As one of the metal processing equipment, the hydraulic shearing machine plays a very important role in the industrial field. This article compares the two most common types of hydraulic shears: swing beam shears and guillotine shears. Their working principles and performance characteristics are introduced respectively, and the two are compared from many aspects, such as their applications, the differences in their blades, and their different ways of use.
How does the swing beam hydraulic shearing machine work?
The working principle of a swing beam hydraulic shearing machine is to ensure the straightness and parallelism of the sheared plate’s surface while minimizing any deformation to achieve a high-quality workpiece. The upper blade is securely fixed on the tool holder, while the lower blade is fixed on the workbench.
To prevent any scratches on the metal sheet during sliding, a holding ball is strategically placed on the workbench. The positioning of the sheet metal is done with the help of a rear gear, and its position can be easily adjusted using a motor. To prevent any movement of the plate during the shearing process, a pressing cylinder is utilized for compression. Safety is also prioritized with the inclusion of guardrails to prevent any industrial accidents. The return journey of the machine relies on the use of nitrogen, ensuring a fast and impact-free process.
Performance of swing beam hydraulic shearing machine
The frame is constructed using an overall welded structure, eliminating any vibration stress and ensuring excellent accuracy.
The integration of an advanced hydraulic system adds to the machine’s reliability.
The use of a three-point support rolling guide rail eliminates any support gaps, resulting in improved shearing quality.
The blade gap handwheel adjustment is quick, accurate, and convenient, making it easier for operators to achieve precise cuts.
The rectangular blade design allows for the utilization of all four cutting edges, significantly extending its service life. Furthermore, the internal structure of the upper tool holder enables efficient punching and enhances part accuracy.
The swing beam shearing machine is equipped with a segmented cutting function, adding versatility to its capabilities.
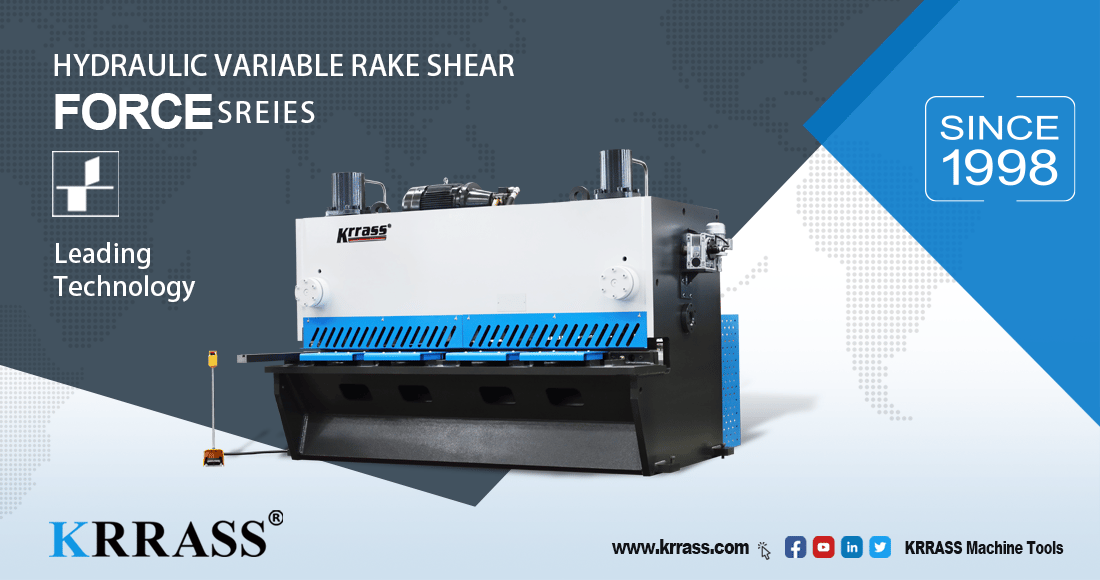
How do guillotine hydraulic shearing machines work?
Guillotine shearing machines work by employing a straightforward vertical cutting motion. The process begins with the operator placing the sheet metal or other material to be cut onto the machine’s cutting bed. The material is then aligned according to the desired cut, and the upper blade, in a rectangular shape, descends vertically to exert force on the material against a fixed lower blade. This shearing action cleanly cuts through the material, producing a precise and straight-edged result.
Performance of guillotine hydraulic shearing machines
Guillotine hydraulic shearing machine is made up of upper and lower cutting blades, a workbench, support system, and a guillotine control system. With a solid and straightforward design, they are not only easy to maintain but also built to last.
Due to the user-friendly control system, operating this kind of hydraulic machine is a breeze. With just a few simple steps, the operator can easily control the shearing process by setting the guillotine opening to match the specific production requirements.
By minimizing the inertia of the lower cutting edge, this kind of hydraulic machine ensure a stable cutting effect that leaves no room for cracks. The result is a smooth and flawless cut that meets the highest standards of quality.
With the ability to adjust the knife edge distance and change the guillotine opening, these machines offer unmatched cutting accuracy. This level of precision allows them to cater to a variety of production needs and deliver exceptional results for different products.
Key differences between swing beam and guillotine hydraulic shearing machines
Applications
Guillotine hydraulic shearing machine is used in automobiles, tractors, rolling stock, ships, motors, instruments and other industries, and are also suitable for stretching various high-strength alloy plates.
Swing shears are used in processes such as stretching, bending, extrusion, and forming of metal sheets in the power industry, aviation and other industries.
Different shear angles
The angle of the blade holder of the swing beam hydraulic shearing machine is fixed, and the shearing speed cannot be adjusted. The Guillotine hydraulic shearing machine can quickly adjust the angle by adjusting the upper and lower strings of engineering oil cylinders to close the cavity oil volume. The shear angle increases, the shear thickness increases, the shear angle decreases, the shear speed is accelerated, the efficiency is higher, and the bending of the plate is effectively reduced.
For instance, if you opt for the QC11Y-20×3200 Guillotine shearing machine, you can adjust the cutting angle within a range of 0.5-3.5° based on the thickness of the metal you are working with. On the other hand, swing beam shearing machines lack this adjustability and are fixed at a shearing angle of 3°.
Different ways of exercise
The blade holder of the guillotine shearing machine moves up and down, while the swing beam shearing machine moves in an arc shape. This distinction in movement greatly affects the overall cutting process and the quality of the sheared material.
The swing beam shearing machine moves in an arc shape. The swing beam shearing machine, with its arc-shaped tool holder body, ensures that the points of the arc are in contact with the material being sheared. This contact helps to maintain the straightness of the sheared material, resulting in precise and accurate cuts. The arc shape allows for a smoother cutting motion, minimizing any distortion or bending of the metal sheets. As a result, the workpieces cut by guillotine shearing machines tend to have smoother edges compared to those produced by swing beam shearing machines.
Guillotine shear moves up and down in a vertical straight line relative to the lower blade. This vertical movement ensures that the sheet is sheared with minimal distortion and high precision. The straight cutting motion of the Guillotine shear enables it to maintain consistent straightness in the sheared material, which is particularly important for industries that require precise cuts for their applications.
Blade difference
The blade of the Guillotine shearing machine is designed to be used on all four sides, maximizing its lifespan and efficiency. This versatility allows for extended periods of use before needing replacement or sharpening, saving time and money in the long run.
Diamond-shaped Blade (Beam Shear): The diamond shape often allows for a more versatile cutting angle. This design can be advantageous when cutting thicker materials or making cuts with varying angles.
Rectangular Blade (Guillotine Shear): The straight edges of a rectangular blade are well-suited for straightforward vertical cuts. Guillotine shears are often used for precision straight-line cuts on thinner materials.
Operation difference
The operation of the guillotine hydraulic shearing machine and the swing beam shearing machine differ in terms of adjusting the blade gap.
The Guillotine hydraulic shearing machine offers the flexibility to adjust the blade gap either through a motor or a handwheel. This allows for precise and convenient adjustments according to the specific requirements of the material being cut. Whether you prefer automated adjustments or manual control, the Guillotine shearing machine provides options to suit your preferences and streamline your cutting process.
The swing beam hydraulic shearing machine adjusts the blade gap solely through the handwheel. While this may require a bit more manual effort, it still offers the advantage of adjustability. By using the handwheel, operators can easily fine-tune the blade gap to achieve the desired cutting results. This manual control ensures that the swing beam shearing machine can be operated with precision and accuracy, allowing for efficient shearing of metal sheets.