Laser cutting machines are indispensable tools in modern manufacturing, widely used in industries like metal fabrication, electronics, and automotive production. However, while benefiting from the high efficiency of laser cutting technology, ensuring the safety of operators is equally critical. Adhering to proper laser cutting machine safety guidelines not only helps prevent accidents but also extends the lifespan of the equipment and improves operational efficiency. In this article, we will explore the best safety practices operators should follow when working with laser cutting machines.
Brief overview of laser cutting technology
laser cutting machine is a device which utilizes a high-energy laser beam to cut and process the material. Its working principle is to generate a high-intensity laser beam via the laser.
After being focused by the optical system, the laser beam will be irradiated onto the material surface, making the material melt, vaporize, or reach the ignition point. Meanwhile, the high-pressure gas will blow away the molten material.
The laser cutting machine features high precision, high speed, narrow gap, small heated zone, high flexibility, etc. This makes it widely used in many spheres like metal fabrication, electronics manufacturing, the automotive industry, and aerospace.
The laser cutting machine is mainly divided into three types, namely CO2, fiber, and YAG. The CO2 laser cutting machine is suitable for cutting non-metal materials such as wood, plastics, and acrylic.
Fiber laser fits for metal cutting owing to its advantages of high efficiency and low maintenance cost. YAG laser cutting machine is suitable for marking and fine processing.
Importance of laser cutting machine safety
Laser-cutting machine safety plays a significant role in metal fabrication due to its high energy level and potential risks. If treated improperly, it will lead to severe safety accidents and health hazards.
Today, we will mainly talk about the common hazards and their corresponding measurements, emergency procedures as well as safety features of the laser cutting machine. Firstly, let’s recognize the safety devices on the machine.
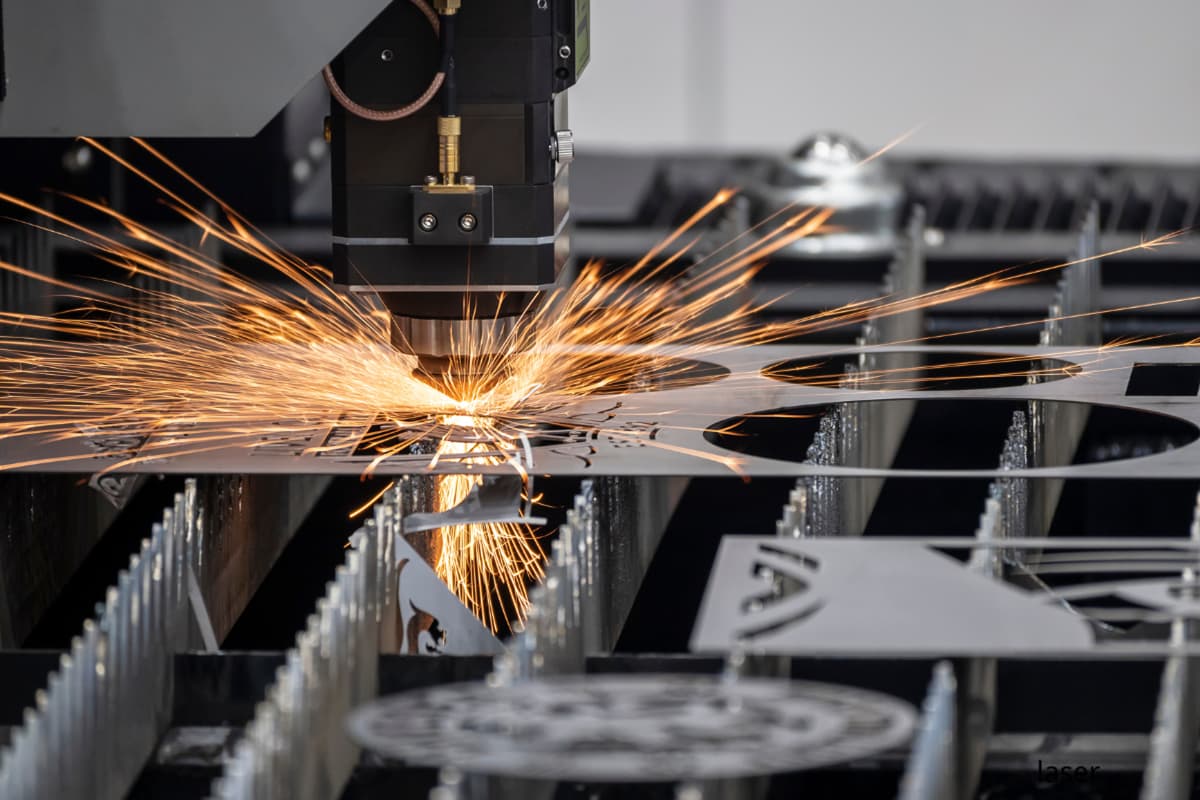
Safety Features of Laser Cutting Machines
To minimize accidents and risks, modern laser cutting machines are designed with several built-in safety features. These devices and systems work together to ensure the safety of operators and reduce the chances of equipment-related incidents. Below are the key safety devices and features commonly found in laser cutting machines:
Interlocking Device
Laser cutting machines are equipped with interlocking devices that automatically stop the machine under specific conditions to protect the operator. These systems can prevent the machine from operating if safety conditions are not met, acting as a safeguard in potentially dangerous situations.
Emergency Stop Button
An emergency stop button is a crucial feature in every laser cutting machine. It is typically located in a highly visible and accessible position, allowing the operator to quickly press it in case of an emergency. Once activated, the machine immediately halts its operation, and the laser and power supply are cut off. This feature plays a vital role in preventing accidents from escalating, ensuring the safety of the operator and minimizing potential damage.
Protective Cover and Shield
Modern laser cutting machines are designed with protective covers and shields to guard against laser radiation. These covers not only protect operators from the harmful effects of laser exposure but also shield them from splashes of molten metal or smoke that could cause injury. Many machines use transparent materials for these protective covers, enabling operators to clearly observe the cutting process while remaining safely protected.
Safety Warning Labels
Eye-catching safety warning labels are strategically placed on laser cutting machines to alert operators to potentially hazardous areas, such as zones where laser emissions or high temperatures are present. These labels serve as visual reminders to exercise caution in high-risk areas, contributing to overall workplace safety.
Cooling System
The cooling system in a laser cutting machine is essential not only for maintaining normal equipment operation but also for preventing overheating or malfunctions. By keeping the laser and other components within a safe temperature range, the cooling system reduces the risk of heat-related issues, ensuring the machine operates efficiently and safely.
Smoke and Dust Extraction System
During the cutting process, laser machines generate smoke and harmful gases. To protect the operator’s health and prevent environmental pollution, laser cutting machines are equipped with smoke and dust extraction systems. These systems effectively remove the hazardous byproducts of cutting, ensuring a cleaner and safer work environment.
Operator Training and Protective Equipment
Finally, proper operator training and the use of protective equipment are critical for ensuring safety. Operators should receive thorough training on the safe use of laser cutting machines and wear appropriate protective gear, such as goggles and gloves, to minimize the risk of injury.
Through a combination of these built-in safety features and proper operator protocols, laser cutting machines can be used safely and efficiently in a wide range of industrial settings.
Common Hazards and Protective Measures in Laser Cutting Machines
Laser cutting machines are highly efficient and widely used across various industries, but they also pose certain hazards if not handled properly. Understanding the common risks and implementing protective measures can greatly reduce the likelihood of accidents and ensure a safe working environment. Below are the most common hazards associated with laser cutting machines, along with protective measures to mitigate these risks:
Common Hazards:
- Laser Radiation Exposure
- Risk: The laser beam used in cutting processes can cause serious damage to the skin and eyes. Even indirect exposure to reflected laser light can lead to severe burns or permanent eye injury.
- Protective Measure: Operators should wear proper protective goggles designed for laser safety and ensure that all exposed skin is covered. Machines should be equipped with protective covers and shields to contain the laser beam within the cutting area.
- Fire Hazards
- Risk: The high-energy laser beam can easily ignite flammable materials near the cutting area. Inadequate ventilation may also increase the risk of fire from smoke and gas buildup.
- Protective Measure: Maintain a clean work area free of flammable objects. Ensure proper ventilation and use a smoke extraction system. Operators should also have fire extinguishers readily available and conduct regular fire safety training.
- Harmful Smoke and Gases
- Risk: During cutting, particularly with materials like plastics or coated metals, harmful fumes and gases can be released. These can irritate the respiratory system and lead to long-term health issues.
- Protective Measure: Install a smoke and dust extraction system to remove harmful byproducts from the air. Operators should wear appropriate respiratory protection when working with materials that emit hazardous fumes.
- Electrical Hazards
- Risk: Laser cutting machines are powered by high-voltage electrical systems, which can pose an electrocution risk during maintenance or operation.
- Protective Measure: Regularly inspect and maintain electrical components, ensuring that only trained personnel handle electrical repairs. Operators should also turn off and unplug the machine before performing any maintenance.
- Mechanical Injuries
- Risk: Moving parts such as cutting heads and moving worktables can cause physical injuries, including crush injuries, if operators get too close.
- Protective Measure: Operators should maintain a safe distance from moving parts and never reach into the machine during operation. Safety guards and interlocking devices should be in place to automatically stop the machine if an operator enters a hazardous area.
- Noise Exposure
- Risk: Laser cutting machines can generate high levels of noise during operation, which can lead to hearing damage over time.
- Protective Measure: Operators should wear ear protection, such as earplugs or earmuffs, especially during prolonged exposure to the machine. Regular noise level assessments should be conducted in the workspace to ensure compliance with safety standards.
General Protective Measures:
- Training and Certification
- Operators must undergo proper training and obtain certification to handle laser cutting machines. This ensures they are familiar with machine operation, safety protocols, and emergency procedures.
- Regular Maintenance
- Scheduled maintenance and safety checks are crucial to identifying potential hazards, such as malfunctioning safety devices or worn-out components, before they become dangerous.
- Emergency Stop Systems
- Emergency stop buttons and interlocking devices should always be functional and regularly tested. Operators must be familiar with their locations and use them whenever necessary.
- Personal Protective Equipment (PPE)
- In addition to goggles and gloves, operators should wear protective clothing, such as flame-resistant materials, to minimize exposure to potential burns and laser radiation.
- Safety Signage
- Clearly visible warning labels and signs should be posted around the machine, indicating high-risk areas like laser emission zones, hot surfaces, or areas where electrical hazards exist.
By addressing these common hazards and following protective measures, operators can create a safer environment and reduce the risk of injury or accidents while working with laser cutting machines.
Compliance with Safety Standards
It is of vital importance for us to know the safety standards during the use of laser cutting machines. This will not only protect the operators’ safety, but also ensure the equipment operation efficiency. Here are the main safety standards:
OSHA
OSHA is an Occupational Safety and Health Administration (OSHA) in America. It aims to protect the workers’ safety and health. As for laser cutting machines, the OSHA relevant standards include:
29 CFR 1910.97:this includes the standards for non-ionizing radiation, which covers the safety requirements for laser radiation.
29 CFR 1910.212: this includes general requirements for machines and machinery.
ANSI
ANSI formulates a series of criteria for laser safety, namely:
ANSI Z136.1: the laser safety standards offer a safety using guideline for the laser cutting machine, which covers the classification of laser radiation, control measures and operational requirements.
ANSI Z136.9:this is especially designed for laser uses in industrial and manufacturing environment, which offers detailed safety operation standards.
IEC
IEC 60825-1 is a laser product safety standard, which is widely adopted by the international. This standard regulates the classification of laser equipment and label requirements as well as safety protective measurements.
Emergency Procedures
Steps to take in case of an emergency
Keep calm: it is very important to keep calm when an emergency occurs. Staying lucid can help you judge the condition and take appropriate action.
Access the condition: quickly access the properties and severity of the emergency. This includes the danger source, amount of people being affected, and the potential results.
Warning: inform the emergency response team on the spot immediately or dial the emergency services hotline. Remember to offer clear and accurate data, namely types of emergency situation, positions and people being affected.
Evacuation: evacuate to a safe area quickly according to the scheduled evacuation route. Make sure that people who need help like injury or inconvenient to move get the help.
Emergency solutions: take proper emergent measures according to the types of emergency situations. For example, use the fire extinguisher to put out the fire, and close the gas valve to prevent the leaking and spreading.
Waiting for professional help: ensure all the staff are in the safety zone, and wait for further instructions before the professional emergency response team arrives.
First aid and emergency response plans
First aid training: all the workers should accept basic first aid training, including CPR, bleeding control, burn treatment, and fracture management. Training and drills regularly to ensure that all the staff master the necessary first aid skills.
First aid equipment: make sure that the working area is equipped with adequate first aid equipment, such as a first aid kit, and AED. This equipment should be placed in a position that is easy to access, and needs to be scheduled checked, and maintained.
Emergency response team: establish a specialized emergency response team, which is responsible for coordinating and exerting the emergent measurements immediately. The team members should accept professional training, and be familiar with the various emergent programs and the use of equipment.
Emergency communications: establish a reliable emergency communications system to quickly transmit information in an emergency. This can include internal broadcast systems, emergency phone lines, intercoms, etc.
Emergency drills: conduct emergency drills regularly to simulate various emergency situations and test and improve emergency response plans. Drills should include all employees, and the results of the drills should be recorded and analyzed to identify and resolve potential problems.
Conclusion
In this article, we examined the safety features of laser cutting machines, including automated protection systems, emergency stop buttons, and fume extraction devices, which collectively enhance operator safety. Despite these advanced safety measures, hazards such as laser radiation, fire risks, and mechanical injuries remain prevalent.
To ensure workplace safety and maintain productivity, it is essential to understand and adhere to strict safety standards and operational procedures.
Elevate your operations with top-tier laser cutting machines from KRRASS. With over 20 years of experience in manufacturing state-of-the-art laser cutting equipment, KRRASS is dedicated to providing the most reliable and advanced solutions available.
Explore our laser cutting machine products to learn more about how KRRASS can help you improve efficiency and safety in your workplace.