Plate bending machines, often called “roll bending machines”, “plate rolling machines” or “rolling machines” are a cornerstone of modern manufacturing and have had a place in manufacturing since the Industrial Revolution. These impressive machines, which are designed to bend metal sheets into curved structures, play an especially important role in various shaping industries such as windmill and shipbuilding productions. That’s because plate rolls are indispensable in the fabrication of large curved metal components. From early invention to modern evolution, plate rolls stand as essential tools for those who rely on the fabrication of curved metal parts.
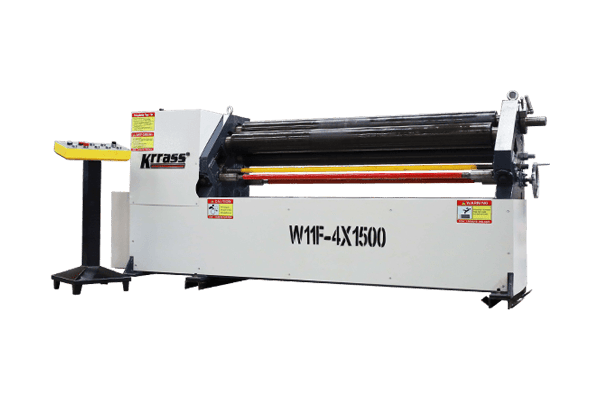
How Do Plate Bending Machines Work
At the heart of these machines lie three main components: the rolls, housing, and motors, all working together to achieve seamless rolling operations. The rolls, typically arranged in a triangular formation consisting of three or four rolls, exert pressure on the metal plate to deform it gradually. These rolls can be adjusted to accommodate different plate thicknesses and curvatures, ensuring versatility in the manufacturing process. The housing encloses the rolls, providing stability and safety during operation, while the motors power the rolls to execute the rolling process.
The rolling process itself involves feeding the metal plate between the rolls, which then applies pressure to bend the material gradually. As the plate passes through the rolls, it undergoes plastic deformation, conforming to the curvature dictated by the positioning of the rolls. The degree of curvature can be precisely controlled through adjustments to the rolls’ positions and pressure exerted, allowing for the creation of different shapes and sizes of curved metal plates. This process is essential in the fabrication of cylindrical and conical structures commonly found in industries such as windmill production, aerospace, and shipbuilding.
Different types of rolls are used based on the specific requirements of the material and the intended application. For instance, softer metals like aluminum or copper require rolls with smooth surfaces that are preferred for minimizing surface imperfections and ensuring a uniform finish. Conversely, for harder materials such as stainless steel or titanium, rolls with serrated or grooved surfaces may be used to enhance traction and prevent slippage during the rolling process. Additionally, specialized products such as cone bending devices are utilized for unique applications, offering enhanced flexibility and precision in shaping metal plates to meet specific manufacturing needs.
The Importance of Plate Rolls in Windmill Manufacturing
Plate bending machines play a vital role in windmill manufacturing, contributing to the production of various components essential for the construction and operation of wind turbines. One significant application of plate rolling machines in this industry is in the fabrication of turbine tower sections. Wind turbine towers are typically constructed from cylindrical or conical sections made from heavy-duty steel plates. The plate roll is utilized to bend the steel plates into the required diameter for these tower sections. Due to the necessary structural integrity of the towers in high wind areas, the ability to produce large-diameter sections from heavy-duty steel with high accuracy is crucial.
Moreover, plate rolling machines are instrumental in manufacturing other key components of wind turbines, such as the nacelle and hub assemblies. The nacelle houses crucial components of the wind turbine, including the gearbox, generator, and control systems. It is often constructed from curved steel plates that are formed using plate roll machines. Similarly, the hub assembly, which connects the rotor blades to the main shaft, requires precision-formed components that can withstand the rotational forces generated by the blades. Plate rolling machines enable the fabrication of these components with the necessary strength, durability, and dimensional accuracy to ensure reliable performance and longevity of the wind turbine system.
In addition to structural components, plate rolling machines are also employed in the production of wind turbine rotor blades. While the blades themselves are typically manufactured using composite materials, the blade root sections that attach to the hub assembly are often made from metal plates. Plate rolling machines are used to form these sections into the required shape and curvature, facilitating the seamless integration of the blades with the rest of the turbine assembly.
Plate Rolls and Ship Manufacturing
Much like windmill manufacturing, shipbuilding relies heavily on the use of plate rolls, offering unparalleled capabilities in shaping steel to create essential components for marine vessels. One of the primary applications of plate rolls lies in crafting the hulls, bulkheads, and tanks of ships. Rolled steel, prized for its tight tolerance application and resilience, forms the foundation of these critical structures, ensuring the integrity and durability of the vessel. The ability to precisely shape steel sheets into curved sections enables shipbuilders to construct seamless hulls that are not only strong but also aerodynamic which is essential for navigating diverse maritime environments.
The capability of plate rolls allows for the creation of complex and streamlined vessel designs that enhance performance and efficiency at sea. By utilizing plate rolls, shipbuilders can achieve precise shapes and contours that improve hydrodynamics, reduce drag, and ultimately enhance the ship’s fuel efficiency and maneuverability. This demonstrates the indispensable role of plate rolls in modern shipbuilding, where innovation and precision are paramount to meeting the rigorous demands of the maritime industry.
Beyond hull construction, plate rolls find extensive application in the fabrication of various other ship components. From decks and superstructures to internal partitions and compartments, rolled steel serves diverse functions throughout the vessel’s structure.
The versatility of plate rolls enables shipbuilders to manufacture intricate designs and configurations that optimize space utilization, structural integrity, and operational efficiency. Thus, plate rolls play a crucial role in the process of shipbuilding, contributing to the creation of seaworthy vessels that meet the rigorous standards of safety, performance, and reliability required in maritime transportation.
Advancements in Plate Roll Technology
With the advent of computer numerical control (CNC) technology, plate rolls have become even more versatile and precise. CNC-controlled plate rolls allow for automated operation, where complex bending sequences can be programmed and executed with minimal manual intervention. This not only increases productivity but also enhances accuracy and repeatability, ensuring consistent quality in the manufactured components. This also provides the benefit of easing training on newer plate roll operators.
Modern plate rolls also utilize hydraulic systems to exert the necessary force for bending metal plates. Hydraulic cylinders provide high-pressure control, allowing for precise adjustment of bending parameters such as pressure and speed. Additionally, hydraulic systems offer greater power and efficiency compared to traditional mechanical methods, enabling the processing of thicker and tougher materials with ease.
The incorporation of digital monitoring and control systems has further enhanced the performance and reliability of plate rolls. Sensors embedded within the machine can detect parameters such as plate thickness, roller pressure, and bending angle in real time, providing feedback to the control system for immediate adjustments. This level of automation not only streamlines the manufacturing process but also improves safety by alerting operators to any deviations or abnormalities.
Conclusion
While we went over two manufacturing industries that utilize plate rolls, there are numerous more such as aviation, pipe fabrication, nuclear power, pressure vessels, construction machinery, and refrigeration technology. To all of these industries, plate rolls are a cornerstone of their manufacturing. From shaping steel plates for ship hulls to fabricating tower segments for windmills, these machines play a vital role in realizing complex designs and meeting stringent quality standards.
With ongoing advancements in technology plate rolls continue to drive innovation and progress in manufacturing, shaping the future of industry and infrastructure alike. If you are in the market for a plate roll or want to learn more about their capabilities, reach out to us today and get your free quote started.