Hydroforming and hydraulic presses are two types of equipment commonly used in the manufacturing industry. While both of them utilize hydraulic power, they are used for different purposes and offer unique advantages. In this blog, we will explore the differences between hydroforming presses and hydraulic presses.
Hydroforming Press
Hydroforming is a metal forming process that uses a high-pressure hydraulic fluid to shape metal into complex parts. The process involves placing a metal blank into a specially designed die, then applying high pressure hydraulic fluid to shape the blank into the desired shape.
Hydroforming presses are designed to handle this process and are typically equipped with a high-pressure hydraulic system that can generate up to 10,000 psi of force. These presses are commonly used in the aerospace, automotive, and plumbing industries to create complex shapes from a single piece of metal.
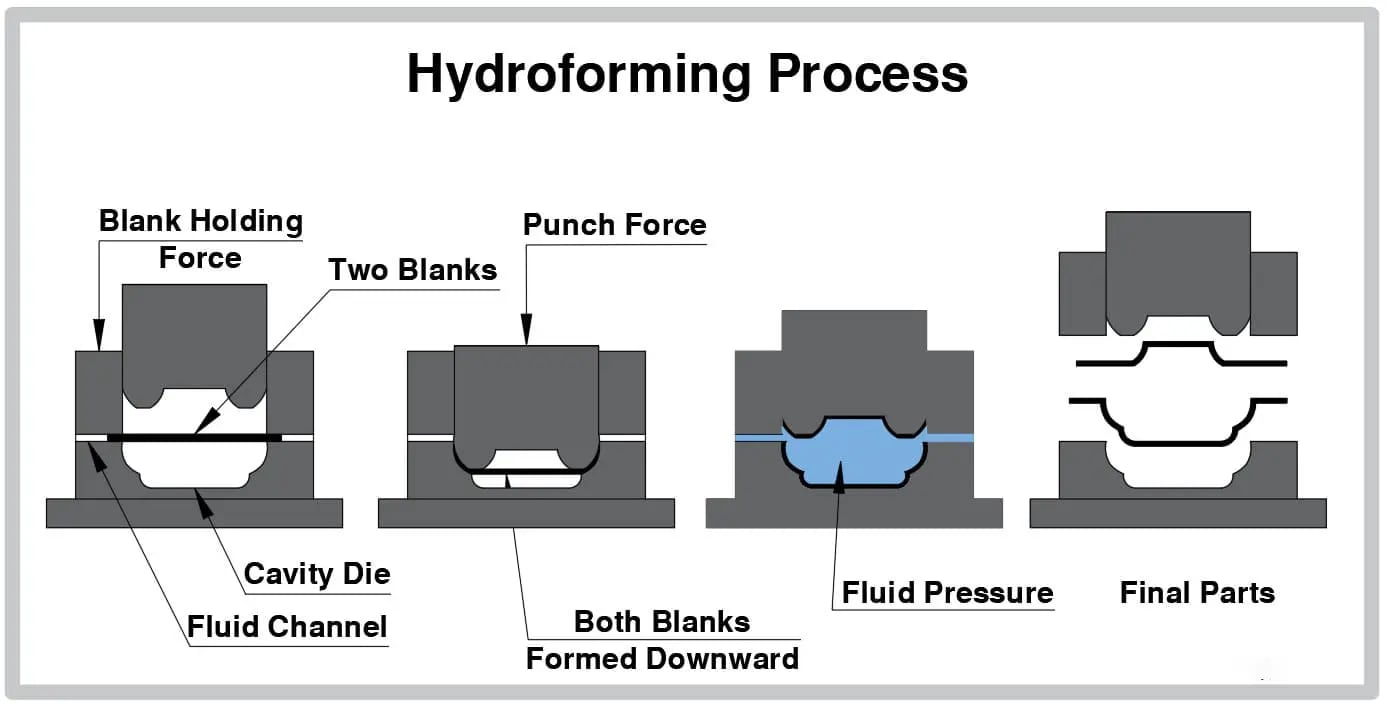
The hydroforming press has the following advantages
Increased design flexibility: Hydroforming press allows for the creation of complex shapes with sharp bends, curves, and varying thicknesses. This process eliminates the need for additional components that may be required in traditional manufacturing methods, which results in more design flexibility.
Improved structural strength: Hydroforming press can create parts with improved structural strength because the process eliminates the need for welding or other joining methods. The lack of seams or joints in hydroformed parts increases the strength and reduces the risk of failure.
Reduced production time: Hydroforming press can significantly reduce production time compared to traditional manufacturing methods. The process can produce parts in a single operation, eliminating the need for multiple production stages.
Lower production costs: Hydroforming press can reduce production costs by eliminating the need for additional components, reducing production time, and minimizing waste material.
Consistent quality: Hydroforming press produces parts with consistent quality, reducing the risk of defects and minimizing scrap rates. This ensures that each part is produced to the same standard, reducing the need for quality control.
Hydraulic Press
A hydraulic press is a machine that uses hydraulic fluid to generate high levels of force. Hydraulic presses come in a variety of sizes and are used for a wide range of applications, such as metalworking, forging, stamping, and molding.
Unlike hydroforming presses, hydraulic presses are used to shape a wide range of materials, including plastics, rubber, and wood. Hydraulic presses can be either manually operated or fully automated, depending on the specific application.
Hydraulic presses are designed to deliver a consistent force throughout the entire stroke of the ram, making them ideal for applications that require uniform pressure distribution. They are also highly customizable, with the ability to adjust the pressure, speed, and stroke of the ram to suit specific requirements.
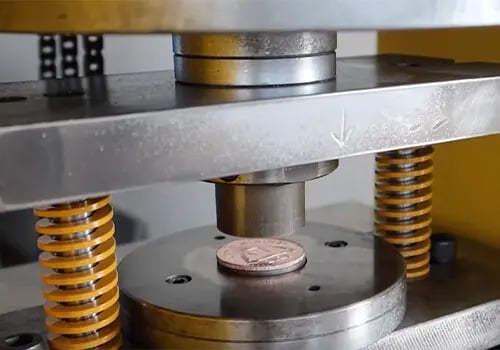
The hydraulic press has the following advantages
High Force Production: One of the biggest advantages of hydraulic presses is their ability to generate high levels of force. This is possible because hydraulic systems can transmit force over long distances without losing power or efficiency.
Versatility: Hydraulic presses are versatile and can be used for a wide range of applications, including metal forming, punching, cutting, stamping, and bending.
Precision: Hydraulic presses can be designed to provide precise control over the application of force, making them ideal for applications that require accuracy and consistency.
Energy Efficiency: Hydraulic presses are highly energy-efficient because they use a hydraulic fluid to transmit force, which reduces energy loss and heat buildup.
Safety: Hydraulic presses are safer to operate than mechanical presses because they have built-in safety features, such as overload protection and emergency stops.
Low Maintenance: Hydraulic presses require minimal maintenance compared to other types of presses, which makes them more cost-effective in the long run.
Reduced Noise: Hydraulic presses are quieter than mechanical presses because they do not have as many moving parts, which reduces noise and vibration.
Conclusion
In conclusion, hydroforming presses and hydraulic presses are both valuable tools in the manufacturing industry. While both of them utilize hydraulic power, they are used for different purposes and offer unique advantages. Hydroforming presses are used to shape complex metal parts with high accuracy, while hydraulic presses are used to shape a wide range of materials with consistent force distribution. Understanding the differences between these two types of presses can help manufacturers choose the right equipment for their specific needs.