What Plate Shearing Machine Used For
Sheet metal and plate shearing machines are used in many fabricating and sheet metal operations. Before selecting a shearing machine, several factors must be evaluated, including the type of shear, required capacity, productivity enhancement options, and safety.
Shear type is determined by many factors, including the material length that it can process and the thickness and type of material that it can cut.
Shearing machines can be broken down into types by sheer design and the drive systems that are used in the design. Two design types are common to power squaring shears: the guillotine (also known as the slider unit) and the swing beam.
Shearing Process of Common Plate Shearing Machine
Shear Design
The guillotine design (see Figure 1) uses a drive system to power the moving blade down and in a position almost parallel to the fixed blade during the entire stroke. Guillotine machines require a gibbing system to keep the blade beams in the proper position as they pass each other.
The swing beam design (see Figure 2) uses one of the drive systems to pivot the moving blade down on roller bearings. This eliminates the need for gibs or ways to keep the blades in proper position as they pass.
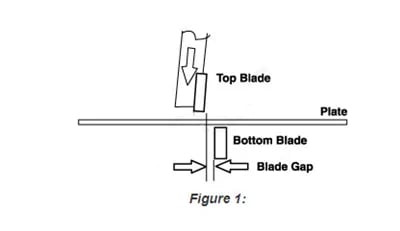
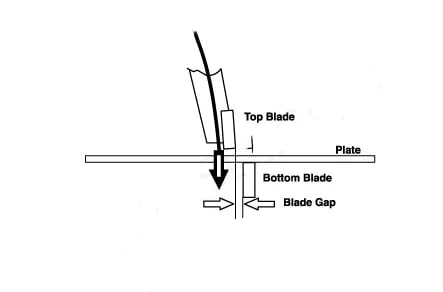
Shear Drive Systems
The drive system powers the moving blade through the material to make a cut. Drive systems can be categorized into five basic types: foot or manual, air, mechanical, hydromechanical, and hydraulic.
Foot Shear
A foot shear is engaged when the operator steps on a treadle to power the blade beam to move down to make a cut. Foot shears are commonly used in sheet metal applications ranging up to approximately 16-gauge capacity and with lengths up to 8 feet, although 8-foot machines are not as common as those with shorter capacities.
Air Shear
To use an air shear, an operator steps on a pedal that activates air cylinders to make a cut. Shop air or a freestanding air compressor is used to power an air shear.
Air shears are used in shops for cutting material up to about 14 gauge with lengths up to 12 feet. Air shears have a simple drive design, and they provide overload protection. Overload protection is designed for proper operation and generally for straight-down loads. For instance, even when cutting a material thickness that is within a machine's capacity, the equipment can be damaged if the material is cut without using a hold-down or if the blade gap is not properly adjusted. This applies to hydraulic machines as well.
Direct-Drive Mechanical Shear
This shear operates when the operator steps on a pedal to turn on the motor that brings the beam down to make a cut. The motor turns off at the end of the cycle, and the blade beam returns to the top of the stroke. This design is suitable for shears when they are not in constant use because the machine uses power only when it is activated.
Evaluating Shears
One consideration used in evaluating shears is the capacity required for specific jobs. The machine specifications for almost all shears list capacities for mild steel and stainless steel. To compare a fabricator's requirements to those of the machine, the fabricator's material specifications must be checked against the machine's capacity.
Some shear capacities are rated on mild steel, which may have 60,000 pounds per square inch (PSI) tensile strength, while others are rated for A-36 steel or 80,000 PSI tensile strength. Capacities for stainless steel are almost always less than those for mild or A-36 steel. It may be surprising to some metal fabricators that certain grades of aluminum require as much power to shear as is required to cut steel. It is always best to check with the shear's manufacturer when there are concerns about capacity.
The rake angle of the blade (the angle of the moving blade as it passes the fixed blade) is important in determining the quality of the cut. Generally, the lower the rake angle, the better is the quality of the cut. Problems with cut quality, such as a bow, twist, and camber (see Figure 3), are seen on shorter pieces (up to 4 inches long) that fall behind the shear after they are cut. Machines with lower rake angles require more power than those that have a higher rate.
Some guillotine-type machines have a variable rake, a rake angle that can be adjusted to suit the length of the part that is being cut. To evaluate whether this variable rake design is a better option for a fabricator, the type and thickness of the material being cut, the length to be cut, how much of it will fall behind the shear, and the rake angle available for the job must be determined.
For example, if a fixed rake angle has a 1-1/3-inch fixed rake and the adjustable rake machine has a range of 1 to 3 degrees using the 3-degree setting for the 1/4-inch thickness, the fixed rake will produce a better-quality cut on a 3-inch strip. The variable rake machine, on the other hand, may give a better-quality cut on a 1/2-inch strip of 24-gauge material.
Generally, one should not expect a good cut on a strip that is smaller than eight times the material thickness (example: a 2-inch strip of 1/4-inch steel). Variable rake machines are generally found in shops with thicker capacity requirements such as 1/2 inch and higher. In the case of these heavier machines, changing the rake angle allows for better cuts on a wide range of thicknesses and types of materials.
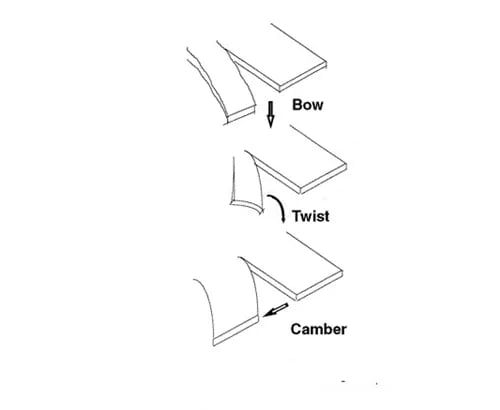
Shearing process of a plate shearing machine is a straightforward yet essential method for cutting metal plates or sheets accurately and efficiently. It is commonly used in various industries, including manufacturing, construction, and metal fabrication, for producing a wide range of components and parts.