The laser source is the heart of any laser cutting machine, determining its efficiency, precision, and overall performance. It generates the focused light beam used to cut through various materials, making it a critical component in the manufacturing process. Among the numerous laser sources available in the market, Max Laser stands out for its exceptional quality and affordability. Known for its innovative technology and robust construction, Max Laser provides a reliable solution for businesses seeking high performance without breaking the bank. Understanding the Max laser cut price is essential, as it offers a competitive edge in terms of cost-effectiveness while maintaining superior cutting capabilities. In this guide, we explore the benefits of using Max Laser as your laser source, examining the Max laser cut price and its impressive price-to-performance ratio compared to other leading brands.
Table of Contents
Introduction
Importance of the Laser Source in a Laser Cutting Machine
The laser source is the heart of any laser cutting machine, playing a crucial role in determining its efficiency, precision, and overall performance. It generates the focused light beam that cuts through various materials, making it a critical component in the manufacturing process. The quality and capabilities of the laser source directly impact the speed, accuracy, and quality of the cuts, making it essential for businesses to choose the right laser source to meet their specific needs.
Overview of Max Laser and Its Significance
Among the numerous laser sources available in the market, Max Laser stands out for its exceptional quality and affordability. Known for its innovative technology and robust construction, Max Laser provides a reliable solution for businesses seeking high performance without breaking the bank. The Max laser cut price is a key factor in its popularity, offering a competitive edge in terms of cost-effectiveness while maintaining superior cutting capabilities. Max Laser's reputation for delivering consistent and high-quality results has made it a preferred choice for various industrial applications.
This guide aims to provide a comprehensive exploration of the Max laser cut price and its performance. By examining historical pricing trends, performance metrics, and the price-to-performance ratio, we will help you understand the value proposition offered by Max Laser. Additionally, we will compare Max Laser to other popular brands, highlighting its unique selling points and benefits. Whether you are considering purchasing a Max Laser or simply want to learn more about its capabilities, this guide will offer valuable insights to inform your decision-making process.
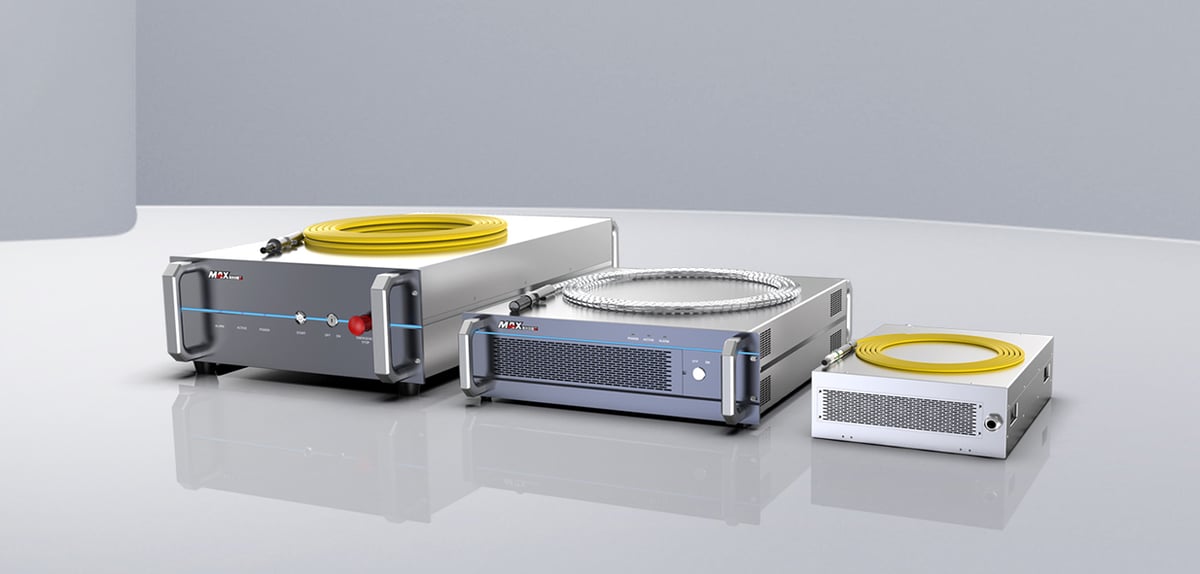
Where Max Laser Can be Applied
Max Photonics lasers are versatile and find applications across various industries due to their advanced technology and reliability. Here are some common industries where Max Photonics lasers are applied:
Manufacturing and Fabrication: Used for cutting, welding, and marking metals such as steel, aluminum, and titanium in industries like automotive, aerospace, and shipbuilding.
Electronics: Precision cutting and drilling of circuit boards and semiconductor materials.
Medical Devices: Laser welding of medical components and devices, as well as laser marking for product identification and traceability.
Consumer Electronics: Laser cutting and engraving for smartphone casings, tablets, and other electronic devices.
Jewelry and Watchmaking: High-precision cutting and engraving of precious metals and gemstones.
Packaging: Laser cutting and perforation of packaging materials such as plastics and foils.
Textiles and Apparel: Laser cutting and engraving for textile patterns and branding on apparel.
Automotive Industry: Laser welding of automotive components, cutting of sheet metal for car bodies, and marking for part identification.
Understanding the Powerhouse: How Fiber Lasers Work
Fiber lasers represent a significant advancement in laser technology, leveraging a unique method to generate and amplify laser beams through an optical fiber doped with rare-earth elements like ytterbium. This innovative approach enhances efficiency, precision, and reliability in laser cutting and other applications.
Energy Pumping:
Energy pumping begins with diode lasers, which serve as pump sources injecting energy into the doped optical fiber. This process excites the rare-earth ions within the fiber, elevating them to higher energy states.
Photon Generation:
As the excited ions return to their lower energy states, they emit photons. These photons are the fundamental units of the laser beam, characterized by their coherence and intensity.
Amplification:
Within the doped fiber, the emitted photons undergo a process of stimulated emission, where each photon stimulates the emission of more photons. This cascade effect amplifies the light exponentially, resulting in a highly concentrated laser beam.
Beam Delivery:
The amplified laser beam exits the optical fiber through a collimator lens. This lens ensures the beam remains parallel and focused, ready for precise cutting or engraving tasks. The efficiency and power of fiber lasers make them ideal for a wide range of industrial applications, from metal processing to telecommunications, showcasing their versatility and effectiveness in modern manufacturing.
Laser Source: More Than Just a Light Bulb
Stability: Ensuring Consistent Performance
Stability in laser sources is essential for maintaining consistent cutting quality and operational efficiency in industrial settings. It encompasses two critical aspects: power stability and beam pointing stability. Reliable power output ensures uniform cutting depth and edge quality, while precise beam alignment guarantees accurate geometries and tight tolerances during the cutting process.
Stable laser sources offer significant advantages in manufacturing. They ensure consistent performance by minimizing power fluctuations and beam alignment errors, thereby reducing scrap and enhancing product consistency. Additionally, stable sources support operational efficiency by enabling uninterrupted production runs, maximizing throughput and overall productivity.
Manufacturers employ advanced technologies such as sophisticated control systems to regulate power output and beam direction in real-time. These systems adapt to varying operational conditions, ensuring stable performance throughout production cycles. Rigorous quality assurance practices, including regular maintenance and calibration, further enhance stability over the laser source's lifespan, ensuring sustained reliability and operational effectiveness.
Wavelength: Precision in Material Interaction
The wavelength of a laser beam, although invisible to the naked eye, plays a critical role in how it interacts with materials. Fiber lasers, which commonly emit light at approximately 1064 nanometers in the near-infrared spectrum, are particularly advantageous for cutting metallic materials. This wavelength is chosen because of its high absorption rate in metals, allowing the laser to efficiently convert energy into heat during the cutting process.
This high absorption rate translates directly into efficient cutting operations. More of the laser's energy is absorbed by the metal, resulting in faster cutting speeds and cleaner edges. Whether cutting through steel, aluminum, copper, or brass, the 1064nm wavelength exhibits versatile performance across a wide range of metals. This versatility is crucial in industrial applications where diverse material types are processed, ensuring consistent and high-quality cutting results.
Power: The Driving Force
The power output of a laser source, typically measured in kilowatts (kW), plays a crucial role in determining the cutting speed and thickness capacity of a laser cutting machine. Higher power lasers are capable of cutting through thicker materials at faster rates due to their increased energy output and intensity.
Selecting the appropriate laser power depends largely on the specific requirements of your application.
For Thin Sheet Cutting, where precision and speed are paramount, lower power lasers (around 1-2 kW) can often deliver optimal results. These lasers are efficient for cutting thin sheets of metal with minimal heat affected zones, making them suitable for applications such as electronics or automotive components.
Thick Plate Cutting, on the other hand, requires higher power lasers (4 kW and above) to effectively penetrate and cut through thicker materials. These lasers provide the necessary energy to maintain cutting speeds and ensure clean edges on materials like stainless steel or aluminum, commonly used in construction and heavy industry sectors.
Choosing the right laser power involves balancing the cutting requirements with energy efficiency and operational costs, ensuring optimal performance tailored to specific manufacturing needs.
Beam Quality: The Mark of Precision
Beam quality in laser cutting refers to how well the laser beam can be focused and how its intensity is distributed across the cutting surface. A high-quality beam is characterized by its ability to focus down to a very small spot size, which results in a narrow kerf width—the width of the cut itself. This capability is crucial for achieving precise cuts with intricate geometries and sharp corners.
Another hallmark of a high-quality beam is its Gaussian intensity distribution. In an ideal scenario, the laser beam has a Gaussian profile where the majority of the energy is concentrated at the center of the beam, gradually tapering off towards the edges. This distribution ensures that the laser energy is evenly applied across the cutting surface, minimizing heat buildup and reducing the likelihood of material distortion.
Beam quality is pivotal for several reasons:
Precision Cutting: A high-quality beam enables laser cutters to achieve intricate designs with tight tolerances. By focusing the laser energy precisely, operators can create complex shapes and patterns without compromising accuracy.
Edge Quality: The focused, clean beam produced by a high-quality laser results in smooth, aesthetically pleasing cut edges. This is particularly important in applications where the finished appearance of the cut is critical, such as in architectural components or decorative metalwork.
In summary, beam quality is fundamental to the performance and capabilities of laser cutting machines. It directly influences the precision of cuts, the quality of finished edges, and the overall efficiency of manufacturing processes that rely on laser technology.
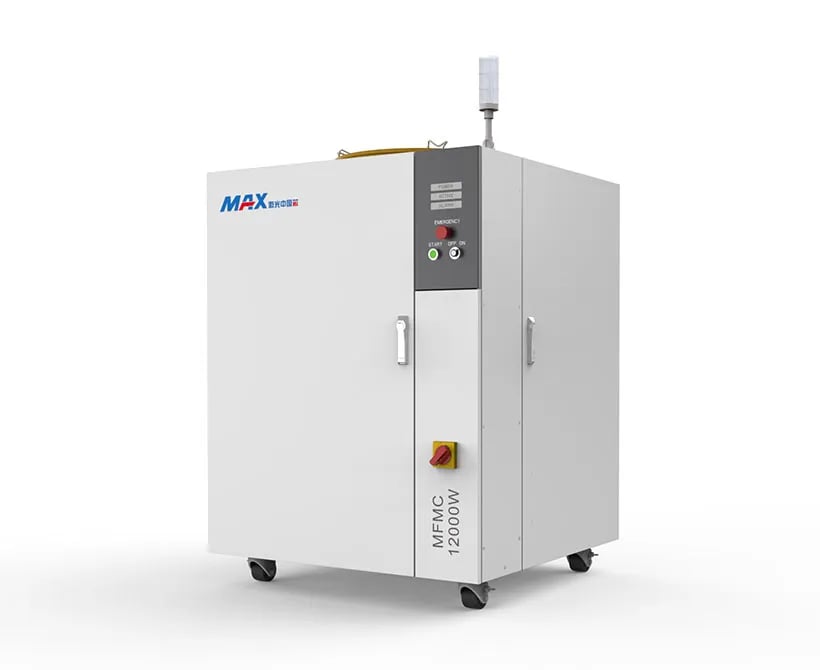
Beyond Basics: Exploring Max Laser Cut Features
Pulse shaping in laser cutting technology plays a crucial role in optimizing cutting processes by allowing operators to finely adjust the temporal profile of the laser pulse. This capability enhances control over how laser power is delivered to the workpiece, offering significant benefits across various applications.
Pulse Shaping: Tailoring the Beam for Perfection
1. Fine-Tuning for Material Specificity
One of the primary advantages of pulse shaping lies in its ability to tailor laser parameters to specific materials and cutting tasks. By adjusting parameters such as pulse duration, peak power, and pulse frequency, operators can optimize energy delivery for different material types. For instance, delicate materials may benefit from shorter, more frequent pulses to minimize thermal impact and achieve finer cuts. In contrast, thicker materials might require longer pulses with higher peak powers to ensure efficient material removal without compromising cut quality.
2. Advantages in Cutting Performance
Pulse shaping contributes to enhanced cutting performance in several ways:
- Heat Management: Precisely controlling the energy delivered to the workpiece helps in managing heat input more effectively. This reduces the risk of thermal distortion and minimizes heat-affected zones, preserving material integrity and dimensional accuracy.
- Edge Quality: Optimized pulse shapes contribute to smoother cut edges by reducing burrs and eliminating rough surfaces. This is particularly beneficial for applications requiring high surface finish and dimensional precision.
- Versatility: The flexibility offered by pulse shaping extends the range of materials that can be processed efficiently. Whether cutting thin metals, composites, or reflective materials, operators can adjust pulse parameters to achieve optimal results across diverse material properties.
pulse shaping technology enhances the versatility and precision of laser cutting processes by providing operators with nuanced control over energy delivery. By optimizing pulse profiles according to material specifics and cutting requirements, manufacturers can achieve superior cut quality, reduce production costs, and expand their capabilities in demanding industrial applications.
Modulation Techniques: Enhancing Control and Precision
Modulation techniques in laser cutting involve dynamically adjusting the laser beam's characteristics to optimize performance across various materials and applications. These techniques are pivotal in achieving superior control and efficiency in laser cutting operations.
1. Pulse Width Modulation (PWM)
Pulse Width Modulation focuses on controlling the average power delivered to the material by varying the duration of laser pulses. This technique allows for precise control over the energy deposition on the workpiece surface. By adjusting the pulse width, operators can finely tune the heat input, which is crucial for achieving clean cuts and minimizing heat-affected zones, particularly in thinner materials.
2. Frequency Modulation
Frequency Modulation involves adjusting the repetition rate of laser pulses. By modulating the frequency, operators can optimize cutting parameters such as edge quality, cutting speed, and material interaction. This technique is particularly advantageous when cutting materials of varying thicknesses or when aiming for specific edge characteristics. It helps in maintaining consistent energy delivery, thereby enhancing cutting precision and efficiency.
Applications of Modulation Techniques
Enhanced Piercing of Thick Materials
Modulation techniques significantly improve the piercing process for thick materials. By carefully managing the laser's energy output through PWM or frequency adjustments, operators can reduce piercing time and achieve cleaner entry points. This capability is critical for industries requiring efficient processing of thick metals or composites.
Optimized Cutting of Reflective Materials
Reflective materials like copper and aluminum pose challenges due to their high reflectivity, which can impair laser cutting efficiency and quality. Modulation techniques mitigate these issues by precisely controlling the energy deposition. By adjusting parameters such as pulse width or frequency, operators can effectively manage the interaction between the laser beam and the material surface. This results in improved cut quality and reduced incidences of burrs or heat-induced deformities.
In conclusion, modulation techniques in laser cutting offer versatile solutions to enhance control and precision across a wide range of materials and applications. By leveraging PWM and frequency modulation, manufacturers can achieve superior cutting results, optimize production processes, and expand the capabilities of laser cutting technology in various industrial sectors.
Max Laser Cut Price Analysis and Trend
The Max laser cut price can vary widely depending on several factors such as the specific model, its capabilities, and the region where it's being sold. Generally, Max laser cutting machines are positioned as cost-effective solutions offering competitive performance in the mid-range to high-end segments of the market.
What's the Max Laser Cut Price
Here’s a general overview of the pricing range you might expect for Max laser cutting machines:
- Entry-Level Models: These are typically smaller machines suitable for small to medium-sized enterprises (SMEs) or workshops. Prices for entry-level Max laser cutting machines can start from around $30,000 to $80,000, depending on the specific features and capabilities.
- Mid-Range Models: These models offer higher laser power and larger cutting areas, suitable for medium to large-scale production environments. Prices for mid-range Max laser cutting machines generally range from $100,000 to $300,000.
- High-End Models: High-end Max laser cutting machines incorporate advanced features such as automation integration, enhanced precision, and high-speed cutting capabilities. Prices for these machines can range from $300,000 to over $1 million, depending on the specifications and customization options.
It's important to note that these prices are approximate and can vary significantly based on factors such as local market conditions, additional features, service agreements, and customization requirements. For precise pricing and availability, it's advisable to consult directly with Max laser or authorized distributors who can provide tailored quotes based on specific business needs and geographic location.
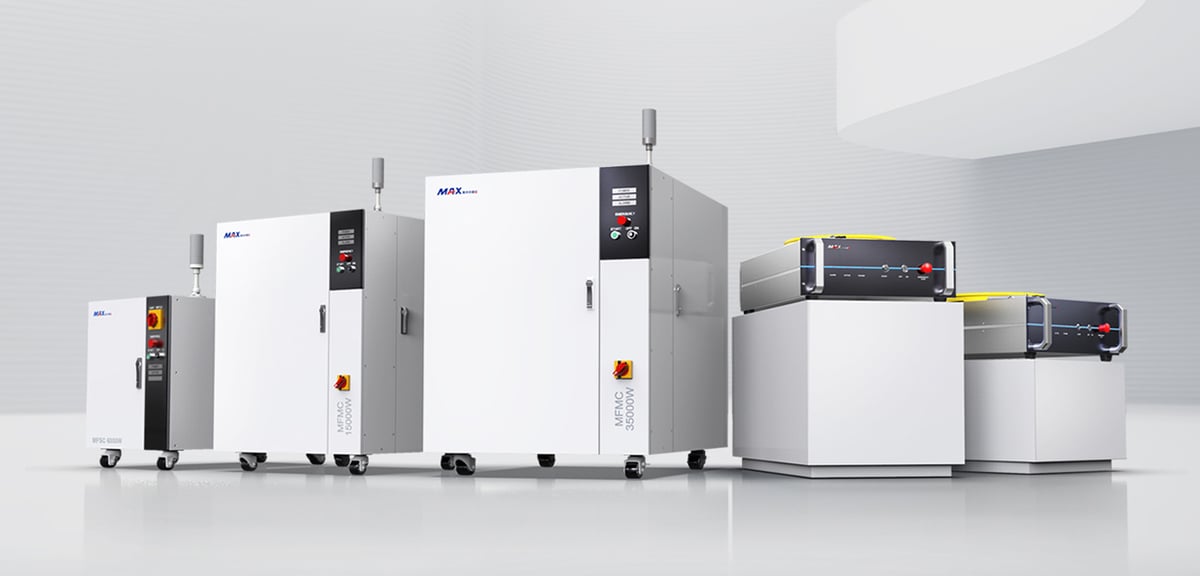
Most Popular Types of Max Photonics Fiber Laser Sources
1. MFSC Series Fiber Lasers
Features:
- Power Range: 500W to 3kW.
- Applications: Cutting, welding, and marking.
- Beam Quality: High quality for precise material processing.
- Cooling: Efficient cooling systems.
- Price Range: Typically ranges from $30,000 to $150,000, depending on power and specifications.
2. MOPA Series Fiber Lasers
Features:
- Power Range: 20W to 100W.
- Pulse Width Modulation: Adjustable pulse widths for fine engraving and marking.
- Applications: Versatile for various materials.
- Price Range: Generally priced from $15,000 to $50,000, depending on configuration.
3. CW (Continuous Wave) Fiber Lasers
Features:
- Power Range: 1kW to 12kW+.
- Stable Output: Consistent performance for continuous operations.
- Applications: Cutting thick materials and high-speed processing.
- Price Range: Typically starts from $50,000 and can exceed $500,000 for higher power models.
4. QCW (Quasi-Continuous Wave) Fiber Lasers
Features:
- Power Range: 150W to 300W.
- Pulse Control: Precise control over pulse duration.
- Applications: Precision welding, drilling, and cutting.
- Price Range: Generally priced between $30,000 to $100,000, depending on specifications.
5. Single-Mode Fiber Lasers
Features:
- Power Range: Up to 2kW.
- Beam Quality: Superior quality for high-precision applications.
- Applications: Fine cutting, engraving, and micromachining.
- Price Range: Typically ranges from $20,000 to $80,000, depending on power and features.
6. High-Power Fiber Lasers
Features:
- Power Range: 6kW to 30kW+.
- Heavy-Duty Applications: Industrial-scale cutting, welding, and additive manufacturing.
- Price Range: Prices can range from $100,000 to over $1 million, depending on power and specifications.
7. UV and Green Fiber Lasers
Features:
- Wavelengths: Ultraviolet (355 nm) and green (532 nm).
- Applications: Fine engraving, marking on sensitive materials, and micro-processing.
- Price Range: Generally priced from $50,000 to $200,000, depending on wavelength and power.
These types of Max Photonics fiber lasers cater to a diverse range of industrial applications, offering solutions from precision marking to heavy-duty cutting and welding. Prices can vary significantly based on specifications, power output, and additional features. For precise pricing and detailed specifications, it's advisable to contact Max Photonics directly or their authorized distributors.
Advantages of Max laser Over Other Globle Brands
What Are Other Popular Lasers?
Besides Max laser from China, here are some globle famous laser manufactures listed as below table:
Ranking | Brand | Company | Year Established | Location | Employees | Website Address |
---|---|---|---|---|---|---|
1 | IPG | IPG Photonics | 1990 | USA | 5,000+ | IPG |
2 | Coherent | Coherent Inc. | 1966 | USA | 5,000+ | Coherent |
3 | Trumpf | TRUMPF SE + Co. KG | 1923 | Germany | 13,500+ | Trumpf |
4 | nLIGHT | nLIGHT, Inc. | 2000 | USA | 1,000+ | nLIGHT |
5 | Raycus | Wuhan Raycus Fiber Laser Technologies Co., Ltd. | 2007 | China | 2,000+ | Raycus |
6 | JPT | Shenzhen JPT Opto-electronics Co., Ltd. | 2004 | China | 1,000+ | JPT Laser |
8 | Keopsys | Keopsys Group | 2000 | France | 200+ | Keopsys |
What Are Advantages of Max laser Over Other Globle Brands?
Cost-Effectiveness: Max Photonics lasers are often priced competitively compared to other global brands, making them accessible for a broader range of industrial applications without compromising on quality or performance.
Reliability and Durability: Max Photonics is known for the robustness and durability of its laser sources. They are engineered to withstand rigorous industrial environments, ensuring long-term reliability and minimal downtime.
Advanced Technology: Max Photonics incorporates cutting-edge fiber laser technology in their products, including high beam quality, efficient cooling systems, and advanced control interfaces. This technology integration enhances performance and operational efficiency.
Customization Options: Max Photonics offers flexibility in customization to meet specific customer needs, including different power outputs, wavelengths, and application-specific configurations. This customization capability allows for tailored solutions that optimize productivity and meet unique manufacturing requirements.
Global Presence and Support: With a strong global presence and extensive service network, Max Photonics provides comprehensive after-sales support, including technical assistance, training, and maintenance services. This ensures prompt support and service reliability for customers worldwide.
Wide Range of Applications: Max Photonics lasers are suitable for diverse applications across industries such as automotive, aerospace, electronics, and medical devices. They excel in cutting, welding, marking, and surface treatment applications, offering versatility and high performance in various material processing tasks.
Innovation and Research: Max Photonics invests in continuous innovation and research to stay ahead in laser technology advancements. This commitment to innovation results in improved product features, efficiency gains, and new application capabilities that benefit customers seeking state-of-the-art laser solutions.
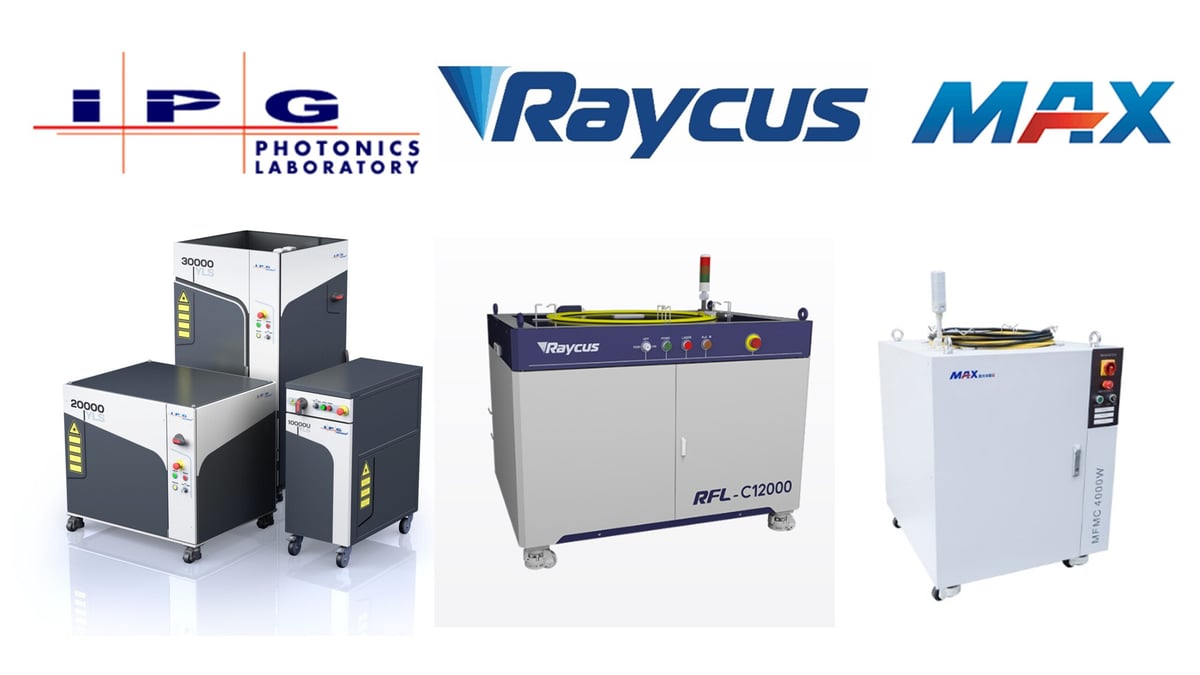
Key Factors to Consider When Purchasing a Laser Source
Selecting the right fiber laser source is crucial for achieving optimal performance and efficiency in laser cutting, marking, and welding applications. Here are key factors to consider when evaluating different manufacturers:
Power Output:
Range and Adjustability: Fiber laser machines offer a wide range of power outputs, from a few watts to several kilowatts. Choose a machine that allows for tunable power output to adapt to various material thicknesses and processing speeds.
Wavelength:
Material Compatibility: The wavelength of the laser affects its absorption and interaction with different materials. Select a wavelength specific to the materials you commonly work with to optimize cutting efficiency and quality.
Pulse Duration:
Control over Thermal Effects: Pulse duration controls the heat input and thermal damage to the material. Shorter pulses are preferable for delicate materials to minimize distortion and heat-affected zones.
Beam Quality:
Precision and Focus: A fiber laser source with excellent beam quality ensures precise control over the laser beam, allowing for sharper focus and finer details in cutting, marking, or welding processes.
Customer Service and Support:
Maintenance and Training: Consider the reliability of the manufacturer's customer service. Look for companies that offer affordable maintenance plans, responsive technical support, and comprehensive training for operators.
Cost-effectiveness:
Quality vs. Price: While high-quality fiber laser sources can command higher prices, it's essential to balance cost with the performance and longevity of the equipment. Many reputable manufacturers offer competitive pricing without compromising on quality.
Key Criteria for Selecting a Top Fiber Laser Source Manufacturer
When choosing a fiber laser source manufacturer, several critical criteria can guide your decision-making process to ensure you select a provider that offers quality, reliability, and performance. Here are essential factors to consider:
Reputation and Industry Experience:
Opt for manufacturers with a strong reputation and extensive experience in the fiber laser industry. Established companies often have a proven track record of delivering reliable products and innovative solutions.
Product Quality and Certifications:
Ensure the laser sources meet international quality standards such as ISO and CE certifications. High-quality certifications indicate compliance with stringent manufacturing processes and reliability in performance.
Technological Innovation and Advancements:
Choose manufacturers that prioritize research and development (R&D) to offer cutting-edge and innovative laser solutions. Technological advancements can significantly enhance operational efficiency and overall performance.
Customer Support and Service:
Reliable customer support is crucial for addressing any operational issues promptly. Select manufacturers known for excellent after-sales service, technical support, and comprehensive training programs for operators.
Conclusion
For industries seeking reliable laser cutting solutions, Max Photonics provides competitive pricing without compromising on quality or technological innovation. Their lasers are designed to enhance operational efficiency, minimize downtime, and deliver consistent results, making them a valuable asset in manufacturing environments.
When exploring laser cutting machines, consider KRRASS laser cutting solutions as well. Known for their durability and advanced features, KRRASS laser machines offer a range of models tailored to different production needs. Whether for small-scale operations or large industrial applications, KRRASS lasers provide customizable options and robust performance that align well with diverse manufacturing requirements.
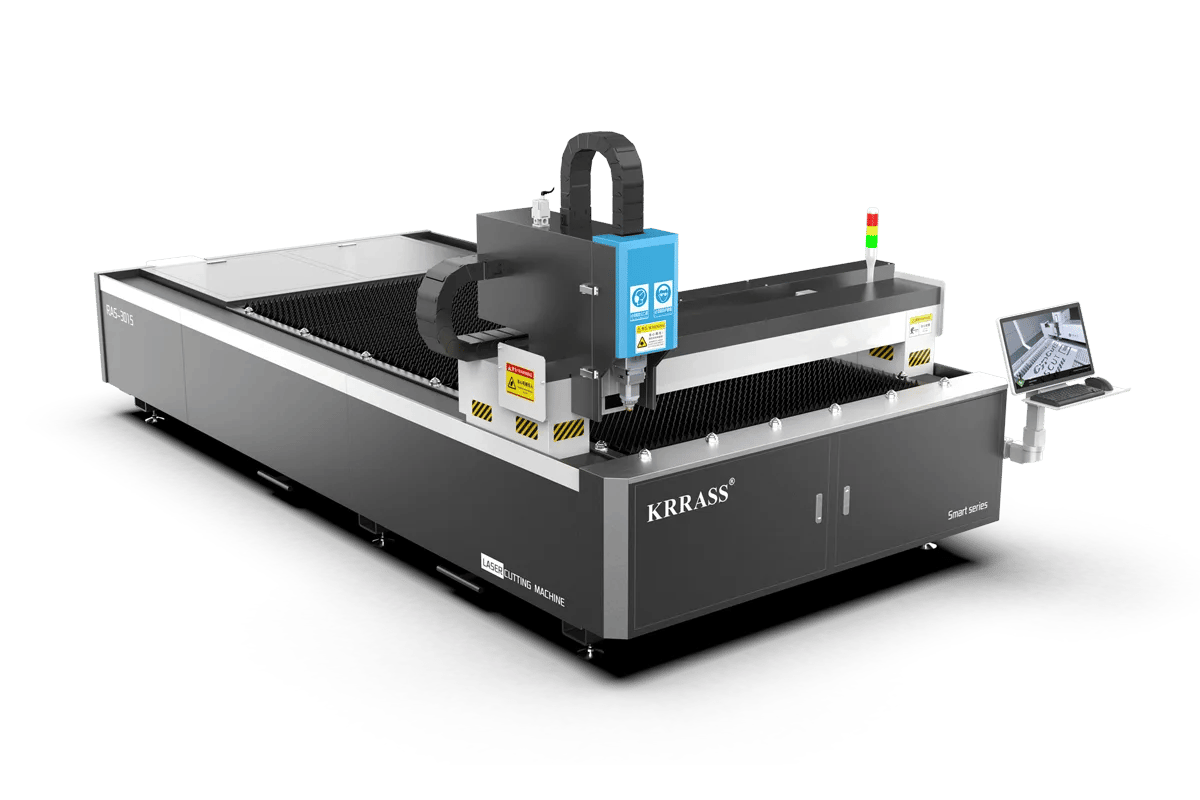