In the industrial machinery market, the plate rolling machine price is a crucial aspect that demands careful consideration. Plate rolling machines play a significant role in various metalworking and manufacturing processes, enabling the shaping of metal plates into desired forms. However, understanding the factors that influence plate rolling machine price is essential for both manufacturers and purchasers. From the machine's technical specifications and capabilities to the brand reputation and market trends, multiple elements interact to determine the final cost. This article aims to provide a detailed and comprehensive analysis of these influencing factors and offer a practical buying guide to assist those involved in the procurement of plate rolling machines.
What is Plate Rolling?
Plate rolling and plate forming is a fabrication process that shapes metal plate materials into cylindrical, conical, elliptical and other shapes. Many kinds of metals can be rolled, these can be carbon steels, stainless steels (including duplex), alloys, heat resistant materials, wear resistant plates and aluminium. These can shaped using a plate rolling machine, through steel rollers, to create a shape to specific requirements.
Metal plate bending, or plate rolling, is a fundamental process in metal fabrication. This process offers immense versatility in shaping flat sheets of metal into curved or cylindrical forms. The transformative technique involves applying force to a metal plate to gradually bend it to the desired angles. Through precise manipulation of the material, complex shapes can be achieved with remarkable accuracy, making plate bending indispensable in manufacturing.
The process of sheet metal rolling relies on the principle of plastic deformation, where the material undergoes permanent changes in shape without fracturing. As the plate is fed through the rollers of the bending machine, pressure is applied, causing the metal to yield and bend. The curvature of the bend is determined by factors such as the diameter of the rollers, the thickness and composition of the metal, the position and pressure applied by the bending rollers, and the speed at which the plate is fed through the machine. This used to be a very skilled process, but innovations have made this easier.
One of the key advantages of metal plate bending is its ability to produce uniform and consistent curves across large metal sheets. This makes it an ideal method for creating components such as pipes, cylinders, tanks, and structural elements with smooth, continuous contours.
Additionally, plate bending allows for the fabrication of complex geometries that would be challenging or impossible to achieve using other machines such as press brakes. Whether it’s shaping metal for architectural structures or crafting specialized components for machinery, metal plate bending offers unparalleled flexibility and efficiency in transforming raw materials into functional products.
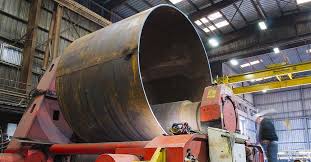
How a Metal Plate Rolling Machine Operates?
Adjusting the Bending Force Based on the Target Radius
The first crucial step in the operation of a metal plate rolling machine is to determine and set the appropriate bending force. This is directly related to achieving the desired radius of the bend, whether it's an inside or outside diameter. The operator needs to carefully evaluate the workload of the machine, taking into account essential variables such as the thickness and the specific material of the metal plate. This assessment is fundamental as it paves the way for the machine to apply the correct amount of pressure, which is vital for accurately and effectively forming the metal plate into the intended shape.
Positioning the Metal Plate on the Table for Stable Bending
After setting the bending force, the next significant step is to place the metal plate precisely on the table of the rolling machine. This step is of great importance as it serves to prevent any undesired movement or displacement of the metal plate during the bending process. When the metal plate is properly aligned and well-supported on the table, it enables the achievement of uniform bending along the entire length of the plate.
This, in turn, minimizes the occurrence of distortions or irregularities in the final bent product. Moreover, securely fastening the metal plate in position not only ensures the quality of the bend but also enhances the safety of the operation by reducing the potential for accidents. With the metal plate firmly seated and clamped between the upper and lower rolls, the operator can then proceed with the bending process with certainty, expecting to obtain precise and high-quality results.
Pre-Pinching / Pre-Bending: A Key Prelude to Bending
Before starting the actual bending, operators use pre-pinching or pre-bending. They slightly bend the metal plate edges inward before feeding it into the machine. This reduces wrinkles and irregularities at curved edges, enables a seamless transition between flat and curved parts, optimizes the bending process, and minimizes distortion by reducing strain on the plate.
Bending via the Metal Plate Bending/Rolling Machine
With the bending force set, plate positioned, and edges pre-bent, the workpiece is ready for bending. When the operator starts the machine, the plate is fed through rollers that apply regulated pressure to shape it as desired. Minor adjustments are made as needed to meet project specs. The rollers ensure uniform pressure for smooth bends without harming the material's integrity. Given the process's importance and the machine's cost, an experienced operator is advisable for accurate results and efficient operation.
Application scenarios of Plate Roller
This machine efficiently shapes metals into cylindrical or conical forms. It ensures uniform thickness and precise bending. Adopting this technology can vastly improve production speeds and product uniformity. In this blog, we will take a look into the varied applications of plate rolling machines in different industries.
How are Plate Rolling Machines Used in the Transportation and Infrastructure Sector?
Plate-rolling machines are essential in the transportation and infrastructure sector. They transform flat metal plates into structural components. Here are the ways they impact road/railway tankers and earth-moving equipment.
Road / Railway Tankers
- Plate rolling machines enhance the manufacturing process of road and railway tankers.
- These machines curve flat metal plates into cylindrical or multi-radius tanker bodies.
- This process ensures the tankers are robust enough to safely transport liquids and gasses.
Earth-Moving Equipment
- Plate rolling machines form cylindrical shapes and curved sections in the metal components of excavators and bulldozers.
- These machines enhance the durability of equipment used in challenging job sites.
- By using these machines, manufacturers can guarantee the longevity and performance of their equipment.
What Role Do Plate Rolling Machines Play in the Aerospace Industry?
These machines facilitate the creation of essential aerospace components. Here are the ways they shape aerospace manufacturing.
Manufacturing Aircraft Structures
- Plate rolling machines form critical parts for aircraft, including fuselages and wing components.
- Their precision ensures the structures are both lightweight and robust.
- The performance of plate rolling machines ensures aircraft meet rigorous safety and performance standards.
Rocket Shells
- Rocket construction relies on the curvature provided by plate rolling.
- This method allows for the creation of seamless, aerodynamic rocket shells.
- These machines ensure rockets can withstand the extreme conditions of space travel.
Fabricating Engine Components
- Plate rolling machines are crucial in fabricating various aircraft engine components.
- They precisely shape metal plates into parts like casings.
- This ensures engine components fit perfectly and function reliably under high stress.
Factors Affecting Plate Rolling Machine Price
Here are seven factors that you should take into consideration before buying a metal plate bending machine.
1. Technical Capabilities
A plate-bending machine can streamline your production process, reduce material waste, and achieve accurate and consistent results. Note that plate rolling machines' technical capabilities and quality can vary depending on the manufacturers.
The bend plates' quality is directly proportional to the machine's quality. This in turn affects overall efficiency, including providing accurate results, minimizing risks, and optimizing long-term productivity. Thus, it is crucial to invest in a reliable and high-quality machine.
2. Materials Used
The choice of top-notch material plays a key role in manufacturing a plate bending machine. Not all manufacturers will use top-quality materials, and the quality also affects the plate rolling machine's price.
Imagine constructing a machine with the finest materials available, carefully handpicking each component. The result? A magnificent masterpiece that surpasses expectations in every aspect.
3. Manufacturing Process
Before purchasing a machine, will you consider the machine alone or the entire manufacturing process?
The process of production and the necessary backend checks is crucial. To ensure that you're acquiring a quality machine that prioritizes safety, ask yourself these questions before making a purchase.
- Design Verification: Does the machine's design meet the necessary functionality and safety requirements?
- Material Inspection: Is the material providing strength, durability, and suitability to the product?
- Component Testing: Is the manufacturer testing individual components for proper operation and reliability?
- Assembly Evaluation: Does the manufacturer inspect the machine's assembly for proper alignment and secure connections?
- Performance Testing: Does the machine provide bending accuracy, precision, and repeatability?
- Safety Assessment: Is the manufacturer assessing safety features and compliance with regulations?
- Document Quality Control: Is the manufacturer documenting all inspections, tests, and certifications thoroughly?
- Final Inspection and Approval: Is there a final assessment conducted to check the machine's overall quality before granting approval for its use?
4. Post-Installation Service
What if your machine stopped working? Wouldn't you want to have support technicians ready for when you have a problem with the machine? After all, it is a huge investment. When buying a plate bending machine, post-installation service is one of the most important factors to consider.
You need to know how long it will take for the manufacturer to provide this service to you. What if it takes more than your expected time? Post-installation services will ensure peak performance, safety compliance, and production or turnaround time. So, contact the manufacturer or research these services before you purchase a machine.
5. Uptime & Durability
Let's get back to the scenario where you buy a ₹20 lakh plate bending machine. This is a huge chunk of your gross investment. Now the machine stops working after a few years, which was not worth your money. Thus, the amount of time your machine was operational has drastically reduced than what you expected.
Moreover, you would experience a disrupted workflow and a delayed project timeline due to the in-between machine breakdowns and repairs, leading to financial losses. Will this be worth your investment? No! So, for the long-term success of your project, you need to invest in a reliable and durable machine.
6. Delivery Time
Last, but not the least, imagine you purchased a plate rolling machine today, which is cost-effective for your total investment. But, the manufacturer delivers the machine months later.
What are the factors that will affect a delayed delivery time? Will it affect effective operations, ease resource planning, or ensure business continuity? With such a huge investment, like a plate bending machine, wouldn't you want to have on-time delivery?
7. Company’s Reputation & History
Are you willing to buy a product with negative customer feedback or poor post-sales service? Of course, not!
A company's reputation & history play a major role when investing a king's ransom for one machine.
When choosing a manufacturer, consider customer feedback, machine design efficiency, and client support. It's also crucial to assess whether the manufacturer offers reliable technical support and has long-term stability as a company.
It's important to acknowledge that these are crucial factors beyond the price when buying a plate rolling machine. While it may not be the most pleasant thing to think about, ignoring these elements could lead to a less efficient and effective machine in the long run.
What Kind of Plate Rolling Machine Do You Need?
When searching for a plate roll it’s important to know the type of plate rolls available. In a recent article entitled: What type of plate roller fits your production needs we discuss just that. Typically, plate bending rolls come in two different types: single and double-pinch. However, in terms of style and geometry, there are three-roll variable translating, three-roll initial-pinch, three-roll double-pinch, two-roll systems, four-roll plate machines, and three-roll pyramid. When deciding which equipment to buy, it is crucial to match the machine style to its application. So, besides knowing the type or style of the machine you want, you need to consider other things.
Material Type
The material of the sheet to be rolled is a crucial factor that will help determine the design of the rolling plate machine you choose. With the strength of today’s steel becoming much higher than ever, the steel plate rolling machine you select should also be able to produce high levels of pressure for it to yield the desired results. As such, there are essential factors that manufacturers need to consider when purchasing a metal sheet roller. These include the yield strength, temper brittleness of the metal, and the use of the sheet. This is essential, primarily due to the transformation of the smelting industry over the last decades.
The diameter and thickness of the plate for rolling
Essentially, the smaller the diameter of the roll, the more pressure you’ll need and thus the more yield in the rolls you will have. If you want to roll a thick plate with a small diameter, you should pay attention to how the upper roll and how the structure of the plate rolling machine are positioned. This is because these are the two crucial elements that affect the size of the opening and its quality. Theoretically a plate rolling machine can roll material to a diameter of 1.5X the top roll diameter and in some applications even down to 1.3X However this is entirely dependent on the material itself and the capacity of the plate rolling machine you are using.
Horizontal and vertical support forces
The support you offer to your metal sheet roller will also determine how effective your rolling processes will be, and this is considered in terms of vertical or horizontal forces. When you choose a plate roll machine that has adequate support, in both side supports and overhead supports it will reduce the workload and save you some valuable labor costs. For instance, when you’re rolling a cylindrical product with a diameter that is 200 times the thickness of the plate, its weight helps it to be bent to the desired size. Therefore an overhead support is required. If there is no adequate support, the ideal diameter can’t be achieved.
Best Practices for Buying Used Plate Rolls
Since new plate rolling machines are relatively expensive, you may opt to buy a used machine and, thus, lower the initial investment cost. However, you need to check out the following:
- Ensure that all handling options are effective. You should ensure that any motorized loading tables, overhead supports, part ejectors, plate alignment systems, and infeed conveyors are not only functional but also optimal for your specific application.
- Inspect the rollers and see if they have been damaged. Although they are hardened, roll surfaces and cone rolling devices can be damaged, especially when narrow pieces are passed through them. Damage can occur either to scoring the surfaces which will be reprinted in future work, or by bending the roll out of roundness. Severe damage can occur by breaking the roll ends over excessive over-tonnage applications..
- You also need to ensure that all the safety devices are intact. These include emergency-stop buttons such as low-voltage control circuits, safety tripwires, safety mats, light curtains and detached operator consoles.
- Check whether welding has been done on the plate roller. Some welders consider it time-saving to weld materials on top of the roller, rather than take the rolled items to a second station. Although this may be convenient, it may damage electrical systems and controls with hot weld splatter. It is vitally essential to ensure that the machine you are buying was used carefully if any welding occurred, as some of its controls and electrical systems may be faulty or on the verge of being damaged.
At Krrass Machinery Sales we know Plate Rolls and rolling. Call us today for more information on Plate Rolls and help selecting the right plate roll for your parts and budget.