Hydraulic system maintenance, especially for large bending machines, the complexity of the hydraulic system is far beyond people's imagination. Therefore, the maintenance of such equipment is a problem that troubles maintenance personnel. The author uses a certain type of hydraulic press brake as an example. For example, based on the analysis of common causes of machine failures, some maintenance techniques are illustrated with examples.
Hydraulic Press Brake hydraulic system structure?
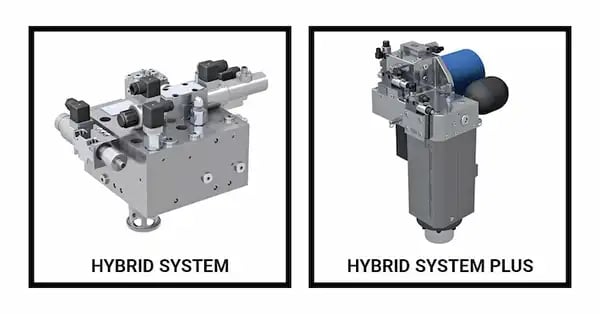
A hydraulic press brake is a machine tool used for bending sheet metal and plate material. Its hydraulic system plays a crucial role in enabling the bending process. The hydraulic system of a press brake typically consists of several key components:
1.Hydraulic Pump: The hydraulic pump is responsible for generating hydraulic pressure by converting mechanical energy (usually from an electric motor) into hydraulic energy. It delivers pressurized hydraulic fluid to the system.
2.Hydraulic Fluid: Hydraulic fluid, often oil, is used to transmit pressure within the hydraulic system. It needs to have good lubricating properties and resistance to thermal degradation.
3.Hydraulic Reservoir: The reservoir stores the hydraulic fluid and allows for the dissipation of heat generated during operation. It also helps in filtering out contaminants from the fluid.
4.Hydraulic Valves: Various types of hydraulic valves control the flow and direction of hydraulic fluid within the system. These valves include directional control valves, pressure control valves, flow control valves, and proportional valves.
5.Hydraulic Cylinders: Hydraulic cylinders are the actuators responsible for applying force to the press brake's ram or beam, which in turn bends the metal. These cylinders operate based on the principle of hydraulic pressure acting on a piston within a cylinder.
6.Hydraulic Lines and Hoses: These are the conduits through which hydraulic fluid flows between the various components of the hydraulic system, such as the pump, valves, cylinders, and reservoir.
7.Pressure Relief Valve: The pressure relief valve is a safety feature that prevents the hydraulic system from exceeding its maximum pressure limit, thereby protecting the components from damage.
8.Control System: The control system of the hydraulic press brake includes electronic components such as sensors, switches, and a programmable logic controller (PLC) that regulate the operation of the hydraulic system based on user inputs and programmed parameters.
These components work together to generate and control hydraulic pressure, allowing the press brake to accurately bend metal according to the desired specifications. Proper maintenance and monitoring of the hydraulic system are essential for ensuring the efficient and safe operation of the press brake.
How does the hydraulic system of a hydraulic press brake work?
The hydraulic system works based on the principles of fluid mechanics and Pascal's law. Here's a simplified explanation of how it operates:
1.Hydraulic Pump: The process begins with a hydraulic pump, typically driven by an electric motor or an internal combustion engine. The pump draws in hydraulic fluid (usually oil) from a reservoir and pressurizes it.
2.Pressurized Hydraulic Fluid: The pressurized hydraulic fluid is then forced through hydraulic lines or hoses to various hydraulic components within the system.
3.Hydraulic Cylinder: When hydraulic fluid is directed to a hydraulic cylinder, it enters one side of the cylinder, applying pressure to a piston or plunger inside. The pressure exerted on this piston creates a force that can move the piston and any attached load. Hydraulic cylinders are commonly used as actuators in machinery to generate linear motion.
4.Control Valves: Control valves within the hydraulic system regulate the flow of hydraulic fluid and control the direction of movement of hydraulic actuators, such as cylinders. These valves can be manually operated or automated, depending on the application.
5.Return Line: After performing its work, the hydraulic fluid returns to the reservoir through a return line. This allows the hydraulic fluid to be recirculated within the system.
6.Pressure Relief Valve: A pressure relief valve is typically installed in the hydraulic system to prevent excessive pressure buildup. If the pressure exceeds a predetermined limit, the relief valve opens, allowing excess fluid to bypass and return to the reservoir, thus protecting the system from damage.
7.Filter and Reservoir: The hydraulic system often includes a filter to remove contaminants from the hydraulic fluid, ensuring smooth operation and prolonging the lifespan of components. The reservoir stores the hydraulic fluid and helps dissipate heat generated during operation.
8.Overall, the hydraulic system converts mechanical energy into hydraulic energy through the pump, which is then used to generate forces and motions through hydraulic actuators like cylinders. This system is widely used in various applications, including heavy machinery, automotive systems, industrial equipment, and more, due to its ability to provide high power density, precise control, and versatility.
9. Analysis of Causes of Failure of Hydraulic Control System
The most common fault of the hydraulic control system is that the slider pressing force is insufficient and the return speed is slow when the hydraulic cylinder is under pressure. This failure not only causes the hydraulic system's handling performance to be greatly reduced, but also makes the stability of the whole system worse. Other faults in the series. The main reasons for inducing such faults are as follows: The first, hydraulic cylinder piston and the end cap are not well sealed, resulting in serious leakage inside and outside the cylinder. The reason why the hydraulic system can realize the function is that the hydraulic cylinder pressurizes the liquid to make the piston or the end cap seal malfunction. The liquid inside the hydraulic cylinder will leak, and the internal pressure becomes lower. The beach is doing normal external work, resulting in a significant reduction in the efficiency of the hydraulic system or even complete paralysis. The second, the relief valve regulates insufficient pressure. The main function of the relief valve is to control the hydraulic system's functional force by adjusting the relief valve to control the outward output of the pressurized liquid when the liquid in the hydraulic cylinder is pressurized to the working pressure. If there is a problem with the pressure regulation, the adjustment is generally low, so that the other parts do not get the energy required for the normal working step, and then the problem that the sliding force of the slider is insufficient and the return speed is slow. However, if the adjustment is too high, the wear of the slider will increase and the damage to the hydraulic system will be more serious. The third, the surface of the male valve spool is severely worn, resulting in a tight closure at the valve port. The cone valve is a key part of maintaining hydraulic stability in the system and is a “sturdy line of defense” that blocks internal and external pressure exchange. If the cone valve spool fails, it will cause leakage of internal high pressure liquid and a slider failure. The surface of the valve body of the fourth reversing valve is worn, which makes the movement of the valve core difficult in the valve body. The one-way closing of the valve is not strict or the gap between the valve surface and the valve body is too large. As a result, the leakage of internal pressure will also cause the slider to malfunction.
10. Hydraulic Operation Fault Diagnosis Method and Conclusion
Immediately after the failure of the hydraulic operating system, stop the fault finding, determination and maintenance work. For the detection of faults, there are mainly the following methods, the first method. The observation method is mainly for the pressure gauge and the hydraulic cylinder on the hydraulic control system to check whether the indication pressure of the hydraulic gauge is normal, thereby determining the cause of the failure and the orientation of the failure. The observation of the hydraulic cylinder is mainly to determine whether the hydraulic cylinder leaks. Because the leakage of the liquid leaves a very visible trace or is accompanied by sound. If the hydraulic gauge is low or there is a trace of obvious leakage, it can be determined that the hydraulic cylinder is faulty, and repair work can be taken immediately. The second fruit was observed and found no obvious faults or faults could not be directly observed with the eyes, such as the poppet valve core wear, such as the bead must use the instrument for detection such as optical imager, particle beam flaw detector. This type of instrument can detect faults such as misalignment or wear inside the hydraulic system by emitting high-energy particles.
11. Disposal Method for Hydraulic Cylinder Leakage
Since the hydraulic cylinder is the core of the entire hydraulic control system, maintenance measures must be taken once liquid and pressure leaks out there. In general, two methods of welding and replacement are adopted. The welding method is mainly for the slight cracks or small holes in the hydraulic cylinder. In the welding, the combination of internal and external welding should be adopted to ensure the welding is complete. In particular, it must be noted that during the welding process, it is necessary to pay attention to eliminate the residual stress, otherwise the damage to the welding joint will be very large. If not handled properly, not only can the failure be repaired, but the failure will be more serious. The replacement method only needs to replace the defective hydraulic cylinder fittings. However, this method of disposal is simple but costly. This method of disposal is only possible when there is a large failure that is difficult to repair in a short time.
12.Conclusion
The hydraulic system of the hydraulic bending machine is complicated, so the troubleshooting work is also difficult. The face repair personnel must have