Panel bender machines are essential tools in the metalworking industry, known for their precision and efficiency in bending metal sheets. These machines are widely used in various sectors, including automotive, aerospace, and construction, where precise metal bending is crucial. Understanding the maximum bending thickness of a panel bender machine is vital for ensuring that the equipment meets the specific requirements of different projects. This guide aims to provide a comprehensive overview of panel bender machines, focusing on the factors that influence their bending capacity, and offering insights to help you select the right machine for your needs. Whether you are looking to enhance your production capabilities or seeking to invest in new equipment, this guide will equip you with the knowledge needed to make an informed decision.
Table of Contents
What Is Panel Bending
Panel bending is one of many methods used for sheet metal fabrication. Automated and semi-automated processes such as CNC panel bending, which use CAD and CAM drawings, produce metal pieces with tight tolerances. Panel bending systems rely on specially designed panel bender machines. The process differs from regular bending, which usually takes place on press brakes or progressive dies.
Depending on the application’s specific needs, the CNC bending process may involve different types of panel bends, including:
- Sharp — In sharp bends, the radius is smaller than the minimum bend radius, while the center of the radius is creased to produce a sharp bend.
- Radius — A custom bend radius depends on the customer’s unique specifications.
- Step bending — A step bend comprises a large bend radius divided into several smaller bends, which form a slightly larger radius.
- Hemming — These bends consist of sheet metal edges bent to 180°, creating a hem at the edge.
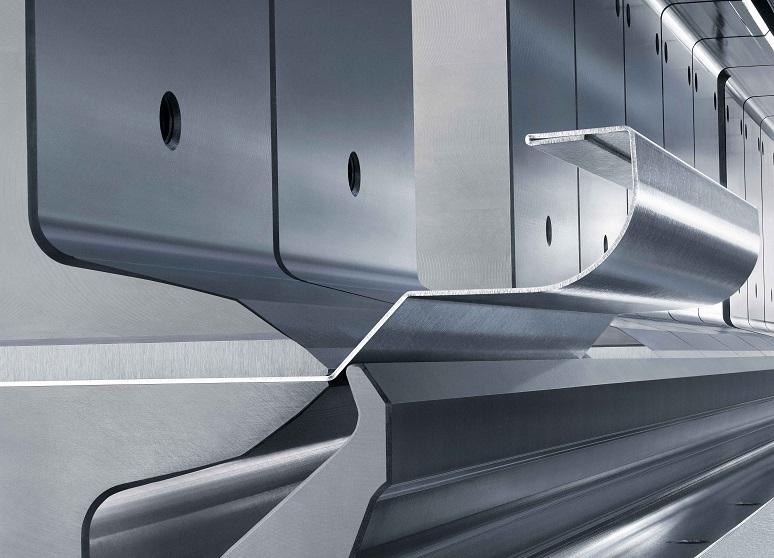
What Is Panel Bender Machine
The soft CNC panel bender machine is a new generation of fully automatic multilateral bending center. It is a new product that allows sheet metal bending to enter fully automated production. The soft bending center does not require molds for bending. It can bend complex shapes of various combinations such as right angles, non-right angles, arcs, up and down bends, etc. It can complete multilateral bending in one positioning. It is used in the field of metal forming of different workpieces in different industries. At present, the soft bending center is gradually replacing CNC bending machines.
Components of the Panel Bender
The flexible bending center consists of a control system, operating system, reducer, servo drive, screw, guide rail, bearing, negative pressure pump, fuselage, feed rack, upper and lower bending knives, hinge knives, pneumatic accessories, suction cups, couplings, oil circuits and other systems.
Structure of a panel bending machine
Panel bending machine usually consists of the following parts:
- Body: The body is the main body of the panel bending machine, usually made of steel or cast iron, with sufficient strength and rigidity to withstand the pressure and vibration of the process.
- Upper and Lower Dies: The upper and lower dies are the core parts of a panel bending machine and are used to bend sheet metal into the desired shape. The upper and lower dies are usually high-strength alloy steel, resistant to abrasion and corrosion.
- Pendulum arm: The pendulum arm is the part that connects the upper and lower molds and makes the upper and lower molds move relative to each other during the process through the pendulum movement.
- Operating system: the operating system is usually composed of a CNC system and hydraulic system, which is used to control the operation of the panel bending machine and various parameters during the processing, such as bending angle, bending radius, bending speed, etc.
- Support device: support the metal sheet to be processed to ensure the stability and accuracy of the sheet during processing.
- Clamping device: tight metal plate to be processed to ensure that the processing process does not occur during the plate movement or sliding.
Shortcomes of Traditional Sheet Metal Bending
① Low degree of automation: Bending of large pieces (1m*1m) with a thickness of 1.2mm galvanized sheet requires at least 3+1 mode (3 auxiliary workers + 1 skilled worker).
② Unable to mass produce: For bending of small pieces (0.5m*0.5m), a skilled worker needs to rest after 20 minutes of operation, and the accuracy of each bending varies.
③ High safety hazards: If the operators do not have enough tacit understanding, work-related injuries are very likely to occur.
Advantages of Panel Bending Machine
1. Fast bending speed
The advantage of the flexible bending center is its fast bending speed. Since the CNC bending machine needs to manually adjust the direction and then bend, a lot of labor is wasted. The bending speed of the flexible bending center is 3 times that of the CNC bending machine, which greatly reduces the cycle time of multilateral and multi-pass bending, reaching 0.5 s/time. The full servo control can control the product accuracy within 3S, which greatly saves labor.
2. No bending mold required
The flexible bending center adopts a universal bending mold, and realizes bending of various shapes through multi-axis concurrent linkage full servo control. Traditional CNC bending machines require one bend and one mold, and special molds are customized for each bending shape, which is costly.
3. High degree of automation
The flexible bending center has reserved a wealth of interfaces to facilitate the connection of upstream and downstream production lines of sheet metal. It can be connected to the robot to realize automatic integrated loading and unloading, and realize full automation.
4. High safety factor
CNC bending machine: It is necessary to manually feed the bent parts into the bending machine for bending, which has certain safety risks.
CNC panel bending amchine: The bending workpiece is automatically pushed into the flexible bending center through the suction cup, and is automatically pushed back through the suction cup after bending. The whole process reduces manual intervention, and the flexible bending center has higher safety performance.
Summary
With the rapid development of the manufacturing industry, the process requirements for sheet metal bending are getting higher and higher. Manual operation of CNC bending machines for bending cannot guarantee the consistency of workpieces, resulting in different errors for each workpiece and failing to meet the standards. CNC panel bending centers can ensure bending accuracy and have a good control over the quality of workpieces.
CNC panel bending centers have been widely used in various industries such as kitchenware, ventilation, air conditioning, filing cabinets, electrical cabinets, tool cabinets, environmental protection and purification, and more and more people are choosing CNC panel benders.
Dimensions and Design Considerations for Panel Bending
With each panel bending project, there are certain design considerations and dimensions that influence the workpiece’s outcome.
Bend Line
The bend line is a straight line on either side of a panel bend that shows the start and end of a bend.
Bend Radius
The bend radius is the distance between the axis of the bend and the bend’s interior surface. The most frequently used radius is a 90° angle. To save time and money, Metal Works can bend up or down on the same plane for more efficient production.
Parts often need to be overbent to achieve the ideal radius and bend angle due to residual stress in the material following bending, which is known as springback. The minimum bend value depends on the specific material and application, but the bend radius in most applications should be at least equal to the material thickness, which helps prevent fracturing.
Bend Angle
The bend angle, or inside bend radius, is the angle from the bent flange to its starting position before bending. The inside bend radius plus the sheet thickness will give you the outside bend radius.
Neutral Axis
The neutral axis is the part of the metal sheet that remains uncompressed and unstretched. It stays at a constant length.
K-factor
This defines where the neutral axis is within the bending material. The formula for calculating the K-factor involves dividing the neutral axis (T) by the sheet thickness (t). The value of the K-factor tends to be higher than 0.25 but below 0.5.
Bend Allowance
The bend allowance is the bend’s arc length or the neutral axis length between the bend lines. You can use bend allowance to calculate the total flat length, specifically by adding the bend allowance to the flange lengths.
Bend Relief
Applications use bend reliefs if a bend extends on an edge. The bend relief must not be deeper than the combination of the bend radius and material thickness. To prevent tearing, the bending process requires a relief notch.
Bend Height
The bend height (H) needs to be a minimum of four times the thickness (t) of the sheet added to the bend radius (r). Otherwise, a bend height that’s too small will lead to part deformation. The formula for calculating bend height is as follows: H = 4t + r.
Bending Near Holes
Panel bending near holes on a workpiece can result in hole deformation.
Why Can CNC Panel Bender Machines Replace Traditional Bending Machines?
First of all, the panel bender machine can greatly improve production efficiency. The traditional bending process requires manual operation, which is not only inefficient but also cannot guarantee accuracy. For example, Krrass panel bending center can automatically bend according to the preset program without manual intervention, which greatly improves production efficiency. At the same time, the bender machine also has a variety of bending modes, which can adapt to various production needs and realize flexible production.
Secondly, the efficiency of the Panel Bender Machine can significantly improve product quality. Panel Bender adopts a high-precision servo motor and an advanced CNC system, enabling precise bending control and ensuring top-notch product quality. Additionally, the panels feature automatic detection and correction functions, which monitor the bending process in real-time, identify and rectify issues promptly, further enhancing product quality. This advanced technology makes the panel bender machine an ideal choice for achieving superior results in metalworking projects.
The labor-saving effect of panel bending machines cannot be ignored. The traditional bending process requires a lot of manual operation, which is not only labor-intensive but also incurs high labor costs. However, panel bending machines can realize unmanned operation, greatly reducing labor costs. Additionally, the stable operation of panel bending machines can reduce production accidents caused by human errors and improve production safety.
In addition, panel benders are also energy-saving and environmentally friendly. Panel benders are electrically driven and do not require fuel, which is both energy-saving and environmentally friendly. At the same time, the operating noise is low and the impact on the environment is minimal.
In general, the flexibility, efficiency and labor-saving effects of the machine are obvious. It can not only improve production efficiency and product quality, but also save labor costs and protect the environment. Therefore, the panel bender machine is undoubtedly an ideal choice for modern manufacturing industry and is surpassing traditional bending equipment to become the mainstream.

Bending Process of Panel Benders
Feeding and Positioning
The metal sheet is fed into the machine either manually or through an automated feeding system. Once fed, the sheet is positioned accurately within the machine using stops and alignment systems to ensure precision in bending. These systems help maintain consistent alignment and prevent deviations, which is crucial for achieving the desired bend angles and dimensions. The combination of automated feeding and precise positioning ensures that each sheet is correctly placed for the bending process, enhancing both efficiency and accuracy.
Clamping and Bending Blades
Upon positioning, the metal sheet is securely clamped in place using upper and lower clamps. These clamps ensure the sheet remains stable throughout the bending process, crucial for maintaining accuracy and preventing material slippage. Simultaneously, the upper and lower bending blades of the panel bender machine are positioned. These blades work in tandem to execute the bending sequence: the upper blade lifts to bend the metal upward, while the lower blade bends it downward. This synchronized action allows for precise shaping of the metal sheet according to programmed specifications, ensuring consistent results across each production cycle.
Bending Process and Precision Control
As the clamps secure the metal sheet, the panel bender's upper and lower bending blades initiate the bending process. The upper blade rises to bend the metal upward, while simultaneously, the lower blade bends the sheet downward. This dual-action bending sequence is meticulously controlled by the machine's programming, ensuring each bend meets exact angles and dimensions required. Advanced sensors and feedback systems provide real-time adjustments, maintaining precise control over the bending process.
Repositioning and Unloading
After completing a bend sequence, the clamps release, allowing for repositioning of the sheet to execute additional bends if needed. This repositioning may be performed manually or automatically, depending on the machine's capabilities and the complexity of the part being fabricated. Once all bending operations are finished, the clamps release the formed sheet, which is then extracted from the machine. This efficient unloading process prepares the bent metal sheet for subsequent manufacturing stages or final product assembly.
Common Bending Methods
Free Bending
Free bending, also known as air bending, is simpler than other methods. The depth of the upper mold controls the bending angle into the V-groove of the lower mold.
The accuracy of a bent part depends on various factors, such as Y1, Y2, V-axis upper and lower molds, and plate.
However, it is widely used due to its versatility and wide processing range. It is suitable for simple, large or less productive structures.
Three-point Bending
Three-point bending, also known as mold bending (bottoming), has a bending angle determined by the height of the wedge in the lower mold.
The upper die provides only sufficient bending force and eliminates non-parallelism between the dies using hydraulic pads on the ram.
This method allows the production of high-precision parts, i.e., with low angular and straightness errors. It is used for complex structures, small sizes and batch processing.
Corrective Bending
Corrective bending is formed in the cavity formed by the upper and lower molds, which can obtain the desired cross-section shape. However, it requires a larger bending force and repeated mold repair, and the generality of the mold could be better. When special requirements or cross-section shapes can not be realized by free bending, often use this bending method.
What's the Max Bending Thickness?
The bending thickness capability of panel bender machines can vary significantly depending on the specific model and manufacturer. Generally, panel benders are designed to handle a range of material thicknesses, typically from thin gauges up to medium thicknesses of sheet metal. Here are some typical capabilities:
- Thin Gauges: Panel bender machines can often bend very thin gauges of sheet metal, sometimes as low as 0.5 mm or even thinner.
- Medium Thicknesses: They are also capable of bending medium thicknesses, ranging commonly from 1 mm to 3 mm, and in some cases, up to 4 mm or more depending on the machine's design and power.
- Material Type: The bending thickness can also depend on the type of material being used (e.g., stainless steel, aluminum, mild steel). Different materials may require adjustments in bending parameters such as clamping force and bending speed.
- Machine Specifications: It's essential to check the specifications provided by the manufacturer for each model of panel bender, as they will specify the exact bending capacities in terms of thickness and material type.

Tips for Choosing the Best Panel Bender Machine
1. Bending Capacity
Bending capacity is a crucial factor that determines whether your machine model is compatible with handling your workpiece size. You can easily fit any workpiece smaller than the maximum capacity of your machine.
However, don’t choose a bending machine with a bending capacity that is too large, as it requires extensive tooling and more energy consumption. It can also reduce productivity, increasing production costs.
2. Material
Each bending machine can handle various types of material. Stainless steel is hard to bend and needs a high-powered metal bending machine. However, you don’t need excess bending force when dealing with ductile metals like aluminum.
Check the manufacturer’s recommendation before picking a bending machine. It will enable you to pick the machine that best fits your material’s strength.
3. Number of Tool Stacks
The number of tool stacks indicates the capacity of a bending machine to install bending dies. Installing multiple dies allows you to handle multiple radii in a single setup. Bending metal pipes in a tube bending machine with a large number of tool stacks allows you to minimize material handling. It also offers you higher design freedom, enabling you to create various designs at once.
4. Bend Quality
Bend quality is another prominent factor that impacts the choice of a bending machine. It determines your machine’s capability to create precise bend angles and lengths of straight portions. The machine assembly and quality of its various components also impact the bend quality it produces.
5. Control System Stability
The stability of a control system involves several aspects, including hardware configuration, functionality, and reliability. It impacts the efficiency of a bending machine. The reliability of controllers is a critical factor in picking the right machine. You also need to focus on the durability of various components to ensure smooth operation.
6. Wall Thickness
Wall thickness is a crucial factor in choosing the right tube-bending machine. It determines the bending force required to bend a pipe or tube to a particular angle. The thickness of the material is also crucial when dealing with metal sheets and plates. Thicker materials required more force. You need to select a highly efficient bending machine to bend thick materials.
7. Power Source
Various bending machines employ different power sources. They use hydraulic, pneumatic, or electric power. Hydraulic bending machines are best for bending tasks that require excessive power. Meanwhile, pneumatic or electric machines are known for their efficient energy consumption and smooth operations.
If you are dealing with workpieces that demand high-powered machines, you should go with hydraulic-powered bending machines. However, if you are looking for an energy-efficient solution, pneumatic or electric machines will be better for you.
8. Maintenance
Maintenance of a bending machine is a time-consuming and costly pursuit. However, without regular maintenance, your expensive machine will be ruined.
Some companies offer you durable machines with exceptional features that require less maintenance. Investing in such machines allows you to be carefree and concentrate on the bending process.
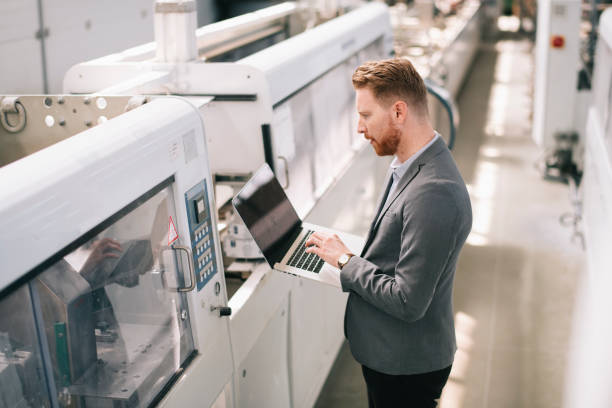
Generally Speaking
In conclusion, a panel bender machine is essential for crafting innovative and bespoke metal products across diverse industries. Selecting the right panel bender enables you to streamline operations and achieve precise bends and shapes with efficiency. It's crucial to invest time in researching reputable suppliers to secure the optimal machine that aligns with your production needs and budget. By choosing the appropriate panel bender machine, you can effectively fabricate intricate metal components and achieve flawless results in shaping metal materials.