The significance of focal positions in laser cutting operations cannot be overstated, as they directly impact the quality, efficiency, and precision of the cutting process. The focal position refers to the exact point at which the laser beam converges to its smallest diameter, known as the focal spot. This spot is where the laser beam delivers maximum energy density, allowing for optimal cutting performance. Here are several key reasons highlighting the importance of focal positions in laser cutting operations:
Focusing of Laser Cutting
Focusing Laser Beams
Every fabricator may have his or her opinion as to what is the most important element in laser cutting. Do you think it is maintaining the smallest spot size and a lens orientation perpendicular to the axis of the laser beam? If you answered yes, you are partially correct, but many other factors need to be considered with respect to laser beam properties and cutting applications. Maintaining focus positions within the material is crucial to the repeatability of laser-cut parameters and for producing consistent edge quality.
For example, when dealing with thick materials, it actually is necessary to create a larger burn pattern to create a wider channel, which is needed to support a larger volume of molten material that must be expelled during the cutting process. To create this enlarged burn pattern, you focus the beam either above or below the surface of the material depending on the assist gas. Consequently, focusing a small spot on the surface typically is a less successful approach for thicker material.
For thinner material, however, a small spot focused on the material's surface is much more effective than a larger one because less material is involved and, consequently, a broader channel is not required.
One very important factor to consider with laser cutting is the use of an assist gas, such as oxygen, nitrogen, or compressed air. Each gas has specific properties related to accelerating the burning process, evacuating the molten material, or both.
In laser cutting, assist gases support two specific reactions: exothermic or endothermic. Focusing rules vary with the type of reaction and gas used.

Focusing for Exothermic Reactions
Exothermic reactions are created by using a gas that offers accelerant properties, such as oxygen. During this type of reaction, the laser beam's intense energy vaporizes—or literally boils—the cut material as the oxygen vigorously reacts with the molten material in its liquid state. During high-pressure, oxygen-assisted cutting, the base material is brought to such an intensely high temperature that conversion of the material into a thermal vapor is very nearly complete.
Focusing rules for supporting exothermic reactions require focus positions to be above the surface for thick materials or just into the top surface for thinner materials.
When the focus is above the material, you typically are using a low pressure and low volume to help liquefy and then expel the molten material (approximately 6 to 8 pounds per square inch at 40 cubic feet per hour). Actually, very little of the material is vaporized because the small volume of oxygen is unable to support complete vaporization. When the focus is positioned just into the surface of the material, you typically are using a high pressure and high volume (approximately 60 PSI at 80 CFH). This is enough to support vigorous vaporization of the material.
That's why when you inspect most cutting tables where thinner material is cut predominantly, you see very little material accumulated on the table supports. In contrast, cutting tables used for processing thicker materials will have a much larger volume of material accumulated on their supports.
Focusing for Endothermic Reactions
Endothermic reactions, on the other hand, are created when you use a gas that has inert, or nonreactive, properties. Nitrogen and argon fall into this category.
During this type of reaction, the gas is supporting only the evacuation of the molten material through the cut channel. The endothermic process highly depends on the raw energy of the focused laser beam to bring the base metal quickly to a molten state and to create the proper cut channel. This allows the inert gas to expel the liquefied material through the cut channel, leaving a cleanly cut surface with no slag adherence.
Focusing rules for supporting endothermic reactions require focus positions to be at, or just below, the bottom of the material. Maintaining the focus below the material creates a slight V shape within the cut channel, allowing the high-pressure gas to compress the molten material through the cut channel at a high velocity and expelling it through the channel's base.
Endothermic reactions require high volume and high pressure to support rapid evacuation of the molten material. Typical volumes can start at 350 CFH for thin materials and reach more than 3,000 CFH for thicker materials. Pressures can begin at 140 PSI for thin materials and rise to more than 300 PSI for thicker ones.
Using compressed air as an assist gas actually produces both endothermic and exothermic reactions at the same time. However, because air volume is composed mostly of nitrogen (approximately 78 percent), it is primarily an endothermic reaction, with the small volume of oxygen (about 20 percent) creating a simultaneous but smaller exothermic reaction. This results in quicker melting of the base material because of oxygen's reactive properties. The balance of the air is principally inert in composition and adds only to the endothermic reaction produced by the nitrogen.
Compressed-air cutting has the best results when the focus position is maintained at the center of the material thickness.
Raw Beam Effects
Just as the intensity of the sun affects the ability of the magnifying glass to focus and create an effective spot size, so does the raw laser beam influence how well you can focus its energy and the size of the focused spot that results. Here's the general rule: The larger the raw beam diameter, the larger the resulting focal waist diameter, and the farther the focal point is projected from the lens.
Another way to change the spot size effectively is by using a lens with a different effective focal length (EFL). This creates not only a different spot size, but also a different depth of focus (DOF), as illustrated in Figure 3. Keep in mind that DOF is not just where the beam is smallest (focal waist), but also includes a range just before and after the smallest spot size.
As an example of changing the spot size and DOF, consider a CO2 laser beam with a wavelength of 10,600 nm, a 20-mm raw beam diameter, and an M2 of 2. If we pass this beam through a 3.75-inch (95.25-mm) lens, the diameter at the focal waist would be approximately 128 microns (0.128 mm). Now, if we substitute a 5-in. (127-mm) lens, using the same 20-mm raw beam, the diameter at the focal waist would be 170 microns (0.170 mm). Concurrently, a change in the depth of focus between the two lenses would occur. The 3.75-in. lens would have a DOF of approximately 1.2 mm, compared to a DOF of 2.16 mm for the 5-in. lens.
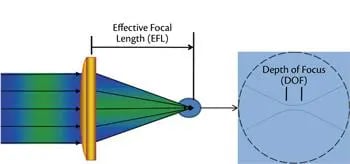
Yet another consideration that can alter the beam's focal point projection is a change in the wave front of the beam before it strikes the lens. The wave front of the raw beam can be described as either converging, parallel, or diverging. In the case of a converging wave front, the beam is essentially getting smaller as it travels. As this converging wave front strikes the lens, the resulting focus projection is shorter than that of a parallel wave front because of the smaller beam diameter projection at the top of the lens. Conversely, focusing a diverging wave front results in a longer focal point projection than that of a parallel wave front because of the larger beam diameter projected at the top surface of the lens .
Real-world Applications
It is important to control every aspect related to maintaining the proper focus point projections. You must ensure that the raw beam at the optical resonator is in good condition, and that the beam is being delivered properly to the lens. Using the proper focal length lens can change the rate at which the material is melted and the thickness that can be processed. A short focal length lens, such as a 3.75-in. EFL, is most effective up to a maximum thickness of 12 gauge or 0.104 in. A 5-in. lens is most effective up to a maximum thickness of 0.250 in. For thicker materials, use a 7.5-in. lens to a maximum of 1.25 in., and a 10-in. lens to a maximum of 1.312 in. to achieve the most effective cutting.
A genuine time-saving practice is to use an EFL that allows you to cover the majority of your daily production without having to change to a different lens. The use of a 7.5-in. lens will, for the most part, enable you to achieve all of the objectives related to maintaining the proper focus, from 16 ga. to 1 in. thicknesses, throughout the course of a day's production.
As mentioned before, choosing the assist gas has a lot to do with how your focal position will be determined within the material. Oxygen-assisted laser cutting (exothermic) will require focus positions to be just into the surface or above the surface of the material. Very little focal changes are required unless you are changing from high-pressure to low-pressure cutting because the focus is always on or near the surface of the material and is consequently unaffected by changes in material thickness. On the other hand, nitrogen-assisted laser cutting (endothermic) is very focal-dependent based on the material thickness to be processed because the focus is at or near the bottom of the material.
In either case, all of the basic focal points can be satisfied by utilizing a CNC, autofocusing device, such as an adaptive mirror.
An adaptive mirror works by changing the mirror's surface shape through the application of pressure to the back of the mirror. In its normal state, without applied pressure, the adaptive mirror's surface is concave. As pressure is applied to the mirror, the surface changes from concave, to flat, and then to convex. Changing the mirror's shape changes the wave front of the beam and consequently alters the size of the beam on the lens and where the focal position is projected within the material.
Another major benefit of autofocus is the ability to change the focal position dynamically during the piercing process, which allows for maximum energy input within the material thickness and reduces the overall pierce times.
Advancements in laser cutting technologies that serve to improve throughput and productivity continue to this day. What remains very critical, however, is delivery of the raw beam to the lens and maintaining the proper focal positions, based upon the application.
If the proper focal position and projection shapes are maintained within the material to be processed, the remainder of the requirements necessary to produce a consistent, high-quality cut are minimized. This saves setup time while maintaining consistent productivity and throughput.