Table of Contents
What is Plasma Cutter
The plasma cutter is one of the most fine-tuned, broadly used, efficient, and versatile tools for cutting even heavy and thick materials quite easily. It’s a tool that can be used for a variety of materials and projects, helping you to safely cut metals that would otherwise seem impossible to cut. Keep reading to discover what is plasma cutting and the main advantages of working with us on your next project.
What is Plasma Cutting
Plasma cutting is a process used to cut steel, stainless steel, and aluminum using a plasma torch. Put simply, gas is blown at a high speed from a nozzle while an electrical arc melts the metal and compressed air to blow away the molten metal. This leaves a cleaner cut than oxygen-acetylene torch cutting.
Tampa Steel & Supply provides this service up to one-half inch thickness. Contact us today to see if we can help you with this service.
The plasma cutter is one of the most fine-tuned, broadly used, efficient, and versatile tools for cutting even heavy and thick materials quite easily. It’s a tool that can be used for a variety of materials and projects, helping you to safely cut metals that would otherwise seem impossible to cut. Keep reading to discover what is plasma cutting and the main advantages of working with us on your next project.
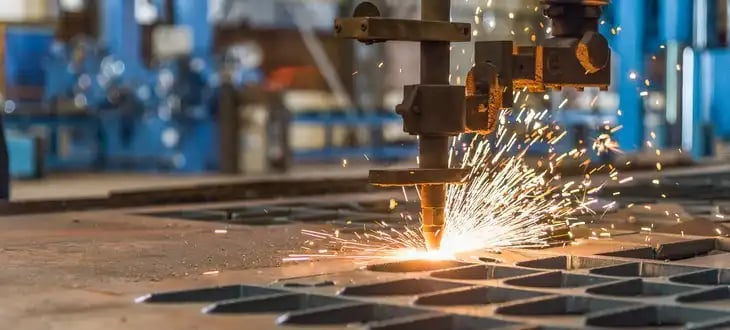
Working Principle
Plasma is a gas that is heated to a very high temperature and is highly ionized. It transfers the arc power to the workpiece. The high heat causes the workpiece to melt and be blown off, forming the working state of plasma arc cutting.
After the compressed air enters the cutting torch, it is distributed by the gas chamber to form plasma gas and auxiliary gas. The plasma gas arc functions to melt the metal, while the auxiliary gas cools the various parts of the torch and blows off the molten metal.
The cutting power supply includes two parts: the main circuit and the control circuit. The electrical principle: the main circuit includes a contactor, a three-phase power transformer with high leakage reactance, a three-phase bridge rectifier, a high-frequency arc ignition coil, and a protection component. Caused by the high leakage reactance, the external characteristics of the power supply are steep. The control circuit completes the entire cutting process through the button switch on the cutting torch:
Pre-venting—main circuit power supply—high-frequency arc ignition—cutting process—discharge arc—stop.
The power supply of the main circuit is controlled by the contactor; the gas flow is controlled by the solenoid valve; the control circuit controls the high-frequency oscillator to ignite the arc and stops the high-frequency operation after the arc is established.
Besides, the control circuit also has the following internal locking functions: the thermal switch operates and stops working.
Features
The plasma cutter with different working gases can cut all kinds of metals that are difficult to cut with oxygen, especially for non-ferrous metals (stainless steel, carbon steel, aluminum, copper, titanium, nickel). The cutting effect is better; its main advantage is that the cutting thickness is not For large metals, the plasma cutting speed is fast, especially when cutting ordinary carbon steel sheets, the speed can reach 5-6 times that of oxygen cutting, the cutting surface is smooth, the thermal deformation is small, and there is almost no heat-affected zone.
Plasma cutter, the available working gas (working gas is the conductive medium of the plasma arc, it is the heat-carrying body, and at the same time the molten metal in the incision must be removed) has obvious effects on the cutting characteristics, cutting quality and speed of the plasma arc. influences. Commonly used plasma arc working gases are argon, hydrogen, nitrogen, oxygen, air, water vapor, and some mixed gases.
The Advantages of Plasma Cutting Machine
More Versatility
Plasma cutting can be performed on diverse types of metal. It uses an electric arc to cut any conductive metal like steel, iron, copper, brass, aluminum, stainless steel, and other durable materials. Plasma can also cut different materials stacked on top of one another with the fastest cutting speed. Techniques like Oxyfuel can’t duplicate this, which is why it’s one of the best options for a variety of metalwork. The cuts a plasma cutter can create are also versatile, allowing you to bring your vision for your artwork or project to life.
Ease of Use
Plasma cutters are portable and you can easily move this wherever the job demands. Some brands are so portable that just one person can easily handle this. As long as the operator of the plasma cutter is well-trained, it’s a very safe and reliable solution for cutting metal.
Fast Cuts
If you compare the cutting speed of a plasma cutter with any cutting tools, you’ll find a plasma cutter is the winner since it’s a time saver and a lot easier than other cutting equipment. A plasma cutter gets the jobs done in a quarter of the time of any other cutting tool. This tool doesn’t need to be preheated before cutting. Thus, it saves cutting time, helping you to complete your project in no time at all.
Precision Cut Quality
It takes an experienced operator with a steady hand to really make a clean cut. Precision or accurate cutting is one of the major advantages of a plasma cutter, especially when it comes to cutting different shapes or angles with sheet metal. When discussing the question of what is plasma cutting, you’ll find that this is one of the top benefits of this type of work.