Table of Contents
What is Pipe Bending Machine?
Pipe bending machine is a machine designed for bending pipes. It is typically used for bending hollow or solid pipes made from hard materials into various shapes, including angles and curves. This includes bending of iron pipes, steel pipes, aluminum alloy pipes, and more.
Pipe benders can be categorized into two types: CNC pipe benders and hydraulic pipe benders. They are widely used in the construction of power plants, highways and railways, pipeline laying and repair in boilers, bridges, ships, furniture, decoration and other industries.
The pipe bender has several advantages, including multiple functions, a reasonable structure, and simple operation.
Types of Pipe Benders
The pipe bending machine is a machine used to bend pipes into various shapes, such as I-beams, channel steels, angle irons, wires, and more. It can also form coils, “U” shaped pipes, half pipes, and coil pipes. The categories of pipe benders include hydraulic electric bending machines, horizontal hydraulic pipe benders, and multi-functional rolling pipe benders.
The electric pipe bender is powered by electricity and driven by a motor, speed changer, and gear chain transmission. On the other hand, the hydraulic pipe bender decomposes the bending operation into driving clamping to retract with hydraulic pressure, bending the pipe back, auxiliary movement forward and backward, feeding and retracting the core.
The hydraulic pipe bending machine is a common plane winding automatic bending machine and has the advantages of multiple functions, reasonable structure, simple operation, convenient movement, and fast installation. It is used in electric power construction, highway and railway construction, boilers, bridges, ships, furniture, decoration, and more.
The CNC pipe bender, on the other hand, uses a servo motor instead of hydraulic power and is able to control feeding and retracting, rotation of the tilting angle, pipe bending and retracting, auxiliary movement forward and backward, and head lift. The difference between the CNC pipe bender and the hydraulic pipe bender lies in the continuous production, processing precision, and three-dimensional forming of pipe fittings.
The numerical control pipe bender can perform winding bending with one or two bending radii for pipes in a cold state and is widely used in the bending of various pipe fittings and wires in industries such as automobiles and air conditioning.
There are two bending methods of the pipe bender
Cold bending, including hydraulic pipe bender, electric pipe bender and three roll bending machine;
Hot bending, the representative model is the medium frequency pipe bender.
Working Principle of Pipe Bending Machine
According to the method of pipe bending, it can be divided into push bending, roll bending, press bending, and circle bending. Of these, circle bending is relatively easy to automate, so currently, bending machines are mostly designed for this method. The bending process principle is illustrated in a diagram.
The bending process is performed using a bending die, clamping die, and pressure die. The bending die is mounted on the spindle, while the clamping die secures the pipe fittings to prevent any axial movement. The pressure die consists of a guide die and a follow-up die. During the bending process, the guide die applies the appropriate pressure on the anti-wrinkle die to the pipe fittings, and the follow-up die moves along with the pipe fittings. A mandrel is also used to fill the inner cavity of the workpiece and prevent any wrinkles, flattening, thinning or other failures during bending.
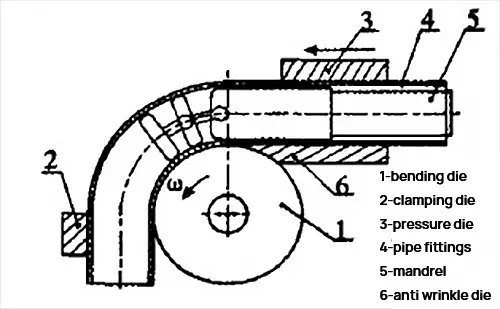
The spindle rotates and the tube is formed by being wound around the bending die. The process also involves feeding the workpiece, preparing the space for the next bend, and so on. The bending radius is determined by the radius of the bending die, and different bending radii can be achieved by simply replacing the bending die with one of a different radius.
Structure and working principle of automatic pipe bender and electro-hydraulic pipe bender:
The hydraulic system of a pipe bender is composed of an electric oil pump, high-pressure oil pipes, quick connectors, working cylinder, and plunger. The elbow part of the machine includes an upper flower plate, lower flower plate, die head, and roller. The electric oil pump outputs high-pressure oil, which is sent to the working cylinder through high-pressure oil pipes. The high-pressure oil drives the plunger in the working cylinder to generate thrust, resulting in bending through the elbow component.
Features of Pipe Bender
The Pipe bending machine uses a touchscreen to add a numerical control module and features a dialogue-type operation for easy program setting. Its structure is stable and not easily deformed.
Each file can store 16 bending angles, and 16 sets of files can be stored in memory. The slow-speed positioning function and stable bending angle ensure a repetition accuracy of ±0.1°.
In case of error, the message will be displayed on the screen to help the operator eliminate the issue immediately. The device also comes with research and development software for converting pipe processing values into coordinates, which can be purchased and installed on a desktop computer for editing and calculation.
Advantages & Disadvantages of Pipe Bending Machine
When using the Pipe Bender, high-pressure oil from the electric oil pump is sent into the working oil cylinder through a high-pressure oil pipe. This high-pressure oil pushes the plunger in the working oil cylinder to generate thrust, and the pipe is bent through the bending parts.
The Pipe Bender has several advantages:
It uses a touch screen and numerical control module with a dialogue operation, making program setting simple and easy.
The bed structure is stable and not prone to deformation.
The mobile foot switch has three functions: automatic start, emergency stop, and emergency stop, providing high safety.
There is the option to choose manual, semi-automatic, and full cycle functions.
The machine head and elbow are elegantly designed, providing ideal elbow space.
The large capacity cooling circulation system ensures stable machine operation.
The mold is easy to replace, allowing for flexible production.
During processing, the screen of the mobile controller displays the current processing value of the elbow, and it is possible to set single step action, half cycle operation, and full cycle operation.
The pipe bender is primarily utilized for bending pipes.
This equipment is commonly employed in industries such as road construction, automobile processing, and shipbuilding.
The pipe bender boasts high stability, user-friendly operation and maintenance, low operational noise, and improved safety and environmental protection.
Parts & Functions of Pipe Bending Machine
The pipe bender is widely used in our daily lives, but many of us are unaware of its components.
Now, I will introduce you to the key components of a pipe bender.
Fully Automatic Bed:
The bed features a channel steel welded spindle frame, with the upper and lower bearing support plates of the spindle mounted on a 15mm thick steel plate frame.
System Component:
The hydraulic system component can utilize either commercial accessories or aircraft hydraulic accessories.
Transmission Component:
The transmission component comprises an oil cylinder, rack, gear, and transmission shaft.
Mold Component:
The mold component is a supportive tool made from bearing steel or coil steel, depending on the surface diameter, and is heat-treated to achieve a hardness of HRC48~52.
Clamping Component:
The hydraulic clamping component consists of a sliding plate, rocker arm, and hydraulic cylinder. The expansion and contraction of the cylinder drives the movement of the rocker arm.
Electrical Components.
Cnclusion
Tube benders are versatile machines capable of producing a wide range of bend shapes, including simple bends, compound bends, and multiple bends in different planes. They are essential tools in industries where precision bending of tubes and pipes is required to meet specific design and functional requirements.