When it comes to precision metalworking, a hydraulic sheet metal brake is an indispensable tool for any workshop. These machines offer unparalleled control and efficiency in bending and shaping metal sheets, making them essential for high-quality fabrication. However, with a wide range of models and features available, selecting the right hydraulic sheet metal brake can be a daunting task. This comprehensive buying guide will walk you through everything you need to know—from understanding the basic components and features to evaluating top brands and models. Whether you're upgrading your equipment or investing in a hydraulic sheet metal brake for the first time, this guide will help you make an informed decision and find the perfect machine to meet your needs.
What Is Hydraulic Sheet Metal Brake
A Hydraulic Sheet Metal Brake apply pressure via hydraulics to force the ram down, instead of relying solely on mechanics. They may have more than one cylinder and give the operator more precise control over the bend. The result is a highly accurate and customizable bend. Like mechanical press brakes, hydraulic press brakes do have some specific disadvantages. Primarily, they cannot exceed the range of their rated tonnage. If your project requires flexibility, mechanical press brakes may be preferred.
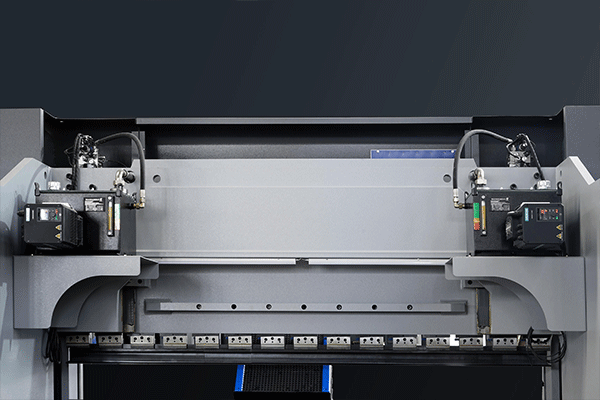
Components
A hydraulic sheet metal brake is a specialized machine used in metalworking to bend and shape metal sheets with precision. Unlike manual brakes, hydraulic models use hydraulic pressure to control the bending process, allowing for more accurate and consistent results. These machines are essential for producing complex metal parts and components in various industries, including automotive, aerospace, and construction.
Hydraulic Cylinder:
The hydraulic cylinder is the heart of the hydraulic sheet metal brake, responsible for generating the necessary force to bend metal sheets. It operates by converting hydraulic fluid pressure into mechanical force. This fluid, usually oil, is pumped into the cylinder, creating a high-pressure environment that drives a piston. The force from the piston is then transmitted to the bending tools, enabling precise and powerful bending operations. The hydraulic cylinder's efficiency and reliability are crucial for consistent performance and longevity of the machine.
Ram:
The ram is the moving part of the hydraulic sheet metal brake that directly applies force to the metal sheet. Mounted on a hydraulic cylinder, the ram moves vertically to create the bend. It is designed to exert uniform pressure across the metal sheet, ensuring consistent and accurate bends. The ram's movement is controlled by the machine's control system, allowing for precise adjustments in bending angle and depth. This precision is essential for producing high-quality metal components with exact specifications.
Bed:
The bed is the stationary platform where the metal sheet is placed during the bending process. It provides a stable support structure and ensures proper alignment of the metal sheet. The bed's surface is typically hardened and machined to withstand the forces involved in bending. It often includes features like alignment guides and clamps to secure the metal sheet in place. Proper bed alignment is critical for achieving accurate bends and maintaining the machine's overall precision.
Back Gauge:
The back gauge is an adjustable component that positions the metal sheet relative to the bending tools. It ensures that the sheet is placed at the correct distance from the ram, which is crucial for achieving accurate bend lengths and angles. Modern back gauges are often equipped with digital readouts and programmable controls, allowing for quick and precise adjustments. This feature enhances the machine's versatility and efficiency, making it easier to handle different bending tasks and maintain consistency across multiple parts.
Tooling:
Tooling consists of the punch and die sets used to shape the metal during bending. The punch applies force to the metal, pressing it into the die, which provides the desired bend profile. Tooling can be customized to create various bend shapes and angles, making it a versatile aspect of the hydraulic sheet metal brake. The quality and condition of the tooling directly impact the accuracy and finish of the bent metal. Regular maintenance and proper alignment of tooling are essential for achieving optimal results and extending the machine's lifespan.
Control System:
The control system of a hydraulic sheet metal brake manages the machine's bending parameters, including angle, depth, and speed. Modern systems feature digital interfaces, programmable settings, and advanced sensors that allow for precise adjustments and automation of the bending process. This capability enhances the machine's versatility and accuracy, enabling operators to produce complex bends with high repeatability. The control system also often includes safety features and diagnostic tools to ensure smooth operation and reduce the risk of errors or accidents.
Hydraulic Pump:
The hydraulic pump is responsible for circulating hydraulic fluid throughout the system, powering the hydraulic cylinder and ram. It creates the pressure required for bending by drawing fluid from a reservoir and forcing it into the hydraulic cylinders. The pump's performance is critical for the machine's efficiency and responsiveness. High-quality pumps provide consistent pressure, reducing the risk of fluctuations and ensuring stable operation. Proper maintenance of the hydraulic pump, including regular checks of fluid levels and system components, is essential for the reliable performance of the hydraulic sheet metal brake.
How Does a Hydraulic Sheet Metal Brake Work?
To gain a thorough understanding of a hydraulic press brake, let's explore the fundamental processes that drive its operation.
What is the Basic Working Principle of a Hydraulic Press Brake?
A hydraulic press brake operates through two main components: the force generated by hydraulic fluid and the precision offered by modern control technology. When the bending process begins, hydraulic pumps generate pressure that pushes hydraulic fluid through the system. This fluid activates hydraulic cylinders, which in turn move the ram vertically. The ram then exerts force on the metal sheet positioned over a die, bending it according to the desired angle. Operators can adjust the ram’s speed, position, and force using CNC or computer controls, enabling precise and consistent bending results.
How Do Hydraulic Forces Enable Bending in a Press Brake?
Hydraulic forces are crucial to the bending process in a press brake. These forces are created by the pressure of hydraulic fluid, which the operator controls to regulate the amount of force applied to the metal sheet. The hydraulic pressure causes the ram to descend and press the metal sheet against the die, shaping it to the specified bend angle. By adjusting the hydraulic pressure, operators can achieve the exact bending requirements for various applications.
Advantages of a Hydraulic Sheet Metal Brake
Precision and Accuracy: Hydraulic sheet metal brakes are renowned for their precision in bending. The hydraulic system allows for exact control of the bending parameters, including angle, depth, and force, resulting in highly accurate bends. This precision reduces the need for manual adjustments and minimizes errors, ensuring consistent quality in every part.
High Efficiency: Hydraulic brakes operate with greater efficiency compared to mechanical or manual brakes. The hydraulic pressure provides a strong and steady force, which speeds up the bending process and increases productivity. This efficiency is particularly valuable in high-volume production environments.
Consistent Results: The hydraulic system ensures uniform bending across multiple operations, providing consistent results with each cycle. This reliability is essential for producing parts that meet strict specifications and quality standards.
Ease of Operation: Hydraulic sheet metal brakes are easier to operate than manual or mechanical systems. Modern models feature user-friendly controls and automation, which simplify the bending process and reduce the physical effort required from operators. This ease of use contributes to higher productivity and fewer operator errors.
Versatility: Hydraulic brakes are highly versatile and can handle a wide range of materials, thicknesses, and bend angles. This versatility makes them suitable for various applications, from simple bends to complex shapes, and allows for flexibility in production.
Reduced Wear and Tear: The hydraulic system experiences less mechanical wear compared to manual or mechanical brakes. This reduction in wear and tear leads to lower maintenance requirements and a longer machine lifespan, resulting in cost savings over time.
Advanced Control Systems: Many hydraulic sheet metal brakes are equipped with advanced control systems that allow for precise adjustments and automation. These systems can include features like digital readouts, programmable settings, and real-time monitoring, enhancing the machine's capabilities and improving overall efficiency.
Increased Safety: Hydraulic brakes often incorporate safety features such as automatic stops, sensors, and emergency shut-offs. These features help protect operators and reduce the risk of accidents during the bending process.
Improved Quality: The combination of precision, consistency, and ease of operation provided by hydraulic brakes contributes to high-quality finished products. This improved quality reduces the need for rework and ensures that parts meet the desired specifications.
Scalability: Hydraulic sheet metal brakes can be scaled to accommodate different production needs, from small workshops to large industrial facilities. Their ability to handle various sizes and complexities makes them adaptable to changing production requirements.
Advantages of Hydraulic Sheet Metal Brakes Over Other Press Brakes
Greater Precision and Control: Hydraulic sheet metal brakes offer superior precision compared to mechanical or manual press brakes. The hydraulic system allows for fine-tuning of bending parameters such as angle, depth, and force, leading to highly accurate and consistent bends.
Increased Efficiency: The hydraulic system provides steady and powerful force, making the bending process faster and more efficient. This efficiency is especially beneficial in high-volume production, where speed and consistency are crucial.
Uniform Bending Results: Hydraulic brakes deliver consistent bending performance across multiple operations. Unlike mechanical brakes, which may require frequent adjustments and recalibration, hydraulic systems maintain uniform results, reducing the likelihood of defects and inconsistencies.
Ease of Use: Hydraulic sheet metal brakes are generally easier to operate than manual or mechanical brakes. Modern hydraulic models often feature user-friendly controls, digital displays, and automation options that simplify operation and reduce the physical effort required from the operator.
Versatility in Material Handling: Hydraulic brakes can handle a wide range of materials, thicknesses, and bend angles with ease. This versatility makes them suitable for diverse applications, from simple bends to complex shapes, and allows for greater flexibility in production.
Reduced Mechanical Wear: The hydraulic system experiences less mechanical wear and tear compared to manual or mechanical brakes. This reduction in wear leads to lower maintenance requirements and a longer machine lifespan, translating to cost savings and increased reliability.
Advanced Control Systems: Many hydraulic sheet metal brakes are equipped with advanced control systems that offer programmable settings, real-time monitoring, and precise adjustments. These features enhance the machine's capabilities and improve overall operational efficiency.
Improved Safety Features: Hydraulic presses often come with integrated safety features such as automatic stops, sensors, and emergency shut-offs. These safety measures help protect operators and reduce the risk of accidents during the bending process.
Consistency in Quality: The ability of hydraulic brakes to deliver precise and consistent results contributes to high-quality finished products. This consistency reduces the need for rework and ensures that parts meet the desired specifications.
Flexibility for Complex Bends: Hydraulic brakes can accommodate more complex bending tasks and intricate shapes compared to mechanical brakes. Their ability to apply uniform force and adjust bending parameters makes them well-suited for producing complex geometries and detailed components.
What Is CNC Hydraulic Press Brake
A CNC Hydraulic Press Brake is an important tool in manufacturing processes. These machines are used to bend metal sheets with a specific bending force. The tonnage of a press brake determines how much pressure is applied to the metal sheet during the bending process. Higher tonnages are better for bending thicker metals, while lower tonnages are best for bending thin metals. Also, consider the bending length of the metal sheet.
A hydraulic press brake consists of a frame composed of two upright plates, a worktable and supporting bodies. These parts are connected by a servo valve. When the upper die is assembled, it overcomes the impact of the ram’s deformation and enables a good bending angle. CNC Hydraulic Press Brake is ideal for a variety of materials and parts. In addition, it features a high capacity hydraulic system.
Press Brake Segmented Punches Reduce Tool Change Time
Press brakes are often equipped with various solutions to minimize tool change time. Wila’s front-loading system, for example, saves time and effort by eliminating the need to change tool dies. The system’s diodes indicate which tool to mount and saves operators from having to reach out to the tool rack. Another feature of the Wila system is its variable-opening full-length die that allows tool changers to quickly change tools without deforming the tool.
The next topic of discussion in bending technology is stroke optimization. Press brakes can only bend a large part so quickly without compromising quality. The next important topic of discussion is stroke optimization. Using a high-speed press brake may increase throughput but reduce quality. Hydraulic press brakes can only bend so fast before sacrificing precision. If speed is not the most important factor for your business, then a high-speed machine may not be the best option.
High Accuracy in Hydraulic Press Brake
High accuracy is an important attribute for a hydraulic press brake. A small deviation can ruin a batch of parts. This type of machine has many benefits. Besides accuracy, it can save a lot of time. Its vertical loading guarantees short set up time. It can achieve good bending angles and reduce labor intensity. It is also durable. It can cut down on set up time and maximize production rate. Moreover, it will help you in producing high-quality parts.
Its independent control circuit, servo valve, and filling valve are designed for small batch and multi-various production. This machine is especially suitable for manufacturing parts with complex shapes. It can complete the production of many types of materials. This machine can reach an accuracy of 4 microns. It can also complete the production of various parts. It is an ideal choice for small-scale production. Its high accuracy makes it a great choice for small-scale production.
Low Cost of Hydraulic Press Brake
When looking for a press brake, the single most important question to ask yourself is “What’s my application?”. What will this machine do for me? How much time will it save me? How big will the parts I need to bend be? What do I expect the finished product to look like? What materials will I be working with? Considering these factors will help you select the best hydraulic press brake for your needs.
When purchasing a press brake, it is important to determine the size of the largest job you need it for. You should buy a machine one size larger than that, so that you can increase the tonnage. Also, consider buying an extra couple of feet, since you never know when you’ll need to bend longer parts. The length of the press brake is another important consideration. If you have a large shop, it is important to be able to bend large parts easily.
Easy to Use Hydraulic Press Brake
Unlike other types of metal bending machinery, a hydraulic press brake is simple to operate and can be customized to suit specific needs. In recent years, bending technology has advanced by leaps and bounds, making it easier to streamline workflows, optimize energy consumption, and cut operating costs. These newer press brakes can increase production speeds and improve operating efficiencies. For this reason, they are increasingly popular with manufacturers and consumers.
Hydraulic press brakes are easy to use because they are operated via a simple, intuitive interface. Many machines feature a built-in back gauge, which allows you to program how far the material needs to be pushed into the die. This backgauge sets the distance from the edge of the material to the center of the die. Using this backgauge makes it possible to control the angle of the bend, even at an angle.
How To Select A Hydraulic Sheet Metal Brake
With the increasing demand for efficiency and precision in metal manufacturing, the decision to select the appropriate hydraulic press brake machine becomes critical for manufacturers. This meticulous selection process entails evaluating various factors to ensure that the chosen machine perfectly aligns with the specific requirements of the operation.
1. Capacity and Tonnage
The first consideration is the machine’s capacity and tonnage. Assessing the thickness and type of materials regularly processed is essential in determining the appropriate tonnage required for the hydraulic press brake. Selecting a machine with the right capacity ensures optimal performance and longevity.
2. Bending Capacity
The bending capacity of a hydraulic press brake determines its ability to handle various sizes and thicknesses of metal sheets. Understanding the typical dimensions of the workpieces involved in your projects is crucial to ensure that the selected machine can effectively meet your bending requirements. Choosing a machine with the appropriate tonnage and bending length ensures versatility and efficiency in production.
3. Precision and Control
Precision is a critical factor in the decision-making process when it comes to press breaks. Opting for a press brake with lower precision to meet high precision requirements may result in the rejection of most parts. Therefore, it is essential to check the bending accuracy of the press brake before making a purchase.
4. Speed and Productivity
Different press brakes have varying bending speeds. Hydraulic press brake machines offer faster cycle times and rapid approach and retract speeds, thereby increasing overall productivity by reducing cycle times and improving throughput. Evaluating the machine’s speed capabilities and productivity features ensures optimal efficiency and output in metalworking operations.
5. Footprint and Space Requirements
Some press brakes come in larger sizes. Before considering a purchase, you must ensure that your factory or workspace has enough space to accommodate them. If high tonnage is not required, you may opt for smaller-sized press brakes.
6. Energy Efficiency & Noise Levels
Energy efficiency and noise levels are important considerations for a sustainable and comfortable work environment. Hydraulic press brake machines equipped with energy-efficient hydraulic systems and noise-reducing technologies minimize energy consumption and operational noise, contributing to cost savings and improved operator comfort. Prioritizing machines that operate in an environmentally friendly and quiet manner enhances the overall efficiency and sustainability of metal manufacturing processes.
7. Maintenance and Support
Reliable maintenance and prompt support are key factors in ensuring the longevity and optimal performance of hydraulic press brake machines. Choosing a reputable manufacturer or supplier that offers comprehensive maintenance plans and timely technical support can minimize downtime and maximize uptime in case of issues or maintenance needs. Prioritizing machines with accessible maintenance features can simplify routine upkeep, prolong machine lifespan, and reduce operational disruptions.
8. Budget Considerations
When considering the various features and functionalities of hydraulic press brake machines, it’s essential to ensure they align with budget constraints. Evaluating upfront costs, long-term maintenance expenses, and potential return on investment helps in making balanced decisions that prioritize performance within affordability. Investing in high-quality machines with the best value for money ensures optimal functionality and cost-effectiveness throughout their lifespan.
How Much Does a Hydraulic Sheet Metal Brake Cost?
A hydraulic press brake can cost anywhere from $5,000 to $200,000 and upwards. Understanding the cost of a hydraulic press brake involves considering various factors, including the size and complexity of the machine and the ongoing costs of operating it.
What Factors Influence the Cost of a Hydraulic Press Brake?
Several elements can affect the price of a hydraulic press brake, including its capacity (tonnage), bending length, CNC capabilities, brand, and whether it is new or used.
Size
The size of the machine is often directly proportional to the cost. Larger machines with higher tonnage capacities typically come with a higher price tag as they can handle thicker materials and larger workpieces.
- Entry-Level Hydraulic Press Brakes: These can cost anywhere from $5,000 to $20,000. These are typically smaller machines with less complexity and tonnage.
- Mid-Range Hydraulic Press Brakes: Machines in this category typically cost between $20,000 and $50,000. These machines often offer greater tonnage and length, as well as more advanced controls and features.
- High-End Hydraulic Press Brakes: Top-of-the-line machines can easily cost $50,000 to $200,000 or even more, depending on the specific model and its features. These machines are typically used for heavy-duty applications and feature advanced control systems, high tonnage, and long bed lengths.
Complexity of the Machine
The complexity of the hydraulic press brake also impacts its cost. Machines equipped with advanced features like CNC controls, a back gauge system, or a variety of press brake tooling options will be priced higher due to their increased functionality and precision.
What are the Ongoing Costs of Operating a Hydraulic Press Brake?
Beyond the upfront purchase cost, operating a hydraulic press brake involves ongoing expenses, including maintenance costs and energy consumption.
How Much Does Regular Maintenance Cost?
Regular maintenance of a hydraulic press brake is essential to ensure its optimal performance and longevity. These costs can include routine check-ups, replacement of worn-out parts, and hydraulic fluid refills.
What are the Typical Energy Consumption Costs?
While hydraulic press brakes are more energy-efficient than their mechanical counterparts, they still require a considerable amount of energy to operate. The energy consumption costs can vary depending on the machine’s size, usage frequency, and local electricity rates.
How to Maintain a Hydraulic Press Brake?
Proper maintenance is crucial to ensure the longevity and efficient operation of a hydraulic press brake.
What are the Key Aspects of Routine Maintenance for a Hydraulic Press Brake?
Routine maintenance for a hydraulic press brake generally involves tasks such as checking the hydraulic oil levels and quality, inspecting the machine for any signs of wear or damage, lubricating moving parts, and ensuring the cleanliness of the machine.
How Often Should Maintenance Be Conducted?
Maintenance frequency can depend on the usage of the machine. Generally, it’s advisable to conduct a full-scale maintenance check-up every six months. However, tasks like lubrication and cleanliness should be addressed daily.
What are the Best Practices for Long-Term Care of a Hydraulic Press Brake?
For the long-term care of a hydraulic press brake, regular maintenance checks, immediate addressing of any detected issues, and usage of the machine within its rated capacity are best practices. It’s also advisable to provide training to the machine operator to understand the correct operation and maintenance of the press brake.
While routine maintenance can be performed by trained operators, it’s recommended to hire a professional for comprehensive maintenance checks or when serious issues are detected. Professionals possess the knowledge and tools to diagnose and fix complex problems that may be beyond the understanding of a regular operator.