The press brake is an essential machine tool in sheet metal fabrication, specifically designed for bending and forming metal sheets, including materials like steel and stainless steel. Various types of press brakes are commonly used, such as mechanical, manual, hydraulic, and CNC press brakes.These machines find applications in diverse fields, including automotive, aerospace, architecture, and manufacturing. Proper press brake installation is crucial, as it not only ensures quality and accuracy in bending but also guarantees the safety of operators. Conversely, inadequate installation of the press brake can lead to undesirable bending outcomes, potential machine damage, and increased risks for operators. In this passage, we will explore the complete process of press brake installation.
Press Brake Installation
Preparation Before Installation
Choose the location: choose a site that offers sufficient space around the press brake, which can ensure stability and safety. The site makes it easy for operators to work and is also convenient for maintenance and care. A cramped space can hinder workflow and increase the risk of accidents.
Ensure appropriate fundamentals: the press brake should be installed on a solid fundamental to make sure it is accurate and steady. The fundamental could be a concrete floor or a specially designed frame. The fundamental should be firm and solid enough to withstand the vibration and working load of the machine.
Level Surface: the installation site must have a level surface to prevent vibrations and uneven pressure distribution during press brake operation. An uneven foundation can lead to misalignment of the press brake, resulting in inaccurate bends and increased wear on machine components.
Reinforced Foundation: use reinforced concrete foundations capable of supporting the weight of the press brake and the operational forces it generates. According to industry standards, a foundation thickness of at least 12 inches with reinforced steel bars is often recommended. This prevents settling or shifting, which could otherwise compromise the machine's performance.
Verify the electricity requirement: usually, the press brake needs an electricity power supply to drive it's motor and controller. Before installation, ensure the power supply is appropriately accessible to fit the electricity requirement. This may be concerned with electricity manufacture cooperation to ensure the steady operation of the machine.
Electrical Requirements: Verify the power supply specifications, such as voltage, phase, and frequency, to match the press brake's requirements. For instance, if the press brake requires a 480V three-phase power supply, ensure the facility can provide this without overloading existing circuits.
Dedicated Circuit: Use a dedicated electrical circuit for the press brake to prevent interference with other equipment and to enhance safety. A dedicated circuit means that the press brake has its own breaker and wiring, reducing the risk of electrical faults.
Ventilation: Provide adequate ventilation to dissipate heat generated during operation. Proper airflow prevents overheating and extends the lifespan of electronic and hydraulic components. In some cases, air conditioning may be necessary to maintain optimal working temperatures, especially in facilities located in warmer climates.
Tooling and equipment prepared: the crane or forklift is indispensable for operating and locating large-scale metal sheets and accessories. The wrench, screwdriver, and other tools can make it easy for operators to quickly and efficiently perform routine maintenance, troubleshoot minor issues, and make necessary adjustments. The precise spirit tool and rulers are also necessary for precision and accuracy checking. Equip yourself with multimeters, insulation testers, and other electrical testing tools to verify the integrity of electrical connections. Ensure that all personnel involved in the installation wear appropriate safety gear, including gloves, safety glasses, and hard hats.
Positioning
Use the forklift or crane to position the press brake to the pre-prepared fundamental. Ensure the lifting equipment is securely attached to the machine's lifting points. Position the press brake machine with enough clearance on all sides for maintenance and operation. For example, leaving a minimum of 1 meter of space around the machine allows easy access for operators and technicians.
Unpacking
Check for any visible damage or missing parts: after the press brake machine tool is unloaded safely, inspect for any dents, scratches, or other signs of physical harm. It is crucial to record any damaged or lost parts and report them to the manufacturers and suppliers.
Remove the coated surface or transportation brackets: before operating the press brake, remove these painted surfaces and necessary shelves. Please follow the manufacturer's guidelines, and learn how to protect the components and tooling.
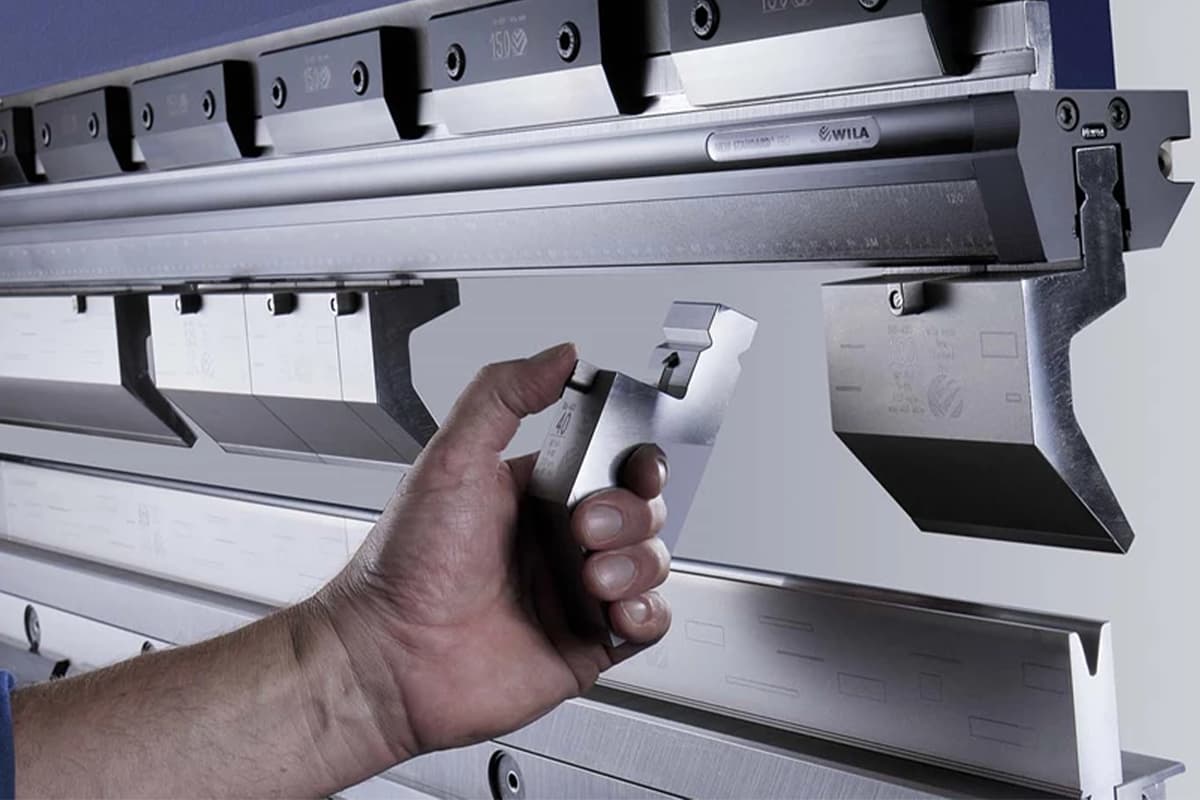
Press Brake Installation Specific Steps
Step 1: install the base
According to the model and specification of the press brake, put the base in a proper position, then use the bolt or other fixed device to fix the base on the ground.
Step 2: install the columns
Mount the columns on the base. The columns are usually composed of two or more components. Install and assemble according to the operation guideline. Use the bolts or other accessories to fix the columns on the base, ensuring it is vertical and stable.
Step 3: install the beam
Install the beam on the column. The beam is made up of one or multiple beam sections. Install the beam correctly refers to the operation guideline. Use the bolts or other fixed parts to fix the beam on the column, ensuring it is horizontal and stable.
Step 4: install the workbench
Put the worktable on the base and ensure it is aligned with the base.
Step 5: install the ram
Install the ram on the workbench, and use the bolt to adjust it to the proper height and position.
Step 6: install the upper punch
After determining the tooling position on the bed, install the upper punch on the ram, and use bolts and other parts to fix it firmly.
Step 7: install the bottom die
Install the bottom die on the workbench, and use bolts and other parts to fix it firmly.
Step 8: install the hydraulic system
Install the hydraulic pump: according to the manufacturer’s reference, mount the hydraulic pump in the proper position of the press brake. Usually, the hydraulic pump can be fixed on the machine tool through bolts. Connect the oil inlet and outlet of the hydraulic pump to ensure a firm connection.
Install the hydraulic cylinder: ensure the position of the hydraulic cylinder according to the design drawings, and use bolts to fix the cylinder on the press brake. Connect the oil inlet and outlet of the hydraulic cylinder to ensure a firm connection.
Install the hydraulic valve and controller: ensure the installation position of the hydraulic valve and controller based on the design drawing, and use bolts to fix them in the appropriate position. Connect the oil inlet and outlet of the hydraulic valve and controller to ensure a firm connection.
Install the hydraulic tank and filter: mount the hydraulic tank properly and use the bolts to fix it. Connect the hydraulic tank and filter and ensure their firm connection.
Install the hydraulic piping: based on the design drawing and manufacturer’s guide, install the hydraulic piping, and connect hydraulic components and piping. Ensure the hydraulic piping is connected firmly without leaking, and mount the piping correctly, fix the clamp.
Fill the hydraulic oil: based on the manufacturer’s regulation, choose the proper hydraulic oil, and pull the oil into the tank until meeting the requirement of the oil level. Start the hydraulic system, extract the air, and check whether the hydraulic system runs commonly or not.
Step 9: connect the electrical system
Connect the electrical system and power supply, and ensure the electricity line is firm and reliable.
Main power connection: connect the main power line to the appropriate outlet or switch. Ensure the connection is firm and use the appropriate electrical connector.
Control panel connection: connect the electrical components on the control panel to the main power supply of the machine. This includes connecting the controller, buttons, Indicator lights, and electric valves to the proper power wiring and terminal blocks.
Motor connection: connect the electric drive motor to the main power supply and controller. This usually is concerned with connecting the power and control wires to the proper terminals.
Sensor and limit switch connections: the press brake is equipped with a sensor and limit switch, which are used for testing and controlling the bending process, and can be connected to the control panel and controller.
Grounding connection: ensure a good connection between the metal part of the press brake and the grounding of the electrical system. This aims to ensure safety and protect against electric shock and static buildup.
Testing and debugging: after finishing the above process, it is necessary to check and debug. Ensure all the electrical components work in good condition and the control panel can control the press brake well.
Step 10: install the back gauge system
Ensure the installation position: usually, the back gauge should be installed on the rear of the press brake to support and position the workpiece to be bent.
Install the bracket: fix the bracket of the back gauge on the worktable of the press brake. Ensure that the bracket is stable and connected with the structure of this sheet metal product.
Install the support bar: the support bar is usually installed on the rear or side of the press brake.
Install the guide rail: make sure it is aligned with the arm and support bar, and fix them firmly.
Connect the transmission: connect the transmission to the controller or moto. Ensure it can be moved and adjusted according to the anticipation. This usually involves installing electric motors, chains, gears, etc.
Install the slider: install the slider on the bracket of the back gauge, and ensure its smooth running. It may be necessary to use the adjustment screw to adjust the slider's position and height.
Install the control system: install the back gauge controller in the proper position, and connect the wire and sensor according to the explanation of the manufacturer. Ensure the control system can control the position of the back gauge’s slider accurately.
Step 11: Leveling and calibration
Precision leveling
Use laser levels or precision spirit levels to ensure the press brake is perfectly level. Check the levelness at multiple points across the machine to achieve even weight distribution. Proper leveling is essential for accurate bending and reducing mechanical stress on the machine. For instance, place a level on the bed and the ram to confirm both are aligned.
Calibration
Once the machine is leveled, calibrate the press brake's components, including the ram and back gauge system. Calibration ensures the machine operates within specified tolerances, resulting in precise and consistent bends. Follow the manufacturer's guidelines for calibration procedures and use calibration tools as needed. For example, use a dial indicator to measure the ram's movement and adjust accordingly.
Step 12: final checking and handover
The first step of the final inspection is to check the installed press brake comprehensively. This includes checking all the components and their performance. The operators need to check the hydraulic system, electric connection, control panel, and other essential ingredients to ensure their correct installation without any damage.
If any problem or difference occurs, please seek help from the manager or manufacturer immediately to avoid severe problems in the future. Also, file recording is an indispensable part of the handover process. Additionally, it is necessary to secure and organize maintenance plans and detailed information to ensure instant maintenance.
Step 13: maintenance and troubleshooting
Maintenance
Regular maintenance: the accumulated dirt, dust, and debris.
Lubrication: especially pay attention to axes, guide rail, hydraulic components, and other vital parts.
Components checking: perform regular visual checking of the machine components and replace and repair the damaged parts.
Calibration and alignment: ensure the press brake can be calibrated and aligned correctly.
Operators training: skilled operators can prolong the life span of the machine.
Troubleshooting
Misalignment or inaccurate bends: check for any damage, and the uncalibrated problem with the bending die and punch. Replace them in time.
Hydraulic system failure: check whether the hydraulic piping, connector, and sealed components leak or damage. Replace all the worn parts and ensure the proper oil level and cleanliness.
Electric problem: check the electric connection, switch, and sensor. Look for loose and damaged wires and connections. Please refers to the guideline and skilled operators for help.
Loud noise and vibration: check whether there is a loose part, damaged bearing, or worn parts on the machine. Tighten loose parts and replace any damaged or worn parts.
10 important steps for metal press brake setup
1. Review the drawing
Firstly, operators need to familiarize themselves with the parts. Reviewing the drawings is vital for accuracy and producing high-quality products. When an operator reviews the drawing, it is easier to know key details such as the type of material, dimensions, blank size, flange tolerance, and inside radius of angles.
2. Select the tooling
There are several types of tooling, and your selection is primarily based on the drawing.
Remember, to produce accurate parts; you must select the right tooling. Your tool selection options include coining, special application, air bending, or bottom bending. Always select the tooling that’s accurate to the manufacturer’s specifications because worn tooling produces faulty parts.
3. Determine tonnage
It is essential to estimate the tonnage requirements as an operator, especially in air bending. Usually, there are tonnage charts you can refer to for air bending. In bottom bending, operators are advised to use x4 the air bending tonnage while x8 the air bending tonnage is ideal when coining. Check the manufacturer’s recommendations if you want to use the special application tooling.
4. Press brake selection
There are several types of press brakes. You can skip this step if your shop does not have more than one press brake. However, if you have several press brakes machines to choose from, choosing the right press can determine the quality of the final product.
Operators must understand how different press brakes work and factors to consider, for example, the type of metal to bend.
5. Determine the tooling position on the worktable
The operator should check and confirm whether the press brake manufacturer allows off-center loading or not. When working off the center, always follow the manufacturer’s guidelines at all times.
6. Install the tools
After determining the tooling position on the bed, the next step entails installing the tools and aligning them to make the bend. It is considered the most time-consuming, tiring, and costly step in press brake setup.
7. Program the press brake machine
Programming the brake machine is the second most time-consuming step in the setup process because most operators have limited programming skills. Programming manual press brake machines are quite tiring, time-consuming, and daunting. In fact, programming a manual press brake requires trial and error to ensure everything is accurate.
However, if you have a CNC press brake, programming is straightforward. As a press brake operator, take your time to research and learn how to program to avoid wasting time during setup. Alternatively, you can seek help from an expert to understand programming fast and easily.
8. Test run
Now that everything is set up, you can make a test bend. A test run is crucial to ensure the machine is running smoothly. Also, a test run is essential to ensure the setup is successful and accurate. You can use scrap metal for a test run.
9. Correct the program
Sometimes you can make a mistake and incorrectly program the brake press machine. After carrying out the test run, check if the part is acceptable. Making a test band and correcting the program should be done concurrently. However, you shouldn’t correct the program if you have a good test bend.
10. Run parts
With the setup complete, you can start operating the machine. Although everything is working fine, keep an eye on the parts now and then and make necessary corrections if need be.
Press brake machines are used in numerous industries and come in various types and sizes for specific jobs. The accuracy of a bend primarily depends on the tool’s setup. Therefore, operators must be careful when setting up the machine. As a rule of thumb, the operator should not start production until he is confident about the setup of the press brake machine. Luckily, the setup time decreases substantially with research, practice, and patience.
Press Brake Operation Basics
1. Pre-Operation Checks
(1) Inspecting the Equipment
Visual Inspection: Check whether the switch, control, motor, and grounding are in normal working condition. Verify the oil level in the oil tank and the hydraulic system's condition. Idle the machine and maximize the press brake stroke. Check whether the machine is operating normally, the motor's rotation is normal, and the sound is normal.
Tooling assembly and alignment: Before installing the punch and die, stop the machine, and install the lower and upper dies. The upper and lower dies of the press brake must be aligned to obtain higher bending accuracy. To align the upper and lower dies, drive the ram downward, bringing the upper dies close to the lower dies, leaving a distance equal to the workpiece thickness. Manually adjust the upper and lower die positions using the lower die bolts and upper die clamps. After aligning the upper and lower dies, drive the ram upward.
(2) Safety Equipment
- Safety Devices: Ensure all safety devices (such as light curtains and emergency stop buttons) are functioning properly.
- Personal Protective Equipment: Operators should know to wear appropriate personal protective equipment, such as gloves and safety glasses.
2. Operation Steps
(1) Setting Up the Machine
- Selecting Tools: Choose the appropriate punch and die based on the required bending angle and material thickness.
- Adjusting the Back Gauge: Adjust the position of the back gauge according to the size of the workpiece to ensure accurate positioning.
(2) Programming (for CNC Press Brakes)
- Programming: Use the software interface to program the bending angle, bending length, and tool parameters.
- Test Run: Perform a test run to ensure the machine is working properly and the tools are correctly installed.
(3) Bending Operation
- Placing the Workpiece: Place the metal sheet on the press brake bed, ensuring it is aligned with the back gauge and reference points.
- Starting the Machine: Start the press brake, allowing the punch to press down on the metal sheet to perform the bending operation.
- Checking the Bend Angle: After bending, check the bend angle and dimensions to ensure they meet the requirements.
- Tool splicing and replacement: Select manual mode, lower the ram, and turn off the press brake. To replace the tool, stop the machine and remove the tooling from the side. Then, insert a new die from the side and tighten the bolts or clamps. Nowadays, many quick clamps are available for fast and convenient tool replacement. There is no need to loosen the bolts, and the tooling can be loaded and unloaded vertically.
3. Shut down the machine
When turning off the press brake, switch to manual mode, and lower the ram by stepping on the pedal to align the upper die with the lower die. Press the stop button and turn off the main motor.
The switch parameter should be set to 0. In case of emergencies, press the emergency stop button, but this will not affect the subsequent procedure since only the axes and pump are turned off. Release the button to restart.
Press Brake Maintenance
Daily Maintenance
To ensure optimal performance and longevity of the press brake, daily maintenance is essential. This involves having qualified professionals conduct routine checks and services. Key maintenance tasks include:
- Lubrication: Regularly lubricate all moving parts of the machine using high-quality lubricating oil. This not only reduces friction but also prevents wear and tear. It’s recommended to focus on high-wear areas weekly, ensuring they receive adequate lubrication to maintain smooth operation.
- Cleaning: Thoroughly clean machine components to remove metal shavings, dust, and other debris that can interfere with performance. A clean machine operates more efficiently and reduces the risk of malfunctions.
Regular Inspections
In addition to daily maintenance, conducting regular inspections is vital for the safe and efficient operation of the press brake. Key areas to focus on include:
- Hydraulic System: Regularly check the hydraulic oil level and ensure its cleanliness. Contaminated oil can lead to performance issues, so replace the hydraulic oil as necessary to maintain optimal function.
- Electrical Components: Inspect the wiring within the electrical cabinet for any signs of wear or damage. Ensure all connections are secure and functioning properly to avoid electrical faults.
- Sensors: Test the functionality of sensors, such as the grating ruler, to ensure they are providing accurate readings. Faulty sensors can lead to improper bending and safety hazards.
- Structural Integrity: Regularly check the tightness of bolts and other fasteners to confirm that they are secure. Loose components can lead to misalignments and potential accidents during operation.
By adhering to a comprehensive daily maintenance and regular inspection routine, operators can significantly enhance the reliability and safety of the press brake, ultimately leading to improved productivity and quality in sheet metal fabrication.
Tools Needed for Press Brake Installation
Installing a press brake requires a variety of specialized tools to ensure a safe, accurate, and efficient setup. Here’s a detailed breakdown of the essential tools needed:
1. Lifting Equipment
- Forklift or Crane: Essential for moving and positioning heavy components safely. A forklift can maneuver in tight spaces, while a crane is suitable for lifting large, heavy parts.
- Slings and Shackles: Used in conjunction with lifting equipment to securely hoist and stabilize components during the installation process. Ensure they are rated for the load being lifted.
2. Measuring and Alignment Tools
- Spirit Level: Vital for checking the levelness of the press brake, ensuring proper alignment during installation.
- Laser Level: Provides a more precise alignment over longer distances, helping to ensure that the machine is perfectly straight and level.
- Dial Indicator: Used to measure the alignment and spacing of components with high precision, ensuring all parts are correctly positioned.
3. Hand Tools
- Socket Set: Necessary for assembling and tightening various components of the press brake, ensuring secure connections.
- Torque Wrench: Ensures that bolts and fasteners are tightened to the manufacturer’s specifications, preventing loosening during operation.
- Hex Keys: Used for adjusting and securing hexagonal screws, which are common in machinery assembly.
4. Electrical and Hydraulic Tools
- Voltage Tester: Essential for ensuring electrical systems are safe and properly functioning before powering up the press brake.
- Hydraulic Pressure Gauge: Allows for monitoring and adjusting hydraulic pressure to meet the necessary specifications for optimal operation.
- Oil Dispenser: Used for adding hydraulic fluid and lubricants, ensuring smooth functioning of hydraulic components.
5. Safety Equipment
- Gloves: Protect hands from sharp edges and hot surfaces during installation.
- Goggles: Safeguard eyes from debris and any potential splashes during hydraulic or electrical work.
- Hard Hats: Provide head protection from potential falling objects in the work environment.
6. Calibration Tools
- Protractor: Useful for measuring angles during installation and ensuring that the machine is set up to the correct specifications.
- Feeler Gauge: Helps in checking gaps and clearances between components, which is crucial for precise operation.
- Shims: Used to adjust heights and alignments, ensuring that all parts fit together perfectly.
7. Documentation and Software
- Installation Manuals: Provide step-by-step instructions for the assembly and installation process, ensuring compliance with manufacturer guidelines.
- Calibration Software: If applicable, this software aids in the calibration process, allowing for precise adjustments and settings based on the specific requirements of the press brake.
By having these tools on hand, operators can facilitate a smooth and effective press brake installation, leading to enhanced performance and safety in operations.
Ensuring Proper Leveling of the Press Brake During Installation
To achieve precise leveling of the press brake during installation, follow these steps:
- Choose a Stable Foundation: Ensure the press brake is placed on a solid, stable surface, such as concrete, to prevent any shifts or settling.
- Use a Spirit Level: Place a spirit level on the bed of the press brake to check for levelness. This initial check is crucial for accurate alignment.
- Adjust Leveling Bolts: If the level indicates deviations greater than 1-2 mm per meter, adjust the leveling bolts accordingly to bring the machine into proper alignment.
- Support Plates: If recommended, use support plates under each leveling bolt to distribute weight evenly and provide additional stability.
- Secure Anchoring: Ensure that the machine is anchored securely to the foundation to prevent any movement during operation.
- Center the Machine: Position the press brake centrally on its foundation to maintain balance and prevent shifts.
- Verify Connections: Check all electrical and hydraulic connections. Ensure the hydraulic oil is at the correct temperature and free of bubbles to avoid performance issues.
- Test for Accuracy: After installation, verify the ram parallelism, crowning, and die alignment to confirm that the press brake is leveled correctly and ready for precise operation.
Optimizing the Press Brake Installation Process to Reduce Costs and Time
To streamline the press brake installation process and minimize costs and time, consider implementing the following strategies:
- Set Target Times: Establish clear target times for each phase of installation. Regularly monitor progress to identify areas for improvement.
- Optimize Packaging and Delivery: Organize components in the order they will be installed, making sure parts are easily accessible to reduce unpacking time and streamline the installation process.
- Prepare the Site: Confirm all necessary site conditions (electricity, gas, water, foundation) with the customer in advance to avoid delays during installation.
- Apply SMED (Single-Minute Exchange of Die): Differentiate between internal and external setup tasks. Streamline steps to reduce adjustments, saving time and increasing efficiency.
- Utilize Advanced Scheduling Tools: Implement tools such as Order Slotting and Detailed Scheduling to manage resources effectively, shorten lead times, and adapt to changes quickly.
- Implement Lean Practices: Use lean techniques like value stream mapping, the 5S methodology, and Just-in-Time (JIT) production to minimize waste and enhance workflow.
- Automate Repetitive Tasks: Leverage robotic process automation (RPA) and workflow management systems to handle repetitive tasks, thereby reducing manual labor and the potential for errors.
- Develop Innovative Tools and Processes: Introduce automated commissioning tests or use robotics for repetitive tasks, such as drilling, to save both time and costs.
- Apply Group Technology and Mixed-Model Production: Organize similar processes and products to minimize changeover times and optimize workload balance.
By incorporating these strategies, you can effectively enhance the efficiency of the press brake installation process while reducing associated costs and time.