Is there anything better than reducing work preparation time and improving work efficiency?
The constantly advancing technology and customer demands require manufacturing workshops to accomplish more tasks in one go, increase work speed, and produce more precise parts. CNC press brakes are crucial manufacturing equipment used for bending and forming metal sheets in almost every workshop.
Today's technology provides us with CNC (Computer Numerical Control) capabilities to enhance accuracy and production capacity. However some customers don't know much about CNC press brake knowledge and think it's complex and expensive, In this article, we will debunk misconceptions and myths about CNC press brakes and reveal how your business can benefit from them.
Table of Contents
CNC Press Brake vs. Press Brake
A press brake machine is a tool used for bending sheets and plates, most commonly metal sheets. It works by clamping the workpiece between matching punch and die sets and applying force measured in tons to bend the metal into a predetermined shape.
CNC press brakes are much more specialized than bending machines. CNC stands for Computer Numerical Control, and these brakes can bend metal sheets of only a few inches wide to sections several feet long on the largest industrial machines. They have a fixed bed, V-shaped tool blocks clamped in place, and a top punch that moves under the influence of the V-shaped blade tool, forcing the material to yield between the punch and die.
When using a CNC press brake, the setup time is much faster because the controller calculates all the positions for the ram and backgauge. It can also check for errors, calculate the correct bending sequence, and repeat movements for production forming. In contrast, with manually operated bending machines, the operator must reset the machine with each bend. CNC is programmable, allowing for quicker switches between different bends, parts, or even materials.
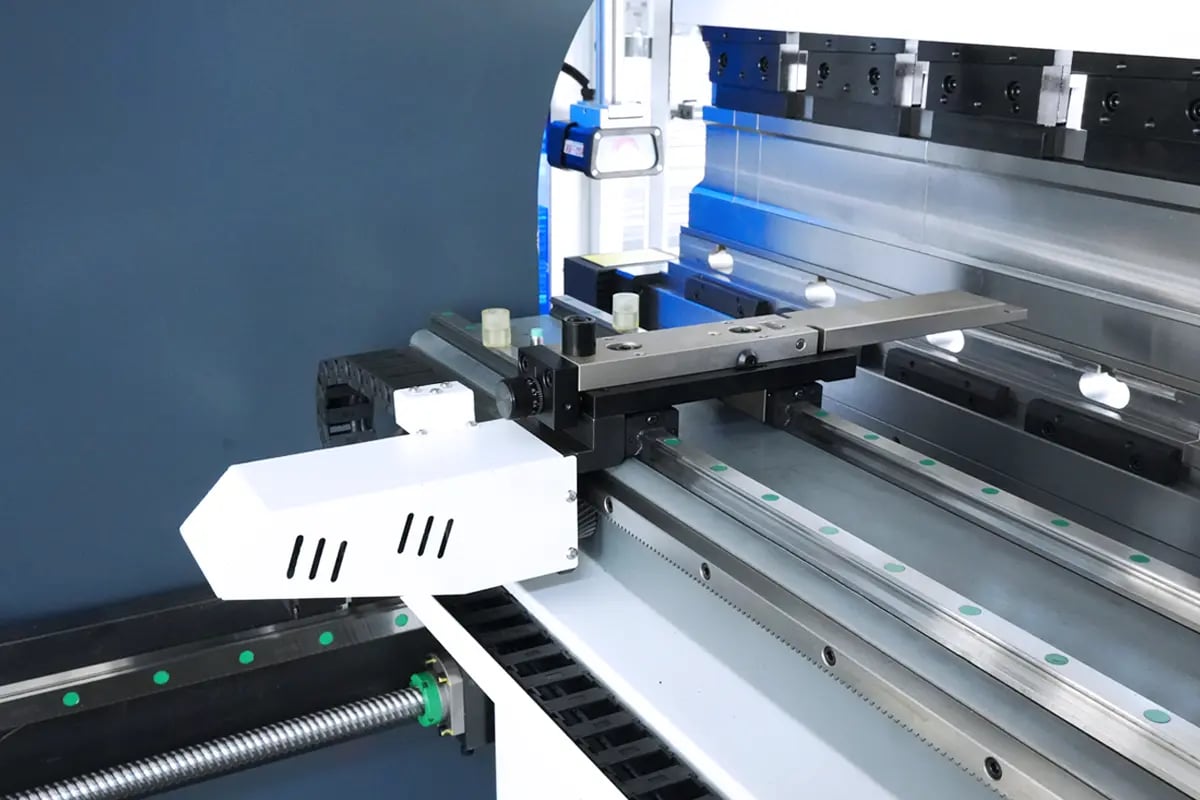
CNC Press Brake Conceptions vs Facts
CNC Press brakes are too expensive
Adding CNC controls to a press brake does indeed slightly increase the cost (10-15%); however, this cost is quickly offset by the increase in productivity. The time saved with a CNC press brake translates to money in the bank. You can boost your production, and the machine will recoup its cost very rapidly. Additionally, you can purchase used and refurbished machines that perform just as well for a much lower cost. You can even trade in your old machines for new or used ones.
CNC Controls are only for production
CNC controls are not limited to production alone. Today's graphical CNC controls are much easier to use for prototypes and small production runs. They automatically calculate bend deductions, blank lengths, ram approach position, bend depth, bend sequence, and much more. They achieve all this with minimal input from the operator, making the setup and operation of a CNC-controlled machine easier, faster, and ultimately more cost-effective.
They are too difficult to learn
Today's CNC controls operate in a simplistic manner, akin to an etch-a-sketch. Taking basic graphic input from the operator, they process it through a series of internal calculations to provide and execute the complex functions of the press brake. However, they accomplish all this while maintaining a simple, user-friendly interface that is easy to navigate and rich in features, making setup and operation of CNC-controlled machines simple and quick. Typically, these control systems require only a few hours of training before operators become proficient in their use.
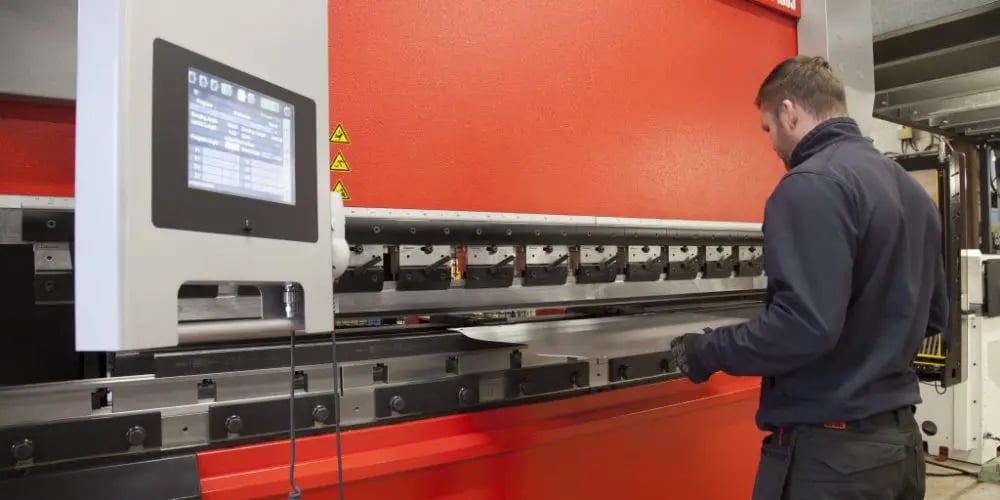
Not suitable for many materials
Some people may think that CNC bending machines are only suitable for certain types of metal sheets and not other materials. In fact, these machines can often be adapted to a variety of materials, including different kinds of metals, plastics, and alloys.CNC bending machines are most commonly used to process metal plates, such as steel plates, stainless steel plates, aluminum plates, copper plates, etc. Also suitable for various alloy materials, such as aluminum alloy, titanium alloy, etc. These materials typically have high strength and lightweight properties, making them suitable for applications requiring structural rigidity and lightweight design. It can even be used to process some plastic materials with good plasticity, such as polycarbonate (PC), polypropylene (PP), etc., to produce plastic components or parts.
How CNC Press Brake Can Boost Your Business
Unlocking cost savings for sustainable growth
Investing in CNC press brakes offers a compelling avenue for significant cost savings. The inherent efficiency of these machines results in accelerated production cycles, effectively minimizing downtime associated with setup and adjustments. Precision and accuracy are paramount, ensuring that components are crafted flawlessly on the initial attempt. This reduction in material wastage not only translates to immediate cost savings but also aligns seamlessly with sustainable business practices, resonating positively with environmentally conscious industries.
Speeding ahead with enhanced productivity
The operational speed of CNC press brakes is a game-changer for businesses aspiring to elevate productivity levels. Setup times undergo a dramatic reduction compared to their manual counterparts, facilitating swift adaptation to evolving production demands. Streamlined processes and automation capabilities empower manufacturers to meet tight deadlines and fulfill orders promptly, fostering a more agile and responsive business environment.
Unmatched flexibility for diverse project handling
A standout feature of CNC press brakes is their unmatched flexibility. These machines can be programmatically adapted to execute a diverse spectrum of tasks, encompassing everything from forming and bending to punching, hemming, and intricate processes like creating louvers. This versatility enables businesses to adapt seamlessly to varying production requirements, positioning CNC press brakes as invaluable assets for handling diverse projects with unparalleled ease and precision.
User-Friendly Interfaces for Seamless Operation
The user-friendly nature of modern CNC press brakes significantly contributes to their effectiveness. Intuitive interfaces, often equipped with touchscreens and graphical programming options, empower operators to swiftly grasp controls and efficiently program the machine. This streamlined interface reduces the learning curve for personnel, enabling them to become proficient in a shorter timeframe and maximizing the machine's potential.
In conclusion, the integration of CNC press brakes into manufacturing processes not only promises transformative benefits but also positions businesses for sustained growth. With an unwavering focus on cost savings, heightened speed, and unmatched flexibility, these machines emerge as pivotal assets for businesses navigating the challenges of modern industrial landscapes. For potential users, a thorough understanding of the functions and advantages of these machines will help eliminate possible misconceptions.