Pipe bending machine are indispensable tools in various industries where precision bending of pipes and tubes is required. These machines are designed to create curved sections in pipes made from materials such as steel, aluminum, and other metals. Whether for construction, automotive, or manufacturing purposes, pipe bending machines offer an efficient and reliable solution for producing accurate bends with minimal material waste. In this guide, we will explore the main components, working principles, and key advantages of pipe bending machines, providing a comprehensive overview of everything you need to know about these essential tools.
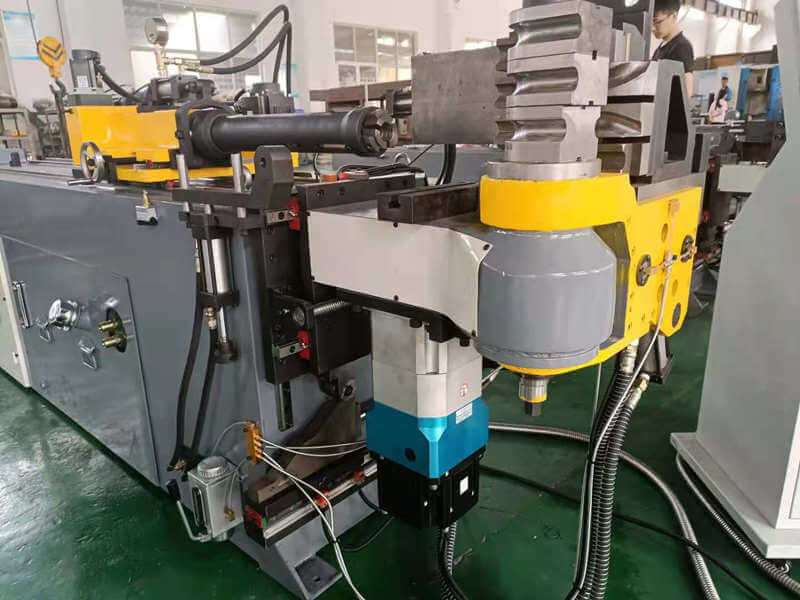
What Are Main Bending Machines
1. Pipe and Tube Bending Machine
These machines are designed to bend metal pipes and tubes into various shapes and angles. They are commonly used in industries like construction, automotive, and shipbuilding. Common subtypes include:
- Rotary Draw Bending Machine: Used for precise, tight-radius bends, ideal for pipes and tubes that require smooth, consistent curves.
- Mandrel Bending Machine: Utilizes an internal mandrel to support the pipe during bending to prevent collapsing or wrinkling.
- Roll Bending Machine: Uses three rolls to gradually bend the material, typically for large-radius bends.
2. Press Brake
A press brake is a machine used to bend sheet metal or plate. It uses a punch and die system to create bends. This machine is typically used for producing straight bends along a sheet of metal. Press brakes come in several types, including:
- Hydraulic Press Brake: Uses hydraulic power to create bends, offering high force for thick materials.
- CNC Press Brake: Controlled by computer numerical control (CNC) for precise and automated bending operations.
- Servo-Electric Press Brake: Utilizes electric servo motors, offering high energy efficiency and precision.
3. Roll Bending Machine
Primarily used for bending large metal plates into cylindrical or conical shapes, roll bending machines use a series of rollers to gradually bend the material. These are widely used for producing parts like metal drums, tanks, and pipes.
4. Folding Machine
Folding machines are specialized for bending sheet metal, particularly in creating precise folds and creases along straight edges. These machines are commonly used in HVAC, roofing, and other sheet metal fabrication industries.
5. Angle Roll Bending Machine
This type of machine is used to bend structural shapes like angle iron, I-beams, and T-bars. It employs a set of rollers to bend these profiles into curved shapes, often used in architectural or structural applications.
6. Wire Bending Machine
Designed specifically for bending wires into various shapes, these machines are commonly used in manufacturing products like springs, hooks, and wire forms.
Each type of bending machine is tailored to specific materials and bending requirements, making them essential tools across a wide range of industries.
What Is Pipe Bending
Pipe bending is a metal forming process used to permanently shape pipes or tubing. It can involve form-bound techniques or freeform-bending methods, with both heat-assisted and cold forming options available.
Form-bound methods, such as "press bending" or "rotary draw bending," involve shaping the workpiece using a die to create the desired form. A pipe bending machine can bend straight pipe stock into various single or multiple curves to achieve the necessary shape. These techniques are often used to create complex shapes from different types of ductile metal pipes. In contrast, freeform-bending methods, like three-roll pushbending, shape the pipe without relying on the tool’s geometry.
While round pipes are most commonly used in pipe bending, square or rectangular pipes can also be bent to suit specific job requirements. Other factors, such as wall thickness, tooling, lubrication, and the intended application of the pipe (tube, pipe, or wire), also influence the bending process.
Applications of Pipe Bending Machine
The most common application of pipe bending machines is for pipeline construction and repair. For this purpose, the machines are generally inserted into the mainline. Then, it makes a complete round arch of the pipe to obtain a cylindrical shape. This further provides for the creation of profiles that are complementary to the pipe’s external curve. In addition to this, it also creates profiles that are not parallel to the pipeline.
Another application of this machine is for the construction and repair of underground piping systems. The main advantage of using mechanical force is that it saves energy that would normally be required for the construction and repair of underground piping systems. Some of the common tasks where the application of this machine is used include drawing out of bends, or corrugated piping. Also, when the pipe is bent, the external diameter of the stock pipe is usually smaller than that of the inside diameter of the inner wall of the pipe.
Main Components of a Pipe Bending Machine
Tube and pipe bending are essential for a wide variety of industries. Ercolina’s tube and pipe bending applications are used in everything from the automotive industry to ship building, aviation, aerospace and much more. The automotive industry relies on mandrel bending machines to minimize the ovality that occurs on thin wall tubing when it is bent. Our bending machines also help to eliminate wrinkles on the inside radius of the bend as well.
Two other industries that rely heavily on top-quality pipe bending are the aviation and aerospace industries. In these industries, bends need to be precise and there is no room for error. Our Ercolina pipe bending machines help these industries achieve extremely accurate bends. In aerospace, it is especially important to produce bends with pinpoint accuracy. Our bending machines are perfect for industrial bending of tube, pipe, square, and rectangular profiles. Our mandrel bending machines can even bend profiles to a center line radius as small as 1.5 x diameter.
View these featured bending applications.
Ercolina’s mandrel and non-mandrel tube and pipe bending machines have proven useful across many industries. Whatever tube, pipe, or profile bending you need to manufacture, Ercolina makes a bending machine that will accomplish your goals and exceed your expectations.
Here are some featured pipe bending applications:
Other Industriesal parts, resulting in material cost savings.
Automotive
Commercial Vehicles
Ship Building
Architectural
Industrial
Aviation & Aerospace
Process
The operation starts when the operator positions the clamping block on the pipe. Once set, the machine is activated via the control panel, initiating the ball-bearing rolling action. As the belt moves, the pulley system applies pressure, guiding the pipe along a curved path. This continuous pressure causes the pipe’s thin walls to bend, forming the desired curved sections.
Tube and pipe bending as a process starts with loading a tube into a tube or pipe bender and clamping it into place between two dies, the clamping block and the forming die. The tube is also loosely held by two other dies, the wiper die and the pressure die.
The process of pipe bending involves using mechanical force to push stock material pipe or tubing against a die, forcing the pipe or tube to conform to the shape of the die. Often, stock tubing is held firmly in place while the end is rotated and rolled around the die. Other forms of processing including pushing stock through rollers that bend it into a simple curve.[2] For some tube bending processing, a mandrel is placed inside the tube to prevent collapsing. The tube is held in tension by a wiper die to prevent any creasing during stress. A wiper die is usually made of a softer alloy such as aluminum or brass to avoid scratching or damaging the material being bent.
Much of the tooling is made of hardened steel or tool steel to maintain and prolong the tool's life. However, when there is a concern of scratching or gouging the work piece, a softer material such as aluminum or bronze is utilized. For example, the clamping block, rotating form block and pressure die are often formed from hardened steel because the tubing is not moving past these parts of the machine. The pressure die and the wiping die are formed from aluminum or bronze to maintain the shape and surface of the work piece as it slides by.
Pipe bending machines are typically human powered, pneumatic powered, hydraulic assisted, hydraulic driven, or electric servomotor.
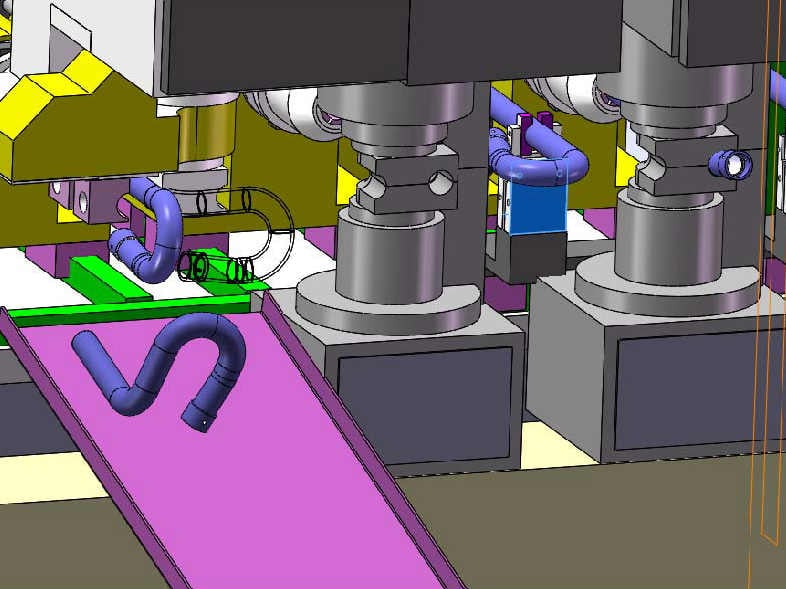
Main Bending Methods for Tube and Pipes
Tube bending as a process starts with loading a tube into a tube or pipe bender and clamping it into place between two dies, the clamping block and the forming die. The tube is also loosely held by two other dies, the wiper die and the pressure die.
The process of tube bending involves using mechanical force to push stock material pipe or tubing against a die, forcing the pipe or tube to conform to the shape of the die. Often, stock tubing is held firmly in place while the end is rotated and rolled around the die. Other forms of processing including pushing stock through rollers that bend it into a simple curve. For some tube bending processing, a mandrel is placed inside the tube to prevent collapsing. The tube is held in tension by a wiper die to prevent any creasing during stress. A wiper die is usually made of a softer alloy such as aluminum or brass to avoid scratching or damaging the material being bent.
Much of the tooling is made of hardened steel or tool steel to maintain and prolong the tool's life. However, when there is a concern of scratching or gouging the work piece, a softer material such as aluminum or bronze is utilized. For example, the clamping block, rotating form block and pressure die are often formed from hardened steel because the tubing is not moving past these parts of the machine. The pressure die and the wiping die are formed from aluminum or bronze to maintain the shape and surface of the work piece as it slides by.
Pipe bending machines are typically human powered, pneumatic powered, hydraulic assisted, hydraulic driven, or electric servomotor.
Press bending
Press bending is probably the first bending process used on cold pipes and tubing. In this process a die in the shape of the bend is pressed against the pipe forcing the pipe to fit the shape of the bend. Because the pipe is not supported internally there is some deformation of the shape of the pipe, resulting in an oval cross section. This process is used where a consistent cross section of the pipe is not required. Although a single die can produce various shapes, it only works for one size tube and radius.
Rotary Draw Bending
Rotary draw bending (RDB) is a highly precise bending method that utilizes tooling, or "die sets," with a constant centerline radius (CLR), also known as the mean bending radius (Rm). This technology allows for accurate and repeatable bends, making it ideal for complex applications. Many rotary draw benders are programmable, enabling operators to store multiple bend profiles with varying angles. Additionally, some machines are equipped with a positioning index table (IDX), which allows for the reproduction of intricate bends with multiple angles and different planes.
Rotary draw benders are widely used for bending tubes, pipes, and solid materials in applications such as handrails, frames, vehicle roll cages, handles, and piping systems. When matched with the appropriate tooling, these machines produce smooth, visually appealing bends. CNC rotary draw bending machines are highly advanced, often using sophisticated tools to create tight-radius bends that meet demanding quality standards.
Full tooling is necessary for bending tubes that are difficult to shape, particularly those with a large outside diameter to thickness (OD/t) ratio and a small mean bending radius (Rm) compared to the outside diameter (OD). To avoid issues such as thinning or collapse on the outer curve of the bend, axial boosting on the tube’s free end or pressure die may be required. Mandrels, with or without linked balls, are often used to prevent wrinkling or ovalization. For simpler bends, the tooling setup can be reduced, eliminating the need for mandrels, wiper dies, or axial assists. In certain cases, custom tooling modifications may be necessary to meet specific product requirements.
Roll Bending
In the roll bending process, pipes, extrusions, or solid materials are passed through a set of rollers—typically three—that gradually apply pressure to bend the material. This method adjusts the bend radius progressively, minimizing deformation in the cross-section of the pipe. Roll benders come in different designs, with pyramid-style roll benders featuring one adjustable top roll, while double-pinch roll benders have two adjustable lower rolls and a fixed top roll. This technique is especially suitable for creating long, gentle curves such as those used in truss systems, as well as for producing pipe coils.
Three-Roll Push Bending
The three-roll push bending (TRPB) process is widely used for freeform bending, allowing for the creation of complex geometries consisting of multiple bending curves. While primarily used for 2D shapes, it also allows for 3D bending. In this process, the profile is guided between a bending roll and supporting rolls as it is pushed through the machine. The position of the forming roll determines the bending radius, and to adjust the bending plane, the pusher rotates the tube around its longitudinal axis. A significant advantage of TRPB is its flexibility—multiple bending radii can be achieved with a single toolset. However, the precision is generally lower compared to rotary draw bending. This method can create contours defined by spline or polynomial functions.
Simple Three-Roll Bending
Three-roll bending of tubes and open profiles can also be performed using simpler, often semi-automatic machines that are not CNC-controlled. These machines typically rely on friction to feed the tube into the bending zone. They often have a vertical layout, where the three rolls are aligned on a vertical plane. Despite being less advanced, these machines are effective for basic bending tasks.
Bending springs
These are strong but flexible springs inserted into a pipe to support the pipe walls during manual bending. They have diameters only slightly less than the internal diameter of the pipe to be bent. They are only suitable for bending 15-and-22 mm (0.6-and-0.9 in) soft copper pipe (typically used in household plumbing) or PVC pipe.
The spring is pushed into the pipe until its center is roughly where the bend is to be. A length of flexible wire can be attached to the end of the spring to facilitate its removal. The pipe is generally held against the flexed knee, and the ends of the pipe are pulled up to create the bend. To make it easier to retrieve the spring from the pipe, it is a good idea to bend the pipe slightly more than required, and then slacken it off a little. Springs are less cumbersome than rotary benders, but are not suitable for bending short lengths of piping when it is difficult to get the required leverage on the pipe ends.
Bending springs for smaller diameter pipes (10 mm copper pipe) slide over the pipe instead of inside.
Types of Tube and Pipe Bending Machines
Computer Numerical Controlled (CNC) benders produce tight-radius bends, large-radius bends, and elliptical bends - all on the same part. They are sophisticated machines that guarantee a high level of productivity and reproducibility. CNC benders are used for creating complex tubular parts because they can manipulate the tube automatically and position it with precision. They consist of three axels and a servomotor driven carriage, which automatically positions the distance between the bends and its plane. CNC benders do not include hydraulic or pneumatic features, leading to greater repeatability and operation. These machines are useful in several industries including automotive, HVAC, ship building and railways. There are three types of CNC axle bending machines:
Vector bend tube bending machines come in various modelsand are designed for automated tube production. They come in various sizes, axis speeds, and controllability for acceleration and deceleration. The high-tech models don't use chains. These machines can be used for high strength aircraft tubing and automotive exhaust tube applications.
Vector bend electric tube bending machines are the most advanced, and deliver a high level of productivity, quality, and reliability. Electric operation of the machines saves more energy than conventional hydraulically operated tube bending machines. These machines are able to reverse the bend head rotation, giving the operators flexibility during complex bending applications. These machines come with an advanced touch screen user interface for programing and monitoring productivity.
Orbital head bending machines offer significant flexibility and can be utilized for complex CNC tube bending. These machines effortlessly produce tubular parts with coils, fittings, and hoses, and can also be easily integrated with automatic loading and offloading equipment. They are used with computer controls on a high resolution touch screen. The advanced features of these machines help to rotate the head and collets simultaneously around the parts, which reduces cycle times and guarantees optimal throughput. The machines are an ideal solution for air conditioning, automotive, truck, and other complex applications.
Hydroforming equipment uses fluid pressure to form ferrous or nonferrous materials to the shape of a die. Machine components consist of a hydraulic hydroforming press, pressure intensifiers, hydroform water system, and a hydroforming unit. The press opens and closes a spilt mold cavity to allow a blank part to be inserted and finished product removed. A pump provides the internal pressure, and ram cylinders seal the ends of the tube to trap the pressure for deformation. Benefits of using this process include weight savings, part reduction and an increase in design options. Hydroforming can create unique geometry in a single process.
Ram bending and pressure bending machines place a tube or pipe in a die. The tube or pipe is held at two ends and the ram advances on the central axis to bend the pipe. The pipe or tube is deformed inside and outside of the curvature. Depending on the thickness of the pipe or tube material, this process will deform the tube or pipe into an oval shape. This is the easiest and least expensive bending process. Ram bending is best used for electrical conduit and similar light gauge product.
Heat bending equipment places an induction coil around the tube or pipe and applies a bending force as the object passes through the heated coil.
Sand packing or hot-slab bending machines fill a pipe with sand, cap the ends, and apply heat. The pipe is bent around pins using mechanical force. This process minimizes distortion in the pipe cross section.
Mandrel benders or rotary-draw benders insert a mandrel, a stationary counter-bender die, into a pipe or tube during bending so that the shape and diameter is maintained and the bends are not deformed. The mandrel supports the pipe internally and ensures that the interior curvature of the pipe is the best possible bend and is not deformed. This is the most common bending process. Mandrel bending maintains a good finish and is best used for handrail, ornamental iron work, exhaust pipes, roll cages and all stainless and aluminum tubing.
Roll benders are tube bending and fabrication equipment that use three powered rollers in a triangular arrangement. Unlike mandrel bending, the inside of the tube or pipe is not supported. The top roller exerts downward pressure, while the two bottom rollers push up to deform the pipe. Two or three driven rollers can be used and the process can be either manually or hydraulically adjusted. The process is best used when a large radius is needed such as for awning manufacturing and other round items.
How to Achieve Accurate Pipe Bending
When using a pipe bending machine, maintaining accuracy is crucial. One of the first steps to ensure this is by controlling the quality of the raw materials. It's recommended to purchase all pipes from the same supplier, preferably from the same batch, as this helps keep pipe dimensions consistent. So, how can you achieve accurate pipe bending?
- Select the Right Bending Tools: Choosing suitable pipe bending dies is essential. By using the correct dies, the bending speed and feed rate can be optimized, ensuring greater accuracy during the bending process.
- Control the Sprocket Chain Tension: The tightness of the sprocket chain is a key factor that impacts the precision of pipe bending. Ensuring proper chain tension helps maintain consistent results.
- Fine-Tune the Tools: Regularly adjusting and fine-tuning the tools can help compensate for wear over time, which in turn improves the accuracy of the pipe bending machine.
- Measure Bend Angles and Compensate for Springback: Manually measuring the bend angle and adjusting for springback compensation can lead to more accurate product outcomes.
- Replace Worn Parts: Over time, parts like the slider, bending head, and bending arm may experience wear. Replacing these small components as needed can improve the machine's accuracy and prolong its operational life.
How to Choose the Right Pipe Bending Machine Model?
Selecting the appropriate pipe bending machine is a critical decision that should align with your production needs. As your pipe bending machine supplier, it's our responsibility to recommend the best model for your specific application. To do this, we need to gather information on six key factors, particularly focusing on the diameter, wall thickness, and bending radius—these three are closely interconnected.
- Material Type
- What type of material are you working with? Options include carbon steel, stainless steel, copper, aluminum, or other metals.
- Tube Sizes
- Provide the outer diameter and wall thickness of the pipes you need to bend.
- Bending Radius
- Important note: The bending radius refers to the radius measured from the centerline of the tube. If you're working with an inner radius, please let us know.
- Make sure not to confuse the bending radius with the bending angle!
- Multiple Bend Radii
- If your project requires multiple bend radii, please specify this clearly. However, we recommend using the same radius for a single pipe unless multiple radii are absolutely necessary.
- Product Drawing
- Sharing a detailed product drawing helps us better understand your exact requirements.
- Annual Production Volume
- Knowing the projected yearly output for your project is essential in determining the right machine model that can meet your production goals.
By considering these factors, we can guide you to the most suitable pipe bending machine for your needs.
Conclusion
Purchasing the right pipe bending machine can be challenging, but we hope this guide has equipped you with a comprehensive understanding of all aspects related to these machines. By being informed, you can navigate potential issues associated with importing from China, particularly regarding international after-sales service, which can be complicated.
At Krrass, we are committed to being your trusted partner for sourcing tube bending machines in China. If you have any inquiries or require assistance, please don't hesitate to reach out to us.