Introduction
Laser cutting and plasma cutting are two widely used methods in modern CNC (Computer Numerical Control) manufacturing processes. Both are thermal processing techniques employed for material cutting in industrial environments. However, there are some key differences between these two technologies, with the most significant being the source of cutting power: laser cutting machines utilize a strong and narrow laser beam to cut materials, while plasma cutting machines use directed plasma streams for cutting.
Laser cutting technology is suitable for a variety of materials, including ceramics, wood, plastics, and metals, whereas plasma cutting is limited to cutting conductive materials only. Laser cutting offers faster and more precise cutting compared to plasma cutting, and it produces smoother cutting surfaces. Additionally, laser cutting is more suitable for complex cutting tasks. However, plasma cutting machines have lower maintenance costs and simpler mechanical structures, resulting in lower overall costs. While both technologies are primarily used for metal cutting, laser cutting is also commonly employed for processing other materials.
Choosing the right CNC cutting process for your needs may depend on several factors. This article compares laser cutting and plasma cutting in terms of speed, applicable materials, cost, and other factors to help you make a more informed decision.
What is Laser Cutting and How Does it Work
Laser cutting works by directing the highly concentrated energy of a laser beam directed onto a material, producing local melting and separation of the workpiece. Depending on the details of the cutting technique, the laser may melt the material, with an assistive gas stream blowing the melted material out of the way.
Or it may directly change the cut material from solid form to gas (sublimation), with the kerf removed in vapor form. Laser cutting equipment can cut structural and pipe materials as well as thin sheets.
Three main types of lasers are used for laser cutting: CO2, neodymium, and fiber laser systems. Although the laser cutter types are all similarly constructed, they differ in that each kind of laser has a different power range, and each is best suited to certain material types and thicknesses.
With CO2 cutters, the cutting is done using electrically-stimulated CO2. Neodymium, or crystal laser cutters, produce beams through Nd: YVO (neodymium-doped yttrium ortho-vanadate) and Nd: YAG (neodymium-doped yttrium aluminum garnet). Finally, fiber cutters use fiberglass to cut through materials. The lasers are derived from what’s called a ‘seep laser’ and are thereafter amplified through special fibers.
CO2 lasers are the most popular because they can cut a variety of materials, are low-power, and are reasonably priced.
Laser cutting is widely used in sectors like electronics, medicine, aircraft, and transportation. Due to the laser’s ability to create precise cuts and finishes, it is mostly used to cut metals like tungsten, steel, aluminum, brass, or nickel. Lasers are also used to cut wood, silicon, ceramics, and other non-metals.
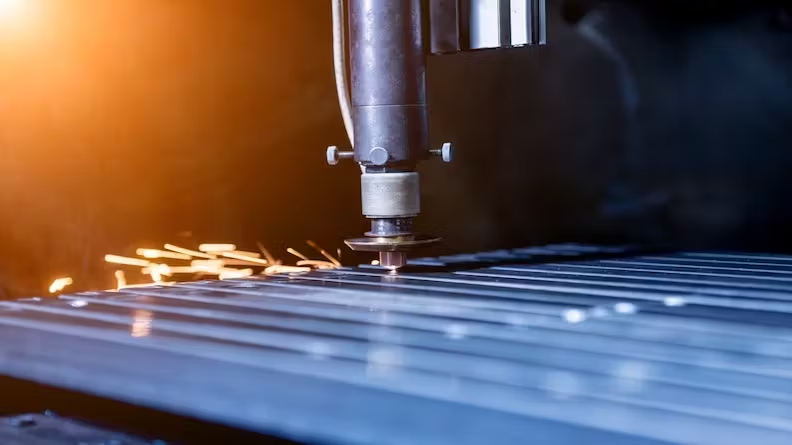
What Is Plasma Cutting and How Does It Work
Plasma cutting is a thermal cutting process that uses a high-velocity jet of ionized gas, known as plasma, to melt and sever metal materials. The basic principle involves passing an electrical arc through a gas that is forced through a constricted opening, resulting in the formation of plasma. Here's how it works:
- Generation of Plasma: Plasma cutting systems consist of several components, including a power supply, gas delivery system, and torch. The power supply generates an electrical arc, which is directed through the torch and into the gas passing through it. The gas, typically compressed air, nitrogen, or argon, becomes ionized and transforms into plasma when it reaches the high temperature of the arc.
- Plasma Jet Formation: The plasma jet exits the torch nozzle at high velocity, typically reaching speeds of up to 20,000 feet per second. This jet of plasma is extremely hot, with temperatures exceeding 30,000 degrees Fahrenheit (16,650 degrees Celsius).
- Material Cutting: As the plasma jet makes contact with the metal workpiece, it rapidly heats the material to its melting point. Simultaneously, the kinetic energy of the plasma jet blows the molten metal away from the cut, creating a narrow kerf.
- Gas Flow: To maintain the cutting process, a secondary gas, often oxygen or nitrogen, is usually directed through the torch alongside the plasma. This gas assists in the removal of molten metal from the kerf and helps to cool the cut, preventing damage to the workpiece.
- Control and Precision: The entire cutting process is controlled by a CNC system, which precisely directs the movement of the plasma torch over the workpiece according to programmed cutting paths. This CNC control ensures accuracy and repeatability in the cutting process, allowing for the creation of intricate shapes and precise cuts.
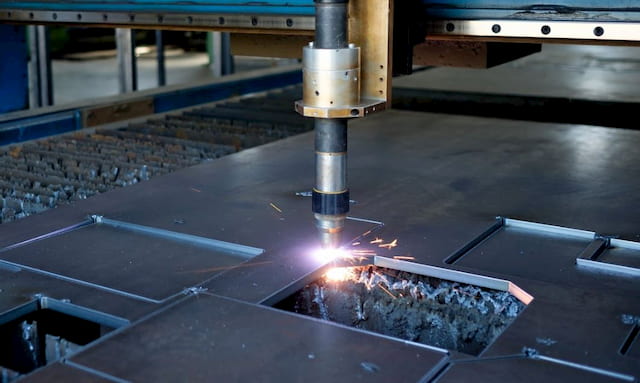
Plasma Cutting vs Laser Cutting: Pros & Cons Analysis
Pros of Laser Cutting
- Accuracy: The energy of a laser beam is concentrated on a single tiny area, penetrating the material and cutting it. This process produces a thin cutting seam (kerf) in the workpiece, as opposed to the wider kerf produced by plasma cutting. The thinner cut made by a laser makes it useful for complex, delicate cutting tasks that cannot be accomplished by a plasma cutter.
- Wide Range of Materials: Laser cutters are capable of cutting a wide range of materials, including: metal, wood, plastics, and ceramics. Plasma cutters, on the other hand, are limited to cutting conductive materials.
- Speed: Laser cutters are a more energy-efficient and faster option for cutting metal compared to plasma cutters, making them a better choice for the environment.
Cons of Laser Cutting
- Reflective Materials: Compared to plasma cutting, laser cutting does not perform as well on highly reflective surfaces like metal.
- Material Thickness: In general, laser machines do not have enough power to cut through materials thicker than 19 mm, whereas plasma cutters are able to cut metal plates with a thickness of up to 38 mm.
- Capital Investment: Capital costs for a laser cutter are significantly higher than for a plasma cutter.
Pros of Plasma Cutting
- Cost: Laser cutters are typically more expensive to operate than plasma cutters.
- Thicker Plates: In general, plasma cutters are able to cut thicker plates (up to 38 mm) compared to laser cutters that can cut 12.7 mm thick aluminum, 19 mm thick stainless steel, and 25.4 mm thick steel.
- Low Maintenance: Plasma technologies require significantly less maintenance than laser cutters.
Cons of Plasma Cutting
- Larger Kerf: The larger kerf size of plasma cutting means that it is less accurate, and therefore is more limited compared to laser cutting.
- Limited Functionality: Plasma cutting does not offer engraving functionality as laser cutting machines do.
- Radiation: Plasma cutters, unlike laser cutters, create radiation. This necessitates the use of protective equipment, including goggles or glasses for workers.
- Limited Materials: Plasma cutters are limited to use on electrically conductive materials.
Laser Cutting vs Plasma Cutting: A Comprehensive Comparison
Principle of Operation
- Laser Cutting: Utilizes a high-power laser beam to melt, burn, or vaporize material along a predetermined path.
- Plasma Cutting: Employs a high-velocity jet of ionized gas (plasma) to melt and sever metal materials.
Cutting Speed and Efficiency
- Laser Cutting: Generally offers higher cutting speeds than plasma cutting, making it suitable for rapid production and intricate designs.
- Plasma Cutting: While typically slower than laser cutting, plasma cutting excels in cutting thicker materials and is often more cost-effective for heavy-duty applications.
Material Compatibility
- Laser Cutting: Suitable for a wide range of materials, including metals, plastics, wood, ceramics, and composites.
- Plasma Cutting: Primarily used for cutting conductive materials such as steel, stainless steel, aluminum, copper, and other alloys.
Cutting Thickness
- Laser Cutting: Preferred for thin to medium material thicknesses, typically up to 1 inch (25 mm) for steel.
- Plasma Cutting: Excels in cutting thicker materials, with capabilities ranging from 0.1 inch (2.5 mm) to several inches, depending on the power of the plasma cutter.
Precision and Edge Quality
- Laser Cutting: Offers high precision and superior edge quality, with minimal distortion, heat-affected zones, and burrs.
- Plasma Cutting: Provides good cutting precision, but the edge quality may not be as clean as laser cutting, often requiring secondary finishing operations.
Cost Considerations
- Laser Cutting: Generally involves higher equipment and operating costs due to the complexity of laser systems and maintenance requirements.
- Plasma Cutting: Typically more cost-effective for cutting thicker materials and large-scale production runs, with lower initial equipment costs and reduced consumable expenses.
Environmental Impact
- Laser Cutting: Produces minimal smoke, fumes, and noise during operation, making it environmentally friendly.
- Plasma Cutting: Generates more smoke, fumes, and noise compared to laser cutting, requiring proper ventilation and safety measures.
Conclusion
This article outlined the disparities between laser cutting and plasma cutting, elucidating their functionalities and applications within manufacturing. For further insights into laser cutting and plasma cutting techniques, feel free to reach out to Krrass Machinery.
Krrass Machinery offers an extensive array of manufacturing solutions, encompassing sheet cutting and various value-added services tailored to fulfill your prototyping and production requisites. Explore our website for additional information or to solicit a complimentary, obligation-free quote.
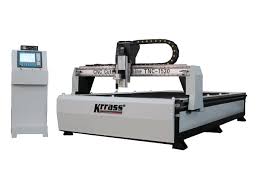