Laser cutting machines for metal have revolutionized the metalworking industry by providing precise, efficient, and versatile cutting solutions. These machines use focused laser beams to slice through various types of metals with remarkable accuracy. However, one critical factor that influences the effectiveness and quality of the cut is the cutting thickness. Understanding the cutting thickness capabilities of a laser cutting machine for metal is essential for selecting the right equipment and optimizing its performance for different metal types and thicknesses. In this analysis, we will delve into the key factors that determine cutting thickness and explore the optimal settings for various metals.
Table of Contents
- Introduction
- Laser Metal Cutting and Fabrication Basics
- What Is Laser Cutting Machine For Metal
- Types of Laser Cutting Machine For Metal
- Advantages of Laser Cutting Over Other Cutting Methods
- Disadvantages of Laser Cutting Machine For Metal
- Cutting Thickness of Laser Cutting Machine For Metal
- Factors Affect the Cutting Quality
- How to Choose a Suitable Laser Cutting Machine for Metal
Introduction
Laser cutting machines for metal are sophisticated tools that utilize focused laser beams to cut through various types of metals with high precision and efficiency. These machines have become indispensable in the metalworking industry due to their ability to produce intricate shapes and designs with minimal waste and high accuracy. The relevance of laser cutting machines in metalworking cannot be overstated, as they significantly enhance productivity and quality in manufacturing processes.
A critical aspect of using these machines effectively is understanding the cutting thickness for different metals. The cutting thickness not only impacts the quality of the cut but also influences the machine’s efficiency and the overall outcome of the metalworking project. Therefore, a thorough analysis of cutting thickness is essential for optimizing laser cutting operations and achieving the desired results.
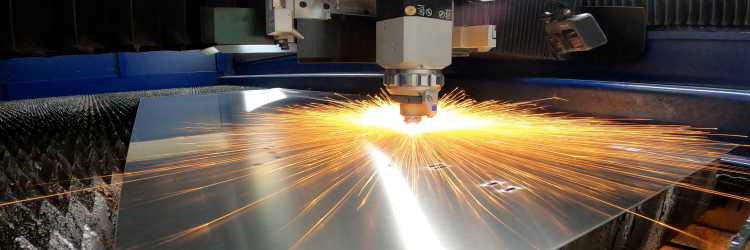
Laser Metal Cutting and Fabrication Basics
Metal cutting is an integral part of the metal fabrication process, which involves creating new metal structures by cutting, bending, and assembling metal into various shapes and formats. Industrial metal cutting machines are essential for precisely cutting thin sheets of metal to produce components for everyday items, such as electronics, automobiles, and medical equipment.
Laser cutting is used to create circuit boards, wire casings, car doors, hubcaps, and more. In the medical field, laser-cut metal is used to manufacture hospital beds, gurneys, surgical instruments, and orthopedic pins, rods, and plates.
Laser cutters are not limited to large, professional metal shops. Advances in technology have made modern metal laser cutters compact and budget-friendly, making them accessible to businesses of all sizes. Small businesses and hobbyists can now use laser metal cutters to create intricate signs and plaques, accurate model buildings, stencils, coasters, keychains, ornaments, and even jewelry.
Investing in an laser cutting machine for metal can significantly benefit your business. Eliminating the need to send metal out to a third party for cutting increases profitability and control over project timelines, reducing wait times that can slow production. Additionally, having an in-house laser cutter allows you to take on new types of projects and expand your business offerings, enhancing your long-term return on investment.
What Is Laser Cutting Machine For Metal
A laser cutting machine is an advanced tool that employs a high-powered laser beam to cut, engrave, or mark materials with exceptional precision. In the context of metalworking, these machines are specifically designed to handle a variety of metals, including steel, aluminum, brass, and copper. The laser beam is generated and focused through a series of optics and mirrors, directing intense energy onto the surface of the metal. This energy causes the metal to melt, burn, or vaporize, resulting in a clean, precise cut.
Types of Laser Cutting Machine For Metal
When it comes to cutting metal, several types of laser cutting machines are commonly used, each with its unique characteristics and advantages. The main types include CO2 lasers, fiber lasers, and Nd lasers.
CO2 laser
A CO2 laser is a type of gas laser that uses a gas mixture primarily consisting of carbon dioxide (CO2), nitrogen, and helium as the lasing medium. When an electric current is passed through this gas mixture, it produces a high-intensity laser beam in the infrared spectrum, typically at a wavelength of 10.6 micrometers. This laser beam is then focused and directed onto the material to be cut or engraved.
CO2 lasers are highly efficient, converting a significant portion of the input electrical energy into laser light, they can produce a high-quality beam, which allows for precise and clean cuts with smooth edges. CO2 lasers are capable of cutting a wide range of materials, including metals, plastics, wood, glass, paper, and textiles.
Fiber Lasers
A fiber laser is a type of laser where the active gain medium is an optical fiber doped with rare-earth elements such as ytterbium, erbium, or neodymium. The laser light is generated within the fiber and amplified as it travels through the optical fibers, which are flexible and can be coiled, allowing for a compact and efficient laser system. Fiber lasers are known for their high efficiency, excellent beam quality, and robustness.
Fiber lasers convert a high percentage of the input electrical energy into laser light, making them energy-efficient, they produce a high-quality, focused beam that allows for precise and clean cuts. The use of optical fibers allows for a more compact and robust design compared to other laser types. They can cut both metal and non-metal, such as mild steel, stainless steel, aluminum, and copper and brrass; as well as plastics and polymers.
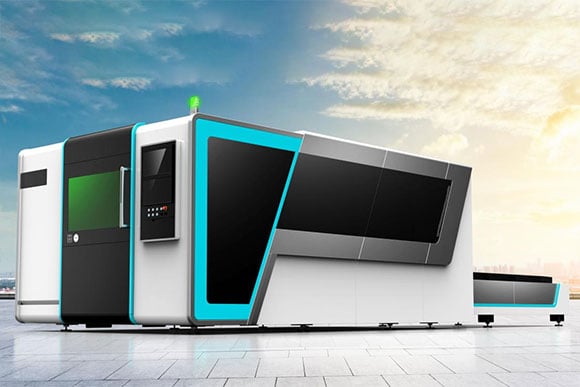
Nd lasers
Nd lasers, or neodymium-doped lasers, are solid-state lasers that use neodymium as the dopant in the gain medium. The most common types of Nd lasers include Nd(neodymium-doped yttrium aluminum garnet) and Nd(neodymium-doped yttrium orthovanadate). These lasers are known for their high power and ability to generate a laser beam in both continuous-wave (CW) and pulsed modes.
Nd lasers can produce high-power laser beams, making them suitable for cutting, welding, and drilling applications. They produce a high-quality beam with excellent focus, enabling precise and accurate cutting. Nd lasers can operate in both continuous and pulsed modes, providing flexibility for different applications, they have the ability to generate short, intense pulses allows Nd lasers to perform fine drilling and micro-machining tasks.
Nd Lasers can cut metal and non-metals include stainless steel, mild steel, ceramics, plastics and so on.
Disk Laser
A disk laser is a type of solid-state laser where the laser-active medium is a thin disk-shaped crystal, typically doped with ytterbium. The disk is mounted on a heat sink, which allows efficient cooling and prevents thermal distortion. This design enables high power output and excellent beam quality, making disk lasers highly effective for precision cutting and other industrial applications.
The thin disk shape allows for a very high beam quality, resulting in precise and clean cuts with minimal heat-affected zones. The disk’s design facilitates efficient cooling, allowing for continuous high-power operation without significant thermal effects. Disk lasers can generate high-power laser beams, making them suitable for cutting thick and hard materials.
Advantages of Laser Cutting Over Other Cutting Methods
Laser cutting offers significant advantages over traditional mechanical cutting methods, such as die punching or saw cutting, as well as other techniques like plasma cutting and waterjet cutting. These advantages largely stem from the precise nature of the laser beam and the high level of energy containment in the cutting process. Here’s why these properties provide substantial benefits over other methods.
Higher Accuracy and Smaller Kerf Sizes
Accuracy: The highly focused beam of a laser cutter only affects a small surface area, enabling extremely accurate and precise cuts. Laser cutters can achieve accuracy levels of ±0.1 mm, making them ideal for applications requiring high precision.
Kerf: The kerf, or the width of material removed during the cutting process, is significantly smaller with laser cutting. Laser cutters can produce kerf widths as narrow as 0.1mm to 1mm, depending on the machine and material. In comparison, waterjet cutting produces a kerf width of around 0.9mm, oxy-fuel cutting around 1.1mm, and plasma cutting about 3.8mm. Mechanical saws generally produce a kerf size of approximately 3.175mm, ten times that of a laser cutter.
Advantages of Smaller Kerf Size:
- Improved material utilization, reducing waste and cost.
- Less need for offset cutting, enhancing accuracy in critical applications.
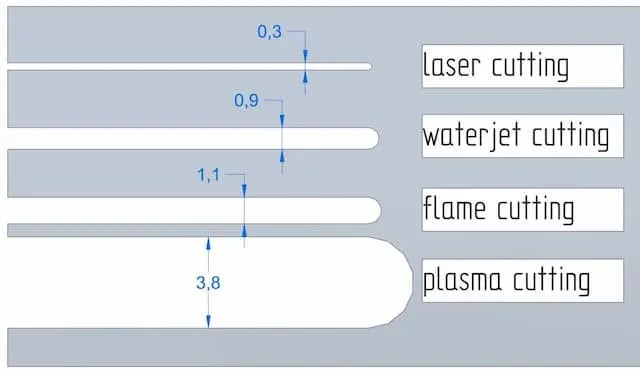
High Levels of Repeatability
Laser cutters can produce complex, precision parts consistently over large production runs due to their CNC control and advanced software optimization. Since laser cutting is a non-contact process, there is no wear or degradation of the cutting edge, ensuring uniform cutting action throughout the production run. This advantage is significant over mechanical methods like saw cutting, where the blade can deteriorate over time. Although waterjet and plasma cutting offer similar repeatability, laser cutting often surpasses them in precision.
Less Material Contamination in the Cut Area
Mechanical cutting methods often require cutting oils to reduce friction, which can be difficult to remove and may hinder subsequent processes like coating or finishing. Laser cutting generally does not require coolants or lubricants, eliminating this issue and ensuring cleaner cuts.
Limited Post-Cut Finishing Requirements
Laser cutting produces high-quality cut edges, often eliminating the need for secondary finishing processes. The clean cuts made by lasers have fewer surface imperfections such as burrs or excess material, reducing the need for deburring or additional finishing. This is a marked advantage over mechanical methods like saw cutting, shearing, or drilling, which typically leave surface imperfections that require further processing. This reduction in finishing steps can save both time and money.
Laser Cutting Offers More Flexibility
Laser cutting is highly versatile, capable of producing intricate and complex designs that might be impossible with other cutting methods. It can efficiently handle a wide range of materials, including metals, plastics, and wood, unlike plasma cutting, which is limited to metals. Laser cutting can often perform multiple cutting processes in one pass, further enhancing its flexibility.
Laser Cutting Offers the Best Sheet Utilization
The combination of smaller kerf widths, minimal mechanical distortion, and tighter tolerances allows for better sheet utilization. Laser cutting can use up to 94% or more of a sheet, reducing waste and lowering part costs compared to other methods.
Laser Cutting Provides Superior Speed
Laser cutters can achieve cutting speeds of up to 1200 inches (3050 cm) per minute, making them much faster than traditional methods like wire cutting or bandsaw cutting. For instance, bandsaw cutting takes about ten times longer than laser cutting, and wire cutting can take up to 100 times longer. Even compared to plasma and waterjet cutting, laser cutting generally offers superior speed, especially for thinner materials or when using high-wattage lasers.
Comparison of Cutting Technologies: Laser, Waterjet, Plasma, and Mechanical
FACTOR | LASER CUTTING | WATERJET CUTTING | PLASMA CUTTING | MECHANICAL CUTTING |
---|---|---|---|---|
Precision/Tolerances | ± 0.0127 mm | ± 0.0254 mm | ± 0.254 mm – ± 0.762 mm | Thicker, but depends on process |
Intricate Design Capabilities | Most Capable | Most Capable | Some not possible | Many not possible |
No Mechanical Distortion | Yes | Yes | No, especially with thin metal sheets | No |
No Thermal Distortion | No | Yes | No | No |
Material Costs (Less Waste) | Yes | Yes | More waste than with laser and waterjet cutting | High waste levels with many methods |
Tooling Costs | None | None | None | Sometimes |
Low – Medium Volume Production | X | X | X | Yes |
Composite/Multi-layer Material | Requires higher laser power | Capable | X | Yes |
Thick Materials | Not capable | Capable | Capable | Capable |
Range of Suitable Materials | Metals, plastic, wood, glass | Metal, glass, wood | Electrically conductive metals | Metals, plastic, wood, glass |
Disadvantages of Laser Cutting Machine For Metal
Hazardous Vapors and Fumes from Melting Materials
Laser cutting involves melting or vaporizing materials, which can produce hazardous vapors and fumes posing health risks to operators. Certain materials are unsuitable for laser cutting due to this reason. Materials that should not be fabricated with laser cutters include:
- Acrylonitrile butadiene styrene (ABS)
- Epoxy resins
- Polyvinyl chloride (PVC)
- Laminated fiberglass
- Polycarbonate (PC)
- Polystyrene and polypropylene foam
Additionally, there’s a risk of eye damage to operators during cutting and the production of sharp cut edges, which require precautions.
Limitation on Material Thickness
Laser cutters have limitations on maximum cutting depths compared to waterjet cutters, CO2 cutters, and many mechanical cutting methods.
- Maximum Thickness:
- Fiber lasers: Up to 20mm
- CO2 lasers: Up to 70mm
Using laser cutters beyond their designed thickness limitations can lead to issues like poor edge finishes and material loss due to melting.
Tolerances for Laser Cutting Thickness
While laser cutters excel within their accepted material thickness range, it’s essential to consider tolerances. For example, at Komaspec, laser cutting is performed with the following tolerances:
- Less than 1.0 mm: +/- 0.05 mm tolerance
- Between 1.0 mm and less than 2.0 mm: +/- 0.05 mm tolerance
- Between 2.0 mm and less than 5.0 mm: +/- 0.07 mm tolerance
- Greater than 5.0 mm and less than 20.0 mm: +/- 0.20 mm tolerance
MATERIAL THICKNESS | TOLERANCE |
---|---|
≤1.0 mm | ±0.05 mm |
1.0 mm to 2.0 mm | ±0.05 mm |
2.0 mm to 5.0 mm | ±0.07 mm |
5.0 mm to 20.0 mm | ±0.20 mm |
Laser Cutting Capabilities: Material Thickness and Tolerances
Material Hardening and Heat Affected Zone (HAZ)
During laser cutting, the high temperature of the laser beam can modify the structure of the material being cut, leading to a hardened zone known as the Heat Affected Zone (HAZ) when followed by rapid cooling. Research indicates that the microhardness in the hardening zone increases with higher laser power. While this isn’t typically problematic for thin or quickly cut parts due to minimal heat transfer, thicker and slow-cut parts can experience larger HAZ due to increased heat transfer.
The hardening of laser-cut edges can pose challenges in some applications. Parts requiring subsequent finishing processes like powder coating or painting may need additional steps after laser cutting, increasing turnaround time and processing costs.
Material Limitations
Laser cutting is versatile and applicable to a wide range of metallic and non-metallic materials, surpassing the capabilities of both waterjet and plasma cutting. However, there are limitations, especially concerning specific types of laser cutters and the use of assistive gases during cutting, which may impose further restrictions.
TYPE OF LASER / MATERIAL TO BE CUT | CO2 | CO2 NITROGEN ASSIST | CO2 O2 ASSIST | FIBER LASER |
---|---|---|---|---|
Carbon Steel | ✓ | ✓ | ✓ | |
Stainless Steel | ✓ | ✓ | ||
Copper | ✓ | ✓ | ✓ | |
Aluminium | ✓ | ✓ | ✓ | |
Titanium | ✓ | ✓ | ✓ | |
Plastic | ✓ | ✓ | ||
Glass | ✓ | |||
Paper | ✓ | |||
Wood | ✓ | |||
Stone | ✓ |
CO₂ vs. Fiber Laser Cutting: Material Comparison
Cutting Thickness of Laser Cutting Machine For Metal
Metal laser cutting machines are versatile tools capable of cutting various metal materials, including stainless steel, carbon steel, alloy steel, aluminum, silver, copper, titanium, and more. The cutting ability of a fiber laser cutting machine depends on factors such as machine quality, laser type, cutting environment, cutting speed, and the use of auxiliary gas. There’s no absolute standard for judging cutting thickness as it varies based on these factors.
When purchasing laser cutters, users should select the appropriate laser configuration based on their specific needs. Here’s an overview of the maximum cutting thickness for different power levels:
1. The maximum cutting thickness of different materials of 500W metal laser cutting machine: the maximum thickness of carbon steel is 6mm; The maximum thickness of stainless steel is 3mm; The maximum thickness of aluminum plate is 2mm; The maximum thickness of copper plate is 2mm;
2. The maximum thickness of different materials cut by 1000W metal laser cutting machine: the maximum thickness of carbon steel is 10mm; The maximum thickness of stainless steel is 5mm; The maximum thickness of aluminum plate is 3mm; The maximum thickness of copper plate is 3mm;
3. The maximum thickness of different materials cut by 2000W metal laser cutting machine: the maximum thickness of carbon steel is 16mm; The maximum thickness of stainless steel is 8mm; The maximum thickness of aluminum plate is 5mm; The maximum thickness of copper plate is 5mm;
4. The maximum thickness of different materials cut by 3000W metal laser cutting machine: the maximum thickness of carbon steel is 20mm; The maximum thickness of stainless steel is 10mm; The maximum thickness of aluminum plate is 8mm; The maximum thickness of copper plate is 8mm;
5. 4000W laser cutting stainless steel is 16mm at most, but the quality of the cutting surface above 12mm is not guaranteed, and the cutting surface below 12mm is definitely bright. The cutting capacity of 6000W will be better, but the price is also higher.
Generally, 1000W fiber laser cutting machine can cut about 10mm carbon steel plate, and stainless steel plate is slightly difficult to cut. If the cutting thickness is to be increased, it is necessary to sacrifice the edge effect and speed. For different metal materials, the cutting thickness of different power metal laser cutting machines has a great relationship with the cutting materials. Due to many external factors, the actual cutting ability is also related to the quality of laser cutting machine, cutting environment, auxiliary gas, cutting speed and other factors.
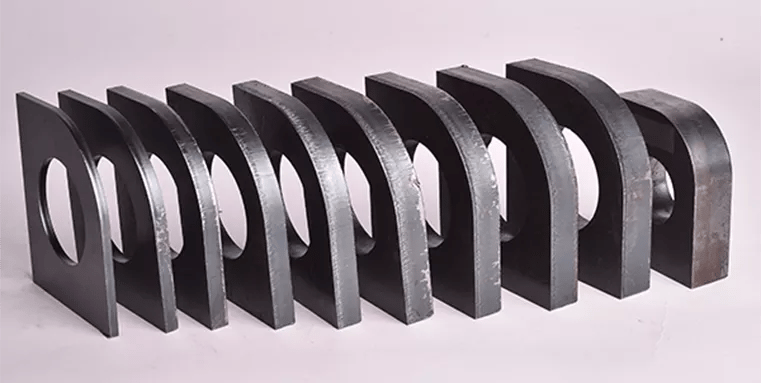
How To Choose Proper Power For Laser Cutting
When choosing a metal laser cutting machine, customers should consider not only the typical thickness of plates they will cut but also the proportion of maximum thickness plates, ensuring it’s more than 10%. This is crucial because the power requirements vary based on plate thickness. For instance:
If the plate thickness ranges from 12mm to 16mm, a 6000 watt laser cutting machine is necessary to meet the cutting requirements. For plate thickness between 4mm to 8mm, a 2000W or 3000W laser cutting machine is generally recommended. However, to account for power attenuation, it’s safer to choose a 3000W laser cutter.
It’s important to note that the price difference between 3000W and 6000W laser cutting machines is significant. Without considering cutting needs properly, investing in high-power machines for small proportion thicknesses can greatly reduce cost recovery speed.
Quality of the Cut Is equal to the Maximum Thickness Cut?
If there’s a requirement for a smooth, bright surface cut, the cutting capacity decreases by 60%. For example:
Cutting on a 500W laser cutting machine ensures smooth material for 3mm thick plates, but it may not be as smooth for 4mm thick plates. A 3000W laser cutting machine can achieve quality cutting for plates up to 12mm thick, ensuring continuous and stable cutting.
Hence, the quality cutting thickness differs from the maximum cutting thickness. Insufficient power may result in holes or incomplete cuts. Therefore, customers must choose laser cutting machines according to their specific needs.
Factors Affect the Cutting Quality
Cutting Speed
For a given laser power density and material, cutting speed conforms to an empirical formula. Increasing power density improves cutting speed. Factors affecting cutting speed include increasing power (within a certain range), improving beam mode, reducing the size of the focus spot, cutting materials with low initial evaporation energy or low density, and cutting thin materials. Cutting speed adjustment is wider for thin metals compared to thick ones. Too slow cutting speed may result in rough cut surfaces due to ablation.
Focus Position Adjustment
The selection of lens focal length is crucial as it affects the spot size and power density. Short focal length lenses are suitable for high-speed cutting of thin materials, while long focal length lenses are better for thick materials. Proper focus position ensures stable cutting quality. Lens heating may require frequent focus position adjustments.
Auxiliary Gas Pressure
Auxiliary gas type and pressure are vital. Gas is used to blow away slag and protect the lens. For metal cutting, active gas like O2 increases cutting speed. Factors include high gas pressure for preventing slag sticking during high-speed cutting of thin materials, reduced gas pressure for preventing frosting on plastic cutting edges, and oxygen purity significantly impacting cutting quality.
Reflectivity of Material Surface
Material surface reflectivity affects absorption of laser beam. Non-metallic materials absorb well, while metals like gold, silver, copper, and aluminum have poor absorption. Factors include metal materials requiring sufficient initial power for penetration, surface state, oxide layer affecting absorption, and absorbance affecting initial heating.
Influence of Cutting Torch and Nozzle
Proper design and maintenance of cutting torch and nozzle are crucial for good cutting quality. Issues include nozzle pollution or damage affecting cutting performance, nozzle misalignment affecting cutting quality and size, and consideration of nozzle diameter and distance from the workpiece surface.
Influence of External Optical System
The external optical path system must accurately transmit the laser beam to the workpiece. Factors include regular checking and adjustment of optical elements, pollution or overheating of lenses affecting beam energy transmission and focus, and any changes in optical elements affecting cutting quality and performance.
In actual operation, attention should be paid to the above six factors that affect the cutting effect of a laser cutting machine.
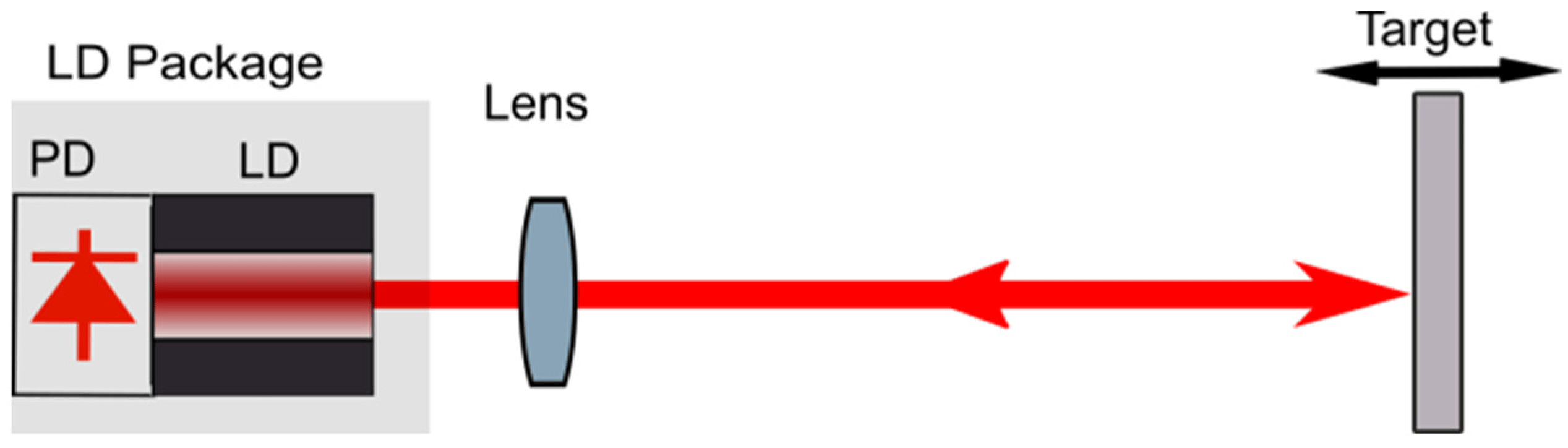
How to Choose a Suitable Laser Cutting Machine for Metal
As a manufacturer considering a laser engraver, several key factors should be considered to make an informed decision. The first question to ask is what materials you will be working with, as this will help determine whether you need a CO2 or fiber optic laser system.
Next, you need to determine the maximum material size that will fit inside the machine, which will help narrow down the system model. Space constraints in your facility will also influence this decision. After selecting the laser source and model size, the next critical factor is power.
Determining Power Requirements
To determine the power requirements of your laser machine, consider the maximum thickness of the material that needs to be cut and the daily production volume. These factors are crucial in selecting the right laser machine for your needs.
General Factors to Consider
- Power: The power of the laser machine is crucial as it determines the thickness of the materials it can cut. For thick materials, a high-power laser machine is necessary. For thin materials, a lower power output may suffice.
- Price: Laser machines can be expensive, ranging from a few thousand to tens of thousands of dollars. Establish a budget before shopping and compare prices by browsing online and talking to different dealers.
- Quality: Ensure the laser machine is made from high-quality materials and has a good reputation. Research different brands and read reviews to find the best options. Seek recommendations from industry peers.
- Bed Size: The bed size determines the maximum size of the material you can cut. If you need to cut large pieces, choose a machine with a large bed size. For smaller pieces, a smaller bed size will be adequate.
- Cooling and Ventilation: Laser machines generate significant heat, so proper cooling and ventilation are essential. The machine should have a good cooling system to prevent overheating and adequate ventilation to allow heat to escape.
- Software Requirements: Laser machines come with their own software and should be able to connect to your computer for file transfers. Ensure the software is compatible with your design programs, like CAD.
- Floor Space: Laser machines vary in size, from a few feet to several yards. Measure the area where you plan to place the machine to ensure you have sufficient space.
- Accessories: Laser machines often come with various accessories, such as chucks, jigs, and additional software. Research what accessories are included and which ones you might need to purchase separately.
- Maintenance: Regular maintenance is required for laser machines. Familiarize yourself with the maintenance requirements, including cleaning, lubrication, and periodic laser beam alignment.
- Specifications of Laser: Ensure the machine can cut the specific types of materials you need. For example, if you need to cut metal, verify that the machine is designed for that purpose.
- Laser Resonator: The quality of the laser beam depends on the quality of the laser resonator. Choose a machine with a high-quality laser resonator to ensure the best laser beam performance.
- Cutting Head: Research the type of cutting head included with the machine. Some machines have fixed cutting heads, while others have movable cutting heads. For cutting large pieces, a movable cutting head is preferable.
How Krrass Empowers Your Cutting Process
Krrass, a leading manufacturer of industrial laser cutting machines, is dedicated to revolutionizing your cutting operations. Here’s how Krrass can empower your manufacturing process:
Cutting-Edge Technology
Krrass machines utilize state-of-the-art laser technology to ensure unparalleled precision and efficiency. Whether you need to cut thin sheets or thicker materials, Krrass offers the versatility required to meet your specific cutting needs.
High Power and Precision
Krrass laser cutting machines feature high-power laser options that can easily cut through various material thicknesses while maintaining exceptional precision. Advanced focusing systems and high-quality laser resonators ensure each cut is accurate and clean, reducing the need for secondary processing.
Minimal Material Waste
One of the key advantages of Krrass laser cutters is their ability to produce a narrow kerf. This precision minimizes material waste, leading to more efficient use of resources and cost savings. The small and precise laser beam ensures clean cuts with minimal material loss.
User-Friendly Software
Krrass machines are equipped with intuitive software that simplifies operation and integrates seamlessly with your existing design programs. This compatibility ensures a smooth workflow from design to production, allowing for easy upload and execution of cutting plans.
Robust and Reliable
Built with high-quality materials and components, Krrass machines are designed for durability and long-term reliability. Their robust construction minimizes downtime and maintenance costs, ensuring continuous operation and high productivity.
Versatility in Applications
Krrass laser cutters are highly versatile and suitable for a wide range of applications. Whether you are producing automotive parts, medical equipment, or intricate custom designs, these machines can handle it all with ease. The ability to execute complex cuts and contours makes them ideal for various industries.
Cost Efficiency
Investing in a Krrass laser cutting machine can lead to significant cost savings over time. By bringing cutting processes in-house, you eliminate the need for third-party services, reduce production lead times, and gain greater control over your projects. This boost in efficiency and flexibility can enhance your profitability and competitiveness.
Enhanced Safety Features
Krrass prioritizes safety in the design of their laser cutters. Advanced cooling systems, proper ventilation, and protective enclosures help ensure a safe working environment. These safety measures also contribute to the longevity and reliable performance of the machines.
Comprehensive Support and Training
Krrass offers comprehensive support and training for their laser cutting machines. From installation and setup to ongoing maintenance and troubleshooting, Krrass provides the resources and expertise needed to ensure your operations run smoothly.
In summary, Krrass empowers your cutting process by delivering high-quality, reliable, and versatile laser cutting solutions. By choosing Krrass, you are investing in advanced technology that enhances precision, efficiency, and cost-effectiveness, significantly improving your manufacturing capabilities. If you have any need, pls call us without any hesitation, our team will give you the best support.
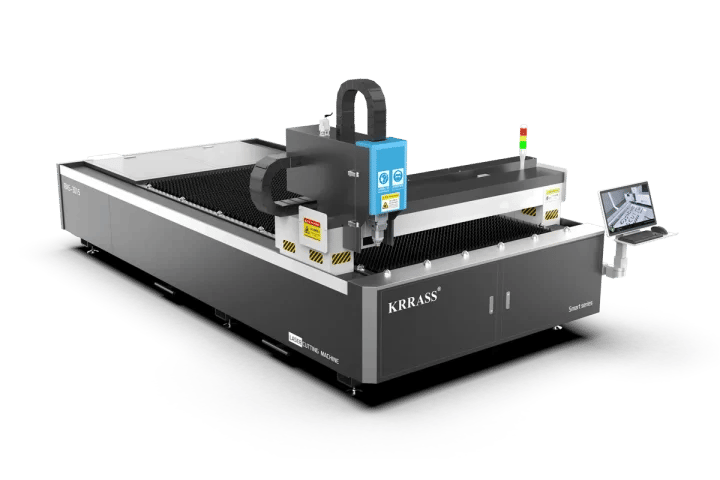