What Is Press Brake Dies?
The press brake die is a tool utilized by the press brake machine to form sheet metal. This tool comprises of various components, and the composition of the tooling can vary.
The primary function of the press brake die is to alter the physical state of the material being formed, thus shaping the part.
Press brake dies can typically be divided into several parts, including the upper die, lower die, guide rail, and lower die base. These dies offer a great deal of versatility, with many of them able to be manufactured.
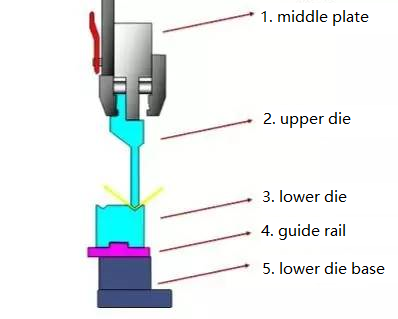
PS: regarding how to make press brake dies, we will cover this topic later.
Commonly Used Press Brake Dies
To extend the life of the mold, the press brake punch and dies are designed with rounded corners whenever feasible. The commonly used press brake dies include:
V bend dies
U bend dies
Z bend dies
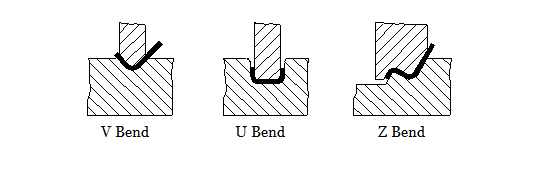
Typically, the height of the flanged edge should be at least three times the thickness of the plate (t), or L ≥ 3t. If the height of the flanged edge is too low, it becomes difficult to form even when using a bending die.
Punch Type | Main Application |
Straight Punch | Fabricated angles ≥90° |
Goose Neck Punch | Fabricated angles ≥90° |
Acute Punch | Fabricated angles ≥30° |
Press Brake Dies
Punch Type | Main Application |
Sing V Die | 1. While V angle = 88°(ref), able to bend angles ≥ 90° |
Double V Die | 2. While V angle = 30°(ref), able to bend angles ≥ 30° |
Press brake segment die
Typically, the standard length of a press brake punch and die set is 835mm, and it can be divided into various sizes to accommodate the bending of workpieces of different lengths.
The sizes usually include 10mm, 15mm, 20mm, 40mm, 50mm, 100mm, 200mm, and 300mm, totaling up to 835mm.
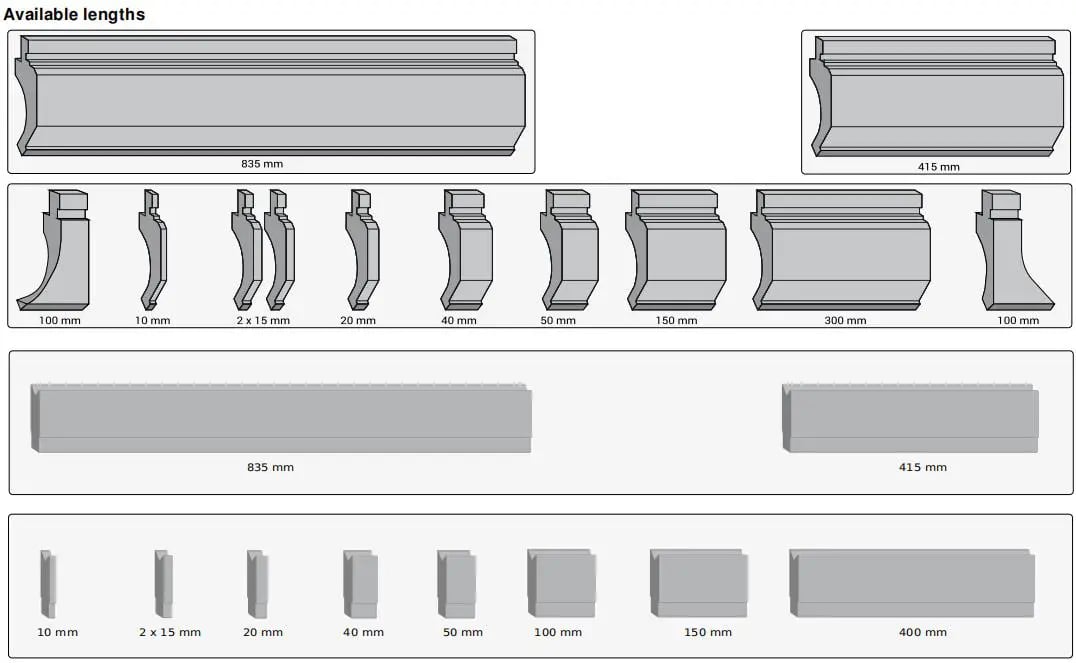
Press Brake Dies Materials
What are press brake dies made of?
There are various materials that can be utilized to manufacture press brake tools, including steel, alloy materials, and polymer materials, among others.
Currently, steel is the most widely used material for producing press brake tools, including T8 steel, T10 steel, 42CrMo, and Cr12MoV.
42CrMo is a high-strength alloy steel that has undergone quenching and tempering to display high strength and toughness.
It can operate at low temperatures down to -500°C and is known for its high strength, toughness, and resistance to wear.
The common materials used for press brake dies can be divided into eight categories.
- Carbon tool steel
T8A and T10A carbon tool steels are frequently used in the manufacture of press brake dies because of their good machinability and cost-effectiveness.
However, these materials have poor hardenability and red hardness and can undergo significant deformation during heat treatment. Additionally, they have a low capacity to bear loads.
- Low alloy tool steel
By incorporating the appropriate amount of alloy elements into carbon tool steel, low alloy tool steel is produced, which reduces the deformation and cracking tendency during quenching and improves the hardenability and wear resistance of the steel.
Some of the commonly used low alloy steels in the production of press brake dies include CrWMn, 9Mn2V, 7CrSiMnMoV, and 6CrNiSiMnMoV.
- High carbon and high chromium tool steel
High carbon and high chromium tool steel is known for its good hardenability, toughness, and resistance to wear.
It undergoes minimal deformation during heat treatment, making it a high-wear-resistant steel with a load-bearing capacity second only to high-speed steel.
However, due to significant carbide segregation, repeated upsetting and drawing (axial upsetting and radial drawing) are required to reduce the heterogeneous nature of the carbides and improve its performance.
Some of the common high carbon and high chromium tool steels include Cr12, Cr12MoV, and Cr12MoV1.
- High carbon medium chromium tool steel
High carbon medium chromium tool steels utilized for press brake dies include Cr4W2MoV, Cr6W, Cr5MoV, among others.
These materials have low chromium content, fewer eutectic carbides, uniform carbide distribution, minimal deformation during heat treatment, good hardenability, and stable dimensions.
Compared to high carbon and high chromium steel which can exhibit significant carbide segregation, these materials offer improved properties.
- High-speed steel
High-speed steel is frequently used in the production of press brake dies due to its high hardness, resistance to wear, and compressive strength. It also has a high load-bearing capacity.
W18Cr4V, W6Mo5, and Cr4V2 with reduced tungsten, as well as 6W6Mo5 and Cr4v high-speed steels developed to enhance toughness, are commonly used.
In order to improve its carbide distribution, high-speed steel also requires forging.
- Basic steel
Basic steel is produced by adding a small amount of other elements to high-speed steel and adjusting the carbon content to enhance its properties.
This results in improved properties compared to high-speed steel, such as increased wear resistance and hardness, as well as better fatigue strength and toughness.
It is a press brake die steel with high strength and toughness, and it is more cost-effective than high-speed steel.
The commonly used basic steel materials in press brake dies include 6Cr4W3Mo2VNb, 7Cr7Mo2V2Si, 5Cr4Mo3SiMnVAL, among others.
- Cemented carbide and steel bonded cemented carbide
The hardness and resistance to wear of cemented carbide in press brake die steel are the highest, but its strength and toughness when bending are poor.
Tungsten cobalt is used as the cemented carbide in press brake dies.
For press brake dies that require low impact and high resistance to wear, cemented carbide with low cobalt content can be selected. For high-impact dies, cemented carbide with high cobalt content can be used.
Steel-bonded cemented carbide is made through powder metallurgy, using iron powder and a small amount of alloy element powder (such as chromium, molybdenum, tungsten, or vanadium) as the binder and titanium carbide or tungsten carbide as the hard phase.
The matrix of steel-bonded cemented carbide is steel, which addresses the poor toughness and difficult processing of cemented carbide.
This material can be cut, welded, forged, and heat treated. Steel-bonded cemented carbide contains many carbides and has a hardness and resistance to wear that is lower than that of cemented carbide but still higher than other steel grades.
After quenching and tempering, its hardness can reach 68-73 HRC.
- New materials
The material utilized for the press brake tool is a type of cold working die steel, and its primary performance requirements are strength, toughness, and resistance to wear.
Currently, the development trend in press brake die steel has two main directions, both centered around high alloy steel D2 (Cr12MoV).
(1) Improving the toughness of press brake die involves reducing the carbon content and alloy element content and enhancing the uniformity of carbide distribution in steel. Examples of this direction include 8CrMo2V2Si and Cr8Mo2SiV.
(2) Improving the resistance to wear of press brake die to accommodate high-speed, automated, and high-volume production with powder high-speed steel. An example of this direction is 320CrVMo13.
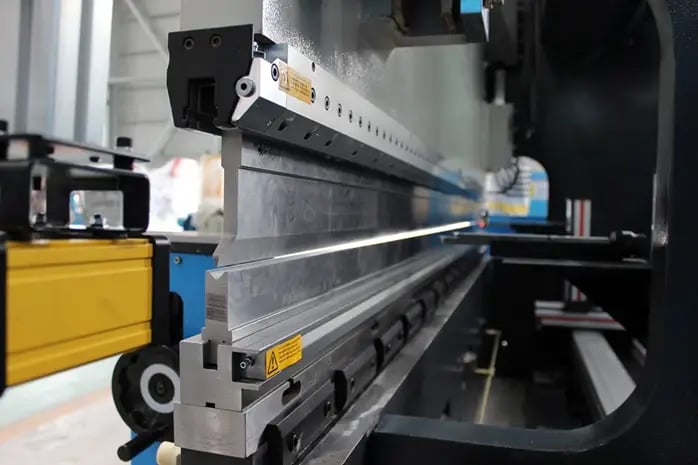
Press Brake Tools Heat Treatment
In order to improve their mechanical features, tools are subjected to heat treatments such as quenching and hardening.
QUENCHING:
This is a heat treatment consist-ing of heating and sub-sequently cooling steel to reduce the material’s intermal stress. During the heating process martensite is produced, which has a very hard structure and high ultimate tensile strength but low resilience.
As a result, the material can be easily broken; to avoid this problem, the steel is then tempered by controlled cooling. The cooling speed during tempering has a major effect on the residual stress of the steel, as the slower the cooling phase, the weaker the residual stress.
Steel types which can undergo this treatment contain 0.4-0.6% carbon and are therefore referred to as quenched and tempered steel.
HARDENING:
The purpose of this treatment is to increase the hardness of the material and it consists of heating the steel to a certain temperature and then rapidly cooling it.
The usual method used to measure the hardness of the tools is the Rockwell hardness test which is carried out with the conical (HRC) or spherical (HRB) indenters.
It involves gradually increasing the load on the instrument. The hardness is determined by the depth of penetration of the indenter into the piece.
INDUCTION HARDENING:
This is the most common heat treatment for press brake tools, but as it is a surface treatment, it affects only the external layer of a tool.
This type of hardening uses the the principle of electromagnetic induction: by placing a conductive material (a coil)into a strong alternating magnetic field, the tool is heated to a high tempereture and then rapidly cooled by a flow of coolant.
Induction hardening creates very hard surfaces, resistant to wear and fatigue without affecting the toughness of the core.
CORE HARDENING:
Some press brake tool manufacturers use core hardening to obtain consistent hardness throughout the whole tool, with lower values for the surface, which usually suffers wear.
Length and Precision
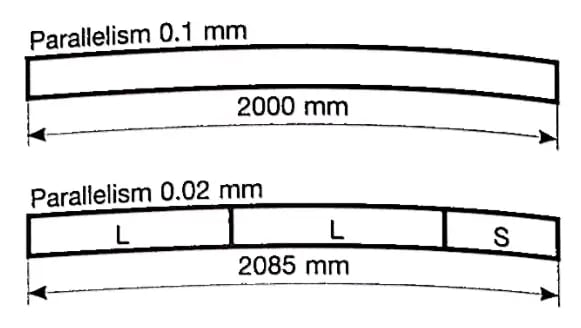
In the past, press brake tools were produced in a single piece that was as long as the press brake or the profile to be bent. These steel tools were planed, since hardening and grinding would have deformed them due to their length. Since the tools could not be machined, their precision was quite low, about 0.1 mm per meter.
With the advent of new technologies press brake tool precision has improved significantly. Today tools are produced, hardened and machined pieces, which can guarantee greater precision (0.0mm per tol) and have better mechanical properties than before. Press brake tool length varies according to the type, e.g. Promecam tools are 835mm long.
Segmented tools have several advantages: standard modular lengths, so that operators can buy tools to makeup the total length required;
Ease of handling, resulting in time-saving when setting up the press brake;
Cost savings, as only worn or damaged tool sections have to be replaced and not the total length;
Possibility of setting up the machine with different workstations used in sequence and of mounting tools with different profiles.
It is essential that the tools are of the correct size, and are perfectly interchangeable and aligned to take advantage of modern press brakes and to guarantee high quality bends and repeatability.
Thanks to the surface finishes produced by grinding machines, modern press brake tools can be produced with a radius in the die vee and in the punch tip.
This makes it possible to bend uniformly without marking the sheet metal, and to know the exact point of contact between tools and the sheet metal. This is essential information for the press CNC system for automatically seting the bending parameters to achieve maximum repeatability.