendicular during operation, accompanied by abnormal noises.
This failure is often attributed to prolonged use of the guide rail, inadequate lubrication, and increased clearance due to wear. Perform a thorough examination of the guide rail pressure plate for wear and readjust to meet required clearance standards. Based on the severity of wear, consider replacing the rail pressure plate if necessary.
- Evaluate the condition of the original pressure plate, ensuring the hardness of any affixed plastic and the bonding surface of the guide rail. After scraping, ensure the bonding surface is at least 85% intact and create a zigzag lubricating oil groove.
- For the original pressure plate containing a metal plug iron, opt for tin bronze plate or ductile iron. Process the bonding surface with a grinder, ensuring the connecting bolt is lower than the bonding surface, and create a zigzag lubricating oil groove.
Issue 6: The bending machine ram can only descend and encounters difficulty in ascending.
● No pressure on the return stroke, preventing the ram from ascending:
- Circuit malfunctions.
- Sticking of the pressure regulating valve.
● Pressure exists on the return stroke, hindering the ram's ascent:
- If pressure is insufficient, increase it.
- Sticking of the reversing valve.
● High return pressure causing slow ram ascent:
- Sticking of the hydraulic control valve.
- Low hydraulic control oil pressure.
- Sticking or failure to switch direction of the control oil reversing valve.
- Reversed solenoid valve spool.
● Ram can ascend and descend without pressure or with a delay in pressure:
- Electrical circuit issues, preventing the solenoid valve from receiving power.
- Damage to the large hydraulic control valve spring or spool.
- Loose screw on the lifting cylinder.
● Machine tool descent:
- Circuit issues.
- Damaged oil cylinder sealing ring, causing oil leakage.
- Leakage or damage in the locking device oil circuit (small hydraulic control, throttle valve, etc.).
● Slow or jittery machine tool descent:
- Roughened or damaged oil cylinder, or stuck nut screw inside the oil cylinder.
- Worn or misaligned track.
Issue 7: Impact sound during rapid ram movement.
- Loose rail plate causing impact sound.
- Incorrect position of the grating ruler or travel switch.
- Delay parameter before fast down set too low.
Issue 8: Ram unable to descend quickly.
- Check for electrical signal or blockage in the quick lower valve.
- Verify electrical signal and movement or potential blockage in the electromagnetic proportional directional valve (check feedback voltage).
- Mechanical components connected too tightly, such as overly tight guide rail plate or cylinder.
- Closed filling valve preventing oil suction.
- Grating ruler issues.
- Inspect foot switch condition and wiring.
- Closure of the filling valve after energizing the slow down valve, preventing oil suction in the upper cavity.
Conclusion
Regular maintenance and prompt troubleshooting are essential for ensuring smooth operation of hydraulic press brake machines. By following these troubleshooting steps, operators can efficiently address common issues and minimize downtime in manufacturing processes.