Table of Contents
Why Need Protection Device for Press Brake
Press brakes are vital tools in metal fabrication, enabling precise bending of metal sheets and plates. However, the operation of benders presents inherent safety risks, particularly during bending processes involving high-pressure forces and moving parts. To mitigate these risks and ensure operator safety, the implementation of laser protection devices for safety guarding has become increasingly crucial in modern press brake systems.
Understanding Laser Protection Devices
Laser Curtain Systems: Laser protection devices for press brakes commonly take the form of laser curtain systems. These systems utilize infrared laser beams to create a protective curtain around the working area of the press brake. When the laser beam is interrupted by an object, such as a hand or limb, the system triggers an immediate stoppage of the bender operation, preventing potential injuries or accidents.
Key Components:
Emitter and Receiver Units: Laser curtain systems consist of emitter and receiver units positioned opposite each other to create the protective curtain. The emitter unit emits the laser beams, while the receiver unit detects interruptions in the beam caused by foreign objects.
Control Unit: A centralized control unit monitors the emitter and receiver units, processing signals and activating safety protocols when necessary. The control unit ensures rapid response times to prevent accidents effectively.
Safety Interface: Laser protection devices are integrated with the bender's control system through safety interfaces, enabling seamless coordination between machine operation and safety protocols.
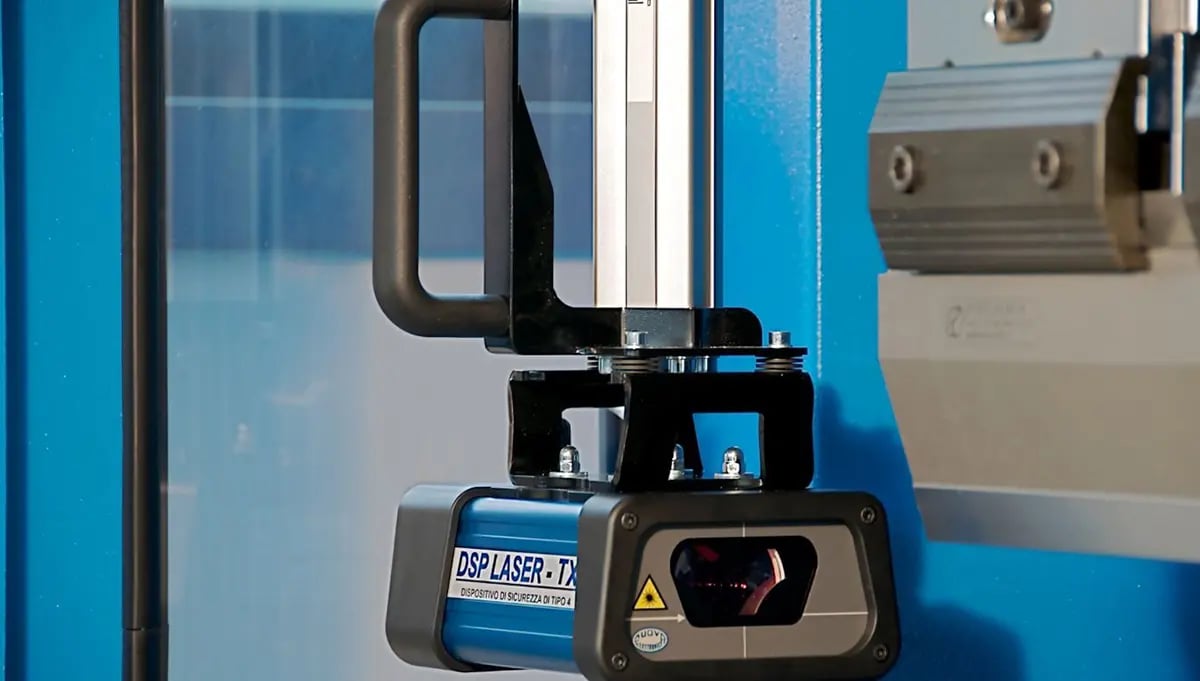
Benefits of Laser Protection Devices
Operator Safety: The primary benefit of laser protection devices is the enhancement of operator safety. By instantly halting press brake operations upon detecting unauthorized access or potential hazards, these devices minimize the risk of accidents and injuries in the workplace.
Compliance with Safety Standards: Laser protection devices help manufacturers adhere to industry safety standards and regulations governing press brake operations. Compliance with these standards not only protects workers but also mitigates legal and financial risks associated with workplace accidents.
Maintaining Productivity: While prioritizing safety, laser protection devices also contribute to maintaining productivity in metal fabrication operations. By swiftly identifying and addressing safety risks, these devices minimize downtime and ensure continuous production flow.
Flexibility and Adaptability: Laser protection devices can be customized and adjusted to accommodate various press brake configurations, working environments, and operational requirements. This flexibility enables seamless integration into existing bender systems without compromising efficiency or performance.
Conclusion
In the dynamic landscape of metal fabrication, safety remains paramount. Laser protection devices for benders represent a proactive approach to safeguarding workers and minimizing risks associated with press brake operations. By investing in these advanced safety solutions, manufacturers can uphold high standards of workplace safety while optimizing productivity and efficiency in their operations.