Choosing the right laser cutter for your specific needs involves a careful consideration of the materials you plan to cut, the precision required, the volume of work, and, of course, your budget. With various types of laser cutters on the market, including CO2 lasers, fiber lasers, and diode lasers, each offers unique benefits and is better suited for certain materials and applications.
Table of Contents
6 Factors to Consider Based on Cutting Material
Material Compatibility
The foremost consideration in choosing a laser cutter is the material you intend to cut. Different laser types have varying capabilities when it comes to the range of materials they can effectively process.
CO2 lasers are incredibly versatile, able to cut and engrave a wide range of materials, including wood, acrylic, fabric, and leather. However, they struggle with cutting metals without an added air assist system.
Fiber lasers excel at cutting metal sheets, including stainless steel and aluminum, offering high precision and speed. They are not as effective with non-metal materials.
Diode lasers offer a balance between CO2 and fiber lasers, capable of cutting thinner materials and engraving on both metals and non-metals, but with limitations in power and material thickness.
Material Thickness
The thickness of the materials you plan to cut is just as important as the type. Laser power is a critical factor here, measured in watts.
Higher laser power (150 watts and above) is necessary for cutting through thicker materials like thick wood or metal plates.
For thinner materials, such as paper, cardboard, or thin sheets of acrylic and fabric, a laser cutter with lower power (50 watts or less) can be sufficient.
Precision and Quality
The desired precision and quality of the cut also play a significant role in the selection process.
Fiber lasers are known for their incredible precision, making them ideal for industries requiring high detail, such as electronics manufacturing.
CO2 lasers offer a good balance of quality and versatility, suitable for a wide range of laser cutting applications needing clean edges and fine details.
Production Volume
Consider the volume of work you expect to process. High-volume projects require a laser cutter that is not only fast but also reliable over extended periods.
Fiber lasers tend to have a faster cutting speed, especially for metal materials, making them suitable for high-volume production.
CO2 lasers might be slower in comparison but are often more affordable, making them a good choice for small businesses or educational settings.
Budget Constraints
Your budget will undoubtedly influence your choice of laser cutter.
Fiber lasers, while highly efficient for cutting metals, tend to be more expensive due to their advanced technology and components.
CO2 lasers offer a more cost-effective solution for those who primarily work with non-metal materials.
Diode lasers represent an even more budget-friendly option, especially for hobbyists or small-scale operations, but with limitations in capabilities and durability.
Safety and Ventilation
Lastly, the safety features of the laser cutter and the ventilation requirements for safe operation should not be overlooked.
Materials like PVC and certain plastics can emit toxic fumes or chlorine gas when cut, necessitating good ventilation and air filtration systems.
Ensure the laser cutter comes with built-in safety features to protect against fire, toxic gasses, and other hazards associated with laser cutting.
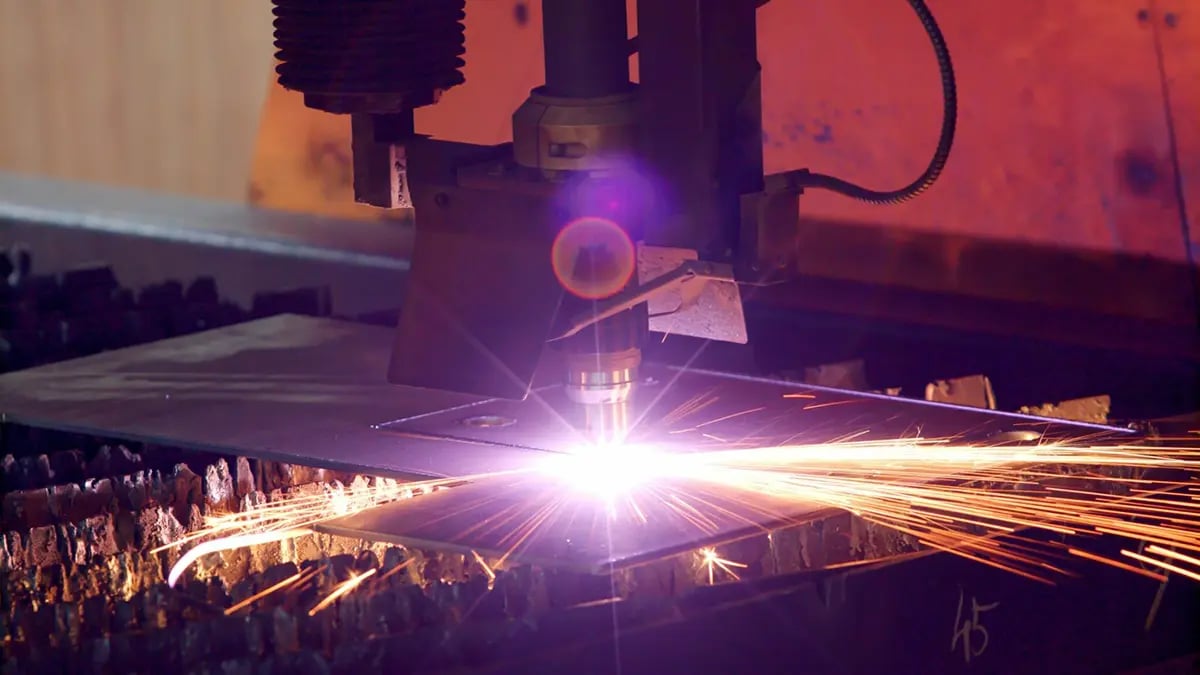
Influence of Different Materials on the Selection of Laser Cutter
The choice of laser cutting machine is heavily influenced by the type of material being processed. Different materials have unique properties that impact the laser cutting process, including their thickness, composition, and surface characteristics. Here's how various materials influence the selection of a laser cutting machine:
Metals:
Steel: Fiber laser cutting machines are commonly used for cutting steel due to their high power and efficiency. CO2 lasers can also cut steel, but fiber lasers offer faster cutting speeds and better precision.
Aluminum: Fiber lasers are preferred for cutting aluminum because they provide excellent beam quality and are highly efficient at cutting reflective materials like aluminum.
Stainless Steel: Fiber lasers are well-suited for cutting stainless steel, offering clean and precise cuts with minimal heat-affected zones.
Non-Metals:
Acrylic (PMMA): CO2 lasers are ideal for cutting acrylic due to their ability to produce polished edges without melting or discoloration.
Wood: CO2 lasers are commonly used for cutting and engraving wood materials, offering high precision and intricate detailing.
Plastics: CO2 lasers are suitable for cutting various plastics, including ABS, PVC, and polycarbonate, providing clean cuts with minimal thermal damage.
Fabrics and Textiles: CO2 lasers are preferred for cutting fabrics and textiles due to their ability to seal edges and prevent fraying.
Composites:
Carbon Fiber: Fiber lasers are often used for cutting carbon fiber composites due to their high speed and precision. However, the abrasive nature of carbon fiber may require special considerations for laser optics and cutting parameters.
Fiberglass: CO2 lasers are suitable for cutting fiberglass materials, providing clean and precise cuts without causing delamination or surface damage.
Other Materials:
Ceramics: CO2 lasers can be used for cutting ceramic materials, although special considerations may be needed due to the brittle nature of ceramics.
Glass: CO2 lasers are commonly used for engraving glass, but cutting glass with lasers requires specialized equipment and techniques due to its high thermal conductivity and potential for cracking.
Conclusion
When selecting a laser cutting machine, it's essential to consider the specific requirements of the material being processed, including its thickness, hardness, and thermal conductivity. Additionally, factors such as cutting speed, edge quality, and cost-effectiveness should be taken into account to ensure optimal results and efficiency in the laser cutting process. Consulting with laser cutting experts or equipment suppliers can provide valuable insights and recommendations for choosing the right laser cutting machine for your material processing needs.