What is A Plate Roller?
A plate roller, also known as a plate bending machine or sheet metal roller, is a mechanical device used to bend or roll metal plates or sheets into curved or cylindrical shapes. It is commonly used in metalworking and fabrication processes to produce cylindrical or conical shapes for various applications in industries such as manufacturing, construction, automotive, and aerospace.
Plate rollers typically consist of a set of rollers arranged in a specific configuration, such as three-roll or four-roll designs. The metal plate or sheet is fed between the rollers, and hydraulic or mechanical pressure is applied to bend the material into the desired shape. Plate rollers come in various sizes and configurations to accommodate different material thicknesses, widths, and bending requirements.
Plate rollers are versatile machines capable of producing a wide range of curved shapes, including cylinders, cones, and arcs. They are commonly used to fabricate components such as pipes, tanks, cylinders, pressure vessels, and structural elements. Plate rollers play a crucial role in the metal fabrication industry, enabling the production of complex and precise curved metal components for various applications.
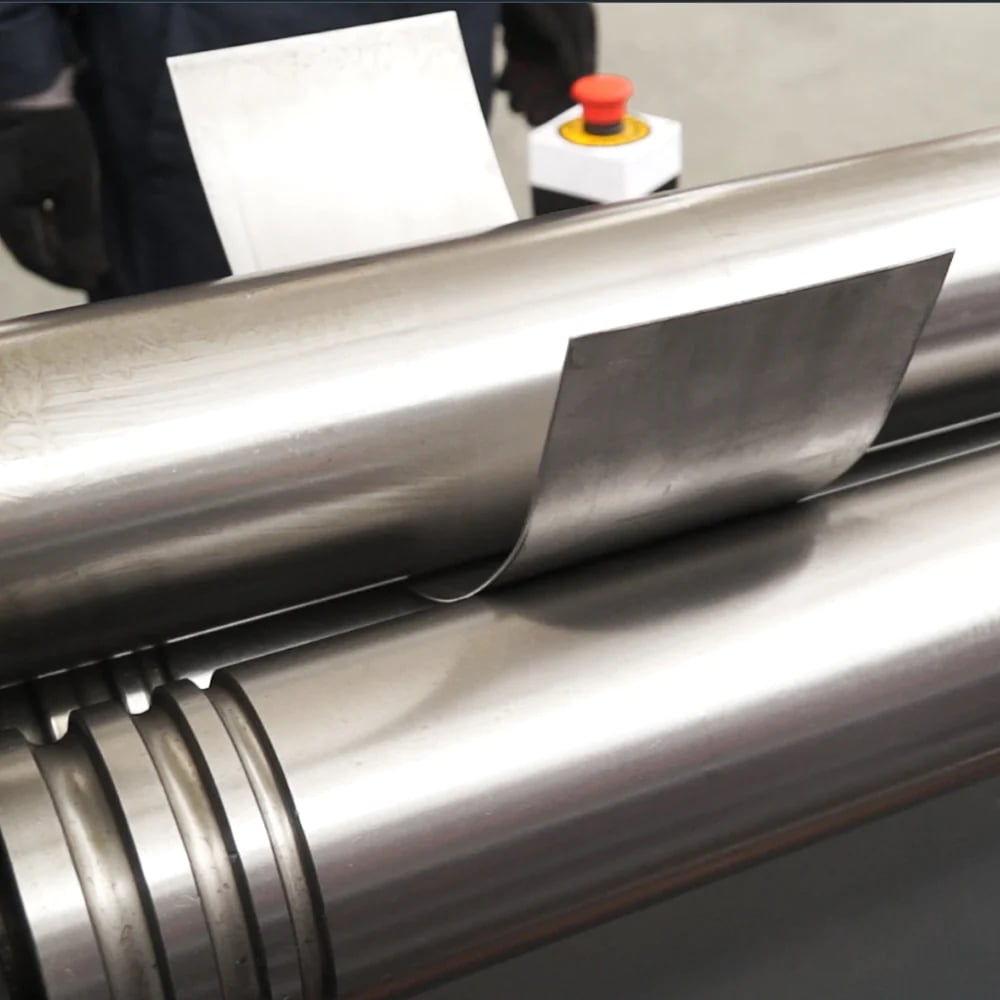
How to Buy A Plate Roller
When considering purchasing a plate roller, also known as a plate bending machine or sheet metal roller, it's essential to take several factors into account to ensure you select the right machine for your needs. Here's a comprehensive buying guide to help you make an informed decision:
Capacity and Size:
Determine the maximum thickness and width of the plates or sheets you'll be bending. Choose a plate roller with a capacity that matches or exceeds your requirements to ensure it can handle your intended workload.
Type of Material:
Consider the types of materials you'll be working with, such as mild steel, stainless steel, aluminum, or other alloys. Ensure the plate roller you choose is capable of bending the materials you'll be using.
Number of Rolls:
Decide whether you need a three-roll or four-roll plate roller based on your bending requirements and preferences. Three-roll rollers are suitable for simple bending operations, while four-roll rollers offer greater precision and control, especially for complex bends.
Roller Configuration:
Choose between horizontal and vertical plate rollers based on the orientation of your workpieces and the space available in your workshop. Horizontal rollers are ideal for long, narrow plates, while vertical rollers are better suited for short, wide plates.
Accuracy and Precision:
Look for plate rollers with features that ensure accurate and precise bending, such as digital readouts, adjustable bending speeds, and hydraulic or CNC controls. These features can help minimize errors and improve the quality of your finished products.
Ease of Use and Maintenance:
Consider the machine's user-friendliness and ease of maintenance. Look for features such as intuitive controls, quick-change tooling, and accessible components for easy operation and servicing.
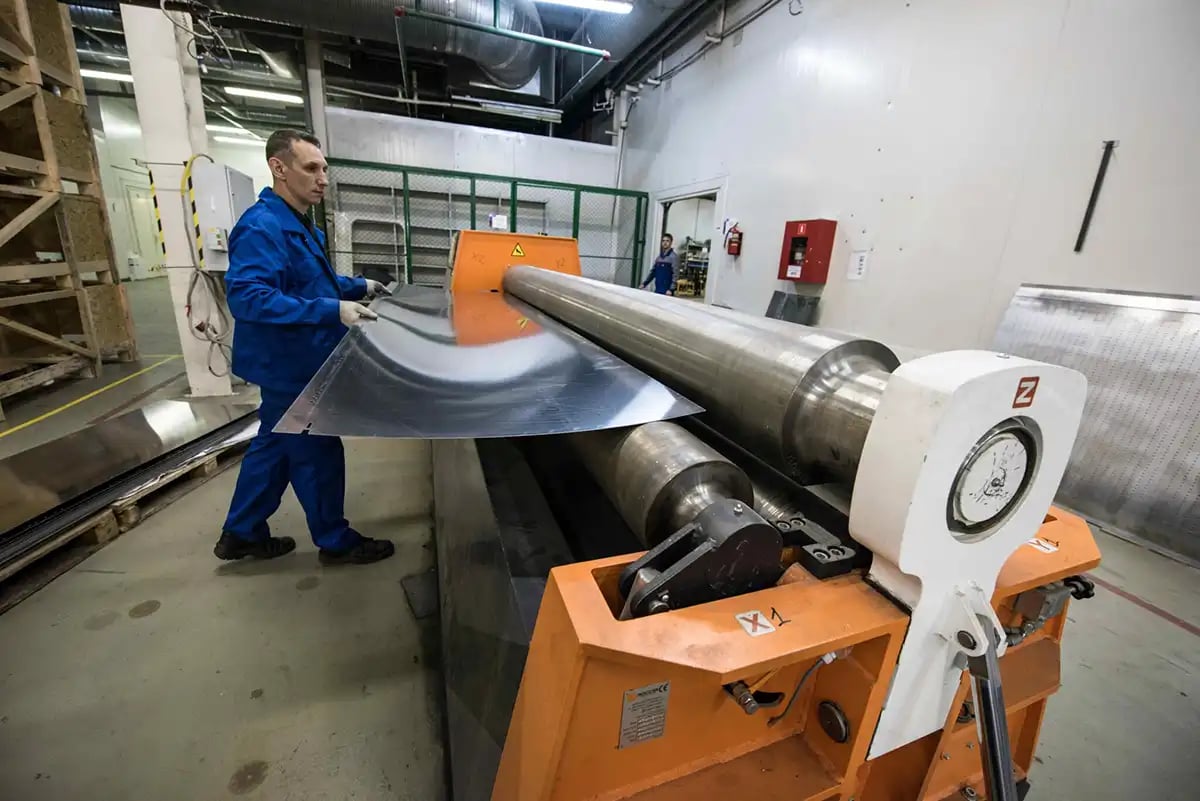
Safety Features:
Prioritize safety features such as emergency stop buttons, safety guards, and overload protection mechanisms to protect operators and prevent accidents during operation.
Brand Reputation and Support:
Choose a reputable manufacturer with a track record of producing high-quality plate rollers and providing reliable customer support. Research customer reviews, testimonials, and warranty policies to assess the manufacturer's reputation and after-sales service.
Price and Value:
Compare prices from different manufacturers and suppliers to find a plate roller that offers the best value for your budget. Consider factors such as machine quality, features, and support services when evaluating the overall value of a machine.
Additional Features and Accessories:
Consider any additional features or accessories that may enhance the functionality and versatility of the plate roller, such as digital control systems, special tooling options, or optional attachments for specific bending applications.
By carefully considering these factors and conducting thorough research, you can choose a plate roller that meets your requirements, improves your productivity, and delivers excellent results for your metal fabrication projects.