Table of Contents
Introduction
The press brake is a commonly used machine tool in sheet metal fabrication, which is designed for metal sheet bending and forming.
It aims to offer precise bending via various metals like steel, stainless steel).
And it is widely used in many aspects like automotive, aerospace, architecture, and manufacturing.
It is crucial to install the press brake correctly. A well-installed machine can not only ensure quality and accuracy but also can ensure the safety of operators.
However, if the press brake is not installed well, it may produce undesired bending results, cause machine damage and bring potential risks to operators and machines.
In our passage, we will delve into the whole installation process of the press brake. Watch the video first.
Press Brake Installation
Preparation Before Installation
Choose the location: choose a proper place to locate the press brake, which can ensure stability and safety. The site makes it easy for operators to work and is also convenient for maintenance and care.
Ensure appropriate fundamentals: the press brake should be installed on a solid fundamental to make sure it is accurate and steady. The fundamental could be a concrete floor or a specially designed frame. The fundamental should be firm and solid enough to withstand the vibration and working load of the machine.
Verify the electricity requirement: usually, the press brake needs an electricity power supply to drive it's motor and controller. Before installation, ensure the power supply is appropriately accessible to fit the electricity requirement. This may be concerned with electricity manufacture cooperation to ensure the steady operation of the machine.
Tooling and equipment prepared:
the crane or forklift is indispensable for operating and locating large-scale metal sheets and accessories. The wrench, screwdriver, and other tools can make it easy for operators to quickly and efficiently perform routine maintenance, troubleshoot minor issues, and make necessary adjustments. The precise spirit tool and rulers are also necessary for precision and accuracy checking.
Positioning
Use the forklift or crane to position the press brake to the pre-prepared fundamental. Make sure its correct place and locates in the center of the fundamental.
Unpacking
Check for any visible damage or missing parts: after the press brake is unloaded safely, inspect for any dents, scratches, or other signs of physical harm. It is crucial to record any damaged or lost parts and report them to the manufacturers and suppliers.
Remove the coated surface or transportation brackets: before operating the press brake, remove these painted surfaces and necessary shelves. Please follow the manufacturer's guidelines, and learn how to protect the components and tooling.
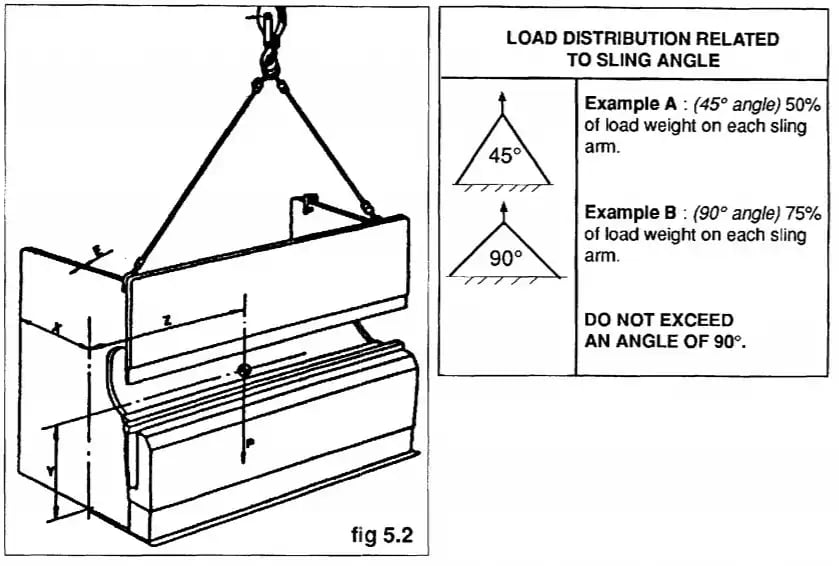
Specific Steps
Step 1: install the base
According to the model and specification of the press brake, put the base in a proper position, then use the bolt or other fixed device to fix the base on the ground.
Step 2: install the columns
Mount the columns on the base. The columns are usually composed of two or more components. Install and assemble according to the operation guideline. Use the bolts or other accessories to fix the columns on the base, ensuring it is vertical and stable.
Step 3: install the beam
Install the beam on the column. The beam is made up of one or multiple beam sections. Install the beam correctly refers to the operation guideline. Use the bolts or other fixed parts to fix the beam on the column, ensuring it is horizontal and stable.
Step 4: install the workbench
Put the worktable on the base and ensure it is aligned with the base.
Step 5: install the ram
Install the ram on the workbench, and use the bolt to adjust it to the proper height and position.
Step 6: install the upper punch
Install the upper punch on the ram, and use bolts and other parts to fix it firmly.
Step 7: install the bottom die
Install the bottom die on the workbench, and use bolts and other parts to fix it firmly.
Step 8: install the hydraulic system
Install the hydraulic pump: according to the manufacturer’s reference, mount the hydraulic pump in the proper position of the press brake. Usually, the hydraulic pump can be fixed on the machine tool through bolts. Connect the oil inlet and outlet of the hydraulic pump to ensure a firm connection.
Install the hydraulic cylinder: ensure the position of the hydraulic cylinder according to the design drawings, and use bolts to fix the cylinder on the press brake. Connect the oil inlet and outlet of the hydraulic cylinder to ensure a firm connection.
Install the hydraulic valve and controller: ensure the installation position of the hydraulic valve and controller based on the design drawing, and use bolts to fix them in the appropriate position. Connect the oil inlet and outlet of the hydraulic valve and controller to ensure a firm connection.
Install the hydraulic tank and filter: mount the hydraulic tank properly and use the bolts to fix it. Connect the hydraulic tank and filter and ensure their firm connection.
Install the hydraulic piping: based on the design drawing and manufacturer’s guide, install the hydraulic piping, and connect hydraulic components and piping. Ensure the hydraulic piping is connected firmly without leaking, and mount the piping correctly, fix the clamp.
Fill the hydraulic oil: based on the manufacturer’s regulation, choose the proper hydraulic oil, and pull the oil into the tank until meeting the requirement of the oil level. Start the hydraulic system, extract the air, and check whether the hydraulic system runs commonly or not.
Step 9: connect the electrical system
Connect the electrical system and power supply, and ensure the electricity line is firm and reliable.
Main power connection: connect the main power line to the appropriate outlet or switch. Ensure the connection is firm and use the appropriate electrical connector.
Control panel connection: connect the electrical components on the control panel to the main power supply of the machine. This includes connecting the controller, buttons, Indicator lights, and electric valves to the proper power wiring and terminal blocks.
Motor connection: connect the electric drive motor to the main power supply and controller. This usually is concerned with connecting the power and control wires to the proper terminals.
Sensor and limit switch connections: the press brake is equipped with a sensor and limit switch, which are used for testing and controlling the bending process, and can be connected to the control panel and controller.
Grounding connection: ensure a good connection between the metal part of the press brake and the grounding of the electrical system. This aims to ensure safety and protect against electric shock and static buildup.
Testing and debugging: after finishing the above process, it is necessary to check and debug. Ensure all the electrical components work in good condition and the control panel can control the press brake well.
Step 10: install the back gauge system
Ensure the installation position: usually, the back gauge should be installed on the rear of the press brake to support and position the workpiece to be bent.
Install the bracket: fix the bracket of the back gauge on the worktable of the press brake. Ensure that the bracket is stable and connected with the structure of the press brake.
Install the support bar: the support bar is usually installed on the rear or side of the press brake.
Install the guide rail: make sure it is aligned with the arm and support bar, and fix them firmly.
Connect the transmission: connect the transmission to the controller or moto. Ensure it can be moved and adjusted according to the anticipation. This usually involves installing electric motors, chains, gears, etc.
Install the slider: install the slider on the bracket of the back gauge, and ensure its smooth running. It may be necessary to use the adjustment screw to adjust the slider's position and height.
Install the control system: install the back gauge controller in the proper position, and connect the wire and sensor according to the explanation of the manufacturer. Ensure the control system can control the position of the back gauge’s slider accurately.
Step 11: adjustment and calibration
Based on the operation manual, all the components should be adjusted and calibrated to ensure they work correctly and meet the requirement.
Step 12: final checking and handover
The first step of the final inspection is to check the installed press brake comprehensively.
This includes checking all the components and their performance. The operators should check the hydraulic system, electric connection, control panel, and other essential ingredients to ensure their correct installation without any damage.
If any problem or difference occurs, please seek help from the manager or manufacturer immediately to avoid severe problems in the future.
Also, file recording is an indispensable part of the handover process.
Additionally, it is necessary to secure and organize maintenance plans and detailed information to ensure instant maintenance.
Step 13: maintenance and troubleshooting
Maintenance
Regular maintenance: the accumulated dirt, dust, and debris.
Lubrication: especially pay attention to axes, guide rail, hydraulic components, and other vital parts.
Components checking: perform regular visual checking of the machine components and replace and repair the damaged parts.
Calibration and alignment: ensure the press brake can be calibrated and aligned correctly.
Operators training: skilled operators can prolong the life span of the machine.
Conclusion
In conclusion, properly installing press brakes is essential to the operation of the metal sheet and mechanical engineering.
It offers fundamentals for highly efficient and precise bending and ensures the expected results, as well as decreases the potential risks.
Manufacturers can seamlessly safeguard their investments while ushering in unparalleled performance.