What is Plasma Cutter
A Plasma Cutter is a tool that cuts metal using a gas that is heated to very high temperatures and is highly ionized. It transfers the arc power to the workpiece. The high temperature melts the workpiece and blows it off, forming the working state of plasma cutting. Then, the metal is melted using a plasma arc as a heat source.
Plasma cutting refers to the high-speed ejection of inert gas or compressed gas from the nozzle to form plasma, which melts metal for cutting. Because does not oxidize metals like flames, plasma cutting machines can cut various metals that are difficult to cut with oxygen and with different working gases.
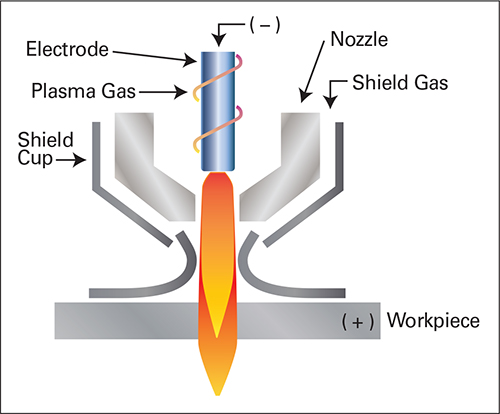
Pros of Plasma Cutter
Better Cutting Quality
Dross, heat-affected zone, top edge fillet, and cut angle are a few major factors affecting cut quality. Especially in the two aspects of scum and heat-affected zone, plasma cutting is far superior to flame cutting. There is basically no scum left on the edge of plasma cutter, and the heat-affected zone is much smaller.
Scum
The plasma process uses hot, electrically charged gas to melt metal and blow the molten metal away from the cut surface. Flame cutting uses the chemical reaction between oxygen and steel to cut, thus producing iron red slag or scum. Because of this process difference, plasma cutting produces less dross, and the dross that adheres to it is easier to remove. This scum can often be easily knocked off without sanding or shoveling, greatly reducing the time required for secondary operations, resulting in higher productivity with fewer sanding operations.
Higher Efficiency
In addition to the time saved in preheating and secondary processing, the cutting and piercing speed of CNC plasma can reach up to 8.5 times that of flame cutting, and the substantial increase in production efficiency can bring huge benefits.
Lower Cost
When analyzing costs, it is important to understand the difference between operating costs and operating costs per part or per meter. So how do you determine the actual cost of cutting a part? Running cost per meter is the cost of everything cut per hour divided by the total length (meters) that can be cut in one hour. The costs involved in cutting include consumables, electricity, gas, labor and ongoing overhead.
Cost per part is the total length of cut required to produce a part times the running cost per meter. Plasma systems cut faster and produce more parts in a given period of time, resulting in a much lower cost per part cut. For handheld cutting, calculating the cost of each job or task provides a better estimate of the savings. The hourly running cost multiplied by the total time required to complete the job equals the job's cost. For oxyfuel cutting, it is important to factor in the preheat time and lengthy secondary processing time into the required time.
Higher Profitability
The lower cost per part of the plasma system translates directly into improved profitability. Cutting each part saves money, which increases profit margins. The more parts you cut per hour, the more you will increase your overall profit.
Easier To Use
For oxyfuel users, it takes time to learn and practice to master setting flame chemistry parameters and maintaining flame chemistry. However, the plasma cutting system is easy to learn and master, and has high stability and easy operation during workpiece cutting. A lot of valuable on-site experience has been integrated into the cutting control process function, which is complete in function and easy to operate.
Higher Flexibility
Plasma cutter systems can cut any conductive metal, including stainless steel, aluminum, copper and brass. Flame cutting machines use the chemical reaction between oxygen and iron in low-carbon steel to cut, so they can only be used to cut low (carbon) steel. In addition, plasma systems can be used for gouging, marking or cutting rusted, painted or even stacked metal. Not only that, but you can also bevel or cut expanded metal with a plasma system, which is difficult to do with oxyfuel.
Higher Security
All types of thermal cutting will produce some odor and noise, such as thermal cutting using cutting table and machine CNC plasma cutter system can choose water cutting bed, which can greatly reduce odor and noise. Most flame cutting should not be done underwater because of the risk of explosion.
The fuel used in flame cutting is a mixture of oxygen and gas. The most commonly used fuel gases are acetylene, propane, MAPP, propylene and natural gas. The most commonly used of these is acetylene because it produces a higher flame temperature and faster perforation than other gases. However, acetylene is an unstable and highly flammable gas that is extremely sensitive to excessive pressure, temperature, and even static electricity. Acetylene explosions can cause thousands of dollars in property damage and serious injury to nearby persons. Some plasma systems typically operate on compressed air and do not require the use of flammable gases.
Cons of Plasma Cutting Machine
But no equipment is perfect, and the plasma cutter is still being improved, and it also has deficiencies. Because its arc light is very strong, it has certain pollution. In addition, the noise generated during processing is relatively large, and there is still a lot of dust, so this is very unfavorable for environmental protection. It should be said that the problems related to environmental protection are relatively big. Now that the equipment is being gradually improved, we also expect it to have a newer and more perfect appearance.
- Plasma cutting will generate harmful gas and arc: The principle of plasma cutting determines the arc intensity, noise and dust during the cutting process, which will pollute the environment to a certain extent. Underwater plasma cutting is generally used for medium and thick plates, so the cutting thickness is limited.
- The verticality of the cutting surface is poor: one side of the cutting surface will have a large bevel, and the verticality is poor.
- During the cutting process, more cutting slag is produced on the surface of the cutting process. Since the process quality is not affected, the slag after cutting must be ground, which also increases labor costs.
- Plasma cutter has a larger heat-affected zone and wider kerf. Not suitable for cutting thin sheets as the sheet will deform due to heat.
- Consumables such as knives are consumed quickly. Now cutting nozzles mainly rely on imports, and the cost is relatively high.
Conclusion
Plasma cutter offers numerous advantages in terms of versatility, speed, precision, and portability, making it a popular choice for metal fabrication and cutting applications. However, it's essential to weigh the pros and cons carefully to determine if plasma cutting is the right solution for your specific needs and budget.