What is a Hydraulic Shearing Machine?
A hydraulic shearing machine represents a pivotal piece of equipment in metalworking processes, leveraging the dynamic interplay between an upper blade and a steadfast lower blade. Operating with a discernible blade gap, this machinery applies precise shearing force to metal sheets of varying thickness, effectually breaking and separating them into desired dimensions. Key components of a hydraulic shearing machine include the frame, hydraulic pump, hydraulic cylinder, and blades, each playing a crucial role in the seamless execution of cutting operations.
The frame serves as the foundational support structure, ensuring stability and durability throughout the machine's operation. Meanwhile, the hydraulic pump assumes a central role in generating hydraulic pressure, a fundamental aspect of the system's functionality. By pressurizing hydraulic fluid, the pump facilitates the transmission of force necessary for cutting operations.
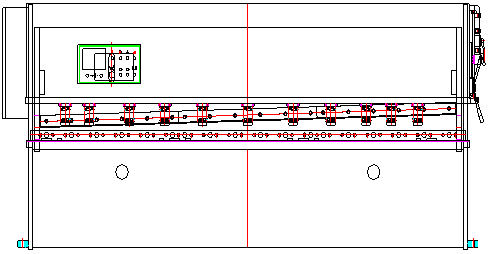
At the heart of the hydraulic shearing machine is the hydraulic cylinder, a core component responsible for generating the requisite cutting force. This cylinder is instrumental in translating hydraulic pressure into mechanical action, enabling the upper blade to exert controlled force on the metal sheets.
The blades themselves are pivotal for executing precise machining operations. Crafted to withstand robust usage, they embody the essence of the shearing process, ensuring clean and accurate cuts. The cooperative motion of the upper and lower blades, orchestrated by the hydraulic system, forms the basis of the machine's proficiency in metal sheet manipulation.
The operational principle hinges on the transmission of pressure through hydraulic fluid. The hydraulic pump pressurizes the fluid and directs it into the hydraulic cylinder, creating substantial force on the blades. This hydraulic force is meticulously applied, allowing the machine to perform cutting and shearing operations on metal sheets with remarkable precision and efficiency.
Hydraulic shearing machines are broadly categorized into two main types based on the motion of the upper blade: hydraulic swing beam shearing machines and hydraulic guillotine shearing machines. Each type offers distinct advantages and is chosen based on specific application requirements. This classification underscores the versatility of hydraulic shearing machines, catering to a spectrum of metalworking needs while embodying reliability and precision in the world of manufacturing.
What Is A Hydraulic Swing Shear?
A hydraulic swing shearing machine is a common metal processing equipment, mainly used to cut metal sheets of different thicknesses into required lengths. It mainly consists of an upper tool holder, lower tool holder, hydraulic system, swing arm, slider, oil cylinder, and hydraulic system. The swing arm connects the upper and lower tool holders to support and transmit shear force.
What Is A Hydraulic Guillotine Shear?
A hydraulic Guillotine shearing machine is a common metal processing equipment, mainly used to cut metal sheets of different thicknesses into metal parts of required shapes and sizes. The hydraulic Guillotine shearing machine adopts an all-steel welded frame structure with hydraulic preload. It is mainly composed of the body, hydraulic system, cutting tools, fixtures, and other parts. Among them, the body is the frame of the shearing machine, the hydraulic system provides power, the cutter is responsible for shearing the metal sheet, and the clamp is used to fix the metal sheet to ensure shearing accuracy and efficiency.
Working Principle
Hydraulic Swing Shearing Machine
The hydraulic swing shearing machine operates through the force of hydraulic pressure, employing an oil cylinder to propel the swing shearing mechanism for the purpose of shearing plates. The mechanism involves the application of significant pressure between the blade and the plate when the oil cylinder moves the shearing blade towards the metal surface. This substantial pressure induces the plate to reach its shear strength, ultimately facilitating the shearing process.
In more detail, as the oil cylinder exerts force, the swing shearing mechanism swings into action, positioning the blade in close proximity to the metal plate. The hydraulic pressure harnessed by the oil cylinder plays a pivotal role in generating the force needed for the blade to make contact with the plate. This force, intensified by the hydraulic system, creates a powerful compression between the blade and the plate.
The culmination of this force on the plate results in it reaching its shear strength, a critical point where the material is poised to undergo shearing. At this juncture, the shearing mechanism seamlessly severs the metal plate, producing clean and precise cuts according to the intended dimensions.
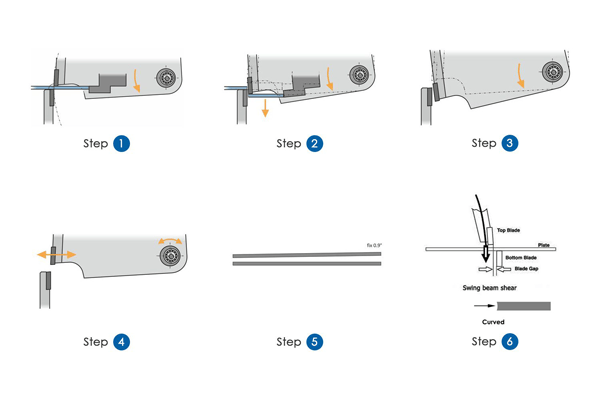
This hydraulic swing shearing machine design offers a robust and efficient means of metal shearing. The hydraulic system's ability to apply controlled force through the oil cylinder ensures a consistent and powerful shearing process. This method is particularly advantageous when dealing with varying thicknesses of metal sheets, providing a versatile solution for a range of industrial applications.
In essence, the hydraulic swing shearing machine's reliance on hydraulic pressure, channeled through the oil cylinder, showcases its effectiveness in achieving the necessary force for plate shearing. This approach, coupled with the precision of the swing shearing mechanism, positions the machine as a reliable tool for achieving accurate and efficient metal cutting in diverse manufacturing settings.
Hydraulic Guillotine Shearing Machine
The operational principle of the hydraulic Guillotine shearing machine revolves around the utilization of hydraulic power to drive the downward movement of the cutter, effectively shearing metal plates. This process is facilitated by a hydraulic system that incorporates a two-way cartridge integrated valve. During the shearing operation, a clamp situated between the cutter and the metal sheet plays a crucial role in securing the metal sheet, preventing any unintended movement or bending.
The hydraulic system is equipped with advanced features, including a digital stroke display, a photoelectric protection device, and a mobile workbench designed for seamless mold replacement. This mobile workbench enhances the machine's functionality by providing a convenient platform for mold replacement, streamlining the overall workflow. The inclusion of a digital stroke display ensures precise control over the shearing process, allowing for accurate and repeatable results.
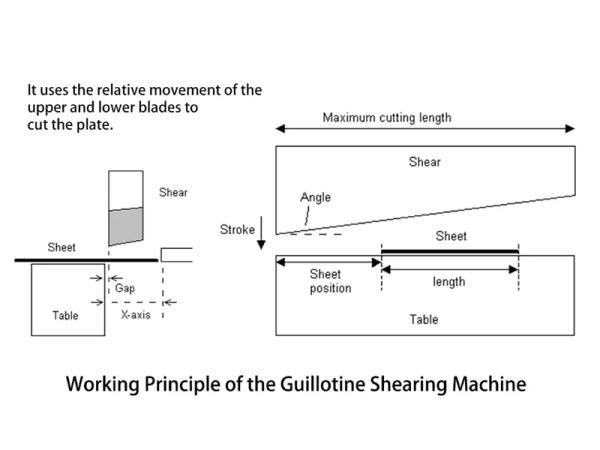
In addition to these features, the hydraulic system offers versatility through adjustable working parameters. The working pressure stroke can be easily tailored within specified ranges to meet the specific requirements of different manufacturing processes. Centralized buttons contribute to user-friendly operation, consolidating control functions for convenient and efficient use.
Furthermore, the hydraulic system's capabilities extend to controlling both the downward force and shearing speed of the tool. This control is achieved by adjusting pressure and flow within the hydraulic system, providing operators with the flexibility to achieve varied shearing effects. This adaptability is crucial for accommodating different metal thicknesses and material types, enhancing the machine's overall utility in diverse industrial applications.
The integration of advanced technologies, such as the photoelectric protection device, adds an extra layer of safety to the hydraulic Guillotine shearing machine. This device ensures the protection of both the operator and the equipment during operation by detecting and responding to potential hazards promptly.
Therefore, the hydraulic Guillotine shearing machine stands as a sophisticated and versatile tool in metalworking. Its working principle, driven by hydraulic power, ensures precision and efficiency in shearing metal plates. The inclusion of modern features, such as digital displays and safety devices, coupled with the flexibility to adjust working parameters, positions this machine as a reliable and indispensable asset in various industrial settings.
Shearing Machine Performance Characteristics
Hydraulic Swing Shearing Machine
The hydraulic transmission ensures that the thickness of the sheet will not change during operation. In addition, this machine has the characteristics of smooth operation, convenient operation, low noise, safety, and reliability.
There is a mechanical stop in the oil cylinder to ensure the repeatable positioning accuracy of the slider to the bottom dead center to ensure the consistency of the bending angle during mass production.
Use German technology for internal stress relief.
The overall frame is rust-removed by sandblasting and sprayed with anti-rust paint.
Hydraulic Guillotine Shearing Machine
The vibration of the frame and tool holder eliminates stress, and the whole machine is welded and durable.
Advanced integrated hydraulic system with good reliability.
Use a three-point supporting rolling guide rail to eliminate supporting gaps and ensure shearing quality.
The blade gap can be adjusted manually or electrically, quickly and accurately.
The upper and lower blades adopt four-sided blades to increase the use time and extend the service life of the blades.
The shearing angle can be adjusted electrically to minimize the deformation of the plate.
It has the function of segmented fixed-length cutting.
Automatic filling function.
Electric back gauge and digtal display, accurate and reliable
The Main Differences Between Guillotine Shears And Swing Shears
Cutting Accuracy
The knife rest of the swing shearing machine itself is arc-shaped, and the point contact of the arc ensures the straightness of the material being sheared, while the knife rest of the Guillotine shearing machine operates relative to the lower blade. Vertical linear motion ensures small deformation and good straightness of the sheared plate. Therefore, in comparison, the hydraulic Guillotine shearing machine is more accurate than the hydraulic swing shearing machine.
Taking the 16*3200 hydraulic swing shearing machine and the hydraulic Guillotine shearing machine as an example, the gap values calculated at the edges of the swing and Guillotine shearing machines are both less than 6 mm, but the gap between the swing arm and the swing frame body of the swing beam machine is The bearing connection gap between them cannot be eliminated.
In addition, the cumulative shearing accuracy error of the gap and edge gap is generally more than 10 mm, and the rear guide rail of the Guillotine shear body is supported by 4 large bearings, and the front guide rail is pressed behind them by 2 bearings with compression springs. Tight, so that there is no gap between the front and rear guide rails, and the additional precision error between the gap and the edge gap is kept below 4 mm, so the sheared material is smoother and burr-free.
Different Shear Angles
When shearing plates with a thickness of less than 20 mm, the shearing angle of the hydraulic swing shearing machine cannot be adjusted, causing the sheared material to be distorted. The narrower the material being cut, the greater the deformation. Since the shearing angle of the hydraulic swing shearing machine is fixed, the efficiency of shearing thin plates and thick plates is the same, which means that a lot of power resources and running time are required. For example: the QC12Y-10X2500 hydraulic shearing machine has a motor power of 55KW and can cut a 10mm thick plate 8 times/minute. Since the shearing angle cannot be adjusted, the same 5mm thick plate can be sheared 8 times/minute. To reduce frame deformation and reduce machine power, the shearing angle of the swing shearing machine is usually at the maximum value, but a larger shearing angle when shearing thin plates will cause greater bending deformation of the sheared work piece.
In contrast, hydraulic Guillotine shears can achieve angle adjustment by adjusting the amount of oil in a closed chamber connected in series between two engineering cylinders. During work, the curvature of the plate is effectively reduced, making the sheared plate less likely to twist and deform, thereby maintaining the accuracy of the work piece. More importantly, the shear force is stronger when the shear angle is increased.
Different Types Of Exercise
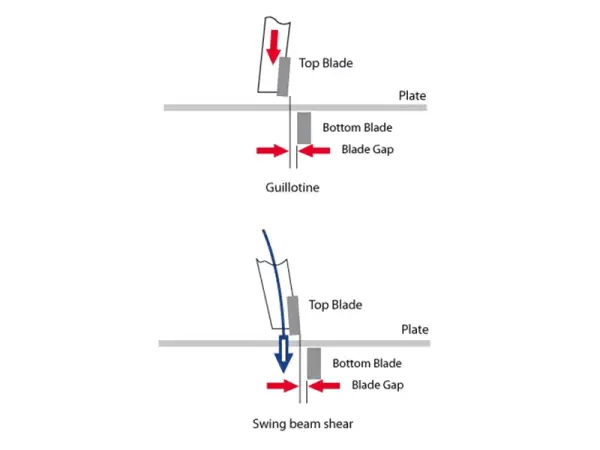
The blade holder of the Guillotine shearing machine moves up and down. It makes a vertical linear motion relative to the lower blade to ensure the shearing of the sheet. The distortion and deformation are small, the straightness is more accurate, and the accuracy is twice that of the swing shearing machine. The swing-type shearing machine has an arc-shaped movement. The tool holder body of the swing shear is arc-shaped, and the points of the arc are used to contact to ensure the straightness of the sheared material.
Blade Differences
Hydraulic swing shears cannot use all four edges of the blade to cut sheet metal due to the arc-shaped motion of their blades.
Therefore, only diamond-shaped cutting edges can be used for double-sided cutting.
In contrast, the blade holder of the Guillotine shearing machine moves up and down in a linear motion, allowing it to directly use a rectangular blade with four cutting edges. This makes the blade of the Guillotine shearing machine last longer than the blade of the swing shearing machine. double. In addition, the diamond-shaped blade shears the plate, which can easily cause the plate to twist. This defect becomes more severe the narrower the material you are cutting, and a rectangular blade avoids this defect.
Cylinder Life
The semicircular block of the built-in oil cylinder used in the swing shearing machine is difficult to lubricate and maintain, but the upper and lower chambers of the oil cylinder in the shearing machine project do not require additional lubrication, thus greatly extending the service life of the shearing machine. Improve service life.
Operational Differences
Since the blade holder of the swing shearing machine is arc-shaped, arc point contact is made to ensure the straightness of the material being sheared.
The Guillotine shear ensures the straightness of the material being sheared through its straight blade holder, thereby achieving higher precision.
However, there is an obvious blade retraction phenomenon in the middle of the swing-type shearing machine, resulting in burrs on some sheared materials. This problem cannot be avoided.
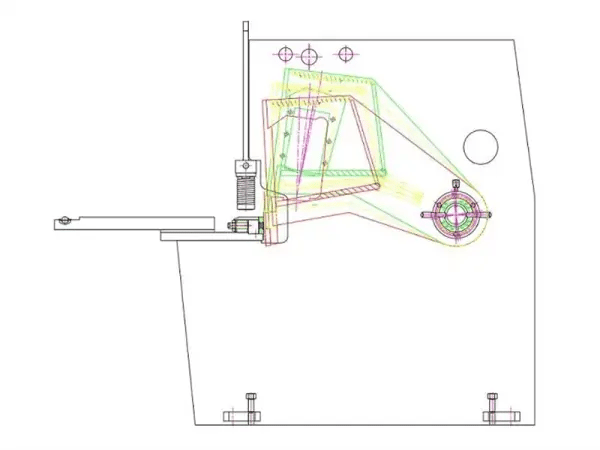
Application Areas
Hydraulic Guillotine Shearing Machine
Hydraulic guillotine shearing machines are widely used in metal processing industries such as automotive, aviation, machinery, and construction. They excel in efficiently and accurately shearing various metal sheets, especially in large-scale production settings. Hydraulic guillotine shearing machines have a broader range of applications and are suitable for industries such as automotive, tractors, locomotives, ships, motors, and instruments, and are also suitable for stretching high-strength alloy sheets.
For example, in a coal processing plant designed to process 3 million tons of coal annually, which later expanded to a maximum capacity of 16 million tons per year, hydraulic guillotine shearing machines play a crucial role in achieving cost savings, reducing production costs, and improving efficiency. The plant faced the challenge of optimizing its operations in the context of high-quality, intelligent development. The existing mechanical shear machine had exceeded its service life, had a high failure rate, and low efficiency, and could not meet the current processing needs. Hydraulic guillotine shearing machines were introduced to transition the processing equipment towards greater automation and efficiency, with the goal of reducing costs, increasing efficiency, and lowering maintenance expenses.
Hydraulic Swing Beam Shearing Machine
Hydraulic swing beam shearing machines are known for their high cutting precision, efficiency, and low noise. Driven by hydraulic systems, they offer precise and uniform motion, and ease of operation, and are suitable for processes like stretching, bending, squeezing, and forming thin metal sheets in industries such as power generation and aviation.
For instance, ABC Manufacturing Co., Ltd. purchased an advanced hydraulic swing beam shearing machine to replace their outdated cutting equipment. They opted for a high-performance swing beam shearing machine capable of meeting their metal sheet cutting needs, offering enhanced cutting capacity and automated control features. They seamlessly integrated this hydraulic swing beam shearing machine into their production workflow. The performance advantages of the new equipment enabled them to meet customer demands more efficiently, reduce production cycles, minimize waste, and improve product quality. This not only increased the company's competitiveness but also led to more orders and business growth. The investment in the swing beam shearing machine not only boosted production efficiency but also helped the company capture a larger market share, establishing them as leaders in the metal processing industry.
Conclusion And Usage Recommendations
In conclusion, the main differences between hydraulic guillotine shearing machines and hydraulic swing beam shearing machines lie in their machine structures and operating principles. The former uses a Guillotine-type pressure transmission mechanism, making it suitable for cutting various material thicknesses with high precision. On the other hand, hydraulic swing beam shearing machines use a swinging arm design and are not suitable for cutting thick materials, but they offer advantages such as a smaller footprint and good stability.
Furthermore, hydraulic guillotine shearing machines offer higher precision, and longer blade lifespan, and are ideal for various material thicknesses. However, their manufacturing cost is higher. Considering cost savings and precision requirements, if precision is not critical and the material thickness is thin (below 8mm), a swing beam shearing machine may be suitable. For materials exceeding 8mm in thickness, a hydraulic guillotine shearing machine is necessary, as the swing beam shearing machine's principle limits it from cutting thick materials. When making a purchase, comprehensive consideration should be given to actual needs. If you have any further questions about shearing machines, please feel free to contact Krrass!